Large component casting, also known as megacasting, or gigacasting if you’re Tesla, is hot right now, and a major milestone has just been reached. Chinese automaker Chery Auto has cast an entire underbody using a 13,000-ton dual-injection press, and while the result is nothing short of impressive, there are a few good reasons why you probably shouldn’t want a one-piece cast underbody on your car.
I don’t have anything against casting as a process, because it’s produced some incredible stuff. Most alloy wheels on production cars are cast, for example. Megacasting an entire underbody is an incredible feat of manufacturing, just an absolutely awe-inspiring flex of might. I also don’t have anything against the structural soundness of this part, as it’s likely perfectly fine. See, my beef lies in repairability, because large structural castings require a completely different approach to a structure made of stamped parts, one that flirts with disposability.


But Thomas, aren’t other automakers already using cast strut towers? Absolutely, but the big difference there is modularity and repairability. Let’s take the jaw-droppingly gorgeous cast strut towers of the Lexus LC 500 as an example. Those astonishing strut towers are separate pieces, attached to conventional pressed steel front longitudinal members using rivets and structural adhesive. Should an LC 500 end up in a collision that cracks the cast strut tower but doesn’t total the car, that part can be replaced, and if the rest of the structure’s fine, it can remain untouched.
In contrast, if a car with towers and floor all cast as one is in a wreck bad enough to damage a strut tower, that entire underbody is junk. The whole thing. Big aluminum castings don’t take safely to straightening like steel does, and having to replace an entire underbody in the event of a moderate small-overlap or front-quarter collision has a dramatic effect on repairability.
What I’m concerned about is that it’s possible all that Chery Auto has done here is find a way to make a car even more disposable, and if this trend picks up steam, it could have knock-on effects for consumers. While the bulk of every insurance premium covers injury and liability, if casting the entire floor as one from strut tower to strut tower makes a car more expensive to repair and more prone to be written off, it’ll absolutely be more expensive to insure as a consequence. There might be savings on the front end for manufacturers, but savings on the back end for consumers? Hmmm.
Secondly, we need to ask how repeatable this process is. Pressed steel parts have a very high usability rate. Huge castings? Much lower. This 2022 report on megacasting from Ducker Carlisle states that Tesla had a gigacasting scrap rate of 45 percent in 2021.
Huge castings are amazing when they’re warranted. Subframes, suspension arms, drive motor housings, hubs, dashboard support structures, seat frames, if it bolts on, you name it. However, casting an entire underbody in one go seems like a process with downsides for consumers. A car is the second-most expensive thing you’ll buy in your life, so let’s keep them repairable.
Former casting engineer Lewin here. That scrap rate is quite poor, but it’s not quite as bad as you think. Castings are highly recyclable. In fact, within the factory, you could pretty much throw the bad casting back into your melt pot and simply try again. It’s not particularly efficient but the castings aren’t really going in the bin—that metal is absolutely being reused in the plant.
Thomas has given us great insight into the consequences of using big castings. It’s worth noting, though, that they can be a great way to make producing a vehicle cheaper by slashing part counts and the number of required assembly and welding operations. There’s value there that offsets the reduced repairability in my book, but not everyone agrees that reduced repairability is a good thing. That’s very fair.
But more importantly, let’s take a quick look over these castings! A quick note on why this is impressive. Basically, die-casting parts involves squirting metal into a mold. The bigger the part, the harder it is to fill it up with hot metal before it goes cold and freezes off inside. Also, the bigger the part, the harder it is to keep the mold closed. Megacasting is all about making bigger castings than ever. It involves a lot of engineering to make big casting machines and effective dies that work at these scales.
So, this is a huge casting, right? The first thing that jumps out to me as a casting engineer is the double biscuit. See those big round protrusions on either side? Those are the biscuits!
Those biscuits are from where the pistons injected metal into the giant casting die. Hence why they’re round! You can also see a little black scorch on the right-hand side biscuit, where some excess tip lube from the injection piston has burned off. That’s generally nothing to worry about. If it gets too bad, though, the gas from the burning lube can end up in the casting and ruin it.
Why is this interesting? Well, most high-pressure die castings use a single piston to inject hot metal into the die. This can put a limit on the practical size of castings. This is because the metal has to flow from the injection point and fill the whole die before solidifying. The bigger the die, the more likely the metal cools before filling the whole thing.
Obviously, this is a massive part—and it would be incredibly difficult to fill this whole die in a split second from a single injection point. You can only run your injection pistons so fast and so hard. Plus, the more metal they’re trying to push into the die, the harder it is to push them quickly. Using two pistons lets you inject more metal at the same time. Key to making this work is ensuring that as the two fronts of molten metal meet, they’re still hot enough to mix properly. Since we don’t see a big ugly seam down the middle of the part (which would be called a “cold shut” in casting parlance), we can assume this strategy is working well.
We’re told a 13,000-ton clamping force machine was required for this part. That’s no surprise, given the sheer cross-sectional area of this part. As the hot metal is injected into the die, it wants to force the two halves of the die apart. This force increases based on the cross-sectional area of the part in question. Thus, to stop the die being forced apart by the injection of hot metal, you need to clamp it shut very tight. Else you get hot metal squirting out the sides—called “flashing” in casting parlance.Â
Also visible are the chill vents on both the top and bottom of the part. In die casting, you want the air inside the die to have somewhere to escape to when the metal is injected. If the air has nowhere to go, it gets into the molten metal and creates air bubbles, known as porosity. These voids weaken the part and are minimized or avoided wherever possible.
To avoid this, you create runners leading to vents in the die, which exhaust to the atmosphere. As metal flows through the die, it eventually reaches the vents, with the air exhausting ahead of the molten metal front. The chill vents have a zig-zag pattern that is used to cool the aluminum and solidify it quickly. You want the metal going into the vents to solidify so you don’t have hot metal squirting out onto the factory floor. The people working in the plant don’t like that.
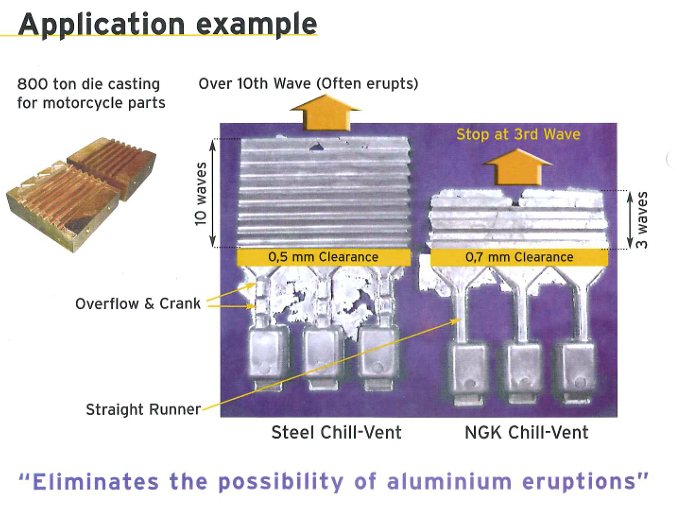
Beyond that, there’s not a whole lot that jumps out at me about the Chery castings. If I’m honest, a big part of that is because they’ve censored a lot of the images. You’ll note that the company chose to sensor areas of the most three-dimensional complexity, where the molten metal has to change direction to fill the complex geometry. Weirdly, they censored the area immediately after the feed-in runners in one shot, but not in another. Odd! The area where metal feeds into the die is critical to casting performance. If it’s so important, though, why not hide it in both shots? Especially as they appear to be the same casting—note the same splotch of burnt lube on the biscuit!
It may be that significant R&D was required to get the die design to flow the metal just right without porosity or early solidification. Chery may not want anyone to see flow patterns in the casting that might teach them something. Alternatively, maybe they’re just hiding the geometry of the final part due to its relevance to their upcoming models. Or maybe these castings are full of defects and they’re hiding the evidence? That’s a long shot, though. Why would they boast if they can’t make the castings work?
In any case, I hope you found these giant castings as interesting as Thomas and I did! Lewin out.]
(Photo credits: Chery Auto, NGK)
Support our mission of championing car culture by becoming an Official Autopian Member.
-
Watch A Tesla Cybertruck’s Rear End Completely Tear Off In This Ridiculous F-150 Durability Battle
-
How Tesla Made ‘Gigacasting’ The Most Important Word In The Car Industry
-
GM Buys Key Tesla Gigacasting Company Out From Under Tesla
-
Why The Tesla Cybertruck’s ‘Gigacast’ Design Seems To Make Inner-Bedside Panel Repairs Easy
-
Here’s Our First Up-Close Look At The Tesla Cybertruck’s Impressive ‘Gigacastings’
Got a hot tip? Send it to us here. Or check out the stories on our homepage.
Hey, we’re all consenting adults here. Do we really need to censor everything here, or did someone’s widdy biddy feelwings get so butthurt?
It’s interesting to see fancy castings coming back into vogue when elaborate (steel) castings were used in steam locomotives, armored vehicles, and other heavy industry in the early part of the 20th century before welding assemblies became more popular. What’s old is new again?
https://penlowry.wordpress.com/wp-content/uploads/2014/01/b282715-5125-c38-loco-integral-cast-steel-locomotive-bed-at-clyde-engineering-blocked.jpg
Maybe they’re just trying to emulate Tesla’s marketing
On a few subreddits I follow people will post pictures of their car ‘is my car actually totalled?’. It’s almost always people with pretty new pretty nice cars with seemingly minor damage that get told that their car is totaled. I feel confident in saying that if a car got hit hard enough to damage a subframe, that car is already totalled, regardless of the manufacturing technique used to make that component.