Large component casting, also known as megacasting, or gigacasting if you’re Tesla, is hot right now, and a major milestone has just been reached. Chinese automaker Chery Auto has cast an entire underbody using a 13,000-ton dual-injection press, and while the result is nothing short of impressive, there are a few good reasons why you probably shouldn’t want a one-piece cast underbody on your car.
I don’t have anything against casting as a process, because it’s produced some incredible stuff. Most alloy wheels on production cars are cast, for example. Megacasting an entire underbody is an incredible feat of manufacturing, just an absolutely awe-inspiring flex of might. I also don’t have anything against the structural soundness of this part, as it’s likely perfectly fine. See, my beef lies in repairability, because large structural castings require a completely different approach to a structure made of stamped parts, one that flirts with disposability.


But Thomas, aren’t other automakers already using cast strut towers? Absolutely, but the big difference there is modularity and repairability. Let’s take the jaw-droppingly gorgeous cast strut towers of the Lexus LC 500 as an example. Those astonishing strut towers are separate pieces, attached to conventional pressed steel front longitudinal members using rivets and structural adhesive. Should an LC 500 end up in a collision that cracks the cast strut tower but doesn’t total the car, that part can be replaced, and if the rest of the structure’s fine, it can remain untouched.
In contrast, if a car with towers and floor all cast as one is in a wreck bad enough to damage a strut tower, that entire underbody is junk. The whole thing. Big aluminum castings don’t take safely to straightening like steel does, and having to replace an entire underbody in the event of a moderate small-overlap or front-quarter collision has a dramatic effect on repairability.
What I’m concerned about is that it’s possible all that Chery Auto has done here is find a way to make a car even more disposable, and if this trend picks up steam, it could have knock-on effects for consumers. While the bulk of every insurance premium covers injury and liability, if casting the entire floor as one from strut tower to strut tower makes a car more expensive to repair and more prone to be written off, it’ll absolutely be more expensive to insure as a consequence. There might be savings on the front end for manufacturers, but savings on the back end for consumers? Hmmm.
Secondly, we need to ask how repeatable this process is. Pressed steel parts have a very high usability rate. Huge castings? Much lower. This 2022 report on megacasting from Ducker Carlisle states that Tesla had a gigacasting scrap rate of 45 percent in 2021.
Huge castings are amazing when they’re warranted. Subframes, suspension arms, drive motor housings, hubs, dashboard support structures, seat frames, if it bolts on, you name it. However, casting an entire underbody in one go seems like a process with downsides for consumers. A car is the second-most expensive thing you’ll buy in your life, so let’s keep them repairable.
Former casting engineer Lewin here. That scrap rate is quite poor, but it’s not quite as bad as you think. Castings are highly recyclable. In fact, within the factory, you could pretty much throw the bad casting back into your melt pot and simply try again. It’s not particularly efficient but the castings aren’t really going in the bin—that metal is absolutely being reused in the plant.
Thomas has given us great insight into the consequences of using big castings. It’s worth noting, though, that they can be a great way to make producing a vehicle cheaper by slashing part counts and the number of required assembly and welding operations. There’s value there that offsets the reduced repairability in my book, but not everyone agrees that reduced repairability is a good thing. That’s very fair.
But more importantly, let’s take a quick look over these castings! A quick note on why this is impressive. Basically, die-casting parts involves squirting metal into a mold. The bigger the part, the harder it is to fill it up with hot metal before it goes cold and freezes off inside. Also, the bigger the part, the harder it is to keep the mold closed. Megacasting is all about making bigger castings than ever. It involves a lot of engineering to make big casting machines and effective dies that work at these scales.
So, this is a huge casting, right? The first thing that jumps out to me as a casting engineer is the double biscuit. See those big round protrusions on either side? Those are the biscuits!
Those biscuits are from where the pistons injected metal into the giant casting die. Hence why they’re round! You can also see a little black scorch on the right-hand side biscuit, where some excess tip lube from the injection piston has burned off. That’s generally nothing to worry about. If it gets too bad, though, the gas from the burning lube can end up in the casting and ruin it.
Why is this interesting? Well, most high-pressure die castings use a single piston to inject hot metal into the die. This can put a limit on the practical size of castings. This is because the metal has to flow from the injection point and fill the whole die before solidifying. The bigger the die, the more likely the metal cools before filling the whole thing.
Obviously, this is a massive part—and it would be incredibly difficult to fill this whole die in a split second from a single injection point. You can only run your injection pistons so fast and so hard. Plus, the more metal they’re trying to push into the die, the harder it is to push them quickly. Using two pistons lets you inject more metal at the same time. Key to making this work is ensuring that as the two fronts of molten metal meet, they’re still hot enough to mix properly. Since we don’t see a big ugly seam down the middle of the part (which would be called a “cold shut” in casting parlance), we can assume this strategy is working well.
We’re told a 13,000-ton clamping force machine was required for this part. That’s no surprise, given the sheer cross-sectional area of this part. As the hot metal is injected into the die, it wants to force the two halves of the die apart. This force increases based on the cross-sectional area of the part in question. Thus, to stop the die being forced apart by the injection of hot metal, you need to clamp it shut very tight. Else you get hot metal squirting out the sides—called “flashing” in casting parlance.
Also visible are the chill vents on both the top and bottom of the part. In die casting, you want the air inside the die to have somewhere to escape to when the metal is injected. If the air has nowhere to go, it gets into the molten metal and creates air bubbles, known as porosity. These voids weaken the part and are minimized or avoided wherever possible.
To avoid this, you create runners leading to vents in the die, which exhaust to the atmosphere. As metal flows through the die, it eventually reaches the vents, with the air exhausting ahead of the molten metal front. The chill vents have a zig-zag pattern that is used to cool the aluminum and solidify it quickly. You want the metal going into the vents to solidify so you don’t have hot metal squirting out onto the factory floor. The people working in the plant don’t like that.
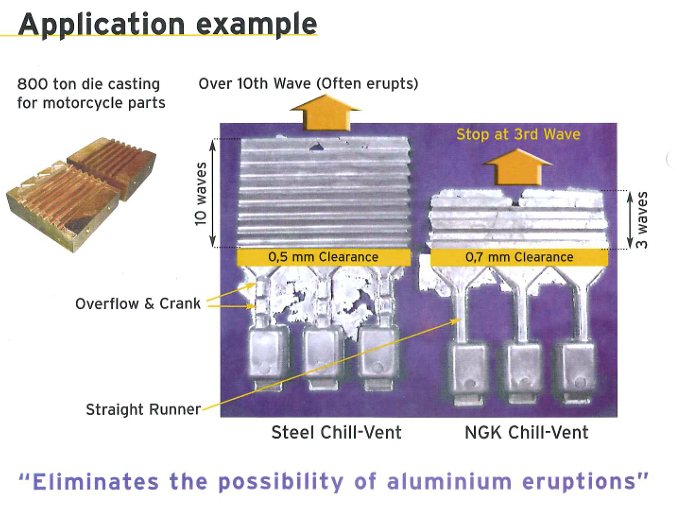
Beyond that, there’s not a whole lot that jumps out at me about the Chery castings. If I’m honest, a big part of that is because they’ve censored a lot of the images. You’ll note that the company chose to sensor areas of the most three-dimensional complexity, where the molten metal has to change direction to fill the complex geometry. Weirdly, they censored the area immediately after the feed-in runners in one shot, but not in another. Odd! The area where metal feeds into the die is critical to casting performance. If it’s so important, though, why not hide it in both shots? Especially as they appear to be the same casting—note the same splotch of burnt lube on the biscuit!
It may be that significant R&D was required to get the die design to flow the metal just right without porosity or early solidification. Chery may not want anyone to see flow patterns in the casting that might teach them something. Alternatively, maybe they’re just hiding the geometry of the final part due to its relevance to their upcoming models. Or maybe these castings are full of defects and they’re hiding the evidence? That’s a long shot, though. Why would they boast if they can’t make the castings work?
In any case, I hope you found these giant castings as interesting as Thomas and I did! Lewin out.]
(Photo credits: Chery Auto, NGK)
Support our mission of championing car culture by becoming an Official Autopian Member.
-
Watch A Tesla Cybertruck’s Rear End Completely Tear Off In This Ridiculous F-150 Durability Battle
-
How Tesla Made ‘Gigacasting’ The Most Important Word In The Car Industry
-
GM Buys Key Tesla Gigacasting Company Out From Under Tesla
-
Why The Tesla Cybertruck’s ‘Gigacast’ Design Seems To Make Inner-Bedside Panel Repairs Easy
-
Here’s Our First Up-Close Look At The Tesla Cybertruck’s Impressive ‘Gigacastings’
Got a hot tip? Send it to us here. Or check out the stories on our homepage.
I look forward to seeing these to turn up for welding repairs in those pakistani sandfloor workshop youtube channels
Great article, even answered my question about why the images are censored before I got to ask it! I learn something new every time I come here and it’s always entertaining. It’s like the old site used to be. Can you guys hurry up and poach Rob Emslie so I don’t have to go back there anymore?
At what energy cost, though? Melting that much aluminum has to be hideously energy-intensive.
I have similar concerns about the Tesla method, even if it’s not taken to this extreme. Yes, that test where they dropped it on the hitch and the broke the casting was contrived, but things like that happen in the real world too. I’ve been in vehicles that drove over a step large enough to land on their hitch. If that has the potential to total your vehicle that’s terrible.
I’m also curious if it would have junked my Corvette when I hit a deer at 60 mph. It penetrated far enough into the front end to have cracked the weld between the front subframe and the impact bar. If that had instead been mounted to a giant casting it probably would have been unrepairable.
I’m sure it’s an impressive technical achievement, but it feels like yet another step down the road toward disposable yet still very expensive (both in terms of money and environmental impact) vehicles.
Remaking aluminum from scrap requires a good deal less than breaking the bonds with raw ore, iirc, its around 70 percent less energy required, but also, it’d be broken into chunks to significantly speed the process up.
Used to do plastic injection molding and we’d do similar stuff with rework plastic that was shredded and used as like new granules
Interesting. I wouldn’t have expected it to be that much easier to re-melt. That does make it much less terrible than I thought.
Yeah, if they tried on the whole part, it’d take a while, but like pop cans, smaller surface area, quicker it goes.
Kinda surprised they don’t try to aggressively collect aluminum really
So, amateur talking here- do we need more injection points, and do we need to heat the mold while we’re filling it? Then kill the heat once we are satisfied that we have a good fill.
I know, I’m j7st spitballing.
Some dies will be preheated by a guy with a big propane torch or similar. However, this only has a minor effect.
The real heating comes from injecting the metal. Each injection to make a part is called a “shot”. Often it takes 3-5 shots to get the die hot enough to make good parts. Probably more in the case of a gigacasting.
Those early shots are full of defects and are scrapped and recycled
another guy talking out of his ass, but wouldn’t induction heating be able to be used to heat up the die and keep it warm through the process?
You don’t always want the entire cast heated. Temperature is also used to control the flow of the molten metal. Albeit this is done moreso with steel and magnesium as those tend to be attracted faster to cold spots.
Imho the reason to reduce costs using gigacasting is to keep the already very affordable cars in CN more affordable / increase the profit margin. The margins on high ends cars are enough to allow for more traditional manufacturing.
Also the life expectancy of these cheaper cars is less than 10 years.
On top of that ; the money saved for buyers absolutely justifies the higher expenses for fixing one of the VERY few that eventually get totaled.
Most cars don’t stop working because of a bad frame, but because nobody wants them anymore because of various reasons ; broken parts which are more expensive to replace or repair than the economic value of the car. Or the risk of having to pay for parts (e.g. 20 year old German cars) is too high so the price gets so low that it almost makes no sense from a technical perspective. But economically you don’t want to pay $10k for a 20 year old Mercedes S-class with 150k miles because the maintenance could easily be more than $10k in the next 2-3 years.
TL;DR; Gigacast more, lower prices of cars, accept higher costs when they get totaled.
A perfect Autopian post. Do I care about gigacasting? Not until today. Do I know more about gigacasting than anyone else I know? I do after today. And I suddenly have opinions on the tradeoffs between repairability and cost efficiency. Cool.
Yeah, but there’s no rust anywhere! The burn mark is close to rust I guess ha ha…yeah, this was interesting and The Autopian rules!
Anecdotal evidence: none of the 22 cars I’ve bought and got rid of would have been scrapped any earlier had the floor pan been a single casting.
One of them had an “unrepairable” bonded aluminium extruding chassis, and that car is still going strong at 27 years old. It was of such minor concern for me that one of my current cars also has an “unrepairable” bonded aluminium chassis.
A few of my ex-cars have been crashed, but by then they were worth so little that any bodyshop repair at all would have written them off.
Cars don’t crash as often as you think.
ReduceReuseRecycle. That’s the last in the line because it’s the least helpful as not every component gets recycled, recycling takes energy, and some materials are degraded with each cycle. Disposable junk. We all pay for this one way or another and it’s about time we stopped loading our debts onto the environment so people can have a disposable bottom barrel POS just because it’s cheaper. It’s unfortunate that cars are such a necessity in many places that it’s not so easy to dispense with them, but this goes for plenty of other items people don’t need.“Repairability”; When was the last time automakers cared about that? It’s the main reason all my vehicles are pre-90’s, next to interest and cost. Haven’t been able to fix my dad’s 2002 and 2006 cars as I don’t fully understand the electronics in them (despite growing up with and interested in computers) and the cramped spaces. I had a terrible time replacing the low-quality power steering line on an old ’91 s15 Jimmy 4.3 and removing the upper exhaust bolts on a much newer diesel truck.
Certainly every OEM I’ve worked for has cared about repairablity. You know why we haven’t had super cheap engines with bonded-on cam covers, front cases and oilpans for the last thirty years? Because you can’t take them to bits to fix them. All the machining and fasteners we could delete, but we keep it all so in twenty years you can fit a new oil pump/cam/crank.
All engineering is a compromise, and until you see what we could have given you you have no idea how much serviceability we’ve engineered in.
Not that we really care, we just don’t want to scrap a whole new car if it gets to the end of the line and it’s got a duff alternator or whatever.
“When was the last time automakers cared about that?”
Auto makers probably car 100x more about it than consumers do. THAT is the real reason it isn’t a focus for car makers. Consumers care way more about price.
I like how we want from we’ll 3d print the whole car to robots will weld everything together to save labor to now just cast it all in one piece in less than a decade.
I mean if they can make a machine that poops out whole car structures, it should be cheaper, like under $20k, so insurance still shouldn’t be so bad. Think most cars are at the point that if it’s over 5 years old and the airbags go off it’s totaled anyways.
“Why would they boast if they can’t make the castings work?”
Its what they learned from Tesla.
Beind disposable is not an issue if you have a solid recycling program. If you can detach the battery from the underbody you end up with what’s essentially a very heavy soda can to recycle. Insurance companies can offset a lot of the underwritting costs just by recycling batteries and underbody (and rest of the body for that matter), so in the end of the day the cost of insurance for consumers may be even lower than today.
I mean…. It probably won’t happen like that, but there it is the economics
This was my thought. The other side of that coin is where the energy and resource consumption that comes with production and where that recyclability leads to higher resource consumption than building something that is repairable.
it’s not like the replacements are made energy free. I would assume it is awash or very close between building something disposable and building something repairable and the spares. Also, energy will go into the repair action itself. I am not advocating either way, I like repairing and tinkering with stuff.
This is my thought. Where is that line. I like tinkering myself too but that isn’t the majority of the population
If it’s an inexpensive car not intended to last over 10 years, I’m fine with it being considered disposable and recyclable.
If this was to be used in a sub $10k city EV in the US, I love it. If it’s intended to be a $50k+ mid-sized car, I hate it.
There’s a whole other issue of emissions and energy use in production and recycling, hopefully these become like other mature technologies, where we previously stretched their capability to the logical conclusion, and then went back to using them only where it’s best instead of everywhere that’s possible.
No, the insurance costs will not be lower.
If the casting is severely cracked or damaged, the car is totaled.
A bare aluminum car shell might weigh 1000 pounds with doors, hood, trunk. If you completely stripped every bit of plastic, copper, steel and and everything else not metal out of the shell, you’d be lucky to get $0.50/pound – or $500. Except that would require an enormous amount of labor to achieve, so you’re going to end up with “dirty aluminum” scrap, which right now pays around $0.20/pound.
Lithium battery recycling is currently very difficult, and prices are all over the place. But a typical 1000 pound EV car battery might yield anywhere from $400-$1000 in scrap value as of this moment.
So instead of paying a body shop $5000 to replace the floor pan in a car after someone runs over a brake rotor on the highway, they now get to replace the entire car for $40,000, and get back only pennies on the dollar for the rest of the vehicle.
Recycling is largely a scam foisted onto the public by private companies looking to dodge their responsibilities and make people feel good about their continued consumption of stuff they don’t need that is designed for short lifespan. It takes energy to recycle things, separating can be labor intensive, it can be messy, many materials cannot be practically recycled, and others degrade in quality with every cycle. It’s like many municipalities with recycling programs are run so the citizens feel better, but it mainly ends up in a landfill, especially now that offshore poor countries no longer want the stuff we packed and shipped by land to ports where they were repacked and sent over in giant container ships burning bunker oil. Who’s separating the different types of plastic from the piles taken out of smelly, filthy bins? Many of those plastics can only be recycled in rare facilities likely far away from point of collection so that it has to be transported to higher cost, and there’s little economic incentive to do so as it’s cheaper to use virgin materials in the first place. Scrap aluminum isn’t worth much, either, and in the case of something like this logistically-challenging massive casting, everything non-aluminum needs to be cleaned off of it—including every clip, adhered undercoating, sound deadening material, etc. Who’s doing that? Who wants to pay for it? Sounds pretty messy. Is it burned off? Chemically removed? Where is that material recycled? I wish they would start including true recycling costs into the purchase prices of this trash, but oh no the economy! How would the poor billionaires sustain themselves if we aren’t always “upgrading” for worse stuff with highly abbreviated lifespans engineered in!
I agree with what you say to some extent. I think the odd thing about these recycling programs is that the most valuable things that go into a recycling bin (aluminum cans) are picked out by scavengers before the trucks come by to pick it up. Aluminum cans go for 35 to 40 cents per pound (depending on quantity recycled) at a for profit facility near me. An entire neighborhood’s poundage of aluminum cans put to the curb must be worth it to go pick through it for at least a bunch of people.
I talk to one of these scroungers from time to time as he checks the dumpster at my work and says it worth it as a side hustle (never gives me numbers). Now that I know what he’s collecting I just leave it next to the dumpster so he has an easier time to pick it up.
Either way it seems better to recycle whatever can be recycled than to just send it straight to the landfill.
I have a spot to store a year or so’s used aluminum cans and bring them to the place that pays me and get around $200 for probably 2 hours of work.
The problem is, the value in aluminum cans is not in the metal but in the return value which is essentially a tax levied on the cans themselves. I’m not saying this is a bad thing, because it definitely succeeds in mitigating littering, but those cans may still end up in a landfill.
I’m in a non deposit state. This is strictly private company pays me going rate per pound. I assume they aren’t paying to take a loss.
Edit to add that I do occasionally take trips to New York state and have considered taking the cans there for the 5 cent deposit but the cans can’t be crushed and the amount of space they would take up doesn’t make sense.
I think Newman and Kramer may be able to help you make it work…although they did it from NY to Michigan
“KRAMER: (realisation) Mother’s Day.
NEWMAN: The mother of all mail days!”
“At ten cents a bottle and ten cents a can, we’re pulling in five
hundred dollars a man. Nine thousand, nine hundred and ninety-eight bottle and cans in
the truck, nine thousand, nine hundred and ninety-eight bottles and cans.
We fill up with gas, we count up our cash!”
I still separate stuff even though I know it’s 98% likely none of it actually gets recycled. At my old house, anything metal that got put out front was gone in hours and once even as I was walking away from it. Helped him load whatever it was (some kind of old cast-iron-heavy heater that POs left behind) and was glad for it as it was otherwise too heavy for trash pickup. It was especially nice to know that it would at least be recycled and I didn’t have to bother doing anything more than leave it at the curb. Even better, when I was getting rid of my engine crane and stand, the guy who stopped said he was actually going to use them. I hate things going to waste and didn’t want to deal with CL or anything to get a few bucks.
Yeah, it’s amazing what people will pick up free…I gave away LAVA ROCKS…somebody dug them out of the flower bed and put them in trash bags. They were definitely a garden person so I knew they would use them. Also, I’ve put out so many various things on the curb over the years that were still useful and they always got picked up. There was an old motorcycle engine grown into a tree a little bit that came w/ the house and I put out an ad for free and somebody got it…obviously more valuable as a metal engine than lava rocks ha ha
One of the things I miss most about my old place was being able to put stuff out for someone to take. Sometimes things just aren’t worth the trouble to try to sell (or I lack the time, like with my engine crane and stand), but they’re still good to someone (probably stems from when I was a kid and I lived near an architect who was always tossing out models and parts and I’d pick that stuff up on my way home from school on trash day to make things with—my mother was very patient! I also built a couple of bikes out of junk for neighborhood stunt riding without wrecking our regular bikes and a whole toy line using various junk of two warring factions of pipe cleaner figures of humanoid numbers and letters). Furniture is a big one I still see all the time. If I was in poor financial shape and needed to furnish a place, I’d pick up furniture for free off the side of the road. I frequently see decent quality solid wood old furniture people don’t want anymore (even stuff 200 about years old). With some imagination and work, they can be updated and modified without a ton of tools and I did that stuff in an apartment living room and outdoors. In the end, you have a piece that you have a personal stake in—supercharged IKEA effect with better quality for much cheaper (especially if you don’t have to replace hardware as that’s the biggest expense) and it can always be modified again if you change your mind. Of course, you never what you’re going to find or when. Anyway, that’s veered off the subject.
Lewin, you talk about the chill vents, but don’t mention pulling vacuum?
I probably should have! But not all chill vents use vacuum.
Suspect, the larger the cavity, the more the need.
So basically the factory that has been making Hot Wheels cars, just scaled up their dies and are making them full scale.
Remember when explosive hydroforming was the big thing? Whatever happened to that?
Still use it for lots of production parts. Fun fact, the nozzles jackets on certain reusable rocket engines are explosive formed.
If castings reduce costs for the manufacturer, they’ll totally pass those cost savings on to us, the consumer. Right?
We’re passing the savings on to you*!
*Savings passed to shareholders. To pass those savings along, we’re offering higher prices for consumers and lower wages for employees.
Yes, eventually. That’s how free markets work. Tesla is the perfect example. They cut costs, but kept prices high until the other OEMs started to catch up. Then they aggressively cut costs to maintain market share.
I believe they just wanted to show that they can engineer something like that.
I am no expert, but I beleve that this kind of casting would kill those variable architectures, that allow different models being larger and wider accordingly the application.
Each model would require a different die, and while some stamping will be different today, but this is completely different.
I think, again, I am no specialist, but would like to hear from someone with more knowledge about.
You can still build a load of cars on the same platform, they’ll just all have the same wheelbase and width. You can have your SUV, SUV coupe, pickup all on the same casting.
You could also do a sedan, estate, coupe and a convertible if anyone cared about making those.
While size is restricted, there are multiple bodies that could be used on the single platform and the platform could very likely be used for multiple generations.
I like that it looks like they’re pixelating the underbody’s privates
The fact that someone put at smiley face on an image with censoring makes me feel uncomfortable.
People in East Asia are all used to pixelated photos and videos.
The full thing looks like an owl with its parts censored.
What do you think the chill vents are for? Ha ha
I was diving on the interstate at night when the car in front of me changed lanes revealing a kitchen sink in the road directly in my path. I had no outs, there were cars on both sides and one close enough behind me that slamming my brakes would have killed us both. I had no choice but to hit the sink….hard. Luckily the only damage was to the transmission cross member (it was rwd) which was pretty severely bent but also replaced with one from the junkyard for less than $100. I bet that sink would have obliterated one of these castings and totaled the car.
This made me think about the time my mom drove over a curb in her Volvo. I was only a kid so I don’t remember all the specifics, but I know the motor mounts had to be replaced and there were some bent suspension components. Maybe more. The car was far from totaled though, was fixed, and that was that. (She’s never hit a curb since either).
I’m not saying a huge casting would necessarily have broken in that specific situation. But I can definitely see circumstances where a relatively minor accident could total a car with only one big cast making up the undercarriage.
Wow, she did that to a Volvo with a curb. That’s impressive. She must have really been moving. I mean tell me your Mom was a speed demon without telling me your Mom was a speed demon.
It was a newer Volvo (then), a 2001 V70 T5. Didn’t help it had the bigger wheels and lower profile tires. My dad is the speed demon though, I’ve never met another soul who drives as fast as he does. The first time I broke triple digits on the speedometer was when I had my permit, with my dad egging me on from the passenger seat.
I had one of those, same year and everything. I loved that car. Also your dad sounds like my kinda guy.
I loved that car, I think even my dad kinda wishes we had kept it around. It had the most comfortable seats of any car I’ve ever driven to this day, and felt so planted and stable when driving in heavy wind and rain. My dad is definitely a character, and I was the envy of all the car guys I knew in high school because he didn’t care what automotive shenanigans I got up to, unlike most people’s parents at the time.
Sounds like the dad that took all the kids out to the school parking lot to do donuts on snow days. All the kids like that dad
I find it interesting that they can’t dissect the casting into two halves (and bolt them together), which might increase the repairability.
As these castings get larger, recycling them becomes easier. So, the “throw away” concept, perhaps, isn’t the end of the world. Plus, I, personally, am not a fan of driving vehicles after that large of an accident, fixed correctly or not. If prices can be dropped, and recycling can be increased, throwing cars away isn’t the end of the world. Absent those two things, though, I’m onboard with “FTFY” approach.
This is really cool to see though I agree I have concerns about what it means for repairability for the consumer. I’m confused as to why they’re getting the dubious credit for leading a negative trend though when Tesla has spent so much press promoting the process. Is Tesla’s gigacasting somehow less encompassing or something?
Teslas aren’t using one single casting. They cast the front and rear frame, then attach those to the battery. Same issues, I don’t think you can remove a front casting that gets crashed from the battery and then attach a new one
Tell your non-college bound offspring to consider heli-arc welding as a profession. It’s gonna be a bull market.
They should one-up Tesla by calling this teracasting. (Not to be confused with pterocasting, which is what you’d call it in aviation.)
LOL the Tesla worshippers on the internet seem to think that this casting stuff was invented by Musk and is exclusive to Tesla.
That’s why they create new terms for existing things. Sure, people had been casting some large components for some time, but this is gigacasting, which is new and entirely different…somehow. The gigafactory is the first of its kind! (That kind being factories that are called gigafactories.)
Onward and upward until the entire car is made in a single quettacasting.
I think by that point, it’s actually one casting for several cars, and they cut them apart after the fact.
Maybe this can extend in to the kit car market, and I can get my my kit car on sprues just like an old plastic model!
The 1957 Lotus Elite had the entire load bearing chassis moulded in a single piece out of fibreglass.
Any of the modern carbon fibre chassis cars (like the BMW i3 DT loves so much) are also a single lump of plastic, just like a model kit.
With all of that blurring, I thought it was made in Japan.
Thumbs up to the new giga car porn
Are we going to end up on some sort of Aluminum Casting Offender list by having these pixelated images on our computers? Are we going to have to report to our local diecasting plant that we live near by? My late father, the robotics engineer and diecasting wizard, would be having a field day over all of this.