You’ve seen a bunch of Tesla Cybertruck Reviews, and I bet you’ve seen some cool graphics that Tesla has released, but nobody has really gotten under the skin of the new Cybertruck. Which is why these new images from the manufacturing experts at Munro & Associates are so cool. Let’s take a peek and see what these pictures can teach us.
If you’ve been hanging around automotive blogs over the last few years, you’ve heard plenty of mentions of Tesla’s Gigacasting technology. If you’ve worked in the casting industry, you’ve probably been hearing scuttlebutt about the company’s plans for big castings as far back as 2016 or earlier. The technology has already been put to extensive use on Tesla’s existing lineup. Now, we’ve gotten our first look at those used on the Cybertruck, thanks to photos from Munro & Associates.


The company is known for its automotive benchmarking teardowns, which help engineers understand what other automakers are doing. Munro is yet to share its full insights on the Cybertruck, but these new photos show us that their work on the long-awaited model is already underway. Before we dive into the castings and what we can see, let’s talk about why Tesla’s Gigacasting tech is important in the first place.
Some Background On Gigacastings
There are big gains to be had from making larger cast components for automotive use [Ed Note: It’s worth mentioning that casting is not a new process in vehicle bodies. It’s been used for things like strut towers for many years, it’s just that Tesla has chosen to make the castings larger than was typically seen before, and then create a buzzword: Gigacasting. -DT]. High-pressure die casting can be a very economical way to make geometrically complex parts. While it costs a great deal to create a casting die–this is the big metal thing that has a cavity shaped like your part and that you pour molten aluminum into–once produced, a single die set can be used to make hundreds of thousands of parts with proper care and maintenance. Casting machines can also churn out parts very quickly, with cycle times often under two minutes.
Being able to produce a single large subframe or housing in aluminum in a single operation can be a lot quicker and cheaper than fabricating and welding one up from separate parts, assuming you can produce it in good quality and with a minimum of waste. Casting has long been a popular choice for things like oil pans and gearbox housings. Tesla’s grand move was to focus on making larger parts in single-cast pieces to speed up manufacturing and assembly.
[Ed Note: This all came after manufacturing experts at Munro and Associates ripped on the Tesla Model 3’s overly complex rear body structure:
Notice how many parts are welded together, there! -DT]
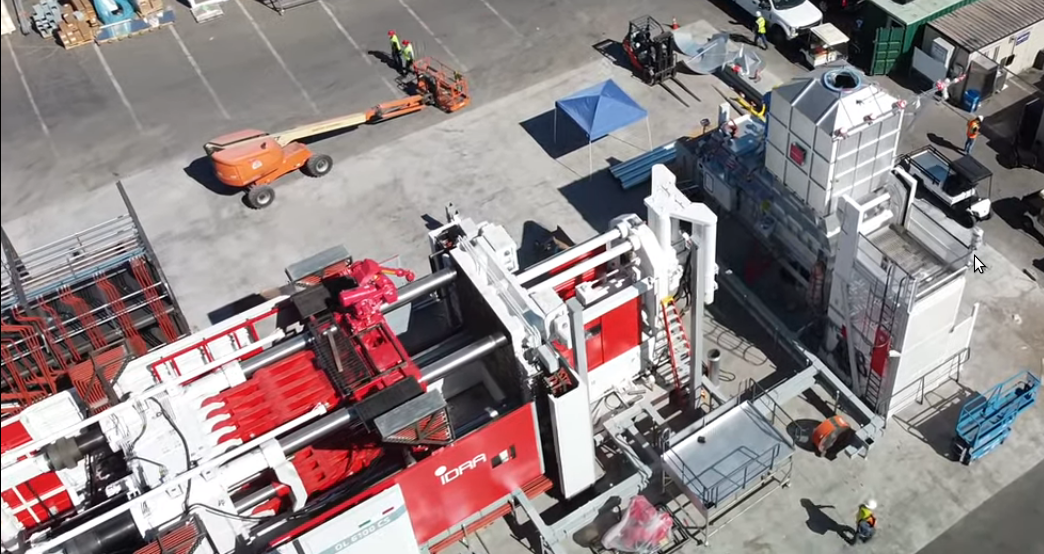
Tesla has credited its Gigacasting technology with huge savings in cost and complexity. The company has noted that the use of large cast aluminum parts on the Model 3 helped eliminate 600 robots from the production line, and also helped shave down the weight of the final design.
Gigacasting is so named for the fact that it involves castings much larger than was previously considered practical in the die casting industry. To achieve this, Tesla needed casting machines with greater clamping force than ever before. This is because as molten metal is injected into a casting die, it tries to force the two halves of the die apart. If it succeeds, molten metal squirts out the sides and the casting is ruined.
The clamping force required depends on the cross-sectional area of the casting, and the pressure of injection of the molten metal. Tesla’s methods, which produce much larger parts, rely on casting machines with clamping forces from 6,000 to 9,000 tonnes. In contrast, during my career as a casting engineer at a major automaker, the largest castings were made on 2,500 tonne machines. As a further guide, Tesla’s casting machines can use up to 80 kg (176 pounds) in a single shot of molten aluminum, around four times as much as the typical casting machines I saw in my career.
A Look At The Cybertruck’s Castings
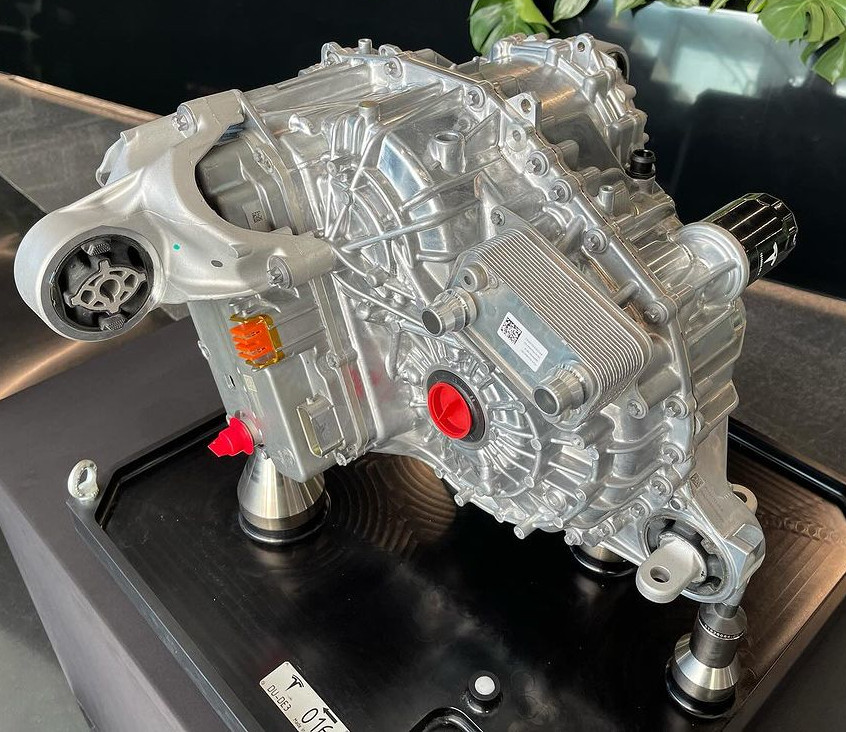
In the case of the Cybertruck castings photographed by Munro & Associates, one thing sticks out. The two smaller castings, which aren’t really in the “Giga” size range, both have beautiful surface finishes. They are very smooth and clean, with no visible burrs or lumps and nice dull sheen. This indicates the dies used to cast these parts are very new. They’re probably within their first 10,000 shots or so, given that production has just begun. “Shots” is casting terminology for the number of times metal has been fired into the die to make a part. Older dies with more shots produce less attractive parts, as thermal cycles begin to take their toll.
Heat check on an aluminum casting made with a die that has produced over 100,000 parts. Note the fine cracks evident in the surface, and the larger metal blobs where the die surface has ablated away. Credit: Lewin Day
Heat check on the tool steel of a die that has produced tens of thousands of parts. This surface cracking transfers to the parts when aluminum is injected into the die. Credit: Lewin DayÂ
Notably, the castings lack any evidence of “heat check,” a casting phenomenon where fine cracks occur in the surface of a casting die after many tens of thousands of shots. This is caused by the tool steel of the die going through many thermal cycles. As molten metal hits the die, it heats the surface up. The die then cools as the part solidifies, and continues to do so once it is removed. Often, a fluid quench is used to then cool the die further to get it in the right temperature range for the next shot. This heating and cooling causes tiny cracks to form in the surface over time. These cracks are then visible on the surface of cast parts. A die can be welded and polished to restore a smoother surface, but the heat check will eventually return. Often, they have no major impact on a casting’s performance and are ignored if they don’t cause leaks or other failures in the part. They are merely indicative of a die that has been in service for a long time.
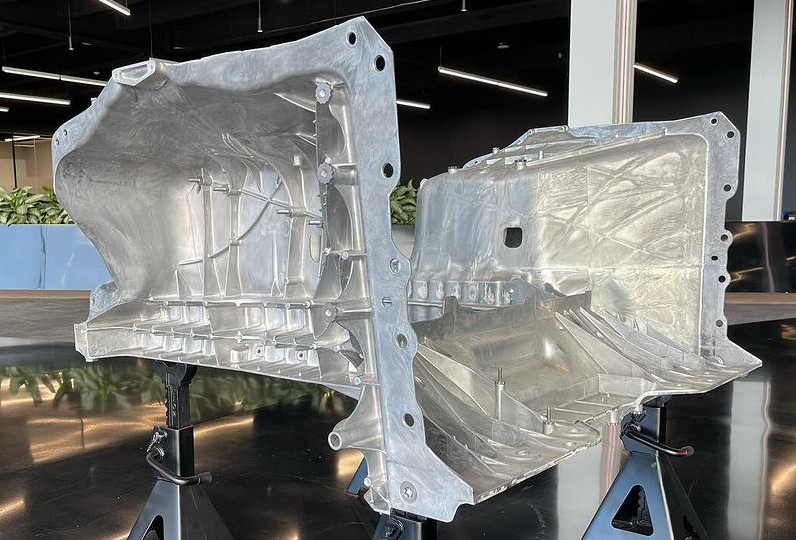
The most interesting part, however, is the larger gigacasting. The sheer size of the part is obvious. With the limited resolution available in the Instagram photo, it’s difficult to get the best idea of the surface finish, but it still appears largely smooth and free of defects as per the smaller parts. In places, it appears that the sheer size of the die may mean that the metal is cooling more during casting, as it takes time to flow into the huge cavity. We can see this in places where the strengthening ribs show through on the back face of the casting. The fact these are visible like this suggests a temperature variation or different rate of cooling in these areas where the ribs meet the thin wall section. This is not inherently a bad thing, just a hint at what may be going on as aluminum flows into this very large casting.
If you’re wondering where this casting sits in the vehicle, it appears to be a major part of the Cybertruck’s front end. If you compare it to the photos of the Cybertruck’s front suspension in our recent extensive explainer piece, you might get an idea. The ribs and standoffs line up with the front suspension mounts for the upper control arm and the shock absorber top hat.
It's massive – no way this thing is less than 60k. Finally got the tire dimensions pic.twitter.com/mTnXJC0UxA
— Devon Guerrero (@DevonGuerrero) November 25, 2023
Without being able to see the die from all angles, it’s difficult to spot features like marks from the ejector pins that help push the finished casting out of the die. However, based on the shape of the casting, we can make an educated guess about which way it comes out of the casting machine. Die casting machines have a movable “ejector” die and a stationary “cover” die. When making a new part, the ejector die is closed over the cover die, and a large locking arm clamps them together. Metal is injected, allowed to cool, and then the ejector die is pulled back, taking the casting with it. At this point, ejector pins push out of the ejector die, ejecting the casting to be grabbed by a robot arm or other mechanical means.
Looking at this casting, the section on each side that corresponds to the wheel wells has a taper, or draft angle, which allows it to be smoothly ejected from the die. While each wheel well area has several strengthening ribs and other undercut features, these are likely formed by “cores” which are movable parts on the ejector die that can be inserted for casting and retracted to allow removal of the finished part. In the orientation shown, the side cores would only have to retract slightly to clear the strengthening features in that area. If the part was put in the die the other way, the cores would have to retract further to fully clear the inner wheel wells. Generally, designing movable cores into a die is tough and it’s easier if you can give them a shorter stroke to clear the part for ejection. I may have gotten this backward, but without being able to inspect both sides of the casting for ejector pin marks, it’s kind of hard to tell.
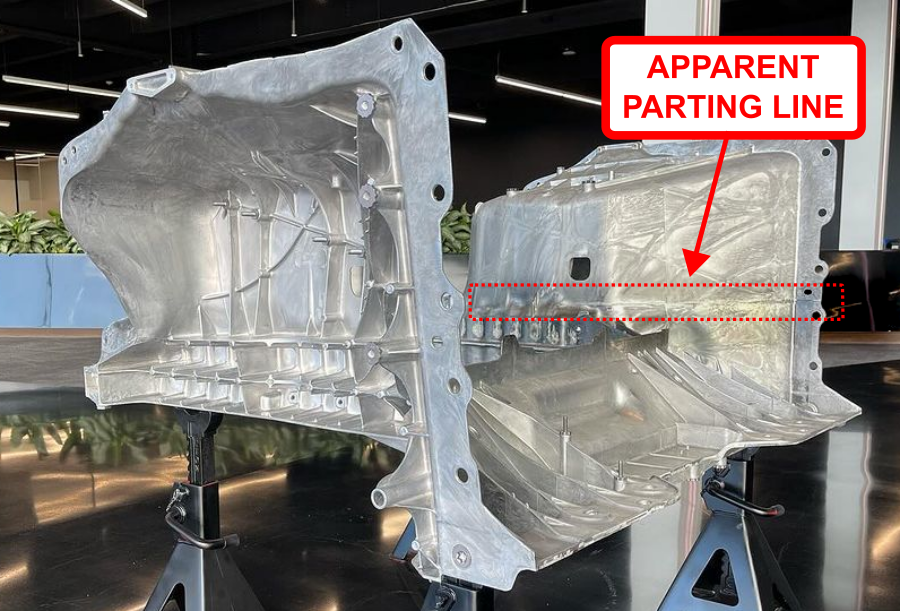
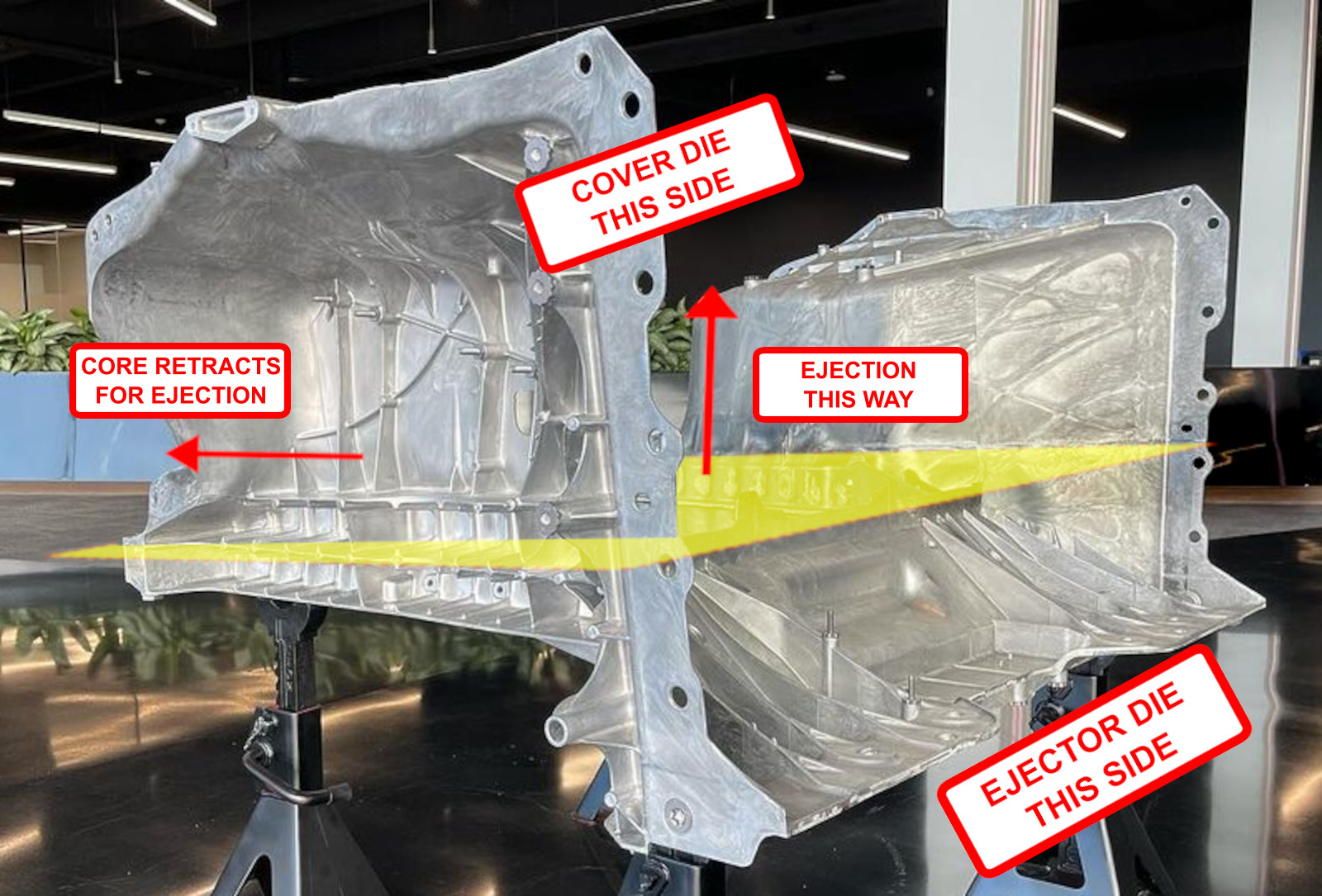
Cybertruck castings at Giga Texas today! All of the castings from Friday are gone, but a large new batch is out in force today! pic.twitter.com/vcgUUAAxae
— Joe Tegtmeyer ???? ???????????? (@JoeTegtmeyer) November 13, 2023
Moving beyond casting minutae, photos show us that Tesla has been producing these parts en masse. They also show us further gigacast parts that are likely part of the Cybertruck as well. Relative to vehicles and people pictured, it’s easy to see just how big these giant castings are.
Indeed, that’s the whole point of gigacasting. It follows the same engineering strategy as Tesla’s EV cooling system we explored relative to Porsche’s effort last week. This is an example of integration. A typical subframe would need multiple sheet or tube steel parts to be fabricated, which would then be assembled in a jig and welded together. Even for a simple subframe, this manufacturing process quickly involves multiple stamping machines and robots to do the job. Instead, by casting it as a single large part, the entire thing can be made in under two minutes in a single casting machine, with maybe a robot or two required to remove the parts or spray coolant on the dies.
Simplifying the manufacturing process saves money in terms of labor, equipment, and time. Of course, achieving this requires great investment. Castings like these simply didn’t exist years ago. Back in my time as a casting engineer at an automotive plant in 2016, whispers were on the air about Tesla’s new giant castings. Back then, they were an interesting R&D project with great knowledge. Now, they’re a unique technological edge that other automakers are eager to bring to their own production lines.
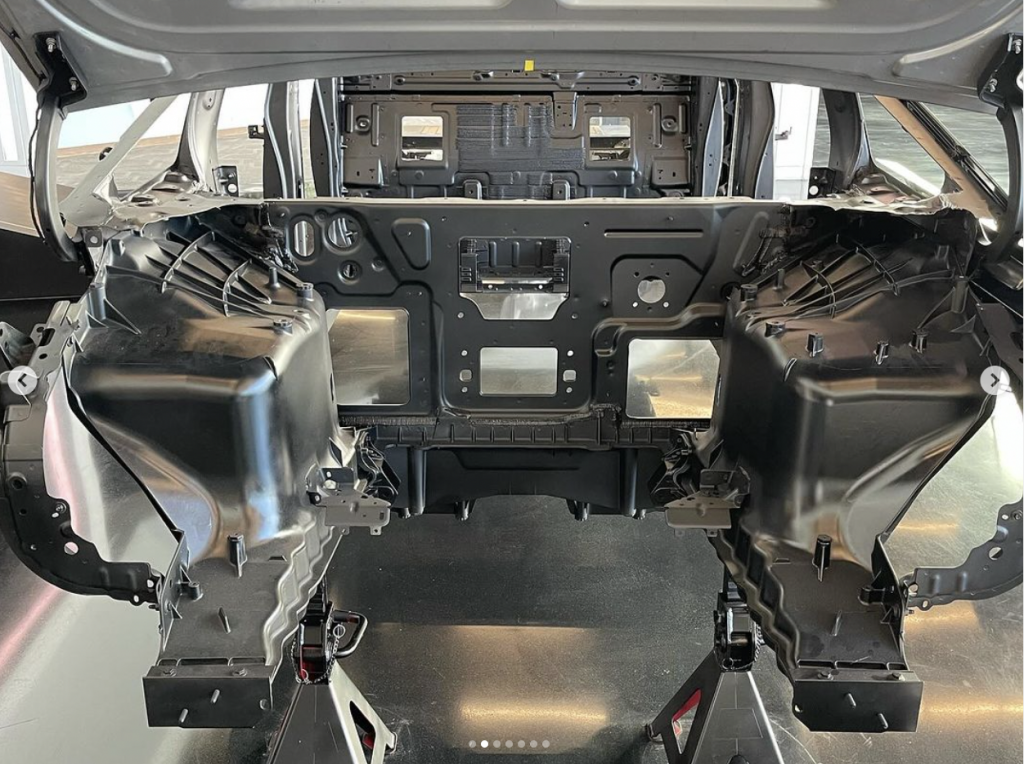
It bears noting that Tesla’s process isn’t without flaws. Some of the company’s cast parts have shown embarrassing aesthetic and casting flaws, and Tesla’s quality record has sometimes left something to be desired compared to its competitors. However, the company is now producing cars in their millions and seems to be getting the hang of the job.
Update: The owner, Nizar, has sent more photos – which reveal serious cold flow or other temperature problems.
Any intern at my old plant would be able to spot these, day 1!
Note the black marker, placed by owner to track crack growth. pic.twitter.com/oxPNwaidv2
— Lewin S. Day (@rainbowdefault) August 30, 2023
Casting problems caused by temperature issues visible in a 2023 Tesla Model Y. The crack appears to be a case of cold shut, where two fronts of molten metal cool off before fully merging in the die.Â
Tesla wasn’t the first automaker to cast parts of automobile bodies, but its supersized castings have drastically cut the number of parts involved in the assembly of its vehicles. It could give Tesla a serious lead over its rivals in terms of cutting the costs of its vehicles, at least until the rest of the industry catches up. As a manufacturer, Tesla may have its quality issues, and it may have gotten many things wrong (looking at you, yoke). Regardless, it’s clear that there is some very smart engineering going on to speed Tesla’s manufacturing and cut costs to the bone.
Image credits: Sladen CC BY 3.0, Munro & Associates via Instagram, Tesla
Wow. A great article with substance. Glad I found my way here from Jalopnik lol.
“Tesla has credited its Gigacasting technology with huge savings in cost and complexity. The company has noted that the use of large cast aluminum parts on the Model 3 helped eliminate 600 robots from the production line”
Even the robot’s jobs aren’t safe!!
Maybe they need to unionize? Or would that be networking
First the robots unionize, then they revolt, then the next thing you know humanity is armageddoned down to 50,000 people on the run for their lives in a rag tag fugitive fleet searching for a new home.
Hellooo Mars!
I’m curious what the fatigue life of these large relatively thin AL castings is when used in high torsional load locations in such a heavy vehicle. At 100k miles will the subframes be cracking whenever they are loaded up from a large suspension articulation?
Very interesting point. Unlike steel, aluminium can’t really be made to last forever in fatigue conditions.
A few random thoughts.
Repairability of large castings (might never be required):
How many cars are actually crashed to an extent that will damage these castings? 1,2 or 3%?
How many cars that are crashed to this extent are actually being rebuilt?
Could the number be as low as 0.2% when combined?
Why should I pay for repairability when I will most likely never need it?
Recycling of large castings (will be required at some point):
These huge casting can simply be shreded and cast again. More and larger castings will lead to more and easier reuseability.
Reuseability/Recycling of EV batteries:
A cluster of cells make up a module and a cluster of modules make up a pack.
I already see a near 100% reuse of undamaged packs, modules and cells after accidents for all sorts of purposes.
A battery pack, module or cell with 65% capacity (after 250.000 miles) still has great value as stationary energy storage and at the end, they can be 95% recycled.
See: https://li-cycle.com/
Adding to above that the latest generation of lithium iron phosphate batteries are both safer and require less/no rare metals makes me realize that Beatles were right:
“It’s getting better all the time”
exactly.
Thanks Autopian and Lewin! I was just asking for this the other day so cool coincidence.