You’ve seen a bunch of Tesla Cybertruck Reviews, and I bet you’ve seen some cool graphics that Tesla has released, but nobody has really gotten under the skin of the new Cybertruck. Which is why these new images from the manufacturing experts at Munro & Associates are so cool. Let’s take a peek and see what these pictures can teach us.
If you’ve been hanging around automotive blogs over the last few years, you’ve heard plenty of mentions of Tesla’s Gigacasting technology. If you’ve worked in the casting industry, you’ve probably been hearing scuttlebutt about the company’s plans for big castings as far back as 2016 or earlier. The technology has already been put to extensive use on Tesla’s existing lineup. Now, we’ve gotten our first look at those used on the Cybertruck, thanks to photos from Munro & Associates.


The company is known for its automotive benchmarking teardowns, which help engineers understand what other automakers are doing. Munro is yet to share its full insights on the Cybertruck, but these new photos show us that their work on the long-awaited model is already underway. Before we dive into the castings and what we can see, let’s talk about why Tesla’s Gigacasting tech is important in the first place.
Some Background On Gigacastings
There are big gains to be had from making larger cast components for automotive use [Ed Note: It’s worth mentioning that casting is not a new process in vehicle bodies. It’s been used for things like strut towers for many years, it’s just that Tesla has chosen to make the castings larger than was typically seen before, and then create a buzzword: Gigacasting. -DT]. High-pressure die casting can be a very economical way to make geometrically complex parts. While it costs a great deal to create a casting die–this is the big metal thing that has a cavity shaped like your part and that you pour molten aluminum into–once produced, a single die set can be used to make hundreds of thousands of parts with proper care and maintenance. Casting machines can also churn out parts very quickly, with cycle times often under two minutes.
Being able to produce a single large subframe or housing in aluminum in a single operation can be a lot quicker and cheaper than fabricating and welding one up from separate parts, assuming you can produce it in good quality and with a minimum of waste. Casting has long been a popular choice for things like oil pans and gearbox housings. Tesla’s grand move was to focus on making larger parts in single-cast pieces to speed up manufacturing and assembly.
[Ed Note: This all came after manufacturing experts at Munro and Associates ripped on the Tesla Model 3’s overly complex rear body structure:
Notice how many parts are welded together, there! -DT]
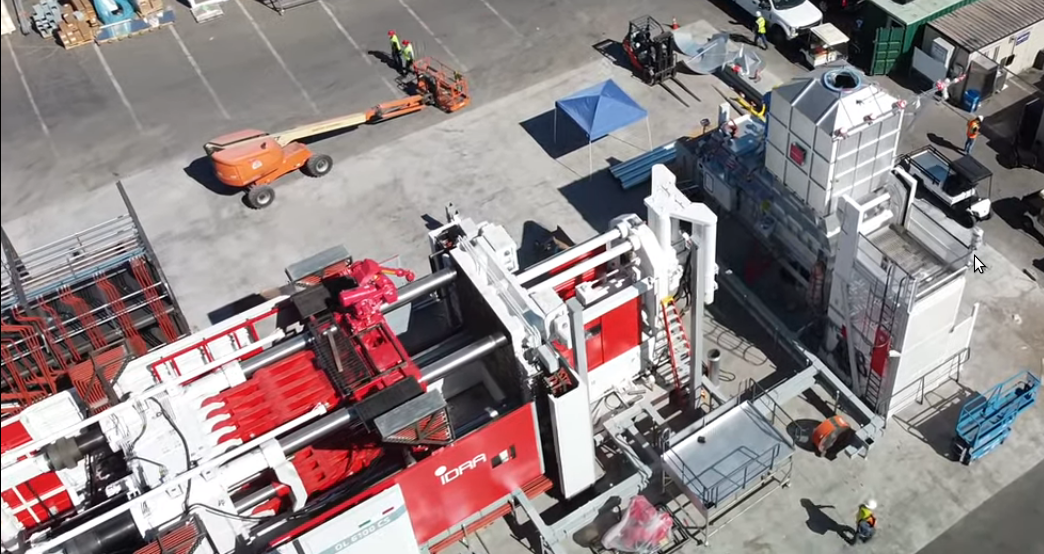
Tesla has credited its Gigacasting technology with huge savings in cost and complexity. The company has noted that the use of large cast aluminum parts on the Model 3 helped eliminate 600 robots from the production line, and also helped shave down the weight of the final design.
Gigacasting is so named for the fact that it involves castings much larger than was previously considered practical in the die casting industry. To achieve this, Tesla needed casting machines with greater clamping force than ever before. This is because as molten metal is injected into a casting die, it tries to force the two halves of the die apart. If it succeeds, molten metal squirts out the sides and the casting is ruined.
The clamping force required depends on the cross-sectional area of the casting, and the pressure of injection of the molten metal. Tesla’s methods, which produce much larger parts, rely on casting machines with clamping forces from 6,000 to 9,000 tonnes. In contrast, during my career as a casting engineer at a major automaker, the largest castings were made on 2,500 tonne machines. As a further guide, Tesla’s casting machines can use up to 80 kg (176 pounds) in a single shot of molten aluminum, around four times as much as the typical casting machines I saw in my career.
A Look At The Cybertruck’s Castings
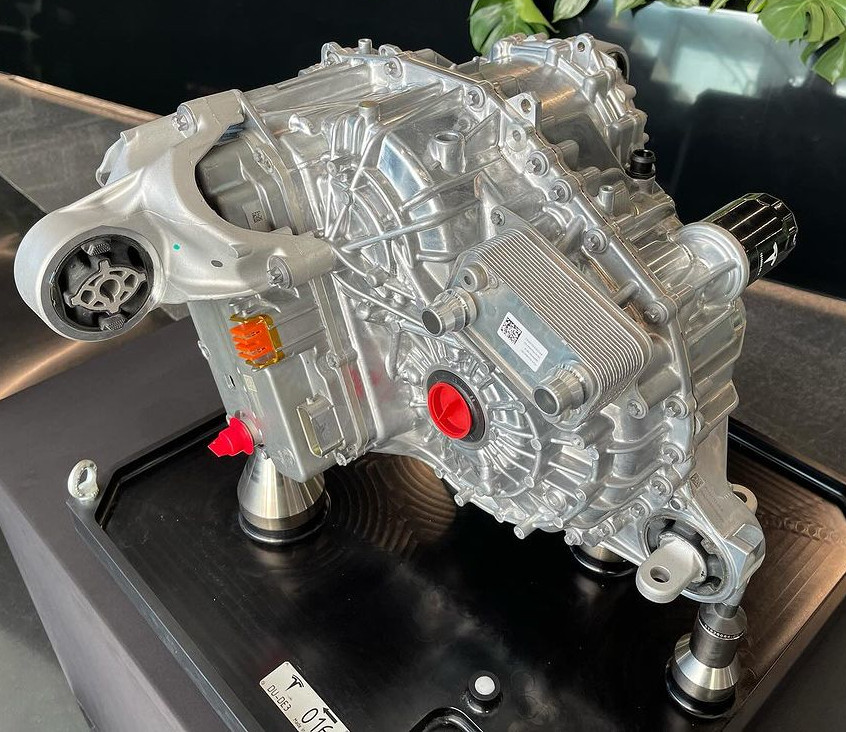
In the case of the Cybertruck castings photographed by Munro & Associates, one thing sticks out. The two smaller castings, which aren’t really in the “Giga” size range, both have beautiful surface finishes. They are very smooth and clean, with no visible burrs or lumps and nice dull sheen. This indicates the dies used to cast these parts are very new. They’re probably within their first 10,000 shots or so, given that production has just begun. “Shots” is casting terminology for the number of times metal has been fired into the die to make a part. Older dies with more shots produce less attractive parts, as thermal cycles begin to take their toll.
Heat check on an aluminum casting made with a die that has produced over 100,000 parts. Note the fine cracks evident in the surface, and the larger metal blobs where the die surface has ablated away. Credit: Lewin Day
Heat check on the tool steel of a die that has produced tens of thousands of parts. This surface cracking transfers to the parts when aluminum is injected into the die. Credit: Lewin DayÂ
Notably, the castings lack any evidence of “heat check,” a casting phenomenon where fine cracks occur in the surface of a casting die after many tens of thousands of shots. This is caused by the tool steel of the die going through many thermal cycles. As molten metal hits the die, it heats the surface up. The die then cools as the part solidifies, and continues to do so once it is removed. Often, a fluid quench is used to then cool the die further to get it in the right temperature range for the next shot. This heating and cooling causes tiny cracks to form in the surface over time. These cracks are then visible on the surface of cast parts. A die can be welded and polished to restore a smoother surface, but the heat check will eventually return. Often, they have no major impact on a casting’s performance and are ignored if they don’t cause leaks or other failures in the part. They are merely indicative of a die that has been in service for a long time.
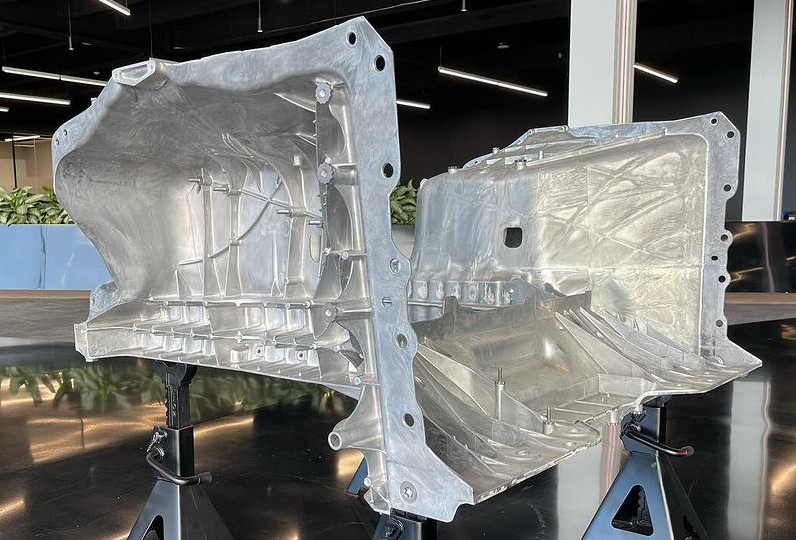
The most interesting part, however, is the larger gigacasting. The sheer size of the part is obvious. With the limited resolution available in the Instagram photo, it’s difficult to get the best idea of the surface finish, but it still appears largely smooth and free of defects as per the smaller parts. In places, it appears that the sheer size of the die may mean that the metal is cooling more during casting, as it takes time to flow into the huge cavity. We can see this in places where the strengthening ribs show through on the back face of the casting. The fact these are visible like this suggests a temperature variation or different rate of cooling in these areas where the ribs meet the thin wall section. This is not inherently a bad thing, just a hint at what may be going on as aluminum flows into this very large casting.
If you’re wondering where this casting sits in the vehicle, it appears to be a major part of the Cybertruck’s front end. If you compare it to the photos of the Cybertruck’s front suspension in our recent extensive explainer piece, you might get an idea. The ribs and standoffs line up with the front suspension mounts for the upper control arm and the shock absorber top hat.
It's massive – no way this thing is less than 60k. Finally got the tire dimensions pic.twitter.com/mTnXJC0UxA
— Devon Guerrero (@DevonGuerrero) November 25, 2023
Without being able to see the die from all angles, it’s difficult to spot features like marks from the ejector pins that help push the finished casting out of the die. However, based on the shape of the casting, we can make an educated guess about which way it comes out of the casting machine. Die casting machines have a movable “ejector” die and a stationary “cover” die. When making a new part, the ejector die is closed over the cover die, and a large locking arm clamps them together. Metal is injected, allowed to cool, and then the ejector die is pulled back, taking the casting with it. At this point, ejector pins push out of the ejector die, ejecting the casting to be grabbed by a robot arm or other mechanical means.
Looking at this casting, the section on each side that corresponds to the wheel wells has a taper, or draft angle, which allows it to be smoothly ejected from the die. While each wheel well area has several strengthening ribs and other undercut features, these are likely formed by “cores” which are movable parts on the ejector die that can be inserted for casting and retracted to allow removal of the finished part. In the orientation shown, the side cores would only have to retract slightly to clear the strengthening features in that area. If the part was put in the die the other way, the cores would have to retract further to fully clear the inner wheel wells. Generally, designing movable cores into a die is tough and it’s easier if you can give them a shorter stroke to clear the part for ejection. I may have gotten this backward, but without being able to inspect both sides of the casting for ejector pin marks, it’s kind of hard to tell.
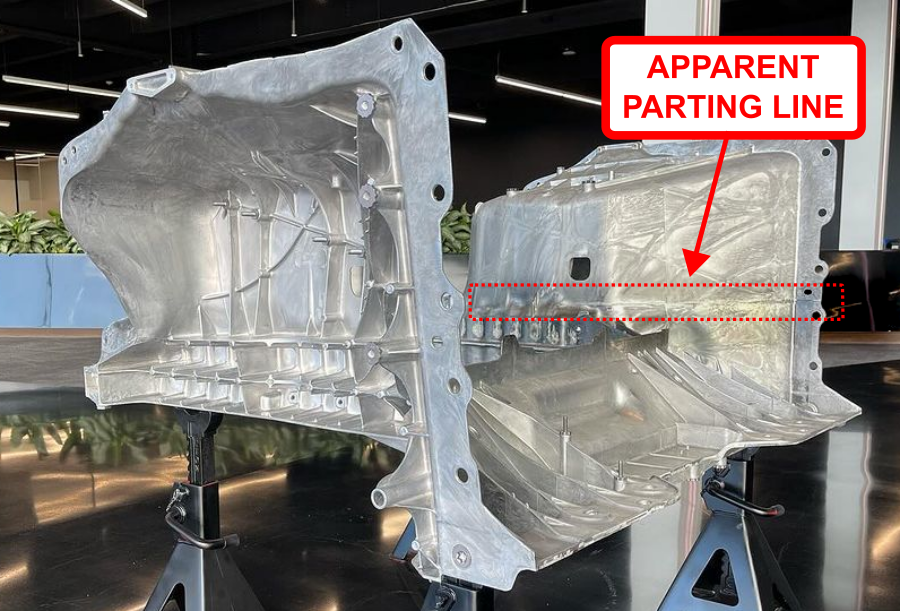
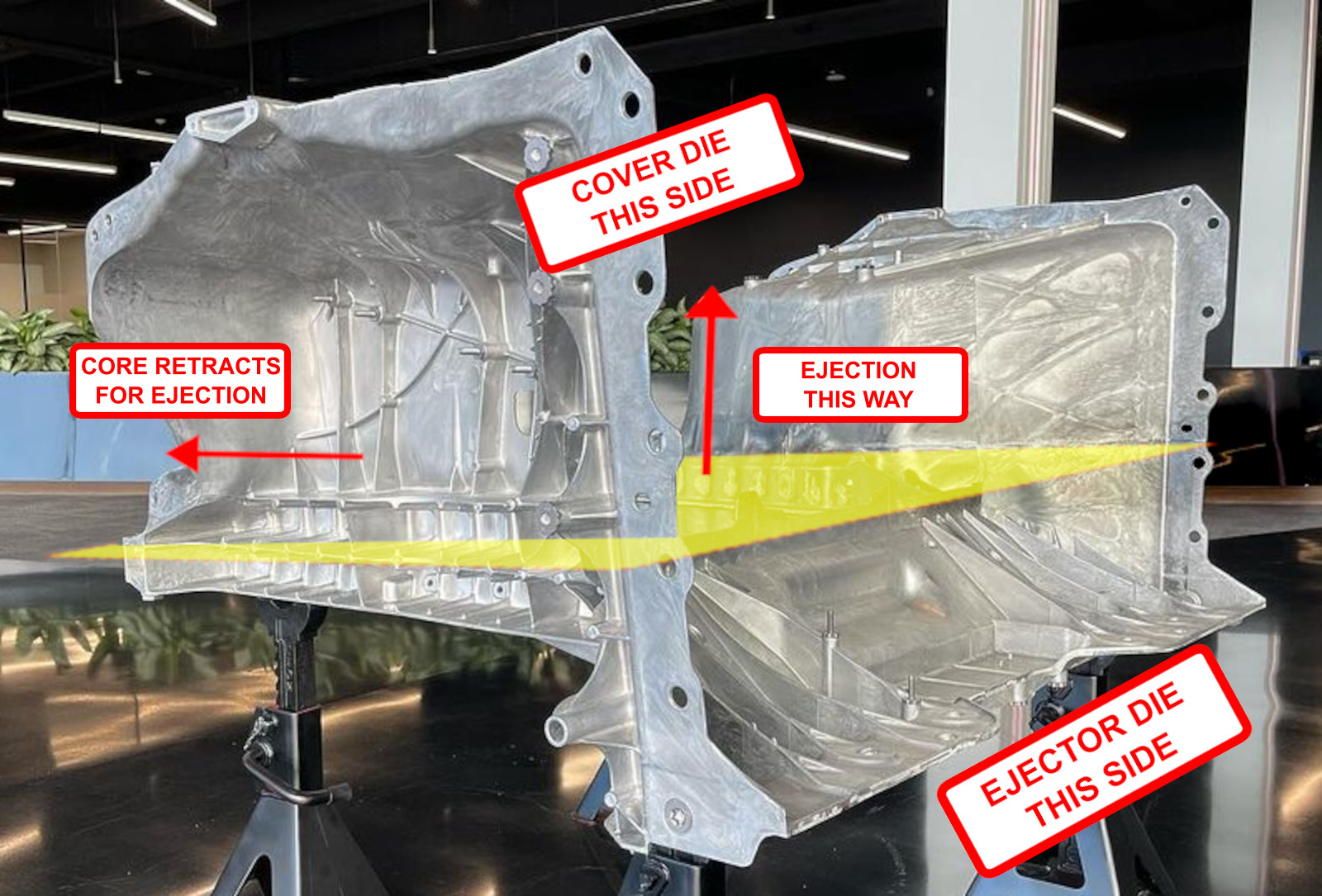
Cybertruck castings at Giga Texas today! All of the castings from Friday are gone, but a large new batch is out in force today! pic.twitter.com/vcgUUAAxae
— Joe Tegtmeyer ???? ???????????? (@JoeTegtmeyer) November 13, 2023
Moving beyond casting minutae, photos show us that Tesla has been producing these parts en masse. They also show us further gigacast parts that are likely part of the Cybertruck as well. Relative to vehicles and people pictured, it’s easy to see just how big these giant castings are.
Indeed, that’s the whole point of gigacasting. It follows the same engineering strategy as Tesla’s EV cooling system we explored relative to Porsche’s effort last week. This is an example of integration. A typical subframe would need multiple sheet or tube steel parts to be fabricated, which would then be assembled in a jig and welded together. Even for a simple subframe, this manufacturing process quickly involves multiple stamping machines and robots to do the job. Instead, by casting it as a single large part, the entire thing can be made in under two minutes in a single casting machine, with maybe a robot or two required to remove the parts or spray coolant on the dies.
Simplifying the manufacturing process saves money in terms of labor, equipment, and time. Of course, achieving this requires great investment. Castings like these simply didn’t exist years ago. Back in my time as a casting engineer at an automotive plant in 2016, whispers were on the air about Tesla’s new giant castings. Back then, they were an interesting R&D project with great knowledge. Now, they’re a unique technological edge that other automakers are eager to bring to their own production lines.
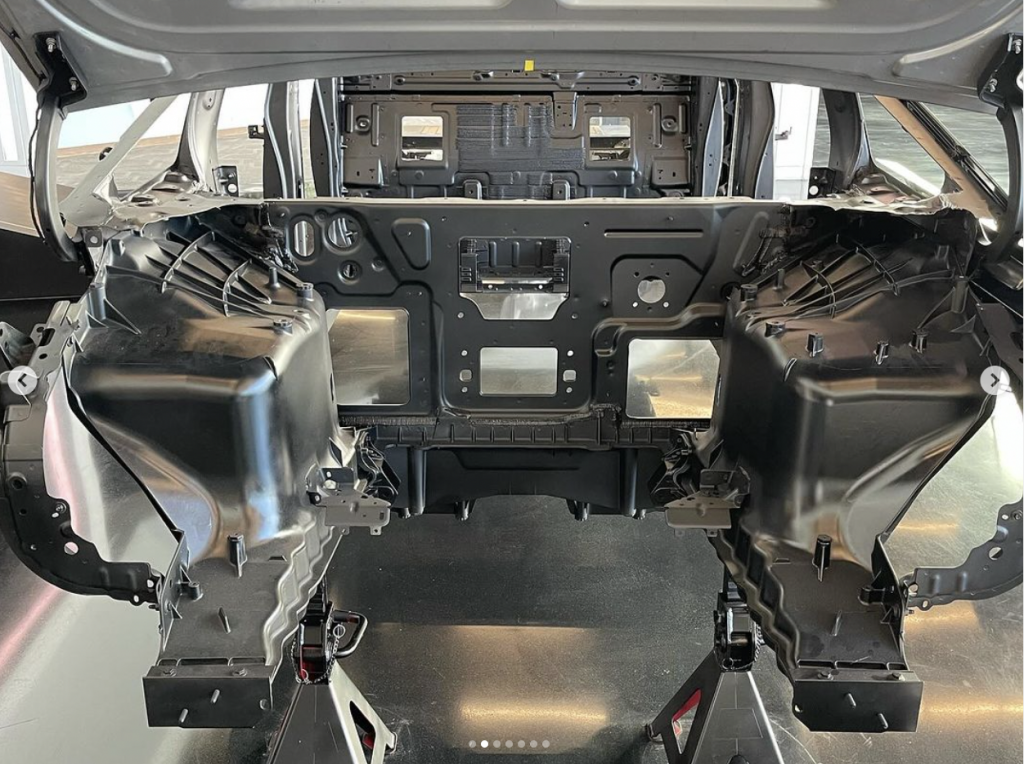
It bears noting that Tesla’s process isn’t without flaws. Some of the company’s cast parts have shown embarrassing aesthetic and casting flaws, and Tesla’s quality record has sometimes left something to be desired compared to its competitors. However, the company is now producing cars in their millions and seems to be getting the hang of the job.
Update: The owner, Nizar, has sent more photos – which reveal serious cold flow or other temperature problems.
Any intern at my old plant would be able to spot these, day 1!
Note the black marker, placed by owner to track crack growth. pic.twitter.com/oxPNwaidv2
— Lewin S. Day (@rainbowdefault) August 30, 2023
Casting problems caused by temperature issues visible in a 2023 Tesla Model Y. The crack appears to be a case of cold shut, where two fronts of molten metal cool off before fully merging in the die.Â
Tesla wasn’t the first automaker to cast parts of automobile bodies, but its supersized castings have drastically cut the number of parts involved in the assembly of its vehicles. It could give Tesla a serious lead over its rivals in terms of cutting the costs of its vehicles, at least until the rest of the industry catches up. As a manufacturer, Tesla may have its quality issues, and it may have gotten many things wrong (looking at you, yoke). Regardless, it’s clear that there is some very smart engineering going on to speed Tesla’s manufacturing and cut costs to the bone.
Image credits: Sladen CC BY 3.0, Munro & Associates via Instagram, Tesla
Just stealing ideas from Jeremy Clarkson!!!
https://www.youtube.com/watch?v=J1KuYXafOAw
When you can see the “ribs” on injection formed component it indicates that the part wasn’t packed long enough or not allowed to cool long enough. There’s always a financial incentive to cut the cycle time. The side opposite the ribs looks funky to me. Also, are those structural design or to facilitate filling the die. Moving that much material, in seconds, needs all the help it can get.
Instead of this expensive and energy hog process, well planed feature rich stampings might make an economical and more reliably stronger construct.
Tell your kids, don’t learn to code, learn to heliarc weld! There will be a big business doing crash repairs on these vehicles (lots of mfgrs are taking the gigacasting route), not sure if they will be saleable in N. America but certainly can be shipped abroad.
Yeah, coding is gonna be almost completely done by AI in two years
I’m sharing this article with my co-workers!
Yay! And if they’re casting engineers, they can chime in on the gigacastings too!
You think that casting is big? Have you seen Jason’s new scar? It’s big as hell!
Jason Torchinsky Medical Expense Fund. Donate now to make your favorite person’s life better (apologies to all the less favorite people on the planet).
Jason isn’t aluminum, despite the rumors!
No, but he is part of the cast we all come here to see 🙂
I mean, we’ve been doing large format metal forming for decades. Wait till you see what we can make with large area 3d printing of metal parts.
3D printing is very cool, but it often produces parts that don’t quite have the same strength as forged, billet, or cast parts. Much better in terms of producing complex geometries though.
For now yeah.
We need to use generative design to design the part to be printed instead of having the hubris to think we as humans could design it better.
For vastly larger stuff, there was the Heavy Press Program, the two 50kt presses still produce parts for every Boeing and military aircraft. Dies are 26’x12′ with a 6′ stroke. https://en.m.wikipedia.org/wiki/Heavy_Press_Program
Technically those are forges, but that makes them even cooler
These can stamp an entire Cybertruck in one go 🙂
Now that’s efficient
3D printing was massively overrated and was right from the start! It’s had years to spread but the vast quantities on nothing being made right now should make that obvious.
3D printing has terrible cycle time. Great if you want a few parts tomorrow, terrible if you want a few thousand parts a month. Plus the cycle time is linked to part mass, so it gets worse the more you use it.
I’ve been using 3D printed parts for 25 years and it’s always been over sold as the next big thing.
All the hobbyists I know are terrible at design, so I keep getting shown parts that would be tricky to machine but also don’t really work. Still, I guess we have to create stock of recycled plastic from something.
Just because YOU don’t know about the parts doesn’t mean they’re not being made and used. There are all kinds of them in the real world of manufacturing. Consumer goods is not representative.
Everyone hears of them.Even though there arent many,they’re still talked up in the press!It’s actually embarrassing.
It’s just like my steam engine!!!!
Except for the many many ways in which it not, but the big unwieldy and being a right bugger to fix castings bit is.
I see giant machines like this and wistfully imagine having a job where I wander about wearing a hardhat, checking dial indicators and stuff. So cool.
EDIT: also want to say this article is awesome, this stuff is why I subscribe.
I’m glad you enjoyed it! Great to finally have somewhere to talk castings.
I’m not sure this will actually be a repairability issue at all. This large casting is replacing sheet metal unibodies. Which are already mostly unrepairable, unibody frame straightening is very out of style and most insurance companies just total cars that have any degree of structural unibody damage.
Assuming the castings are as strong as the unibody sheet metal they’re replacing, I wouldn’t expect this to be damaged any more easily than existing cars
I’m sure that is what Tesla would say. And to an extent it is true. Hard hits = total loss, especially for EVs.
It is a disposable world which does not bode well for cutting CO2 manufacturing emissions.
Every car that gets hard hits get totaled by insurance companies. Its not exclusive to EVs. Some companies rebuild them with branded titles but not many people want a car with a branded title. Megacastings are not going to change that. It’s not more labor to weld new structure to a megacast vs one that was glued and welded like crazy. Its not like a massive hit to a car would somehow damage a welded and glued structure less than a megacast. They won’t replace a megacast with a megacast.
While there is total truth to insurance companies totaling cars for unibody damage, there is also a complete market of dealers who buy those, repair them by cutting up other damaged cars, and sell the vehicles with a branded title. So I’m curious what the weldability of these castings is for repair. Or if you just replace the whole damn thing by buying a car wrecked on the other side, and you can replace them that way?
But I agree. Primary market, most cars are not considered worth replacing the unibody structure or straightening. That secondary market however, I’m curious to see what happens.
This reminds me of the manufacture of Corvair aluminum engine blocks which was brand new technology for GM. Alcoa built a plant near Chevy’s Corvair engine casting location. The molten aluminum was by trucked by flatbeds with giant open crucibles. About nine tons of liquid aluminum could be carried on each trip at 5mph to prevent sloshing.
https://axleaddict.com/auto-industry/The-Making-of-the-Chevrolet-Corvair-Engine
That is nuts, can you imagine being the guy in the meeting who suggested they just truck molten aluminum from the furnace?
It’s ok, we’ll just go slow!
And this was not Joe’s widget shop, it was two of the largest corporations in the world!
A friend of mine in college had a big hunk of polished zinc about the size of a loaf of bread that was block, letters reading, think zinc! Eventually, I asked her what the hell that was all about and she said her father had a company in Detroit that drove tankers full of molten zinc around to various factories where they made things out of zinc, like carburetors and all that stuff. I asked her what happened if the truck ever got an accident and she said we don’t know but probably not good.
I knew of a company that decided to truck sludge (open top tank) from the digesting operation of a sewer treatment plant to the dewatering process. “We’ll just take it slow”. Until inevitably something jumps in the way and then it’s raining brown all over the truck cab and anyone within 50 feet.
Those trucks need a Pinto-esque bumper sticker
Not a big deal, there is precedence. In Pittsburgh (when it was the steel manufacturing capital of country), molten iron was put in special railcars and moved via RR tracks and the ‘hot metal bridge’ to other side of the river for further processing:
https://en.wikipedia.org/wiki/Hot_Metal_Bridge
Cool! I had no idea. I will now go down a wikipedia rabbit hole on all things smelty
I worked in a place where you could feel the heat as forklifts carrying crucibles of molten aluminium drove by
Just hope that overhead water pipe doesn’t start leaking! Worked in a cast where the melt was delivered along tracks to the injection end of machines, and we used ladels to fill the shot pot. A month after I left a water pipe broke over the hot cauldrons. Very bad.
Molten zinc and aluminum were very commonly seen in tanker trucks and rail cars in South Eastern Wisconsin and northern Illinois back 30 years ago. And those were purpose designed and built conveyances. It wasn’t sloshing around on a flatbed trailer. It enables the least expensive melt to be delivered to processers in a geographic area. A LOT of energy goes into liquefaction of aluminum, or if zinc, less. Even time of day can justify melting in off peak hours, then forming later.
Why even live?
LMAO
Wow. Talk about having right of way!
That’s both ridiculous and amazing
I wonder how their facilities compare to Mercury Marine, as they have/had the largest die casting facility in the states for some time.
https://www.boatingmag.com/mercury-marines-mega-die-cast-machine-is-largest-in-north-america/
Anybody know if Tesla beat them?
Looks like Tesla has the edge, on that machine at least. Gigacasting machines will deliver 6000 to 9000 tonnes clamping force.
OK, no part of the design or specifications of the Cybertruck are remotely interesting or impressive to me, but THIS is a cool piece of technology.
Yeah, it’s pretty wild from a manufacturing standpoint. Cool to see basic tech pushed farther.
Except for the premiums insurance companies will charge, a large non-replaceable casting that could total a vehicle if damaged would actually benefit Tesla.
They’re not selling collision repair or used cars. One less used Tesla is, for them, one more person who will have to buy one new from Tesla.
It would be a really weird plan to consider this, but we’re talking about Elon here.
Actually they do sell collision insurance.From memory it started because insurance companies were charging too much(in elon’s opinion).It may even have been related to large castings.Its been awhile,i cant remember.
What would interest me is ,are they running it as a break-even business,and thus kind of confirming their tech is less cost effective long term?
Even if they are running break-even, that doesn’t mean that the tech is more cost-effective; maybe their customers are paying more?
I would assume it’s not breaking even. Tesla can subsidize it to keep expensive repair claims out of the data of the insurance companies. Possibly as a way to control negative publicity?
I didnt think of that angle.That’s totally something musk would do! LOL
Like a lot of others are asking, I’m curious on the replacement of one of those components after an accident. But if it’s a hard enough hit to damage a casting I am not sure I’d trust the integrity of the battery either. Sure seems like an environmentally sustainable option… /s
That aren’t repairable. Tesla has no procedures to repair broken castings, so they can’t be done for insurance reasons. I saw one example where the casting has a metal tab to attach steering components. It was snapped off in a minor collision, but couldn’t be repaired due to no procedures.
Why not replace the entire broken casting then? Well, it’s a big job, but it also can’t be done. Tesla has used industrial adhesives to join the various assemblies, and you can’t separate them.
So we’re saving the environment and progressing as a species by moving away from gas to building electric cars that are not feasible to repair after a collision? The same cars that also pose problems for firefighters if those collisions are bad enough?
I’m sorry but make all this make sense to me.
I wonder if you could at least recycle the aluminum, or is it contaminated with adhesives?
I’d absolutely hope so!
I don’t think there would be any issue recycling it. Melt it down and they can be removed. They’d probably mostly incinerate at that temp since they are hydrocarbon based(I assume).
I’m not 100% certain but i think the answer is yes.Those shouldnt pose much problem
Tesla is not trying to save the environment. They are selling luxury cars.
True, they just build cars, but we keep being told by our authorities how electric cars are the way forward and how we all need to adopt them as such.
They are and we do.
I think this is an interesting point but it’s not as bad as you might think.
Just think about it – a lot of crash repairers will total a car with a badly damaged subframe, and even a lightly bent one will probably be pulled out and replaced.
It’s the same here, only the subframe (despite its size) is a single piece that’s cheaper to manufacture.
This is the one I was talking about. Very minor, but can’t be repaired for insurance reasons.
https://www.youtube.com/watch?v=09AyyT8N4FY
A responsible company would create a toolkit, methods, materials, and training to straighten, patch, and reinforce a damaged gigacasting.
Move fast and break things.Move fast and fix things!I think the question is, do automakers do this with existing damaged front subframes? Or do they toss them and put in a new part to ensure the car is safe and doesn’t have any hidden flaws?
Unbolt and replace. You can buy subframe assemblies. Because these are structurally glued, you can’t do it on a Tesla.
Great write up!
Gigacost repairing is another name for it
Excellent technical deep-dive!
More of this, please!
Missed opportunity for Giga-What? sublines
Awwwwwww
Definitely wonder about the overall sustainability of this approach.
On the flip side (maybe), the crash testing in the Cammisa video seemed pretty impressive. I don’t think it’s clear how comprehensive that is at this point, and I overall loathe these giant/heavy vehicles, but excellent safety/crash testing is always good (as long as it doesn’t mean complete destruction of everything else that it touches).
I’d be onboard with gigacastings if they’re easy to replace and said vehicles are produced for a very long time like Teslas.
That being said it seems like replacing a gigacasting is not practical by any stretch of the imagination.
Is that a fair request, though? We don’t expect steel subframes in other cars to be easy to replace.
Welding is acceptably easy. Can these subframes be welded safely? Most castings are very difficult to weld, where as mild steel welds easy, and modern high tensile body panels can be MIG brazed.
Oh, for sure. But is that what crash repairers are actually doing? I’d say outside of classic restoration shops, probably not. It’s quicker to have an apprentice mechanic yank the engine and swap the subframe for a known good one, rather than trying to weld it up and repaint it, etc.
I agree with that specific point. I’m referring more to when Unibody structure gets tweaked.
I mentioned in another comment, I think in the primary market of cars, this won’t be a serious impact, since insurance companies will likely toss a bent steel unibody as quick as a bent aluminum cast one.
But in the secondary market, where repairers and dealers specialize in fixing those bent unibody cars and selling them “cheap” with branded titles, things look very different if these can’t be treated similarly. Since not just EVs are going to move more gigacasting, a reasonable conclusion is that this entire sector of the secondary market will dry up.
Most the steel subframes I’ve seen are easier to replace than a Tesla’s gigacasting.
What Tesla seems to do (in a way that sort of reminds me of Apple) is market changes made for their benefit as improvements for the customer. Massive casting is impressive and will likely save Tesla a lot of money over time. But I hear Tesla fans talking about “gigacasting” as somehow a beneficial feature and it really seems like these buzzwords work. I also hear a ton of talk about how great the minimalism is, when locating all the controls to one screen is absolutely a money-saving measure.
See also proliferation of screens vs buttons, switches, knobs, and gauges, and also automakers treating vinyl seats and “piano black” plastic as premium materials
I blame Tesla for leading the charge on screens (though not the first to move a bunch of controls to screens, they really seem to have popularized it, taken it to an extreme, and made people expect it, especially on EVs), though the vinyl and black plastic certainly can’t be blamed on them. I blame whoever coined the terms “vegan leather” and “piano black.”
Gigacasting is beneficial for lowering the purchase price of the car. (That cost benefit may well be lost if there’s a bad enough accident, likely)
It can be beneficial in that respect (assuming it does actually lower the price), but that’s not what the buzzword-loving folks seem to think is happening. They are excited to have something that is gigacast and some seem willing to spend extra for it. It’s being pitched as “fewer pieces mean a better product” which resonates with people who don’t consider things like repairs. Some of it is absolutely the same sort of person who believes older cars were safer because they didn’t have crumple zones, but I think a lot of it is just giving it an exciting name.
I have an older Model 3, so keep an interest in what changes are made over time — so pay some attention to what fans are likely reading/watching. The message is largely about assembly line simplification coming with the large castings, with the benefit of decent cost reductions. (I would feel better about it if it included a system for repair shops to slice the casting in half with a bolt-on-able quarter section replacement at the ready — but doesn’t look like it. I suspect that the average cost of ownership is still less as a result of the big castings, though.)
Tesla interiors are the worst thing I’ve ever seen, IMO. The yoke is a joke.
Yeah, nobody ever talks about stuff like this with other manufacturers. It’s interesting to see the Tesla people getting super excited about it and post about it on twitter.
Does seem very apple-fan like. Also expect there to be lots of talk of (for example) 48v being super innovative even though other MFGs already use it.
Yeah, I’d forgotten the 48V bit. I have seen a little of that, and it is exactly like Apple in that instance.
Has anyone documented the repair or replacement of one of these castings? I’d hate to total a car sliding into a curb at relatively low speed.
If these are expensive to repair or impossible to replace, insurance companies will obviously charge higher premiums.
Then Elon will sue them and say they’re trying to ruin his business. Then he’ll buy Geico and replace the gecko with Pepe the Frog.
I hate how plausible this sounds. Well done.
Tesla already has an insurance company. From what I read, they have significantly lower rates than the major competitors, and are great if you never have a claim.
If the rates jump significantly after 6 months with or without a claim, maybe he already owns Geico.
No, it’s German, for “the part, the.”
often told my hair is like sideshow bob, i don’t know why
For all of the pluses of gigacasting, won’t having larger and larger structures cast as a single piece make replacing or repairing these structures – in the event of accident or failure – much more expensive?
“Much more expensive” is the best case. I’d say more like “impossible” in many cases.
Yes
Perhaps. We’d have to look at the price of the gigacasting as a part – which could be surprisingly low given they take a few minutes to make.
I can imagine a small accident will write this off as the labour to replace that casting would be enormous and I dont see any way to patch it
Patching it would be a serious pain. I’m not as familiar with the gigacasting stuff, but generally you heat treat aluminum after forming/casting/whatever. If you’re welding on one of these castings you’re going to destroy the heat treat’s temper in that area.
I don’t see a way to do it either, but I’m not a welder or a body man, just an engineer.