There’s no question that these are challenging times for the auto industry, especially in the U.S. Most of the world has decided it’s a good idea to transition to lower-emissions vehicles, particularly those powered by batteries. Like its counterparts at Toyota, Honda hasn’t exactly been a huge proponent of battery electric vehicles, generally favoring hydrogen fuel cell technology. Nonetheless, Honda is moving forward with expanding its BEV offerings and recently invited me to see what it is doing at its EV hub in central Ohio.
Honda has a more than four-decade manufacturing history in Ohio. The Japanese automaker established its first American factory in Marysville, just up the road from Columbus in 1979 to build motorcycles. Three years later Honda became the first Japanese company to start U.S. car production, and it continues to build the Accord and other models in Marysville to this day.


Over the years, Honda added another assembly plant in East Liberty and an engine plant in Anna, Ohio. There are also plants in several other states and in Canada that build everything from power equipment to off-road vehicles to jets.
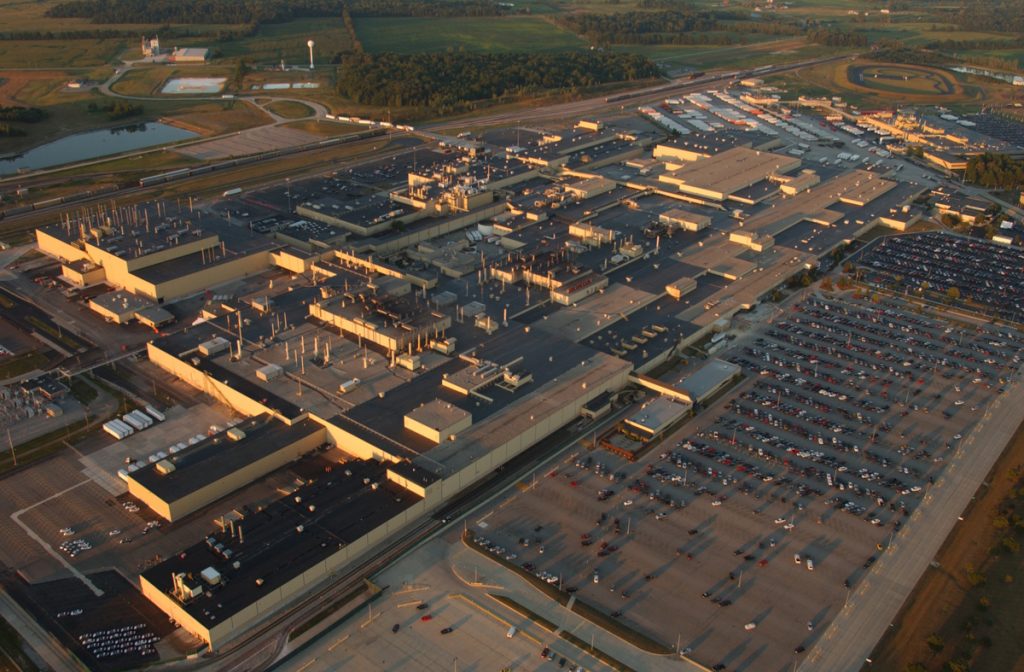
But it’s those plants in Marysville, East Liberty, and Anna along with a new battery plant about one hour away in Jeffersonville, Ohio that comprise the “EV hub.” These four factories will be the core of Honda’s BEV manufacturing in North America in the coming years.
Honda’s Electric Plans
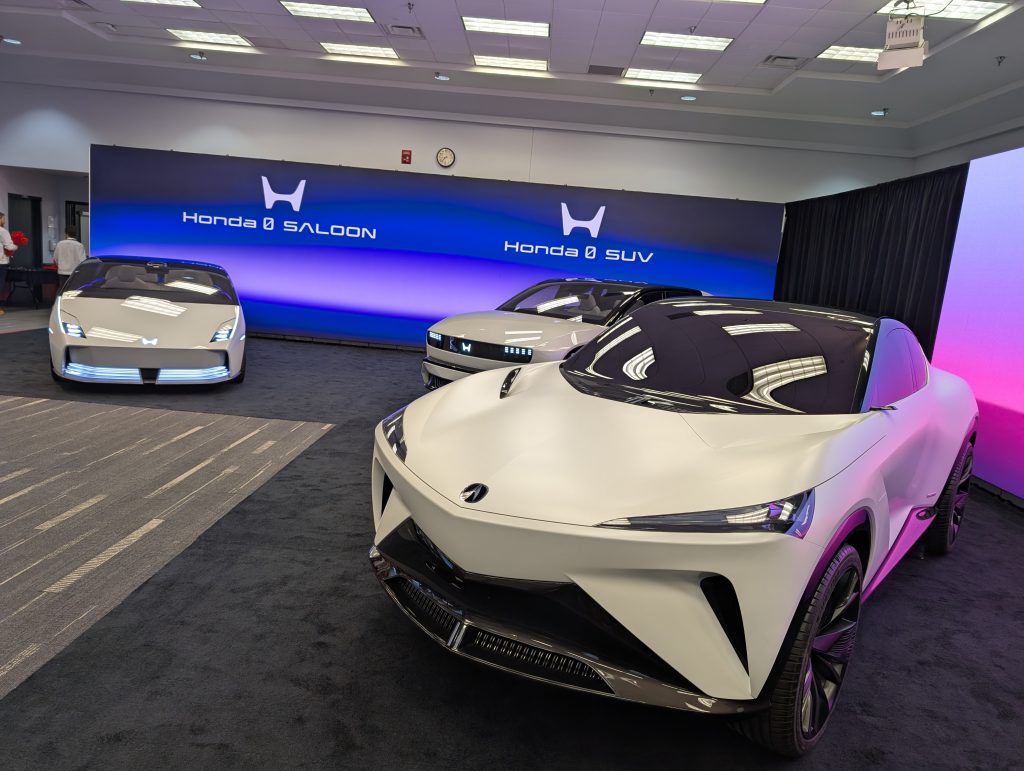
The Jeffersonville facility is a joint venture between Honda and LG Energy Solution and is planned to have an eventual production capacity of up to 40 GWh of lithium-ion cells annually (that would fill about 450,000 Honda Prologue 85kWh battery packs). The plant will produce pouch cells similar to those that LG supplied directly to Honda or through joint ventures to other automakers including General Motors, Ford, Volkswagen Group, Hyundai Motor Group, Toyota, Stellantis, and more.
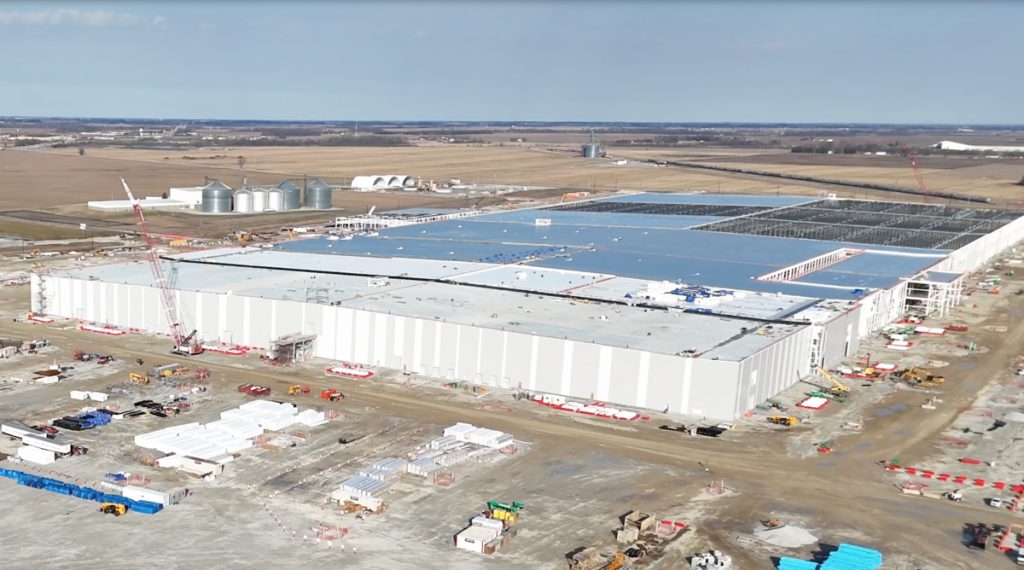
The Jeffersonville factory will also assemble the cells into modules. At this point, Honda is still being coy about specific technical details such as chemistry, capacity, or even how many cells will go into each module although in most other use cases, it’s usually around 12 cells per module.
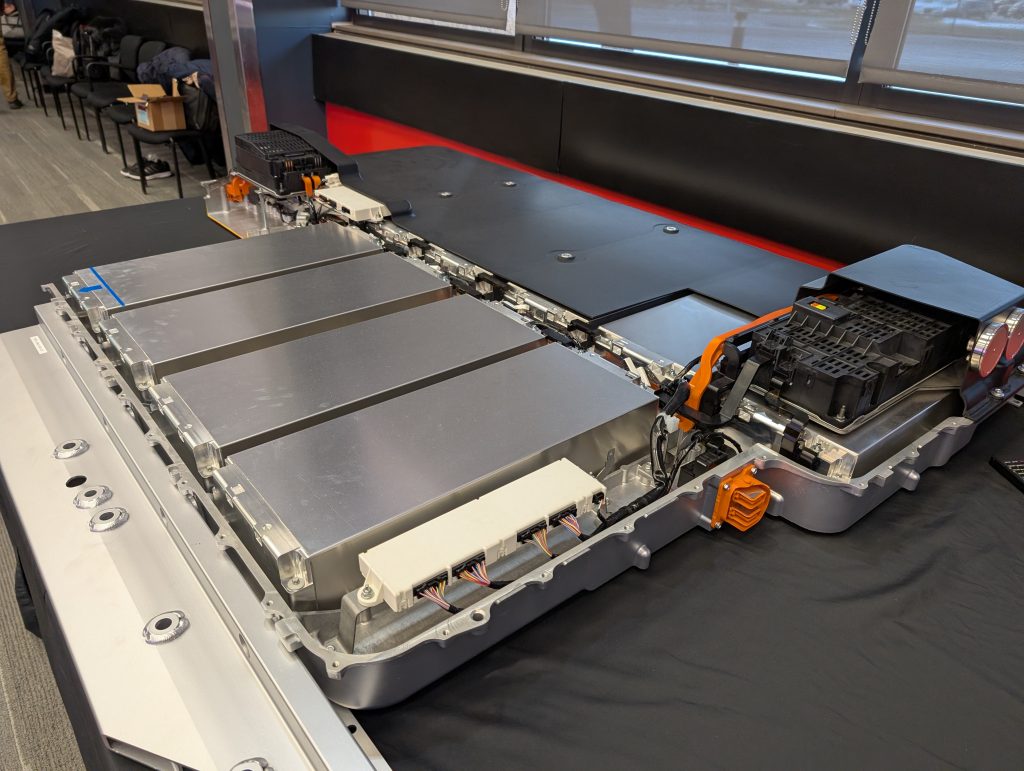
The East Liberty plant has a capacity of 240,000 vehicles a year and currently builds the CR-V and Acura MDX and RDX. In the fourth quarter of this year, East Liberty will also start building the Afeela 1, the product of the Sony Honda Mobility joint-venture, and it has been getting some reconfiguration to support that. Image: Sam A
We didn’t visit either of those factories, but we did get to spend several each in Marysville and Anna to see how those plants have changed in the past year.
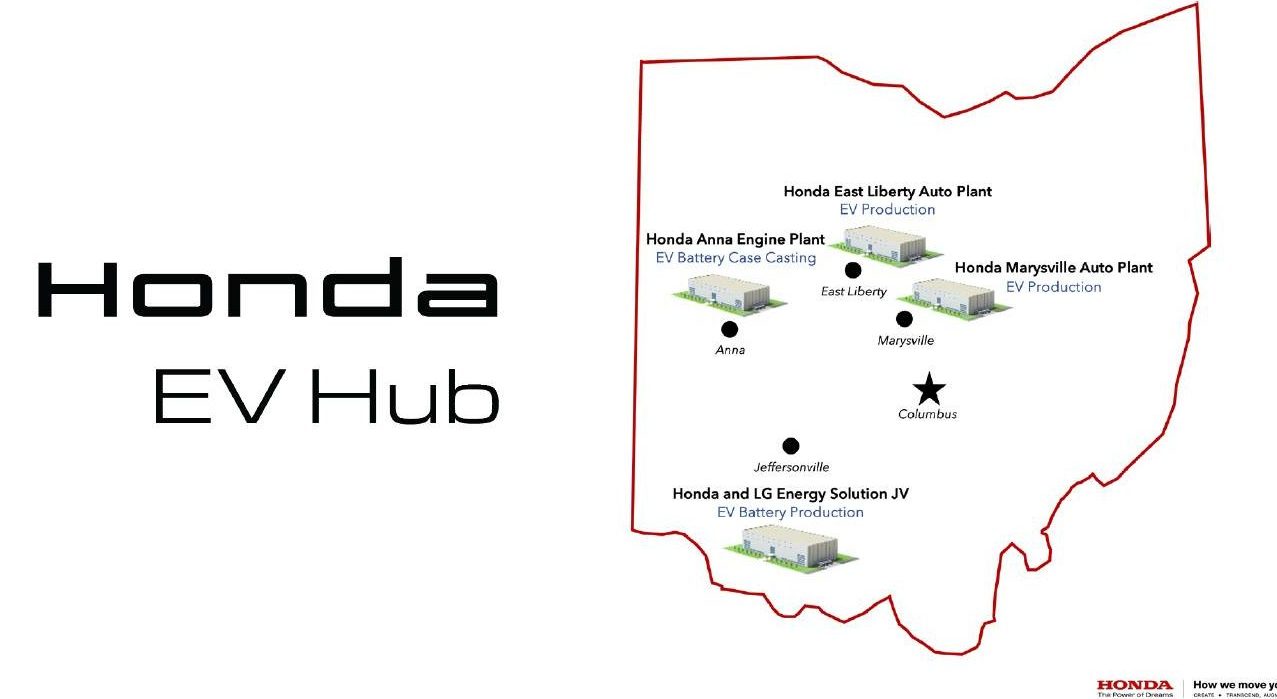
The Original Home of Honda Manufacturing in America: A Flexible Approach to EVs
Marysville was the original home of Honda production in North America and remains the highest capacity factory in the network with 440,000 unit annual capacity. It quickly built such an impressive record for quality that in 1988, it became the first-ever Japanese-owned assembly plant in the U.S. to export vehicles (Accords) back to Japan. Marysville is also the home of Honda R&D, where many of the products that are specifically targeted at this market — including the Odyssey, Pilot, Passport, and most Acuras — are designed and developed.
Vehicle production is a complex and very capital-intensive endeavor. Cars are made of thousands of individual components that are sourced from hundreds of suppliers and need to arrive at the right stations on an assembly line at the right time in the right order. This is a lesson that every successful automaker has had to learn. Many are still learning it, and this has been one of many challenges that has led so many promising startups to fail. Honda has been particularly good at this over the years.
So as Honda started preparations for building EVs in the U.S., it had to make some tough decisions. The U.S. market hasn’t adopted EVs as fast as Europe and China, and the politics here has made more people reluctant to go down the plug-in path. In China and Europe, there is at least some greater certainty around government policy.
Thus with the prospect of spending billions of dollars to build EVs, one has to be very careful about what one decides to spend money on. Honda has traditionally been somewhat conservative, and that continues with its EV program, at least from a manufacturing perspective (the design of the 0 series models is another matter entirely).
Rather than following GM’s pattern with its Detroit-Hamtramck plant and gutting the building to the bare walls, or Ford in building a whole new factory in Tennessee that is unlikely to reach full capacity utilization for many years, Honda is continuing with its flexible manufacturing approach. Interestingly, that does not include ditching a traditional transfer assembly line and installing a system of automated guided vehicles (AGV).
Most Honda assembly plants produce multiple product lines with models of different sizes and shapes. Many Honda products are also built in multiple plants to provide redundancy so that if something happens at one plant, at least partial production can continue elsewhere.
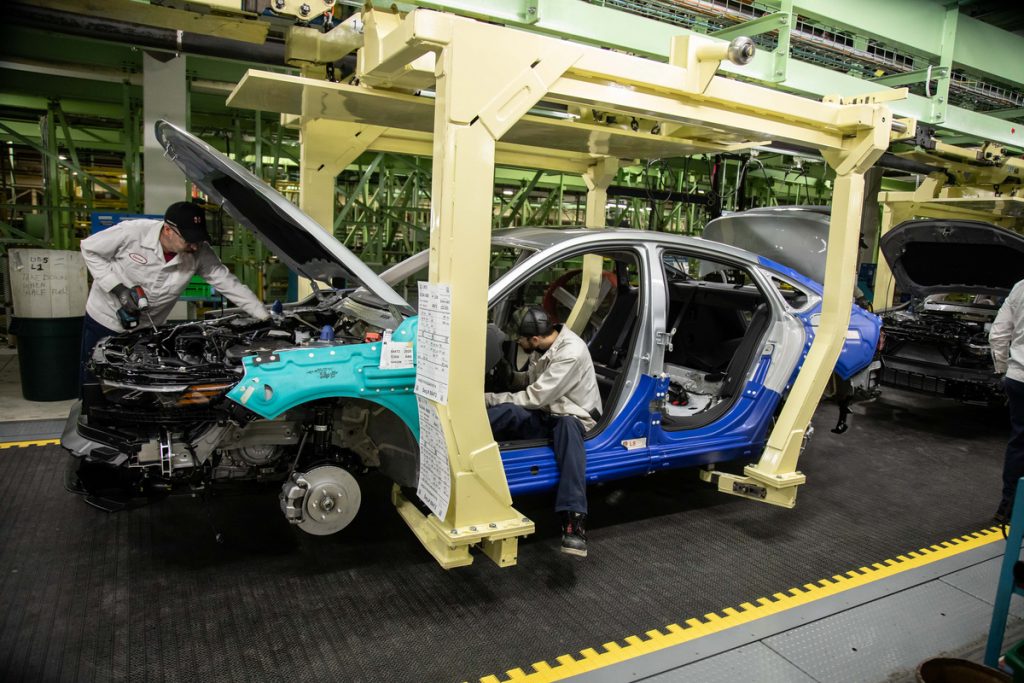
Marysville currently produces the Accord, Acura TLX, and Integra. By the end of 2026, it should be turning out three additional models, the Acura RSX, Honda 0 SUV, and Honda 0 Saloon. As of January 2025, pre-production models are already being assembled. Honda has done this without interrupting production of its existing products. Most domestic brands shut down plants for up to a year or more when making such transformations. Honda regularly executes generational model changes without a shutdown or at worst, only having to utilize the traditional 2-week summer holiday.
Two Assembly Lines Into One
In order to produce three new EVs along with 3 existing cars that use a mix of four and six-cylinder engines, manual and automatic transmissions, and hybrids, Honda decided to combine two assembly lines into one.
In 2023, the Accord was being assembled on a U-shaped assembly line with the TLX and Integra coming together on a second line that wrapped around the perimeter of the Accord line. This made for challenging logistics of getting parts to the stations and yielded relatively narrow aisles. At the beginning of 2024, the Accord was transferred to the outer Acura line and then demolition began.
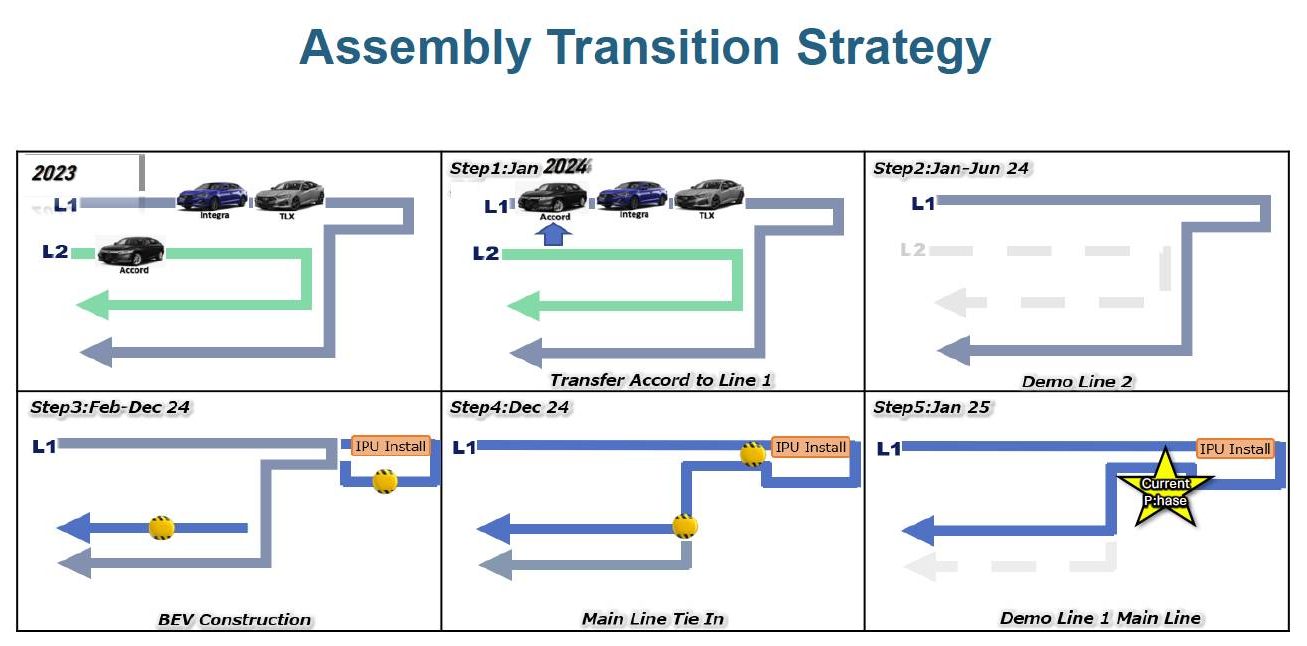
Between February and December of 2024, the first half of the old Accord line was removed and the second half was updated to produce the three combustion models and three EVs. At the turnaround point of the Acura line, a new loop was added that included the IPU installation stations. IPU is Honda’s term for the intelligent power unit, more commonly referred to as the battery pack.
In December, the first leg of the line was connected to the IPU installation loop and the second leg of the old Accord line was connected to the new single line as well. Over the course of the holiday shutdown in December, the entire final leg of the original Acura line was removed and the concrete floor was replaced. When I walked through the plant in late January, there was no sign that there had been a working assembly line there barely a month earlier.
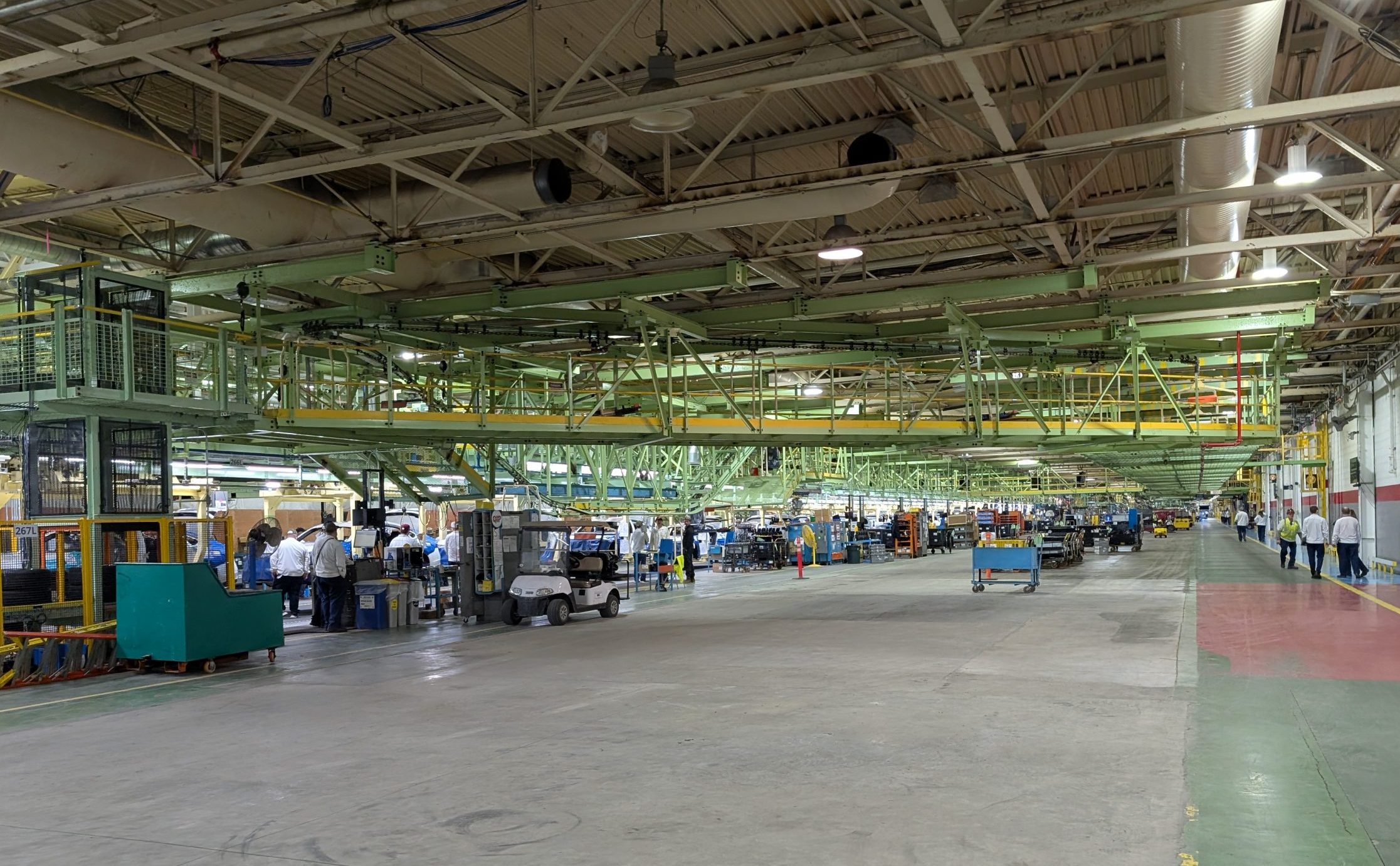
On the day of my visit, there were no EVs actively being assembled, but we did see the new stations including the IPU loop. Combustion-powered models simply continue through this section with no additional work done. But when one of the EVs is coming down the line, a robotic system slides over with a battery pack and lifts it into place while other robots insert and tighten the bolts that hold it in place and transform it into a structural component of the vehicle.
Sharing Assembly Processes Between ICEs and EVs
Further down the line was a station that illustrated how thoughtful vehicle and manufacturing process design can combine to enable this sort of flexibility. Honda’s new EVs are not adaptations of the existing ICE/HEV platforms. However, putting some elements together in a similar fashion allows them to be built on the same production line.
It’s fairly common for modern cars to use a sub-frame architecture for each end of the vehicle that has all of the suspension, braking, steering, and other components assembled on a separate sub-line. This sub-assembly is then inserted from below on the final assembly line, similar to the battery, and fastened in place. For the gas-fueled models, there are three variants of this for the rear sub-frame, with the TLX having an option for all-wheel-drive that includes a rear drive axle.
The rear sub-frame of the EVs will be installed and fastened in exactly the same way, although it will have an electric drive unit included in the assembly. None of these are dimensionally identical or have the same mounting points. But the industrial robots used to lift the sub-frame into place recognize which vehicle is coming down the line and make necessary adjustments, and the robots that drive in the bolts similarly are programmed with the mounting points for each individual model.
ADAS Calibration
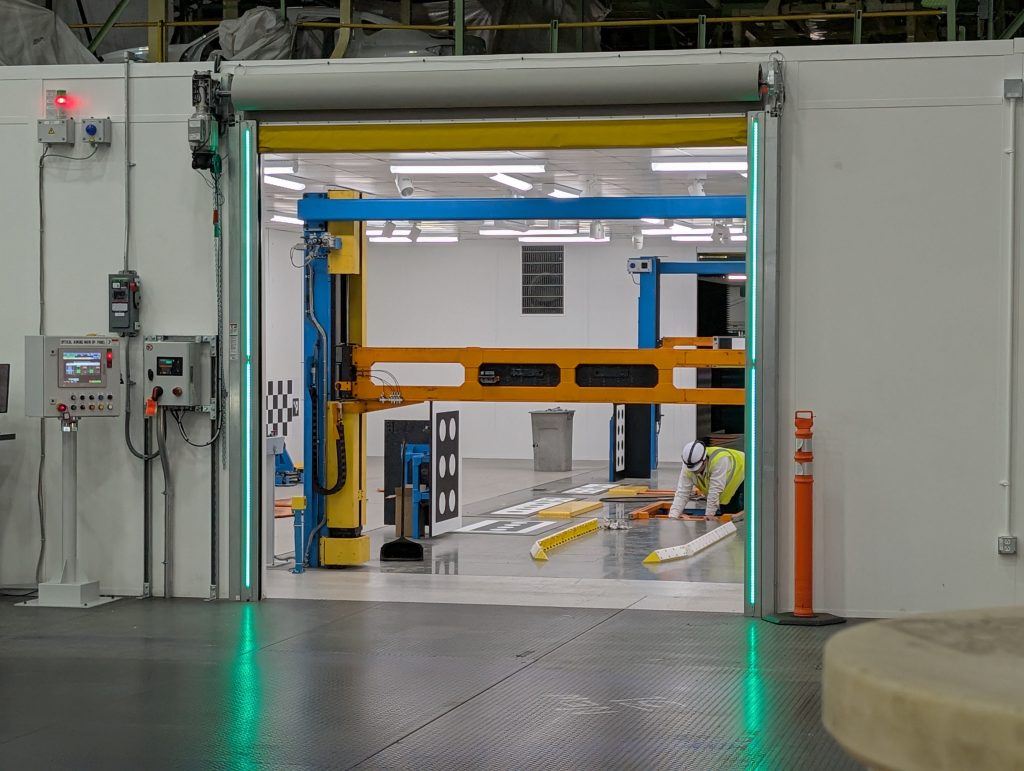
Toward the end of the assembly line is another new station that was being commissioned as we toured the plant. Most modern vehicles have some form of advanced driver assist system (ADAS) with sensors that require calibration when installed. Current Honda and Acura models generally have at least a front camera and long radar as well as rear corner short-range radar sensors.
One of the features that Honda plans to offer on the new EVs is at least hands-free capability as well as the option of a hands-off/eyes-off level 3 automation system. This will require calibration of more surround cameras and radar sensors and potentially also a front-facing lidar. The Honda 0 Saloon prototype included a roof-mounted lidar. All of these need to be calibrated before leaving the factory so a new more advanced booth has been installed before the cars go to the end-of-line rolls test. While we didn’t get to go inside, calibration targets were clearly visible around the booth.
The Rolls
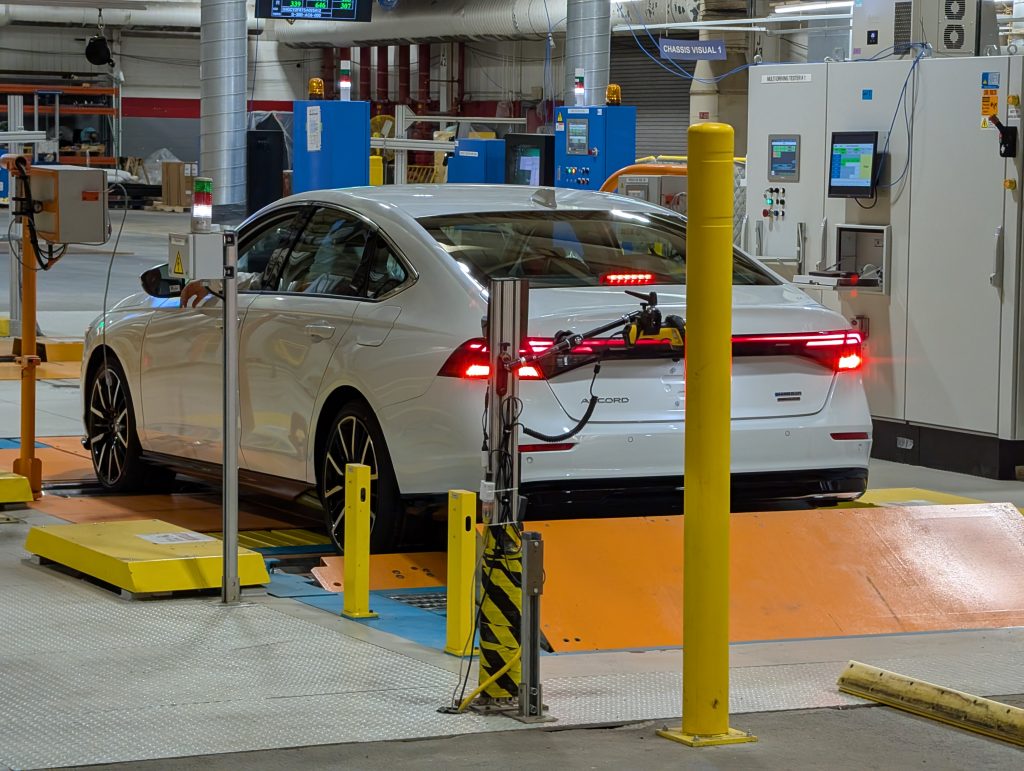
The rolls test is also being updated. This has long been a standard feature of most automotive assembly lines. The vehicle is driven onto rollers, started and a sequence of tests is run to make sure the transmission shifts properly, brakes work and various systems function correctly. Think of it as a quick, in-plant test drive. For the hybrid models, they also test the regenerative braking of the front wheels, and for the EVs, they will also be checking regen on the rear axle.
Assembling Batteries
Since Marysville has been building hybrid models for many years, there was already a section of the plant set aside for preparing those relatively smaller batteries for installation. However, the reconfiguration of the plant also opened up space for IPU assembly. The battery cases are die-cast aluminum produced at the Anna engine plant. Unlike the main assembly line, Honda has gone with AGVs for battery assembly.
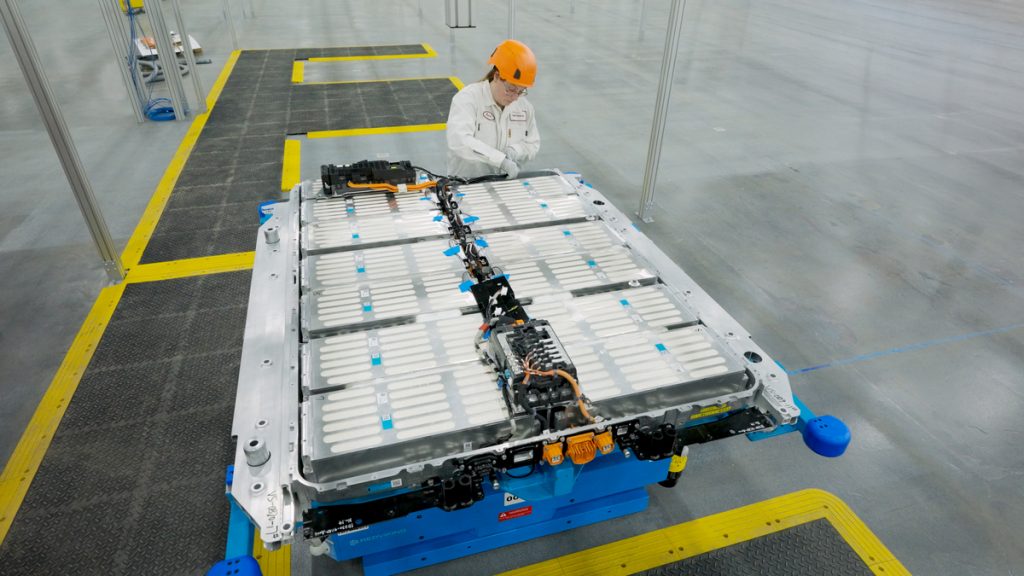
Robots are used to install the modules received from Jeffersonville into the packs along with the bus bars that connect everything electrically. Before the modules go in, robots dispense patterns of thermal paste along the bottom of the cavities where the modules sit and that paste is spread out when the modules are inserted and bolted down to provide a uniform contact area to remove heat from the modules.
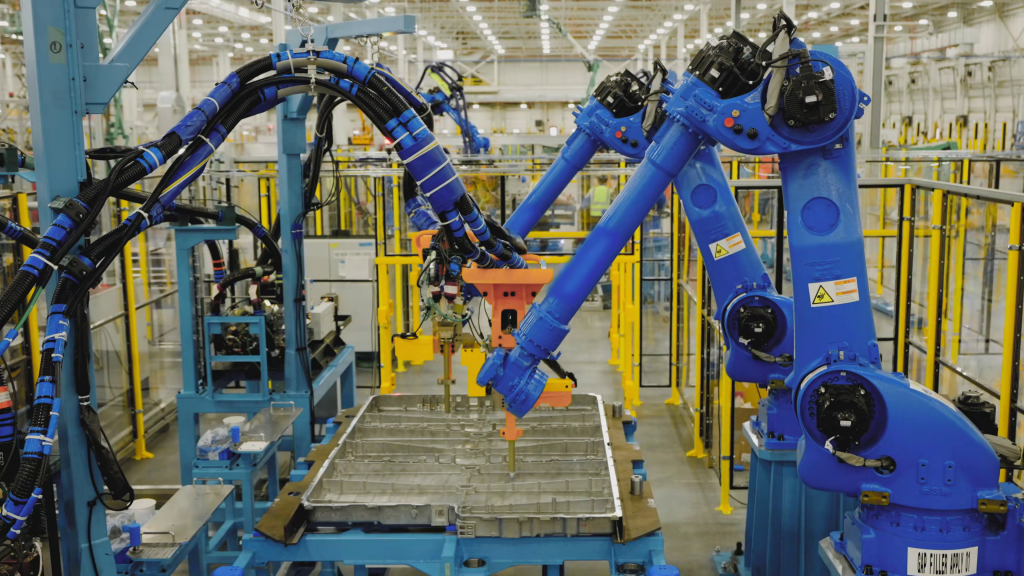
Employees then install smaller components and plug everything in. The packs are lifted up and tilted toward the associates for easier access and better ergonomics. Once everything is in place and connected, the cover is bolted on and the whole case is leak-tested to ensure there won’t be any intrusion.
Interestingly, all of the assembled packs are loaded on pallets and then put into trailers rather than being moved by conveyors directly to the assembly line. This allows for a day or two of inventory to be maintained, at least for now until EV volumes start to increase. Marysville is also doing pack assembly for both that plant and East Liberty, where the Afeela 1 is to be produced. The trailer loading allows for one consistent product regardless of where the packs are being used.
After walking around the Marysville Assembly Plant for about 90 minutes, there was one interesting detail we didn’t see anywhere – forklifts. For safety reasons, Honda only uses forklifts for unloading trailers of parts. Inside the plant, everything is loaded on carts and pulled around by tuggers to the appropriate stations. This allows for better visibility for the drivers and less risk of accidents.
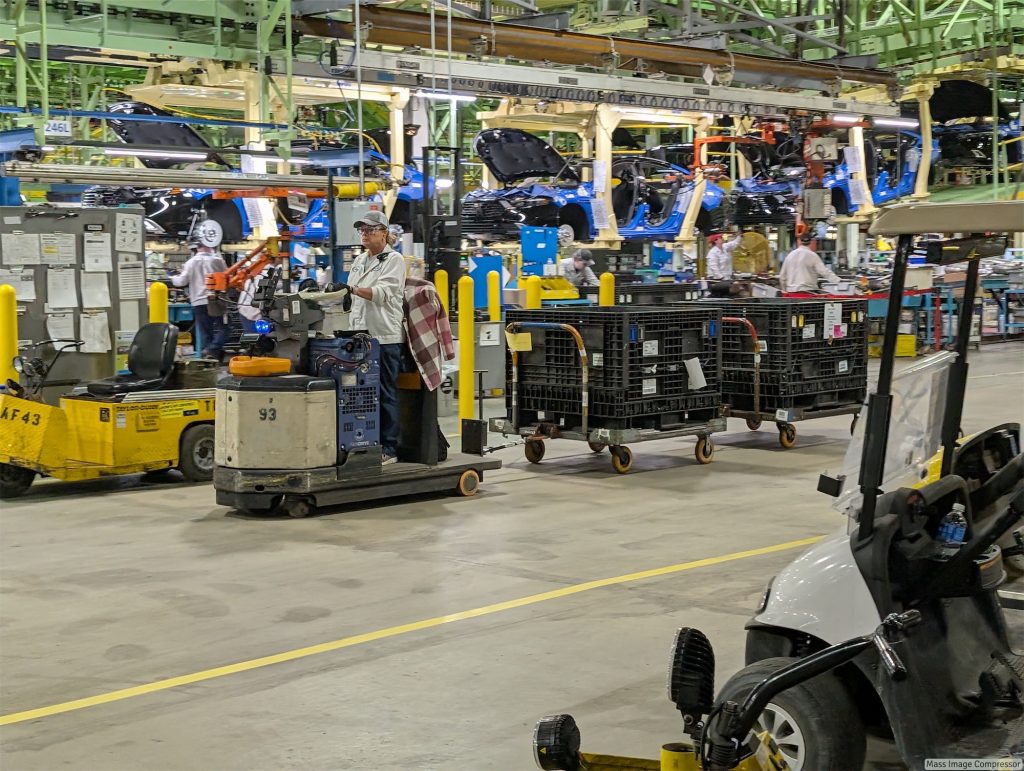
As part of the overall investment Honda also made a variety of other changes to improve sustainability. All of the lighting in the plant has been replaced with LEDs that are more energy efficient and the heating and cooling systems have been upgraded.
Introducing ‘Megacasting’ For Battery Cases
After lunch, we drove about 45 minutes away to the Anna Engine Plant to see where the battery cases are being produced. Anna currently produces three engines, the naturally aspirated Atkinson cycle 2.0-liter four used in the hybrid Accord, Civic and CR-V, the 2.0-liter turbo used in the Civic Type-R and Integra Type-S and the 3.0-liter twin-turbo V6 for the Acura MDX and TLX Type-S.
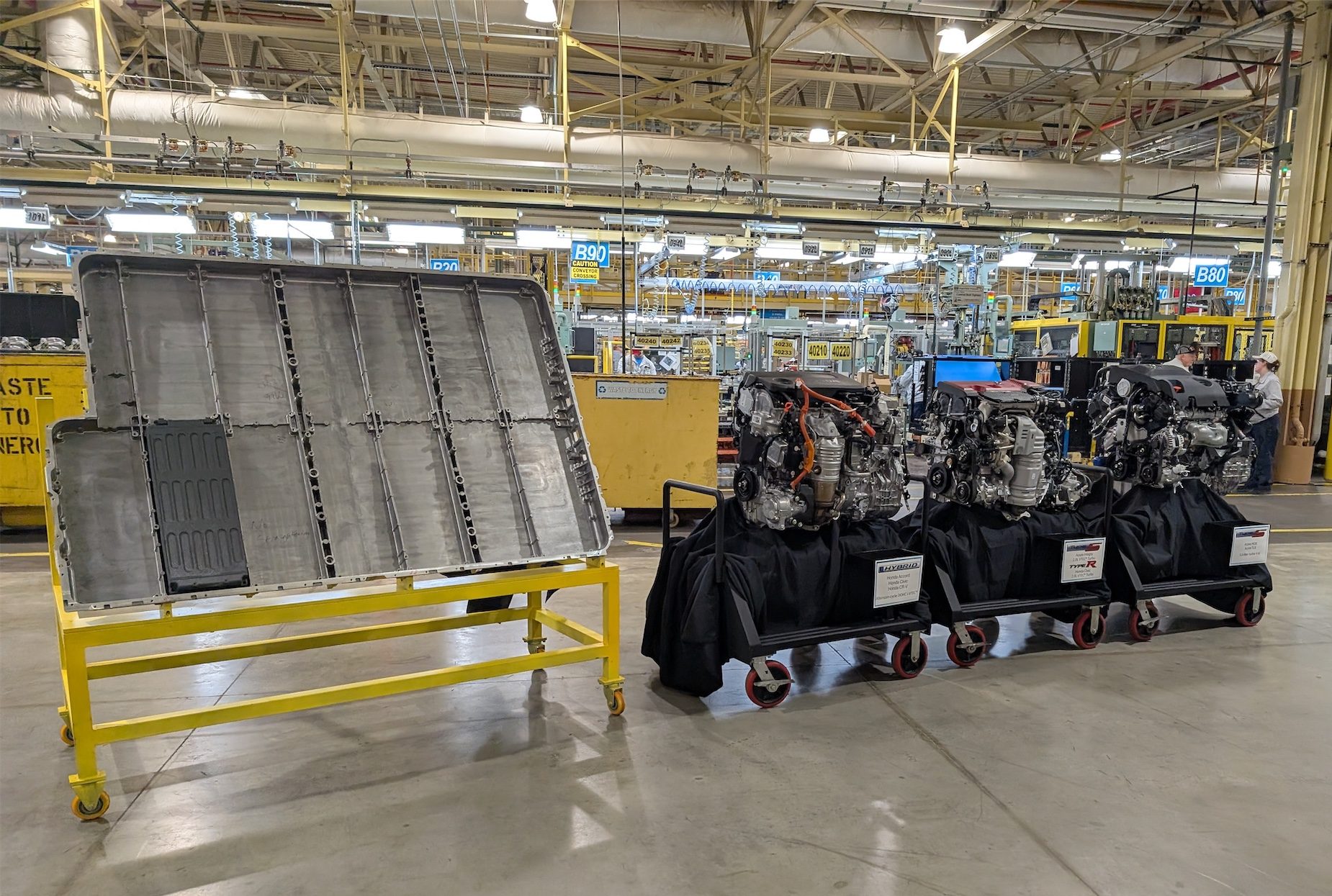
The Anna factory has grown dramatically since it opened in 1985 to produce Goldwing motorcycle engines. It currently spans 2.8 million square feet and produces 1.1 million engines per year. There have long been on-site aluminum and iron casting facilities and the ability to produce many of the major components including cylinder heads, blocks, sleeves, connecting rods, crankshafts, camshafts, and also CVT belts. Since it opened, Anna has produced over 30 million engines.
As part of the EV transition, some of the component manufacturing has been moved elsewhere and some of the older casting facilities have been dropped. Within the existing space of the south building, Honda is in the process of installing equipment for its first in-house megacasting capability.
One of the people on the tour asked about the difference between megacasting and gigacasting (the term that Tesla invented) and which is better. The reality is that they are both nonsense marketing terms that have no actual meaning, just as gigafactory has no meaning. Gigafactory and gigacasting were both coined by Tesla to make factories and processes seem extra special. Mega/gigacasting is just high-pressure aluminum die casting of large-scale components.
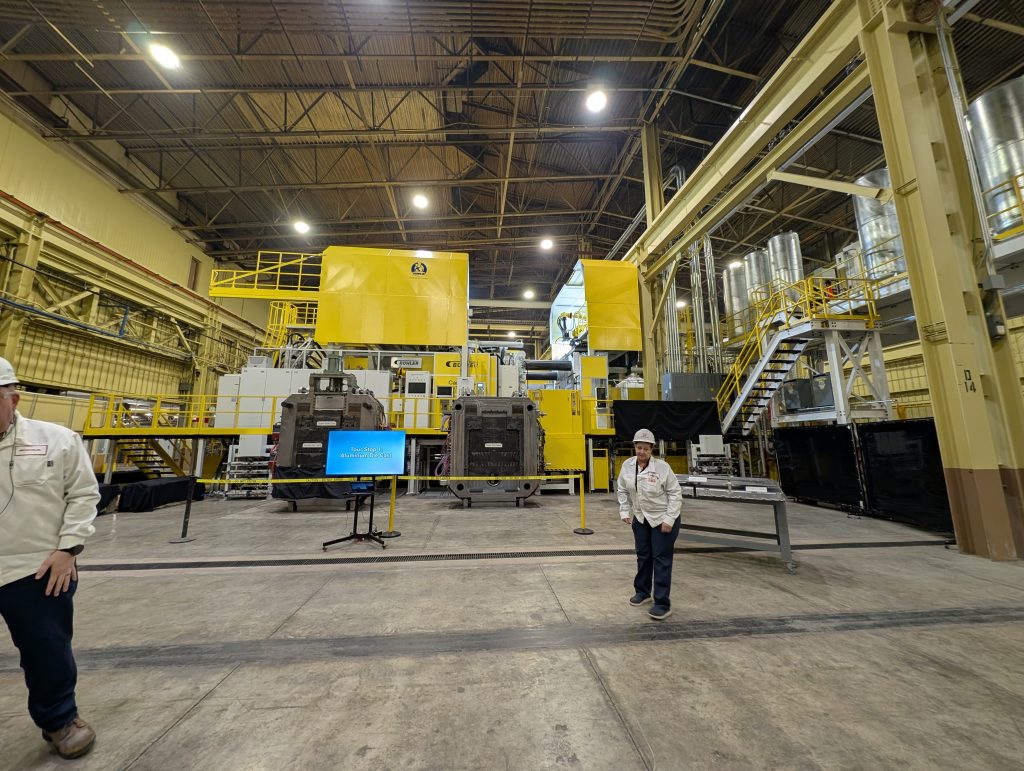
With marketing out of the way, Honda is putting in six 6,000-ton die-casting machines in Anna, five of which are already in place with the last to be installed by the end of February. These machines are so massive, that Honda had to cut a new 16-foot by 16-foot door in the side of the factory to enable the machines to be brought in.
The machines are set up in pairs with one of the machines in each pair producing the front half of the case and the other the rear. Honda is no stranger to die casting having used the process for many years for engine blocks. However, the full battery case at 1.3 meters wide and nearly 2 meters long is more than 4 times the size of a four-cylinder block. The larger a part to be cast is, the more pressure is required to ensure part uniformity and make sure material doesn’t leak out between the two halves of the die.
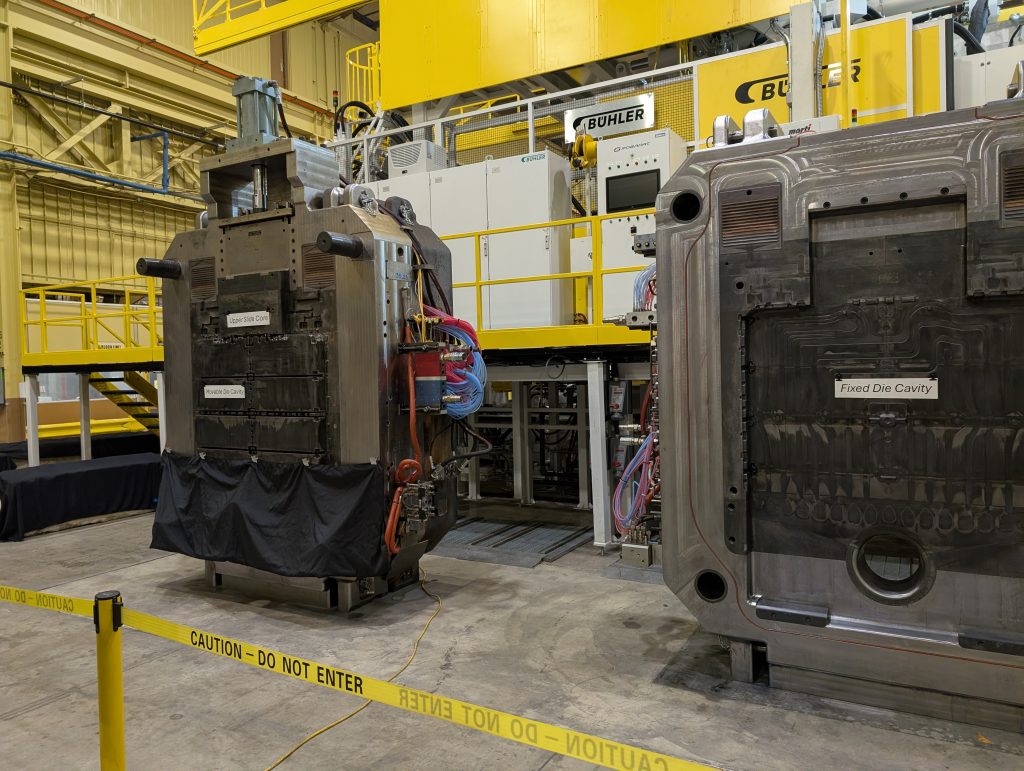
Again, as part of the sustainability push, Honda has focused on a number of areas. They formulated a specific aluminum alloy that would provide the needed material properties to protect the battery, minimize weight, and also be fully recyclable. Many die-cast alloys can’t simply be melted down and reused, they essentially need to be re-smelted. The mixture Honda is using allows scrap, chips, and trimmings to be just put back into the melt furnace and go right back into the process.
High-efficiency melt furnaces are used to minimize natural gas consumption and they have the capability to be modified to plasma arc welding in the future to further cut emissions. The amount of lubricant sprayed on the dies to allow for part separation is also kept to a minimum. Later on in the machining process, Honda uses a minimum quantity lubricant process. This approach allows the lubricant to evaporate during machining and leaves dry chips that can go straight back to the melt furnace after being compressed.
When the castings come out of the die, they go straight into a quench tank for about 8 seconds. This combination of the material and going straight from die to the quench eliminates the need for a separate heat treating process which is one of most energy-intensive parts of metal part production and produces the most CO2 emissions. Another major advantage is that heat treating often causes part distortion that in turn requires more machining, adding to cost, energy use, and emissions.
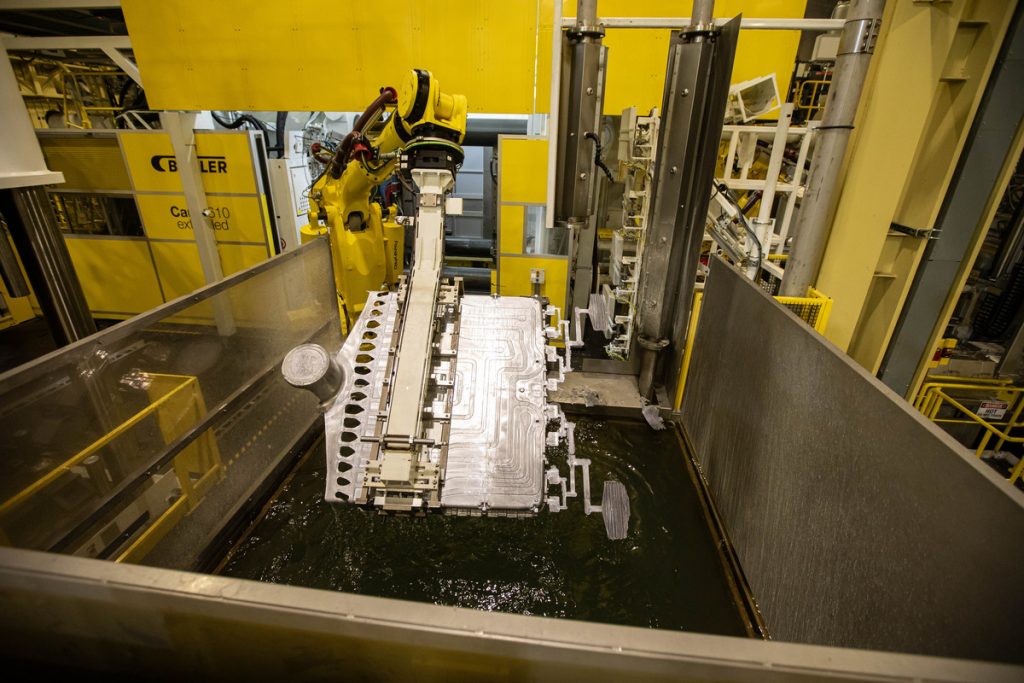
After the quench, a robot puts the casting into another machine to slice off the overflow and sprues from where the aluminum is injected.
The case is cast in two halves because of the size. If it were cast in one piece it would require a significantly larger casting press and even higher pressures. Splitting the case also gives flexibility for different sizes for different vehicles. Currently, all of the cases use a common front half and there are two different rear parts to accommodate a 13-module battery or a larger 16-module unit.
Taking Lots of Pictures Of The Battery Case
After casting and at the end of the line, the cases go through a photogrammetry machine. In the first stage, a system of 90 cameras takes thousands of frames that are stitched together into a precise 3D model with over 1,200 inspection points of the part to ensure that it’s dimensionally correct and flat coming out of the casting process. The whole process takes about 30 seconds and provides more accurate detail than a coordinate measuring machine that might take an hour to perform the same task. This faster cycle time allows for 100% part inspection. Similarly, the completed case is analyzed with another photogrammetry machine with 120 cameras.
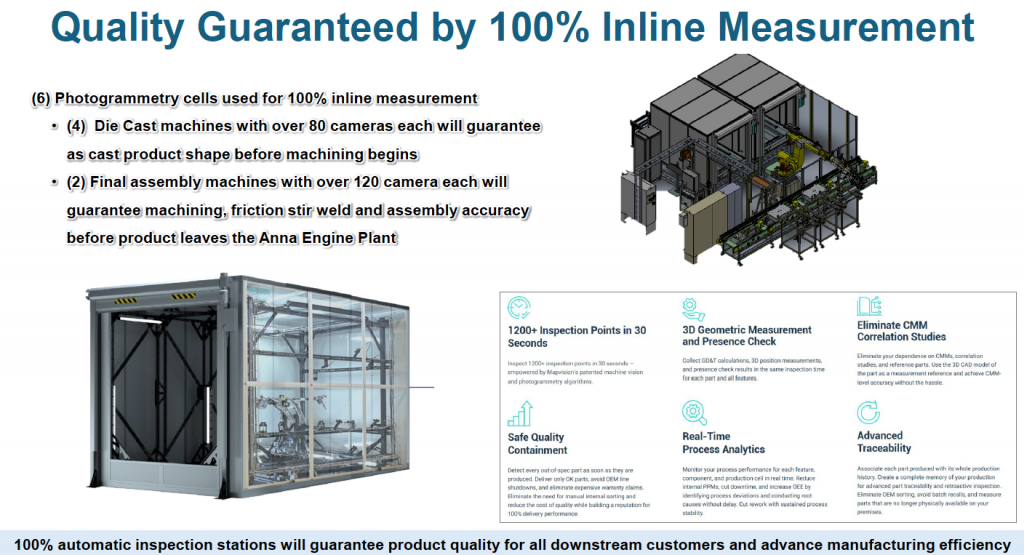
After the two parts are machined, they need to be joined. Honda is using friction stir welding, a process where a spinning head moves across the seam between parts which causes the material to partially melt into a plastic state and fuse together into a single part. As with many of the other processes, this reduces energy use compared to traditional welding processes and has no sparks or other leftover debris.
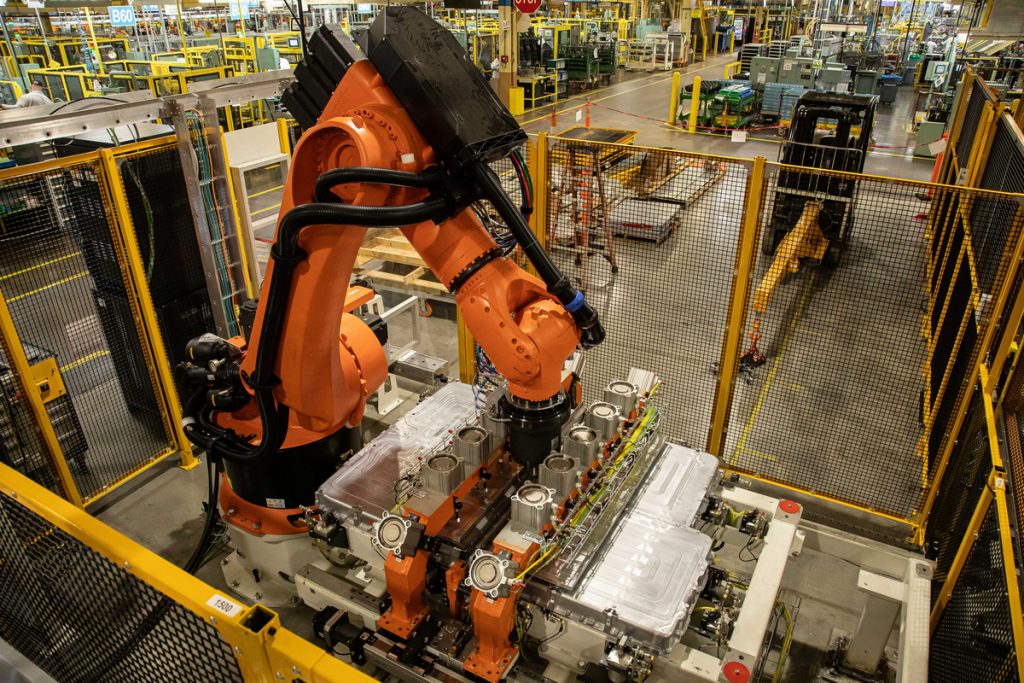
One of the final stages is adding the cooling plate. This is the first time that Anna has been supplied with components from Marysville. The body stamping shop in Marysville produces the cooling plates and friction stir welding is used to join the plate to the bottom of the battery case. In operation, the coolant to manage the temperature of the battery flows through the channels between the plate and the aluminum casing.
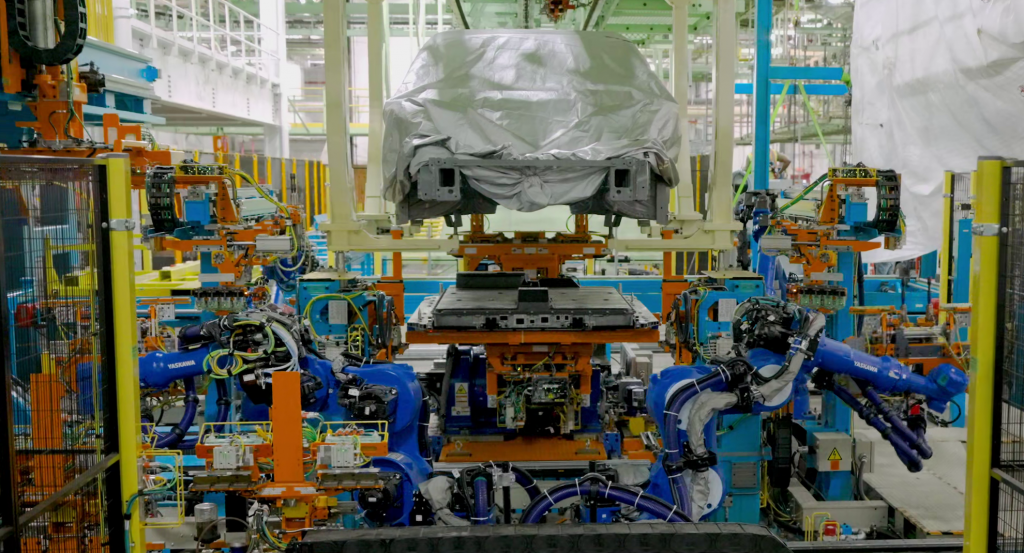
Is This the Right Approach?
Given all the uncertainty around EV adoption in the U.S. and the capital cost of tooling up to build any kind of vehicle, it absolutely makes sense to ensure that you can maximize the utilization of whatever equipment you have. Certainly some of the investment is dedicated to EVs, especially cell production. But having an assembly process that can accommodate anything from 100% internal combustion to 100% electric based on the market is the right answer for the foreseeable future.
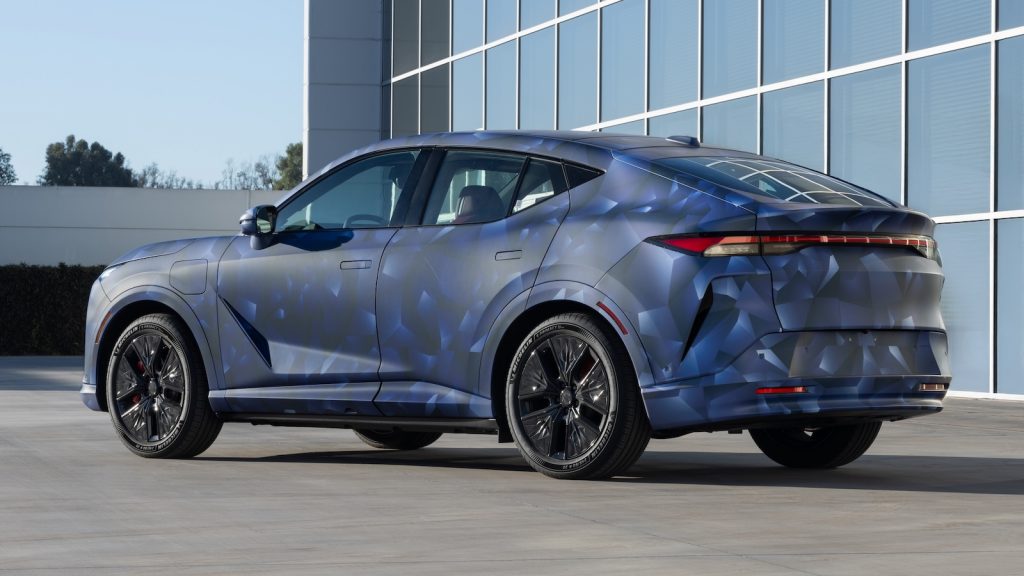
We’ll have to wait and see the technical details of Honda’s EV platform to determine if they’ve been able to take advantage of optimizations from not using a multi-energy architecture. A pure EV could be made simpler and lighter than a flexible architecture and with better packaging. It certainly seems like Honda has incorporated elements into its design that allow it to make better compromises for manufacturability while maintaining some of the benefits of an electric architecture.
The work done at Honda’s EV hub appears to be the best direction to go for now. Hopefully the vehicles that come out of Marysville (I’m far less confident about the East Liberty-built Afeela despite it sharing many components with the Honda and Acura EVs) will be worth the effort.
How refreshing to find a well-researched and well-presented article. In a time of half-baked click-bait and hack journalism, this was a nice change.
I was truly impressed with the clever and efficient engineering employed in the redesign of Honda’s factories. This same clever and efficient engineering is why I’ve been buying Honda/Acura products continuously since 1988. The engineering prowess comes as no surprise.
Wow, I’m just fascinated by the state of the art plant, assembly line, equipment, etc. That other engine plant looks like it would be fun to work in, or at least take a tour
Great, in depth article Sam. Thanks for your reporting on things almost all car buyers never consider. Build quality equates to longevity.
Hey! This article is about work I’m doing! Neat!
I work for an integrator just outside Detroit, and we’ve been working in Honda’s plants for around 25 years. I’ve always thought Honda’s manufacturing system far outclassed anything I’ve seen us build for GM, Ford, or the Tier 1 suppliers we work with.
This article, combined with the lack of Nissan merger, makes me want to work for Honda as an engineer. I have always loved Honda, and knew folks who went to work there as engineers. I love this approach to building cars. It is complete genius, and I agree that it places them in a great position moving forward. I feel Honda should just stay the same Honda they have always been, awesome.
Thanks for this Sam, this was a great read, and I look forward to more like these.
I wish Honda‘s natural gas plant could work out better. That seems like a good idea to me, especially if natural gas in your house already.
There natural gas PLANS! Stupid drunk auto correct
That’s a very good article. I’m not an engineer so these are only impressions. The flexible approach to manufacturing cars with completely different power trains is really interesting. I have no idea how it compares to processes at Tesla, which have had so much attention from Munro. To me it looks like very good hedging of their bets.
Munro quickly learned that you get the most YouTube views by absolutely glazing Tesla. I get that they have good engineering, but he tends to venture outside of engineering and has just become a talking head for them at this point, which is kinda sad
I might agree with that, but don’t really watch enough of him to be sure. Would definitely like to see more makes represented in his teardowns.
A lot of the interest in how Tesla does things is because unlike the rest of us in Auto Engineering (big 3 here personally), Tesla is the only real newcomer in the US market and doesn’t have the 30, 50, or 100+ years of “this is how we’ve always done it” momentum.
Back when I worked at a supplier, I worked on the proto Model 3. Unsurprisingly, Tesla had no clue what it was doing (Front impact beam/aka front crash bar/aka the steel bumper behind the fascia). My working theory is my experience may be roughly what Tesla has done on most facets of vehicle integration, where it relied heavily on supplier design and integration experience to figure out how to design cars. It would certainly explain why some things are near copies of legacy automakers, while others are a 180* flip from normal.
small steps, but it just annoys me that they are more like Toyota over at two wheels, sitting comfortably on their consolidated position, when they alone ARE the motorcycle market and could be the change we needed for electric bikes
Why bother changing motorcycles to electric? They represent quite a bit less than 1% of the fuel burned by cars, which themselves are not a majority of the CO2 emitted by the US.
If you want an electric motorcycle for some reason other than mitigating climate change, by all means go ahead and buy one of the ones that are available. But the return on investment just isn’t there from an emissions standpoint.
Folks may continue wringing their Fireblades out to 14,000 RPM guilt free, as far as I’m concerned.
Noise, pollution, smoothness, low maintainence and for a lucky few cheap, convenient home charging are good motivators to go electric.
Short distance city bikes and scooters? Sure. With swappable batteries FTW!
Dirt bikes? Maybe? As someone occasionally in proximity to such activities I like the idea of nearly silent dirt bikes ridden responsibly and bothering neither person nor animal. I dunno about the range and in-country charging options. Maybe if well spaced, well maintained solar/wind/battery charging stations (along with with well maintained bathrooms) were installed along popular riding trails. You folks who actually do such riding, please add your two cents.
Sportbikes? Maybe for a few if the prices drop. By a lot. But I think ICE noise and fury is part of the experience for a lot of riders.
Long distance cruisers? I think not unless as a mild hybrid to boost torque and range.
yeah I was thinking Gogoro, if they had that available I would be at the dealer the next day, even if they only had swapping stations at the dealer it would cover my entire city, mine would be at walking distance from my house
Lessee:
“With an introductory price that drops as low as just US $760 after government subsidies, the JEGO is positioned as an affordable new model to open up the local market further and entice more price-sensitive combustion engine scooter riders.”
“Riders buy the scooter but don’t own the batteries, instead subscribing to a swapping plan. That helps reduce the price of the scooter further and ensures Gogoro can get the longest life out of the batteries possible via intelligent charging and swapping doctrines. Having started its swapping programs back in 2015, Gogoro has learned that its batteries are lasting even longer than originally anticipated, with a new estimated lifespan of around 12 years.”
“An affordable new battery-swapping subscription plan was also announced along with the JEGO, offering new riders a US $7/month plan to cover up to 1,000 km (621 miles) of riding per month when signing up for a three-year plan.”
https://electrek.co/2024/04/25/gogoros-new-lower-cost-electric-scooter-breaks-sales-records-begins-shipping/
A 40 mph, $760 swappable battery e-scooter that costs $7/mo to go 621 miles*? With 100 miles per charge, swaps to a fresh battery in a few seconds and since you don’t own the battery you don’t have to worry about degradation?
Put in a decent network of swapping stations and yeah, that could work for a whole lot of city and sububan folks.
*assuming that is how it works and you aren’t paying $$$ in fees, taxes, kWh and other bullshit.
If you can pack a bunch of battery cells into a module, it’s the tight approach.