One of the many holy grails for the electric vehicle industry is the commercialization of solid-state batteries. The potential for improving energy density, reducing cost, and enhancing safety with solid-state cells is enticing for all involved. But there have been many challenges associated with this new type of cell.
Most automakers are either actively working on solid-state cells in-house or partnered with companies like QuantumScape, Factorial Energy, or SolidPower. Honda has been following the in-house development path and has just announced the completion of a pilot production factory in Japan.Â


The cells that make up current batteries consist of five main components. There is the positively charged cathode, negatively charged anode, separator, electrolyte, and the package. In current-generation cells, the cathode and anode are sandwiched with a separator between them, stuffed into the package and the whole thing is filled with an electrolyte.
The electrolyte is a conductive medium that allows positively charged lithium ions to move back and forth between the cathode and anode. The separator is a polymer film that does what the name implies, keeping the anode and cathode from coming into contact and short-circuiting which can lead to thermal runaway and fires.Â
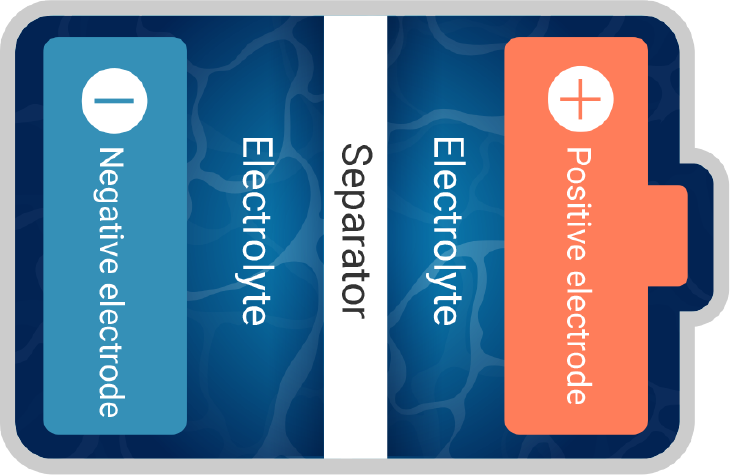
One of the major challenges with batteries today is that the electrolyte materials are flammable and cobalt oxide used in many cell chemistries releases oxygen when overheated, such as when there is a short circuit. This release of oxygen internally is what makes it so hard to extinguish a battery fire.Â
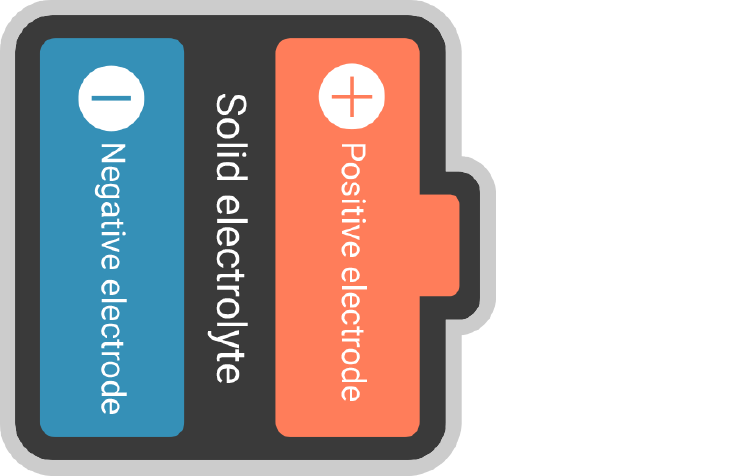
In a solid-state cell, the liquid electrolyte and separator are replaced with a layer of solid electrolyte that prevents the anode and cathode from making contact. This layer is also thinner than the liquid electrolyte, helping to enable more layers in a cell and thus higher energy density. Most of the companies developing solid-state cell technologies are claiming nearly double the energy density of current nickel-cobalt cathode lithium-ion cells, going from about 250 Wh/L to nearly 450-500 Wh/L. If this can be achieved, batteries could potentially be nearly half the size and weight while offering similar capacities or range could be nearly doubled.Â
What is Honda doing?
So far, Honda isn’t sharing very much detail on the chemistry of its solid-state cells except to acknowledge that it is mostly experimenting with sulfide-based materials for the electrolyte. This is consistent with many other companies in this field including SolidPower and Factorial Energy. In general solid-state cells can be made with most of the existing cathode chemistries including nickel-manganese-cobalt and lithium iron phosphate.Â
Where things get interesting for Honda is the work they are doing on the manufacturing process. Producing the cathode and anode typically consists of coating aluminum and copper foils respectively with a slurry paste. The slurry is usually mixed in large batches and applied to one side of the entire roll of foil. After drying, the foils are cut to the appropriate size for the cell format and the scraps are recycled. Honda has developed a continuous mixing system for the slurries and a process to apply only the amount needed to the foil for each electrode with a thin insulator frame around it to avoid short circuits. This should be a faster and more efficient process that removes cost from the production process.Â
Once coated, the anode and cathode are sandwiched with the electrolyte layer and run through a series of rollers. The pressure from this rolling process helps to pack in the electrolyte material and ensure robust contact with the anode and cathode layers. Without this pressing, the electrolyte tends to have voids in it, which increases the internal resistance and limits the ability of the lithium ions to transit between the electrodes.Â
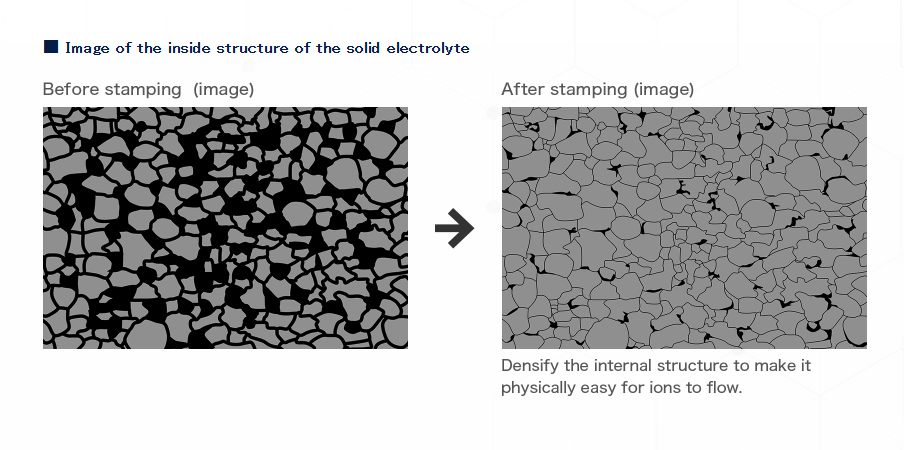
The new pilot plant in Sakura City consists of three main buildings, one for cathode production and cell assembly, one for anode production, and the third for electrolyte activation and storage. The images and video provided by Honda seem to show the cells as typical long, rectangular pouch cells that are currently used by many EV manufacturers. They appear to be similar in size to those typically used in vehicles rather than just the small form factor coin or pouch cells typically used for bench testing.Â
Honda is using the new facility to work out both the ideal material mixes as well as volume manufacturing processes for solid-state cells. At this point, since it is an R&D facility, Honda isn’t discussing the capacity of the new facility. However, at about 290,000 square feet, it is quite sizable and seems like it should be able to produce enough cells to conduct both lab and in-vehicle testing over the next several years with production starting in early 2025.Â
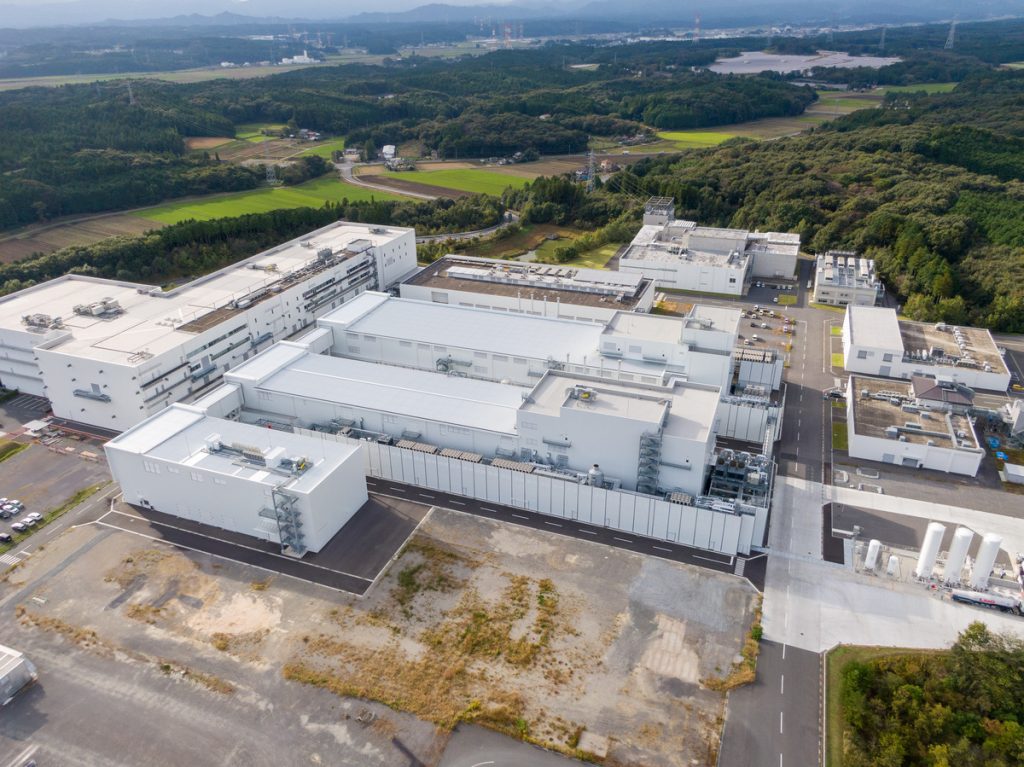
Like most other developers of solid-state cells, Honda is targeting the late-2020s for high-volume production. At this point, there are no announced plans about whether Honda plans to pursue manufacturing entirely in-house or partner with an existing cell manufacturer. Honda has a joint venture in Ohio with LG Energy Solutions to produce current-generation cells for the new line of EVs that it plans to launch in late 2025. Since Honda also builds motorcycles and aircraft, the company also hopes to be able to utilize solid-state cells for those machines, which are even more size- and weight-sensitive than cars.Â
> negatively charged anode
The anode is positively charged. What am I missing?
So the real solution is to have denser communities where you can walk to work, shopping, etc and public transportation so there would be less need for individual transportation. Like NYC.
No, lot of us do want to go out in the country or have stuff to move around. I prefer to live in the country and not to worry about the crimes, pollutions, and like. Some of us would do the shopping and errands in one go: it’s easier with vehicle than buses, subways, trams, etc.
Not every large city has good public transportation system. Houston comes to mind, which is the largest city in the United States without subway system. Sometimes, it takes FOREVER to go from point a to point b with the public transportation system, especially in Denver. Two-hour ride from Smoky Hill in Aurora to Pearl Street in Boulder is norm.
Sounds like you don’t have children so you don’t know what it’s like to have two or three children in tow along with other stuff to carry and such.
In Europe, some of IKEA stores without car parks have several delivery vans for the customers to peruse, transporting the large furniture packages home.
New York City’s subway system isn’t wholly barrier-free: some don’t have lifts or smooth pathways between the entrances and platforms without steps.
Wow, that sounds so unbelievably boring and miserable…I might as well be in a jail and have no life
Why? You can “see” world through the internet. Just get yourself a pair of Apple 3d glasses and be home for dinner. That and a good racing sim setup with bucket seat, stearing wheel, shifter and big curved screen that wraps around your peripheral vision.
I’ve never seen a technical discussion of how solid state batteries compare on an amp per square cm basis. Current flow can create hot spots, which in turn degrade cell components.
Honda tends to go it alone and hopefully they will suceed.
Are there any consumer products currently using solid state batteries?
There are some battery packs for camping and home backup that use solid state, but I’m not sure where else you can find them.
Design News has a nice rundown of the STLA Frame chassis for EV/REEV/IC body-on-frame SUVs and trucks. I doubt they’re ever going to offer a 3/4T 8′ bed REEV, but a guy can hope.
Check out Deboss garage in Canada trying to retrofit for this exact market –
https://youtu.be/eKyYZZTqcRA?si=BL_zVqTloP__iKu6
I’m very curious as I may soon be acquiring a 2000 ram 2500 Cummins long bed from the grandparents farm and the idea of running on electrons in the city and having that diesel take over otherwise is pretty enticing.
Thanks for the great explainer, I’ve actually never seen the reasons for LiON runaway thermal events so succinctly summarized. Thank you.
Oxidizers, baby! Everyone loves having something produce lots of readily available oxygen when it’s on fire!
Yep, it becomes an oxy-torch. That’s why oxygen cylinders and hoses have left-handed threads, to prevent mix-ups and their consequences.
Isn’t acetylene that has the left handed threads, and oxy is right handed? It’s been a hot minute since I changed out tanks.
No, oxy is left-handed, all hydrocarbons and inert gasses are right-handed.
I think you have it reversed, from what I can find. This jives with my memory:
What is the difference between A, B and C welding hoses?
WOW – I stand corrected. I knew one type was reversed.
Yeah, I knew one was always reversed. But I wasn’t confident as I’ve been off the shop floor for several years now and my memory gets fuzzy.
Same; always an engineer or supervisor, not a front line worker. Sometimes I lose the details.
I actually work for a battery electrode coater… I’ll be heading down to check on the coater in about 5 minutes, then up to the calender (yes, calender not calendar) which is the “rolling” process, along with other stuff…
You can’t just leave us with this comment! We need MOAR from an insider. Are you allowed to share your thoughts???
I can share some thoughts, but not all. I work for what we generally call a “toll developer” or sometimes a “toll coater”. We don’t make our own electrodes; it’s all for outside customers. The come up with the formulations and requirements, we make it on a R&D type scale. Mostly trying to turn a customers lab-scale product into one that is viable to actually make in a production environment.
We’ve had lots of big name brands come through us, but it’s mostly start ups that most people will have never heard of.
I wonder if we will ever get to a point where a battery is as energy dense as a tank of petrol ? Anybody ?
By weight or volume?
I was thinking volume. As in replacing my current petrol tank with a same size battery and having a similar range with a motor as the original ICE did.. If you get what I mean.
I have a very shallow knowledge of this stuff, so take it with a grain of salt, but my understanding is that just replacing the volume of the tank with an equal volume of batteries is a huge challenge.
From a broader perspective, though, EVs offer a lot of potential space savings over regular vehicles. Electric motors tend to take up less space than engines, and you can also ditch the exhaust system, which takes up a lot of space.
Actually rearranging those space savings and using them for batteries isn’t exactly straightforward though. EVs have certain demands that don’t exist for regular vehicles too, like the charging system. But just talking about volume, EVs have a lot of opportunities to maintain usuable volume for passengers and cargo despite having to use more volume for batteries than a gas tank. And of course shrinking batteries would help improve that.
Some very rough, basic estimations for one “random” vehicle:
Miata has ~12 gallon/45L gas tank, and say 350-400 ish mile range
A quick google shows at least one result for prototype energy density of ~1000 Wh/L- https://evboosters.com/ev-charging-news/breakthrough-in-lithium-metal-solid-state-battery-technology/
At 1000 Wh/L, or 1kWh/L, that 45L gas tank could in theory be about a 45 kWh battery.
Since a Miata is small and light, I would think it could at least match the 5 miles/kWh I see with a Bolt under nice conditions.
5 mi/kWh * 45 kWh = ~225 miles of range, which doesn’t quite match the 350-400 miles, but isn’t that far off.
If you count space savings of eliminating the engine and transmission, you could argue that some extra space could be used for a bit larger battery to more or less match the range. Or, keep the range lower, and save the weight to potentially have a slightly lighter EV than the current car if all the balance of plant type of parts can be kept to a light weight.
As others have mentioned, the energy density of the battery will still be much less than the chemical energy in gasoline, but the higher efficiency could bring the range up to near the same level, assuming that batteries of this sort can be commercialized in high volume.
A full gas tank only has about 10% vapour volume above the fluid level. If batteries can match a gas tank in either J/m^3 or J/kg that’ll do.
I’m in no way qualified to answer that, but maybe we don’t really need all that energy density to propel cars? Gasoline is so energy dense, we spent the last century continuously creating and perfecting mechanical systems to be strong enough to withstand controlled explosions and use some of the energy they create. And yet, some 80% of energy is lost as heat, requiring complex cooling systems. Most online sources tell me EVs cut down energy loss to around 11% only.
Again, not really in the know, just using common sense here: feels like too much energy density is a thing, if 80% of the actual energy output is wasted and requires added complexity to prevent that wasted energy from destroying the engine. Anyone more informed, please do correct me if I’m wrong, as I would love to understand more about this.
I expect the advantage to more energy dense batteries is having smaller batteries overall in the cars. Reducing battery weight would have lots of advantages, not the least of which being the battery is expending less energy hauling itself around.
We’re still losing energy to heat in an electric system, just not nearly as much. problem is, those components are less tolerant to heat than those that make up an engine, so systems to manage that thermal envelope are still needed, despite the massive gain in efficiency.
Yes, you want the highest energy density possible, it improves essentially everything else about the car. The problem with batteries is that they have terrible energy density compared to liquid hydrocarbons. Like 1/50th for the best experiemental batteries in a lab, and really 1/100th in a real world application. A multi-thousand pound battery pack takes a hell of a lot more energy to accelerate from a stop or lift up a hill than 40 lbs of gasoline, and you are paying this penalty essentially as long as the vehicle is in motion.
Drivetrain efficiency is but one of the many factors that determines the overall vehicle efficiency, and yes a BEV drivetrain is quite a lot more efficient than an ICE one, but gets (literally) dragged down by it’s grossly inefficient energy storage mechanism. Get better batteries and everything improves.
I get that more energy density is better, and I’m aware of the huge defference of the difference between liquid fuels and batteries in that aspect; of course we should always be looking at ways to improve energy density in batteries, but I’m questioning if it even makes sense to expect energy density from batteries in the same order of magnitude as gasoline in our lifetimes, when maybe we could do quite a lot with smaller, more realistic increments. If we could achieve, let’s say, 1/20 energy efficiency for batteries when compared to ICEs, maybe we’ll have short-range batteries the size of gas tanks that can be used in many applications? Not all driven miles are road trips after all.
With our current understanding of physics and chemistry, no, there is no way batteries will approach liquid hydrocarbons in terms of energy density. At a basic level, batteries are chemical reactions that release current, and the chemistries we use in vehicle batteries happen to be mostly reversible when current is input. Thanks to the laws of thermodynamics, this reversible process will always contain less energy than a irreversible one (such as burning hydrocarbons) and because it requires basic “structural” components such as the annode, cathode, and separator that don’t directly contribute to energy storage they will always be many times less energy dense than something you can consume 100% of to release energy.
Realistic increments is a much better idea, like PHEVs with small batteries for short daily trips. The other thing that may end up making the point moot for quite a lot of the transportation industry is ironically solar panels. Solar has gotten so frigging cheap recently that people are exploring novel uses like synthetic fuels that, since they are just distilling C02 from the air are carbon neutral and are a much better store of energy than having to plug solar arrays into the grid (contrary to popular belief, power is not fungible and most solar is generated far from where it would be most useful).
I’ve read about Porsche’s synthetic fuel facility in Chile – that one is wind powered, I believe? – and it did look promising on paper, especially when you have renewables whose peak production requires methods like pumped storage to deal with the excess energy being produced. That energy being diverted to making clean fuels seems like an excellent idea, and from what I undestood, viability depends mostly on scaling up production – which could be achieved using the existing infrastructure. But as with everything else in life, I’m hoping for a diverse future when it comes to energy, where even fossil fuels may have a place if used in moderation and where it makes sense. I’d love to see a future with a variety of options from fossil fuels to hydrogen, EVs and synthetic fuels all competing and spurring innovation in all fronts.
Engines produced in 2024 are a lot closer to 40% efficiency than 20%. Something like a Prius engine that runs an Atkinson cycle is 42% efficient, but even a non hybrid Corolla engine is up to 38% now.
….then you get to the frictional, thermal & gearing losses from the transmission, differential and cooling systems, which reduce that efficency a fair bit.
Not to mention the efficiency of pumping some primordial ooze out of the ground (assuming no need to frack to get it), transporting it hundreds or thousands of miles away to a refinery, breaking it into the desired chemistry, pumping it into something else to transport hundreds of miles away to your local liquid fuel market, then pumping it into your vehicle.
It’s a very inefficient way to power your vehicle – when the alternative is to plug it into your wall socket, which optimally, might be connected to a solar panel array on your roof – or at the sub-optimal extreme, might be powered by a large ooze/rock to electron thermal conversion device that runs off some derivative of the things made and transported all over the place in the above process – yet you still get something like 80%+ efficiencies from plug to road.
The efficiency of pumping things out of the ground is measured in EROEI (energy return over energy invested) because this is over 100%.
If you only read EV advocacy sites, you hear a lot about 20% efficiency like it is still 1994. Efficiency has doubled in 30 years.
Source for your claim? Because that’s not the case at all.
Just refining oil into gasoline is 85% efficient.
Overall processing and transporting is roughly 75% efficient.
There’s much more to the story:
https://rmi.org/the-incredible-inefficiency-of-the-fossil-energy-system/
While efficiency of some vehicles perhaps have doubled – that certainly does not apply not all new vehicles, and depends on the way they’re driven (Stop-Start systems disabled, fast starts/fast stops, lengthy idling, etc) – and is nowhere close to the 80+% efficiency of EVs, where the propulsion motor uses energy only when the vehicle is in motion.
The energy to refine and transport comes from the oil itself. Rocky Mountain Institute is an advocacy group that is not a source you can link to and think it proves your point. LoL.
“The energy to refine and transport comes from the oil itself.”
Correct – Which means that production is far less than 100% efficient.
RMI may be biased – but so is the Big Oil Brain Trust.
“Some authors argue that energy self consumption should be excluded from energy investments, as it represents energy that would not have been available to humanity anyway if the energy system considered was not operating”
https://www.nature.com/articles/s41560-024-01518-6
A good source is going to be a recent article from a recognized peer reviewed journal.
Most likely no. After 60 years of development, lithium ion chemistry is at 250 ish W*hr/kg, and 450 W*hr/l. Gasoline is 12,000 and 8,600, respectively.
Even after you compensate for the handicap battery systems are granted by “paying” for their conversion from chemical into mechanical/electrical energy at the power plant, before going into the battery, batteries would need to get at least five times more dense on a volume basis for this to happen, and more than that on a weight basis.
Densities actually HAVE improved about 5x in the past 35 years or so, but for that to happen again, changes would have to happen that are revolutionary, not evolutionary. That kind of energy density exceeds the theoretical limit of our most volatile chemistries, even if you assume you can eliminate the need for things like cooling, cases, and electrodes.
Probably more favorable if you calculate in the size/weight of a gas engine vs. an electric motor. But still, if we’d been driving electric cars all this time and just now discovered gasoline, people would think it was amazing stuff!
I don’t think so, but that just really accentuates the waste of ICE, not the failure of BEV. Something like 70-80 percent of the energy in a tank of fuel is lost as heat. EVs lose only about 30%.
So, a battery would really only need to be 1/2 as energy dense to equal a the same volume of petrol.
EDIT: I didn’t see Do You Have A Moment To Talk About Renaults’s response. He has a bit more explanation.
Well, gasoline is 9500 Watt-hours per litre but you only get 1/3 or 1/4 of that to the wheels, so let’s call it 3000Wh/l. That also doesn’t count the engine/transmission/radiator which is a lot more volume than an EV drive unit, almost as much as another gas tank. So call it [waves hands] 1500Wh/l.
Looks like current SSB tech is at 1070Wh/l. If that’s the case, this could be pretty exciting.
Still need the battery thermal management system. So at very least you have circulating coolant and a heat pump with it’s exchangers.
Hence the [handwave] – sure, you want a coolant loop for battery, motor and motor controller, as well as an A/C condenser. Not nearly as much heat to dump as an ICE though.
Really curious to see what SSBs do for motorcycles though. Never mind massive range, I want a cheap lightweight city runabout with 4-8 kWh and 10-20kW motor.
It makes sense to do the research at a facility that is also being built for production. The safety concerns are the same and having the production folks involved makes sense. When research is done separately, the processes and personnel involved do not have the same goals.
They are certainly not fucking around on the scale front. They are just going for it. The confidence it shows means we may finally get that doubling of density for real. I can’t wait. Although I can only imagine what it will do to current chemistry used EV values. Can they get much lower?
I could see a thriving battery refurbishment industry for used EVs. Recycle the old chemistry batteries and replace with newer ones for either a lighter car or a bunch more range.
I thought of the same thing, but then realized that because of all the other packaging and control system stuff that it just wouldn’t make sense.