If you’re a casual racing fan you’re likely aware that race teams don’t bring the same car to the track every weekend. In NASCAR’s Xfinity Series, which still uses the old-style stock car the sport has long been known for, teams are allowed ten chassis that have to be spread across 33 races on courses as different as the streets of Downtown Chicago and the high, fast banks of Daytona International Speedway.
How does this even work? Quite simply, cars have to be reused multiple times in order to make it through a season, though how those cars are allocated is entirely up to the team. At least, it’s mostly up to the team. Because of the variety of racetracks, teams have to allocate the different types of chassis to what they believe best suits their needs. For example, a team could have one superspeedway, two road courses, two short track, and five intermediate chassis in their inventory and be in compliance with the rules.


Non-fans might picture NASCAR teams driving the same oval again and again. This isn’t at all what happens.
The 2025 Xfinity Series schedule includes four races with the full superspeedway specification of chassis and body, two at Daytona International Speedway and two at Talladega Superspeedway. Seven of the events take place on road courses, including two back-to-back at the Chicago Street Course and Sonoma Raceway in July. Three events will be held on drafting ovals, two at Atlanta Motor Speedway and one at Indianapolis Motor Speedway. Eight races will be held on intermediate-style ovals, five will be held on traditional short tracks, and the remainder will be contested at venues that fall somewhere in the middle like Phoenix International Raceway.
Given how few of these course types are back-to-back, building a car is a nonstop juggling act. I’ve been lucky enough to work on this process through its various stages in my racing career, and I’m going to give you a peek behind the curtain so you can better understand how a modern NASCAR operation gets a car to the track.
Start With What You Know
The lifecycle of an Xfinity Series racecar typically begins in the background about six weeks prior to the actual event. At this point, the crew chief and engineers will sit down to begin an initial build sheet. In this meeting, the group will start by reviewing the last couple of events at the race track in question. Together, they will pour over driver comments and personal notes from the events to refresh everyone’s memory on what exactly happened. This generally starts with looking at the sim models from the events and trying to determine what the team’s biggest struggles were. For example, at the last race, corner entry to center might have been good but all weekend the car had too much understeer on exit.
Once the deficits have been established, the group will then look at similar notes for the teammate cars. Maybe your car ran about seventh to tenth all day but your teammate was in contention for the win. What did their car have that yours did not?
From all of this information, a general suspension geometry will be settled upon. This doesn’t have to be super refined. Exact dynamic cambers, slips, springs, shocks, sway bar, track bar heights, wedge, and nose weight can all be finalized later but these settings should generally be within the ballpark. The initial setup generally defines the components and pivot points that will be used to assemble the car within about 85% of where the final product will be.
This initial setup sheet is then sent out and will allow the suspension department to begin preparing inventory and monitoring what is being sent to the racetrack. Every part of the car has a mileage limit and crash damage is not exactly uncommon in NASCAR racing. In 2025, the Xfinity Series will visit Darlington Raceway on April 5th and Texas Motor Speedway on May 3rd. If the suspension room doesn’t know at least what the teams generally plan to run in Texas, they will not know which components need to be repaired or replaced immediately and which repairs can wait after Darlington to have enough parts for Texas.
The typical race spacing for a chassis is about four to six weeks between events, let’s go through the life cycle of a chassis on the four-week rotation.
4 Weeks Pre-Race
Monday:
Post-race teardown begins at 6 am. Cars returning from the track will be placed on jack stands and photographed in detail. These photos include everything from temperature strips on brakes and driveline components to cooling duct openings and suspension components. They act as a safety net in case someone makes a typo in the database notes or if records were for some reason incomplete. By the end of the day, all of the returning cars will have had their suspension, driveline, and interiors stripped.
Above you can see the JR Motorsports teardown bay featuring two #9 Chevrolet’s. On the right is the primary car which was wrecked in practice. The interior has already been removed and you can see the oil lines laying on the ground by the left hand side of the car. On the left is the backup car which was raced. Mechanics are beginning to remove the front and rear suspensions. These weeks are always a bit of an extra pain.
Tuesday:
The returning chassis will have body panels removed and then be sent outside for a thorough cleaning. Once the chassis have been cleaned, they will be measured and evaluated for damage. Sometimes even innocuous wheel-to-wheel contact or a brush with the wall can be enough to bend something like an upper control arm plate. The chassis will be thoroughly inspected and a repair list will be generated for each one.
The following items are considered “non-major” repairs and do not require a chassis to be recertified in accordance with NASCAR Rule 14.3.1.6.2.6:
Engine mounts, trailing arm mounting brackets, shock mounts, upper control arm plates, jack screw sleeves, seat mounts, jack posts, track bar mount, additional ballast containers, battery box, idler and pitman arm mounts, front sway bar mounting tube
Wednesday through Friday:
The chassis will go to the fab shop for any of these non-major repairs. If an entire front or rear clip needs to be repaired, or any other major repair, this chassis will be temporarily taken out of rotation until the work can be completed and certified by NASCAR. After the chassis have been repaired, they will be transferred to the body shop. The body shop will install a new body and replace all of the interior panels.
The NASCAR Xfinity series utilizes a composite body made up of thirteen interlocking panels that are flange fit to the chassis. The panels are made and sold by Five Star Race Car Bodies which also provides bodies for the NASCAR Cup series, asphalt late models and multiple divisions of drag racing cars. A complete body, excluding windows, retails for $10,600 but panels can be purchased individually. Quarter panels are $720, front fenders are $460, a hood is $988 and so on and so forth. Used body panels quickly pile up behind the shop over the course of the year and many are resold in the gift store as souvenirs. Companies like The Racing Warehouse have turned these used composite panels into a sizeable retail business that allows both teams to recoup some of their costs and fans to own a piece of the action.
https://theracingwarehouse.com/product-category/race-used-sheet-metal/
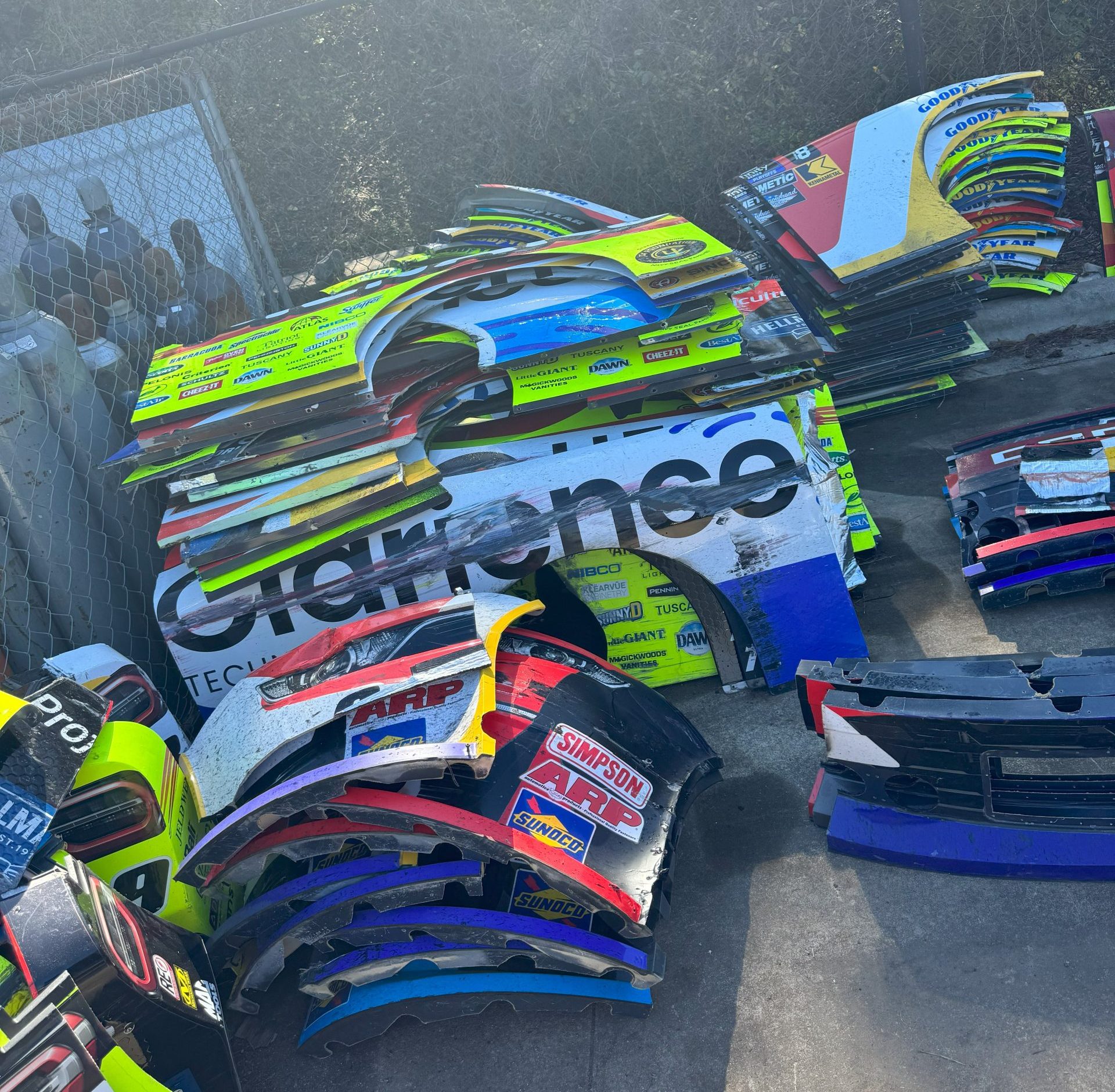
By the end of the day on Friday, the chassis will be awaiting suspension assembly. At this point in time, a suspension cart will have been put together by the suspension room in accordance with the build sheet. This cart includes all suspension components with their corresponding shims and slugs and can be easily wheeled to whichever assembly bay the chassis ends up in.
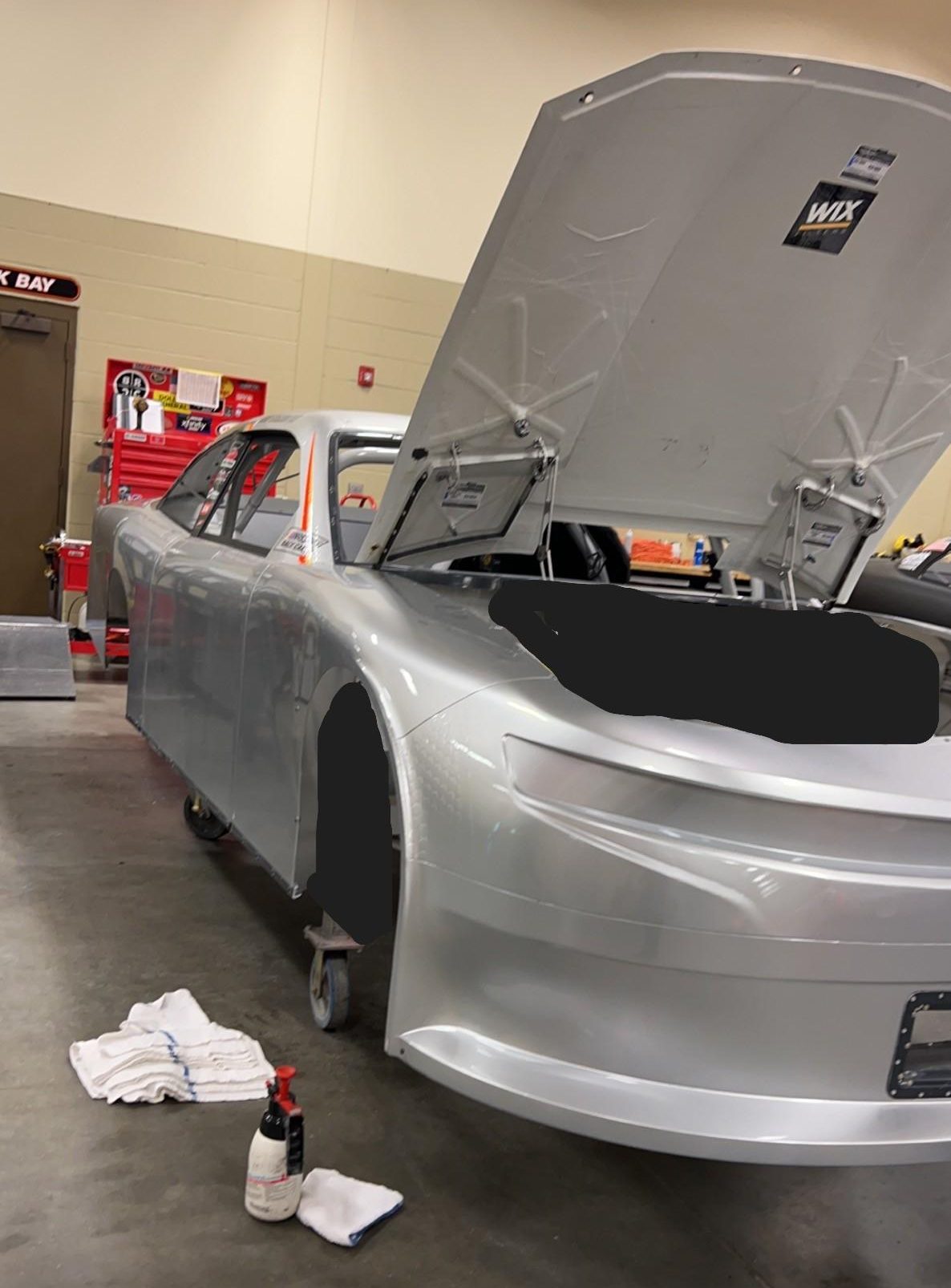
3 Weeks Pre-Race
Monday and Tuesday:
The cars, with their new bodies, will be pushed out onto the shop floor and the suspension cart will come to meet each one. A team of shop mechanics will go from one car to the next to hang their suspensions.
Once the suspension is hung and the interior is mostly assembled (sans seat insert, driver comfort devices, dash panel etc), a mock-up motor will be installed and the cars will be ready for initial setup. A mock-up motor is literally just an engine block that has been filled with ballast (typically lead shot) to account for the weight of all fluids and other components. This weighted block mounts to the four engine mounts and gets the total vehicle weight fairly close to what it will be when the driveline is fully installed.
Wednesday
The cars will be rolled over to the setup plate where each team’s car chief will go over the initial setup. They will check all the suspension angles (caster, camber, toe, bump steer, etc) and match the assembled vehicle to the targets generated by driving hundreds of laps in a simulator. The total vehicle weight is achieved by using additional ballast and the car is roughly scaled in on race springs.
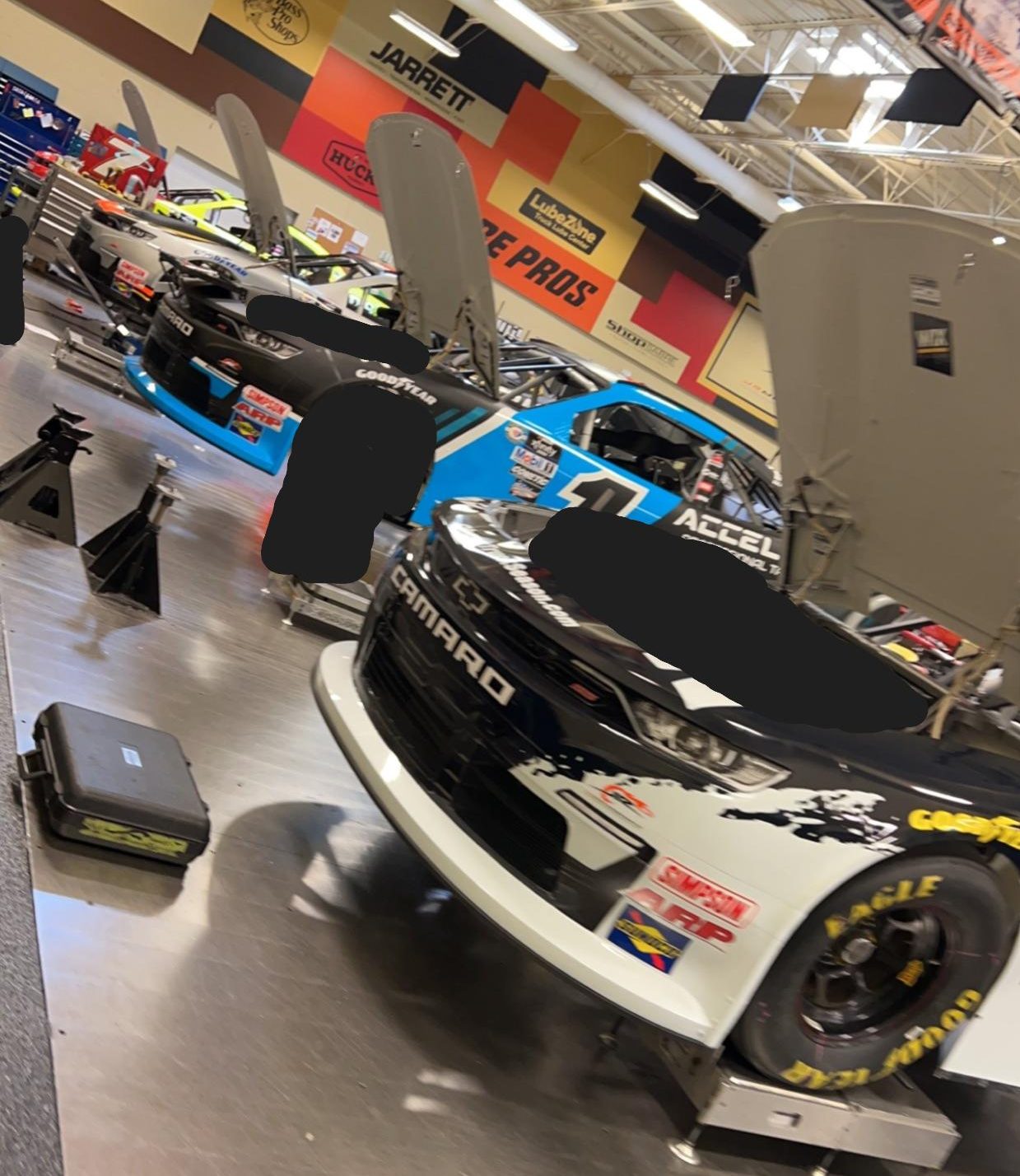
Thursday and Friday:
The car will be set to the side to be wrapped and have other detail items like the windshield and back glass installed. There are various companies that print wraps, but a full body wrap typically costs between $2,500 and $3,000 with an additional fee of around $500 to wrap the car itself.
2 Weeks Pre-Race
Monday:
After the initial setup has been completed, each car will be sent over to the Hawkeye laser inspection station where the team can perform a body and chassis scan in the same way that it will be inspected by NASCAR at the racetrack. At this point, things like wheel spacer, rear-end housing location, camber, and rear toe settings will be adjusted based off of the Hawkeye scan. Once the Hawkeye scan looks reasonable, the car will head back over to its setup plate. The car will be placed on scales and one of the shop engineers will perform a Romer arm measure of the racecar. An experienced measurement engineer can typically measure one car per hour.
After the Romer arm measure, the engineers will create a “setup as measure” sim. Each build sheet is typically done with what we call “design parts” which are the CAD baseline for each type of part. It’s difficult to know which exact parts will be available from inventory weeks in advance so these CAD-spec parts allow engineers to work weeks ahead of schedule. The real parts, however, all have tolerances once they are built and these tolerances compound on each other. For example, the front suspension on each corner is composed of an upper and lower control arm, upper and lower ball joints, a spindle, a hub, and wheel spacers. These, as well as the chassis mounts, all have tolerances. Even the shims and slugs have tolerances. A perfect 1/16” camber shim should be 0.062” thick, but in reality, it might only be 0.060” thick.
When the car chief sets up the car, they will adjust the shims and slugs to make the real car match up with the sim targets. When the car is measured with a Romer arm, all of the suspension pivots, wheel centers, and suspension angles are accounted for to at least two decimal places. The engineers will then use offsets (essentially fudge factors) in sim to account for all of these real-life tolerances in the virtual world. This way the sim model exactly matches the real thing.
Tuesday or Wednesday:
The car will then be moved over to the pulldown rig. There are two types of rigs that essentially do the same thing for teams. The first is a Mittler Brothers-style rig which retails for $97,500. On a Mittler rig the entire car is rolled onto a raised platform. With tires, shocks and bump stops installed the chassis is pulled down onto the scale pads. These rigs are load-dependent, and using one accurately requires having a good grasp of what the dynamic wheel loads on track will be. Teams will use load cells to determine things like bump stop and sway bar load. The scale pads also move up and down individually to allow teams to check things like bump steer and dynamic camber. There is a ground plane between the scale pads so teams can visually inspect things like splitter height and side skirt lengths. Setting the tires to their estimated hot pressures for testing will allow them to account for tire deflection as well.
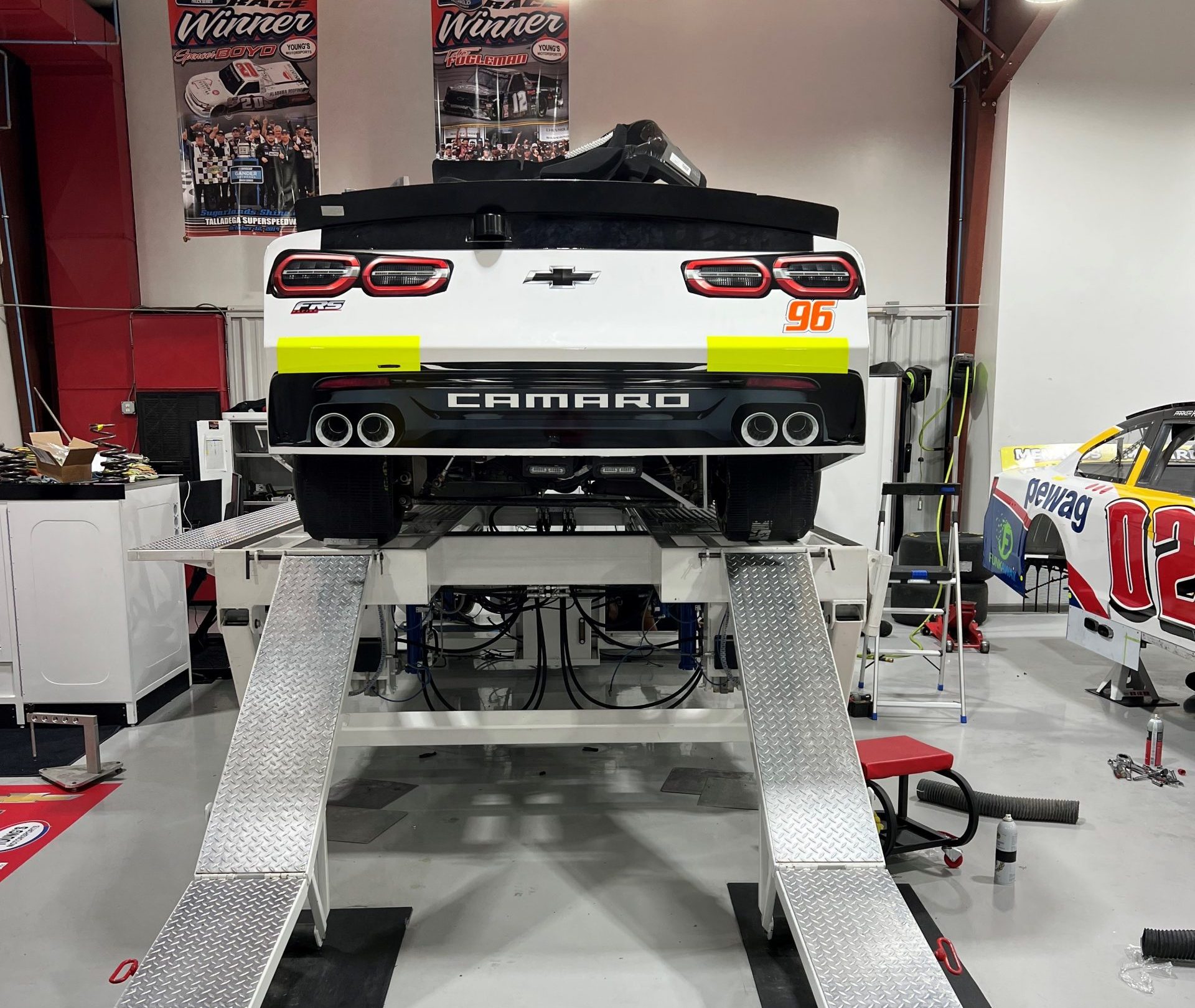
You can see how the machine roughly works in this video posted by Mittler Bros.
The other system is a Petree-style rig, named for former crew chief Andy Petree who developed the system. This system is technically a push-up rig, but its use is still colloquially referred to as “pulling down” a car. On this rig, the chassis is fixed in place and the scale pads are moved up and down. These rigs are travel dependent rather than load dependent and teams will travel the suspension up to their desired race travels.
On a Petree rig, the tires are swapped out for steel wheel plates that do not deflect and the shocks and sway bar are not installed. This rig simply makes a map of wheel rate versus displacement which can be imported into the sim program. It is not necessary to test the car on tires because the sim program will calculate things like a tire’s loaded radius based on a computerized tire model. Other things like sway bar and bump stop load or dynamic camber will also come straight from sim.
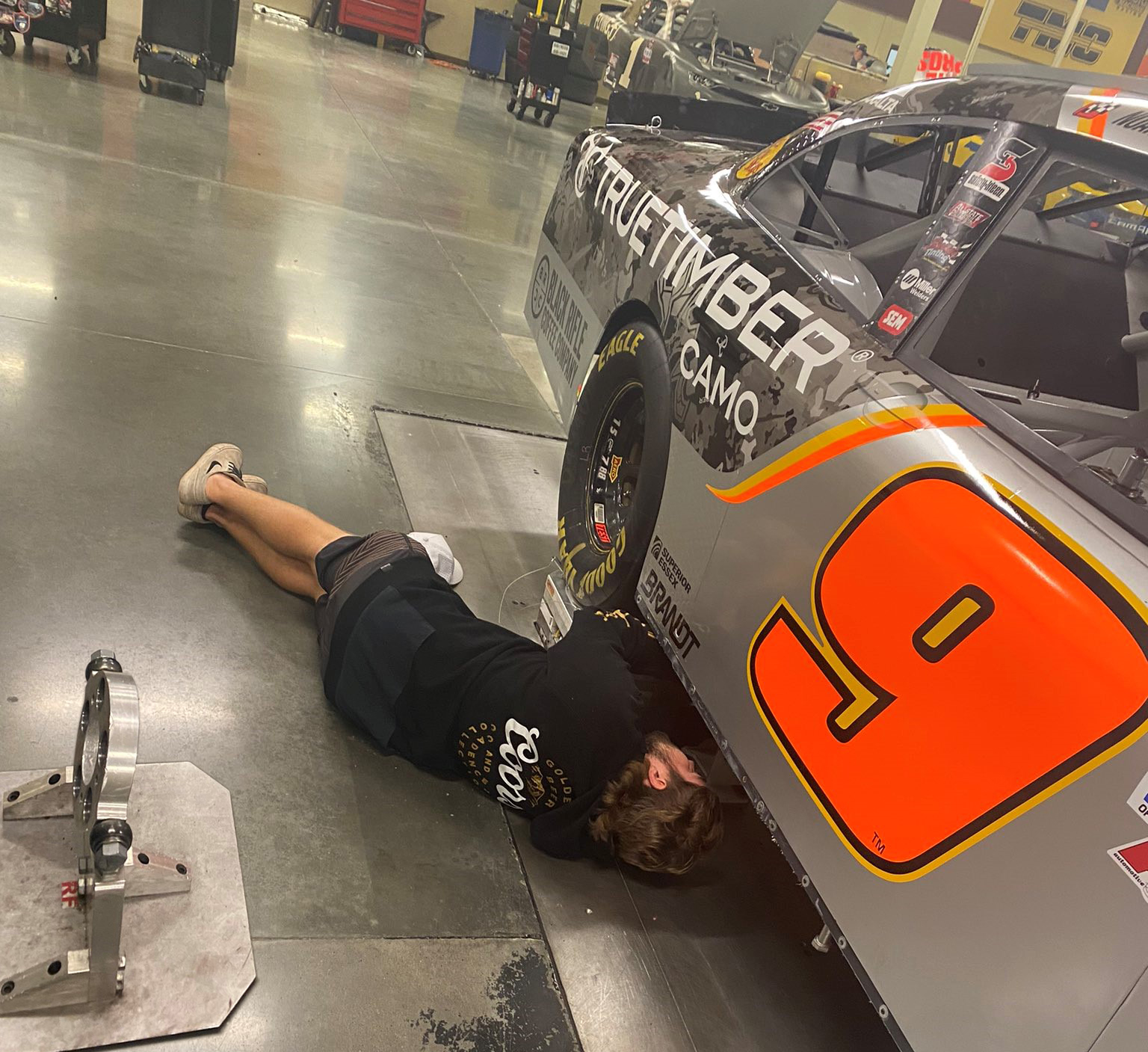
Pulling down a car typically takes between 2 and 6 hours, but can turn into an all-day affair depending on the suspension geometry that the team is trying to run.
Thursday:
This is when the race motors will arrive at the shop. The mock up motor will be removed and the race motors are installed. Once the motor is installed into the chassis, fluids are added and the motor is taken through the initial fire-up procedures.
Friday:
The cars will then be prepped to go to the chassis dyno. A chassis dyno is essentially a giant treadmill for racecars. This is where the engine tuners will finalize all of their settings and make sure that the drive line is performing optimally. Not only will the final power output be determined, but any leaks or driveline vibrations will be detected and rectified.
Race Week
Monday:
Team mechanics will spend most of the day finishing all of the knickknacks, bobs, and bits on the car. This includes things like running the cooling ducts, cutting side skirts, sealing up crush panels, changing studs, and finishing the interior of the car. None of these items require a final setup sheet from the engineers, but they all take a significant amount of time.
While the mechanics are finishing up their detail work, the crew chief and engineers will be preparing final models to run in the simulator.
Tuesday:
The JR Motorsports #1 team I work on goes to the simulator weekly on Tuesday morning. The session is split roughly in half between this week’s track and upcoming events. We will start the session with a final evaluation of and tweaks to the current racecar. At this point there will not be any more major changes but smaller things like shocks, springs, nose weight, wedge, and track bar heights will all be finalized. Once a decision has been made on these items, a final setup sheet will be sent out to the mechanics to begin finishing the racecar.
In the post-Covid era of minimal practice, the simulator is a critical tool as it is essentially the only way that teams can evaluate new setup ideas.
Wednesday
Once the car has been scaled with its final setup it will return to the Hawkeye for final body and chassis scans. The body will be fine-tuned down to the thousandth of an inch and all of the chassis’ measurements are locked in. Each Hawkeye machine reads marginally different, and teams will keep track of the offset from their machine to NASCAR’s at-track machine. In this final fine-tuning process, teams will push their car right up to the line of what they believe will pass inspection as well as make a plan for how to fix it if they pushed slightly too far.
This process often takes several hours and teams will race to be the first one done scaling on Wednesday morning to get into the Hawkeye before their teammates. By mid-afternoon there is usually a line across the shop floor as teams wait their turn in the Hawkeye. After the crew chief signs off on the final Hawkeye scans, the racecar is ready to be loaded and sent to the track.
What Happens When You Get To The Track?
Your car has to be locked-in before it arrives because practice time is extremely limited and your driver will be qualifying after only a few laps. If you did your job well, the driver will have the car they drove in the simulator and your driver will be informing you of how grateful they are for all the hard work you did.
Oh, yeah, and you’re going to do all the work above knowing you might go to the track and watch the car you spent weeks making perfect for the race get promptly stuffed into the fence. See below, Indianapolis Motor Speedway lap 1 turn 3. Pain.
I’m impressed how teams can plan and prep the cars for a particular track a couple of weeks in the future while simultaneously dialing in a car to race this weekend on a very different type of track.
How many people-hours does it take to prep for a single race? Must be thousands.
Also, I’m intrigued by the tight tolerances that you’re aiming for when the car arrives at a track for a weekend. What do those same measurements look like after a race and the car has been pummeled for a couple of hours? The pic in the article of the JRM Chassis 1249 after the race at Darlington shows that it went through the ringer.
Working on multiple cars in the same day is very conducive to my severe ADHD. We’re constantly bouncing from one to the next.
Pre race and post race inspection tolerances are different and there’s an allowance for damage.
Thank you Aedan for doing the deep dive! I am a lifelong NASCAR fan and roundaboutly related to the Wood family and love seeing this sport showcased in a positive way instead of “cars go round” articles of other sites. Great writing!
Thank you!
What is a drafting oval? Google didn’t help.
It’s basically a regular oval where the cars run a restricted engine
Aedan thanks as always. The level of detail you provide in the articles is a real pleasure to read. And the amount of prep for each car is almost hard to believe.
I have been following NASCAR for 60+ years now, but have learned more from your articles, especially on a tech level than I ever have watching the stuff on TV. And that is appreciated greatly. I realize that the time for TV based “education” is obviously very limited, but you step this up in a huge way. Like bigly.
Does NASCAR have inspectors that travel to the shops to examine the cars after a big wreck, or how do they determine that a damaged chassis is too damaged to be approved to race again?
Another question, would you rather work on the Cup side or are you looking to one day again? I apologize if that puts you on the spot.
And really appreciate that the Autopian staff chooses to run your articles. Not only do we learn, but I bet it also helps to bring more non racing fans into the racing community. Thanks to all involved here.
Merry Christmas to you and the family too. I hope your little one is doing well.
Thank you! There are multiple points of measurement on the chassis that determine whether it is in spec or out of spec after a wreck. It doesn’t put me on the spot, I would love to go cup racing again and JR Motorsports prides itself on graduating to cup. That being said I’m quite content right now.
Thanks for the reply. I need to clarify my question regarding a damaged chassis.
Who re-certifies a damaged chassis? Does NASCAR send an inspector to the shops?
Or is it approved by NASCAR at a track? Sorry if my question was not clear.
You have to bring it to NASCAR to be recertified
Thanks.
They measure it with a Romer arm and compare it to the last time the chassis was certified
What percentage of the teams on the Xfinity grid do this level of prep?
JR Motorsports (4), Joe Gibbs Racing (4), Haas Factory Team (2), Kaulig Racing (3), Richard Childress Racing (2) but then there are multiple alliance teams as well that have cars prepared by these teams
And sometimes the driver spins in someone else’s oil in practice and bins the whole thing. That’s gotta be gut wrenching.
Phoenix was a rough weekend this year but a good exercise in teamwork and preparedness
Fantastic as always, Aedan, and definitely relieves some of my post-season depression of going to check TVRacer for the schedule and then realizing damn, no more racing on the weekends anymore.
Dumb question but I have to ask: are the contingency stickers still actual stickers that have to be applied individually, or are they part of the wrap process now?
They are applied over the base layer of the wrap
so here is my question, is the next gen cup car easier or harder to get ready from the “ground up” Does it take 4 weeks to build?
I haven’t worked in a cup shop since 2019 but I would be curious to know as well
Good stuff, “top hole” has the Brits say. A long ways from what guys like Lee Petty and Fireball Roberts did, which was-
I like this approach more, mostly because measuring stuff and being scientific is boring to me. I’m more of a brute-force person.
That sounds more like a Saturday night, “Run what ya brung” type of race rather than what Lee and Fireball were doing.
Because they often won, I think you are probably right.
I’ve always had great respect for NASCAR engineers and mechanics, even though I don’t care for oval racing itself. Boring to watch, but the work put in is amazing.
Amazing story Aedan, love to see stuff about the Xfinity series!
I’d love to see someone from a smaller shop or even a truck or ARCA team go through their process for a race. JR Motorsports is basically a Cup team with a Xfinity rulebook, so I’m sure their process is extremely refined and top tier. Seeing what a lower tier team has to choose to run or spend money on would be pretty neat in the art of the “every man racer”.
Agreed. I wonder if Aedan has any perspective into how MBM, Alpha Prime or Jeremy Clements handles their teams with significantly less budget and likely less than the 10 allowable chassis. I presume they all have a pull-down rig but I doubt they have as much sim time from the manufacturers. In any case, I love the behind the scenes look Aedan provides.
I’ve seen some posts on Reddit of smaller teams having to rent pull down rigs from other shops. Hell, I think it was MBM who drove their car down the street to another shop to set up their car on the pull down.
Or in the Cup series, I’d be fascinated to see how a small single car team like the Wood Brothers manages against the competition it’s up against.
Wood Brothers Cars are built and setup at the Penske shop, it’s basically their 4th car.
Would love to see how Starcom did or how RWR does now.
Another superb article, Aedan, which of course leaves me with enough questions to fill more articles (so write ’em!)….
Here’s one: I’m guessing the Xfinity teams can still build their own chassis. True? If so, does NASCAR mandate suspension/shock/trailing arm mounting points? Do they give teams detailed specs for chassis construction?
Also: can teams modify the bodies in any way, or are they strictly used the way they come from the builder?
I am still amazed at the way mechanics like Smokey Yunick could jiggle, juggle and fiddle their cars for perceived maximum advantage without simulators, computers, and the like. Of course I was fascinated at the ways they walked a tightrope (and sometimes fell off) in the process. I’m assuming that’s not so possible now, and that you wouldn’t tell us if it was!
More articles, please!
“If you ain’t cheatin’, you ain’t tryin’.”
There’s a window in which things can be mounted. As far as the body goes each manufacturer submits their body design and it is referenced as the “gold surface.” Teams are allowed to mount their body within +/-0.150” of this gold surface. The magic is in what areas are + to the tolerance and which are –
And remember – there is a race each weekend. This is a constantly moving assembly line in season!
NASCAR shop-life sounds stressful. When you perform a task weekly , complacency can set in, and mistakes can happen. Also, there must be a lot of checking behind going on to remain competitive when hundredths matter.
As usual, your article provides a behind the scenes look at actions taken well in advance of a race. As with most large events the majority of preparation goes largely unnoticed by the public. The average Rolling Stones concert has the stage taking up to three days to construct. Most fans show up and watch the show never considering what it takes to produce their fun. Bravo and keep ’em coming!
Thank you!