Most people, including car people (and journalists), have no clue how electric vehicles work, so The Autopian is working with engineers to plug this gargantuan electric vehicle knowledge-gap. We’re here to guide you through the minefield of EV technology. Note that I say EV technology, as opposed to EVs themselves. In this new series, we’re not going to be reviewing EVs or saying which are good and bad. There are loads of conventional road tests out there – so If you need to know how a Taycan’s rear knee room compares to that of a Tesla S, or whether the Audi e-Tron’s cupholders are bigger than those in a Mercedes EQS, look elsewhere. But if you want to know how these things tick – or should I say whine – then you’ve come to the right place. Here’s how electric cars work.
That’s not to say that we won’t be referring to specific automakers and name-checking specific EVs when explaining some of the tech, but we’ll be using them more as technical reference points than anything else. We’ll be keeping it neutral, respectful and non-judgemental. Unless they’re shit, of course, in which we’ll call it like it is.


How are we going to tackle this? Well, the car was invented in 1886 by Carl Benz, or maybe in 1881 by Gustave Trouvé, depending on who you talk to. [Editor’s Note: Well, if you talk to me, then the car was invented in 1769 by Nicholas-Joseph Cugnot, and there were plenty of other automobiles before Benz. Mercedes-Benz has claimed credit for inventing the car for too long, and I’m not having it. – JT]. That means that the internal combustion engined car is now over 130 years old. The world’s oldest person – Mrs Kane Tanaka, who was 119 years old – died recently, rest her soul. That means that it’s a 100% certainty that all of you readers were born in the age of the ICE-powered motor car. You may not all be engineers, mechanics or weekend tinkerers, but the piston engine is such a pillar of our society that it’s safe to assume that you know how it – and its associated systems – work. So we’re going to introduce EV technology by analogy, explaining – at a pretty high-level – which systems are significantly different to those in an equivalent ICE vehicle, before digging down into a system level. Then – ‘cos we know you guys love to geek out with us – we’ll be breaking these systems down into their components and even sub-components.
With me so far?
That means that we’ve going to deal with the things that are obviously different – the electrical traction (traction means it propels the car) motor that replaces the internal combustion engine that you’re used to, for example. Or the high voltage traction battery that replaces (conceptually) the fuel tank in your car. Somewhat less obviously, we’ll talk about things like braking systems and HVAC systems – because these are significantly different in a Mustang Mach-E than those in a real Mustang.
On the other hand, we’re not going to be analyzing front axles much – there is a good bet that, apart from spring and damper rates, the suspension set-up in most EVs is not fundamentally that different from those on their ICE brethren [Editor’s Note: With that said, there are some differences, which our dynamics engineer, Huibert Mees, who designed the Tesla Model S’s suspension, discusses in “The Surprising Ways Electric Car Suspensions Are Different Than Gas Car Suspensions.” It’s a good one worth reading. -DT]. Same for seats, interior trim or other systems – apart from genuine efforts by car-makers to reduce mass and or more-or-less-credible efforts to greenwash EVs by offering vegan interiors or woven natural-fibre panels, these systems are pretty much the same whether the car is powered by exploding fossil fuels or by electrickery. We’ll be coming back to weight saving, though- spoiler alert: mass-reducing EVs does not result in as many gains as you might think.
This first article is really your primer or roadmap – a quick tour around the property if you will, before we get into the details of each system. If you get lost in the detail of subsequent pieces, please feel free to come back here to find your bearings and see how the different technology-blocks slot into the big picture. This is a living document, and will be altered as time goes on so that this can become the go-to “How EVs Work” simplified explainer on the internet.
We’ll use this piece to introduce some basic terms, a few units of measurement, and a whole raft of TLAs (Three Letter Acronyms, duh) that will recur throughout the series. Don’t worry, we’ll probably throw in a glossary at some stage so you can find all these abbreviations in one handy reference document. You’re welcome. You can buy us a beer sometime.
In this series, when we talk about EVs, we’re talking about a vehicle that uses one or more electric motors as its sole means of propulsion, and stores its energy in a battery rather than in a tank of liquid fuel or in a bottle of compressed gas. Put another way, we’re talking about cars with no exhaust pipes – not even a sneaky little one hidden up under the rear valance, or one freakily dripping out water. Sometimes we may forget to put in that important ‘B’ in Battery Electric Vehicle and just use EV, but y’all will now know what we mean, OK? We’re talking full-fat, no-cheating battery electric vehicles here.
Right, enough intro – let’s start that tour. Step this way, please.
[Editor’s Note: David Twohig is a legend in the automotive engineering world, having not just led the development of the hugely important Renault Zoe, but also having worked on projects like the Alpine A110 and Nissan Qashqai. He has a book out called Inside The Machine, he contributes regularly to The Intercooler, and he’s someone I will continue to push to have on these here pages of The Autopian — a website led by an engineer and read by thousands of Ti-89-wielding nerds. -DT]
The Electric Motor
Let’s pop the hood and peer in there. To state the obvious, an EV uses an electric traction motor to replace the internal combustion engine. ‘Traction’ in the sense that it pulls the vehicle along the road – to differentiate it from the many other motors in a modern car, driving air-con compressors, or window winders, or seat adjusters. We’ll often shorten this to e-motor. Now, just like ICE vehicles can have gas or diesel engines, or exist in in-line or V or flat configurations, there are several different types of e-motor, each with its own advantages and disadvantages. An EV can have anything from one motor to four of ’em. They can be mounted inboard and connected to the road wheels with half-shafts like we’re used to, or (if you are very brave) built into the wheels in what’s known as an IWM (In Wheel Motor – told you there would be a ton of acronyms) configuration (this is more colloquially called a hub-motor). We’ll be getting down and dirty with all that cool motor stuff pretty soon, but for now we’re keeping things general.
Before we move on, let’s talk units of measurement. We can measure an e-motor’s punch using the units we’re all familiar with – horsepower (hp) and torque (lb.ft). But we usually use the SI or International System of units, sometimes known as the metric system. It’s called SI because the system has its origins in 18th century France and it’s thus short for Système International d’Unités. The SI unit of power is the watt (or more typically, kW or units of 1000 Watts) and the SI unit of torque is the newton-metre or Nm.
When we talk e-motors, we’ll typically use kW. We’ll say, for example, that the smallest e-motor in the Lucid Air produces 358 kW, rather than 480 hp. One hp is 746 Watts or 0.746 kW, making conversion really easy. If it helps, think of a kW as a particularly strong horse – like one of those big-ass Budweiser fellas that pull the beer kegs along at Christmas. They’ve gotta be 34% stronger than your normal hoss, right? And don’t ask me awkward questions right now about German PferdStarke or British horsepower, OK? I’m not even going there…I’m sticking to good ol’ ‘Murican horses.
Now, some of you might be curling a lip and wondering why this suspiciously Irish-French dude is trying to make us adopt these new-fangled Euro-units. Why not just stick with horsepower and be done with it? Well, it turns out that the SI system is very convenient when we make electrical calculations. The equation for power becomes really easy – it’s simply:
P=IV
Where,
P = power in watts (W)
I = current, in amperes, or ‘amps’ for short (A)
V = voltage, in volts (V)
For example, if I have a battery putting out 400 V and 200 A of current, I know that it can power an electric motor at 400*200 = 80,000 W or 80 kW. No conversions, no messing around – that’s the beauty of SI units. So bear with us, as we’ll be talking a lot about kW, volts, and amps.
[Oh yeah, I forgot to mention that we’d throw in the odd equation, just ‘cos we’re nerds and we like them. But we’ll try to explain them properly, and not make them too boring].
Transmission
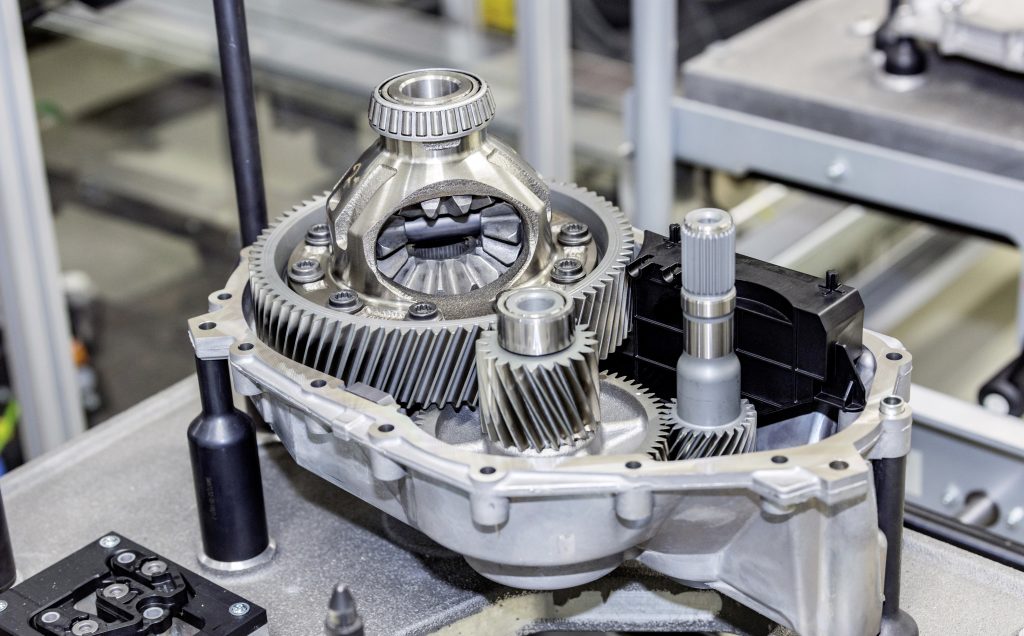
The motor needs to be connected to the wheels in some way. In most EVs, this is done by a very simple single-speed reduction gearbox, which gears down the high-revving motor to a rotational speed more suitable to turning the road wheels. But a few EVs – notably those Teutonic sisters, the Porsche Taycan and the Audi e-Tron – use two-speed gearboxes, automatic of course. And all EVs do that cool trick of eliminating the need for a reverse gear by simply turning the motor backwards – opening the door to various Jackass-style attempts at high-speed reversing in EVs with the reverse speed limiter bypassed…
Inverter/Motor Controller
Power from the outlet in your wall is AC (alternating current), an electric vehicle’s battery needs DC (direct current) input and it outputs only DC current. The motors in EVs run on AC current.
With that in mind, it’s kind of hard to find an ICE analogy for an inverter. If I were to stretch, maybe it’s a kind of a carburetor or fuel-injection system in that it’s taking the fuel source from the tank (battery) and modifying it before it gets to the engine (motor)? Anyway, it’s typically a large metal box somewhere in close proximity to the motor – more often than not these days, literally bolted onto the side of it, or even sharing part of the e-motor’s housing casting.
It’s usually fairly easy to find because it will have two thick cables, usually orange in color, running into it from under the floor. This unit converts the direct current (DC) electricity coming from the high-voltage battery into a variable-frequency (or variable speed), rotating three-phase alternating current (AC) that energizes the motor’s stator and hence makes the rotor spin. Say what? Don’t worry, we’ll eventually explain exactly what that phrase means, and how the inverter achieves this. For now, just think that an inverter “inverts” the flat line trace of a DC supply into the hopefully familiar bumpy sine-wave form of an AC supply.
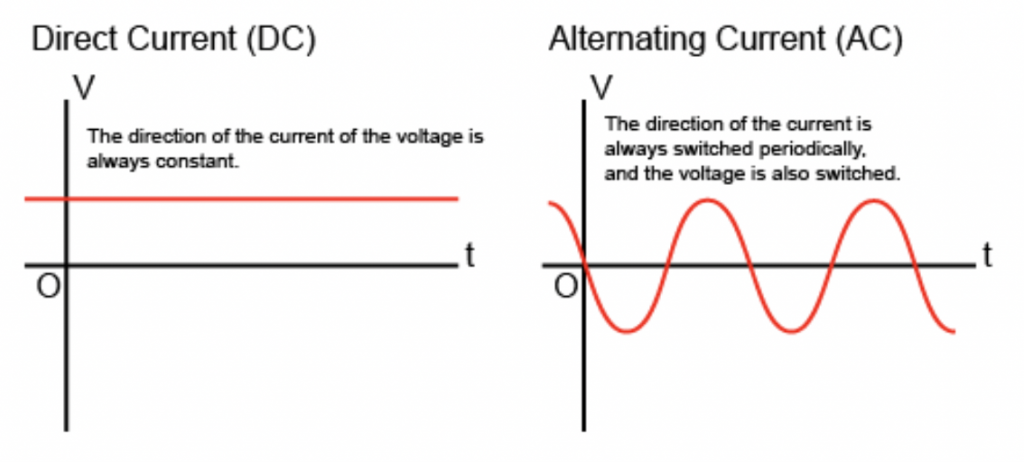
An inverter’s twin brother would be a rectifier – a unit that “rectifies” a bumpy AC supply into a nice rectilinear DC supply. And yes, we’ve got a few of those coming up too. By the way, occasionally, EV makers will call their inverters ‘ECUs’ (Electrical Control Units – so generic that it hurts) or even ‘MCUs’ (for Motor Control Units) but we’ll try to stick to the more general and technically descriptive term of inverter.
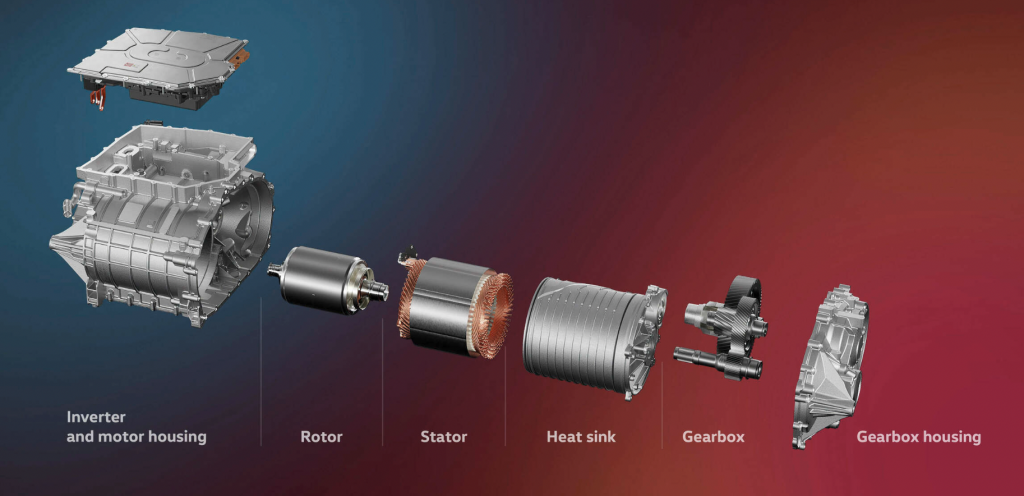
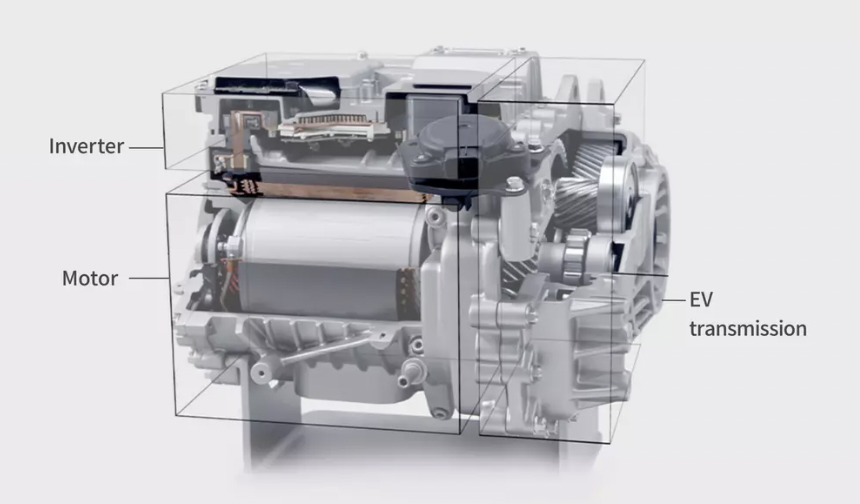
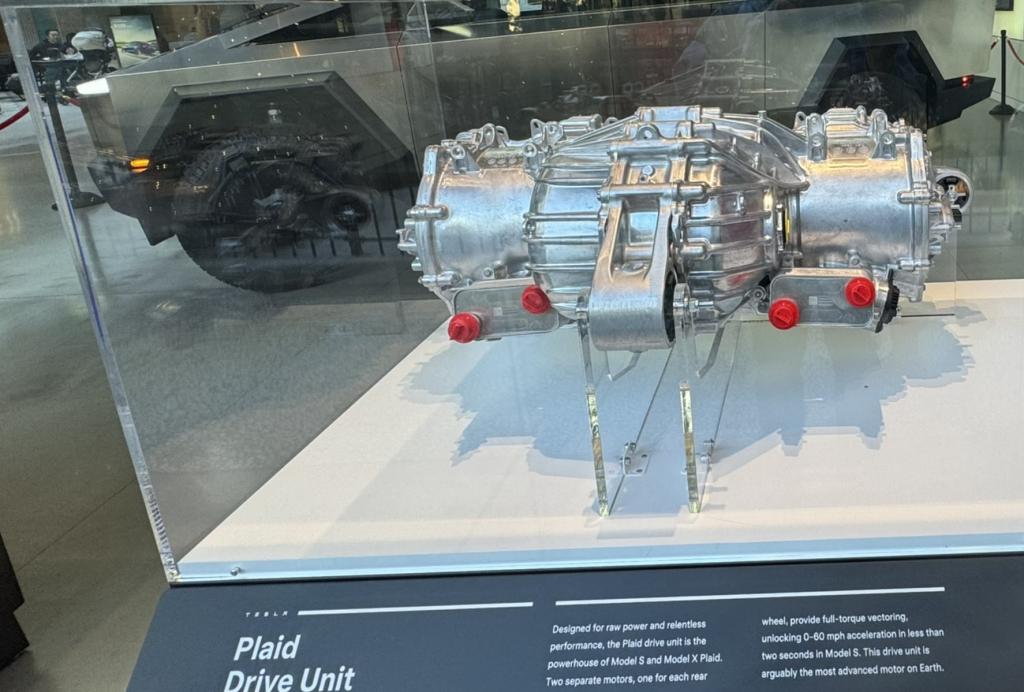
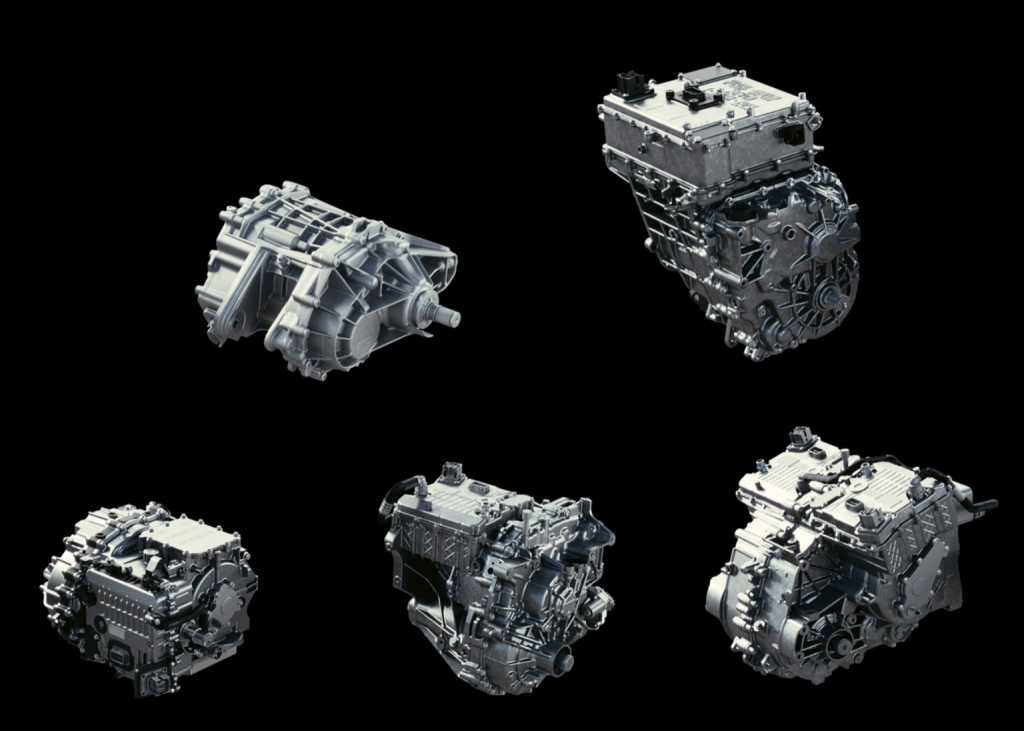
It’s worth noting that inverters are often packaged in a single “unit” that includes the traction motor and transmission. This unit is often called the “drive unit.” You can see some examples above.
HV battery
Next, let’s pop our BEV on a ramp and hoik it up so’s we can get a look at what’s likely to be slung under the floor – or maybe actually be the floor (yes, a structural part of the car) – the battery. More correctly, the high-voltage traction battery. High-voltage to distinguish it from the low-voltage (12V) auxiliary battery that is still required to power lights and wipers and do useful things like pop your airbags if things go in an unplanned direction.
It’s called a Traction battery, as its primary function is to feed that traction motor we talked about. Now “high” voltage in this context has an actual engineering definition. It’s above 60 V. Why 60 V? Well, this is the voltage above which things get really spicy, from an electrical safety point of view. See, your body is a huge electrical resistance – a big one, in the unusual form of a squishy bag of meat and bones, and one which contains a lot of water and salts. And salty water makes a reasonable conductor of electricity. So if I asked you to stand on a rubber mat, hold the red wire of a battery in your left hand, then asked you to kindly hold the black wire in your right while I threw the switch, your body would conveniently close the circuit and the current would run through your chest cavity. Yes, the one containing your heart, lungs and other things that grossed me out so much in high-school biology classes that I signed up for engineering rather than medicine.
But the resistance of your body is such that voltages below 60 V are likely to just make you yelp (we still strongly advise against trying this), drop the wires and quite justifiably seek to inflict bodily harm on me. Above 60 V, things get dicey. The current flowing through your body risks swamping the electrical nerve signals controlling your heart, and you might well end up in an ambulance, or worse. Now, some light-duty EVs, like Renault’s cute little Twizy, or the millions of e-scooters zipping around our cities, do run at voltages below 60 V, which makes life much easier for their designers in terms of electrical safety. But larger EVs, those capable of carrying four or more adults around at reasonably high speeds, run at “system voltages” way above 60 V – typically ‘round about 400 V, and more recently, 800 V or even 900V. This is most definitely High Voltage, fully earning the capitalization, and should not be messed with.
The battery (we’ll call it that without bothering you every time with the ‘high voltage traction’ qualifier) is capable of being charged by an external source, and it delivers high-voltage direct current to the carburetor, sorry, inverter. There are a few exceptions, but the vast majority of modern EVs use lithium-ion batteries slung in a large, heavy and crash-resistant case or housing under the floor of the vehicle. We’ll have a lot to say about what’s inside those boxes in a later article.
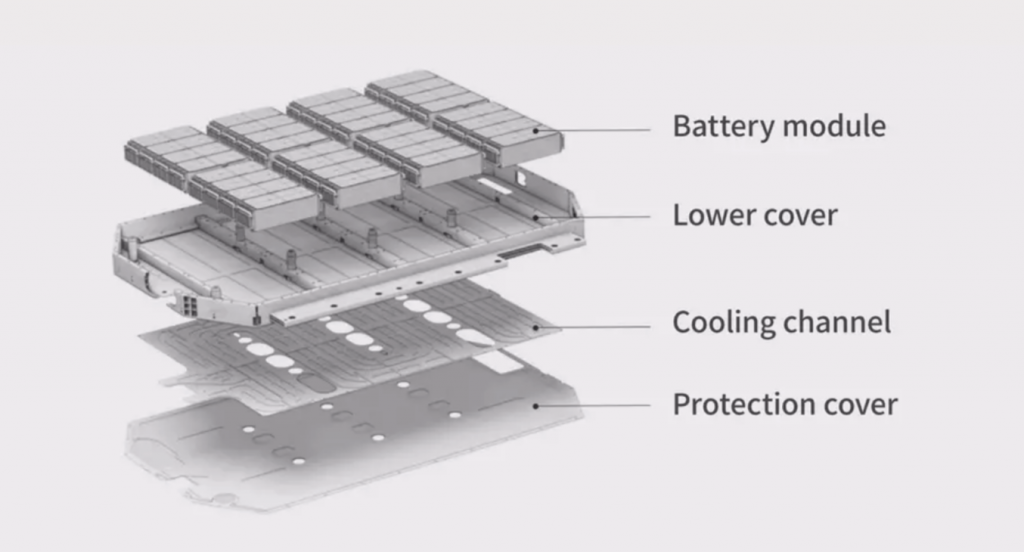
OK, one more quick sidebar on units. The battery is there to store energy. We use the SI unit of energy to measure this – the watt-hour, or Wh, usually again used in the form kWh, which is 1000 Wh. So a Tesla 3 Long Range’s battery can store up to 82 kWh – in other words, in could, theoretically, output 82 kW of power for one hour, or 164 kW for 30 minutes. Got it?
Why don’t we mention ever kWh when we talk about ICE cars? Well, it’s because liquid fuel is just so energy-dense that we simply don’t need to. The 82 kWh of energy in that big Tesla 3 battery (which weighs somewhere about 1000 lbs, by the way) is contained in just 2.4 gallons of gas (which would tip the scales at about 15 lbs – including the can). Yup, you read that correctly. Gas (or Diesel) is a superbly concentrated source of energy. So we don’t need to point out that the 25-gallon tank on a Ford F-150 holds 843 kWh of energy – we have so much of the damn’ stuff that we don’t need to be so precise. We just short-cut it by talking about fuel tank capacity in gallons (or litres, if you want to stick with the SI groove).
Battery Management System (BMS)
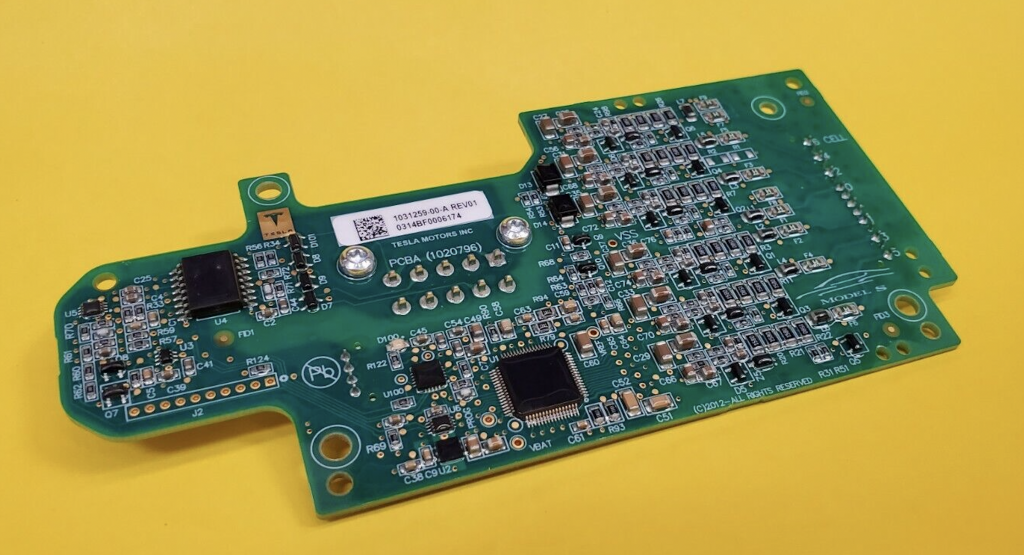
It’s worth noting that battery packs require what’s called a Battery Management System, or BMS. Integrated into the battery pack, the BMS’s job is to ensure the safety of the hundreds or thousands of cells in the pack, to optimize their performance, and to communicate information about those cells/the pack to other parts of the car (including the driver’s gauge cluster). Here are some of things a BMS does:
- Prevent cell over-charge/discharge
- Balance the cells’ state-of-charge to maximize vehicle range
- Ensures optimal thermal management
- Helps ensure precise battery state-of-charge estimation
- Monitors cells internal resistance/pack overall health
[This small section was written by David Tracy]
The On-Board Charger
On Board Charger. Bit of a misnomer really, as no EV can really charge itself via “on-board” systems. Remember we mentioned AC-to-DC rectifiers above? Well, this is one of those. Most EVs chargers – especially Level 1 ‘slow’ or Level 2 “medium” chargers, are simply taking the standard electricity-grid supply and providing it to the vehicle. We’ll get into the definitions of these L1-L2-L3 charge levels later, but for now, assume that this covers charging powers up to approximately 22 kW. Yes indeedy, folks, we measure not just a motor’s output in kW, but also charger ‘speed’!
If you’ve seen the movie The Current War you’ll be aware that the electricity distribution grid in all countries in the world is alternating current or AC, despite Thomas Edison’s best efforts. But that big old traction battery under the floor is, like all batteries, DC, remember? So an EV needs a “box” that can take the external AC supply, rectify it into DC, then feed that directly into the battery. This is the OBC. It’s basically the same as the power supply that feeds your iPhone, or your laptop, just scaled up and made to automotive safety and reliability grades. The OBC can be located in various places in the car – it may be placed near the charge port, it may be packed in the ‘engine’ bay, or in a Tesla Model 3 it’s lurking inside the battery housing.
Don’t even ask me what the equivalent bit on an ICE is. There ain’t one.
Charge Port(s)
Fuel filler, right? Right! An EV may have one or two charge port doors, but under those doors it’s very likely to have two “fuel inlets,” to keep stretching our analogies here. The first is the connector for the”‘slow” Level 1 to Level 2 (L1 and L2) AC charge we talked about above, going through the on-board charger (OBC) and into the battery. Right. Easy.
But now we get tricksy. There is usually a second connector for what’s known as L3 (Level 3) or ‘fast’ charge. This is where we want to charge the battery at power levels above 50 kW or thereabouts.
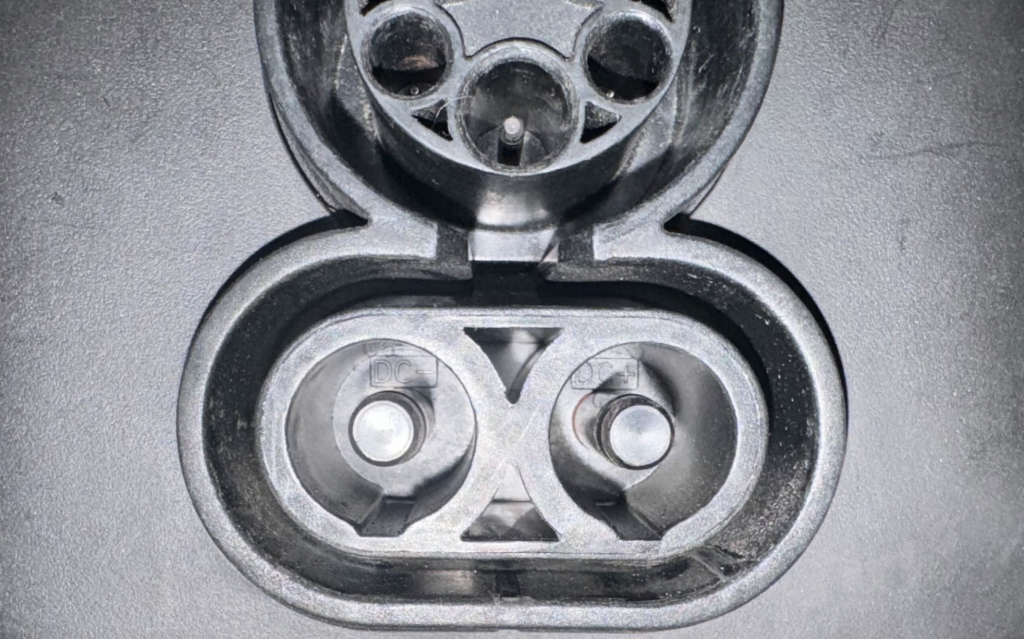
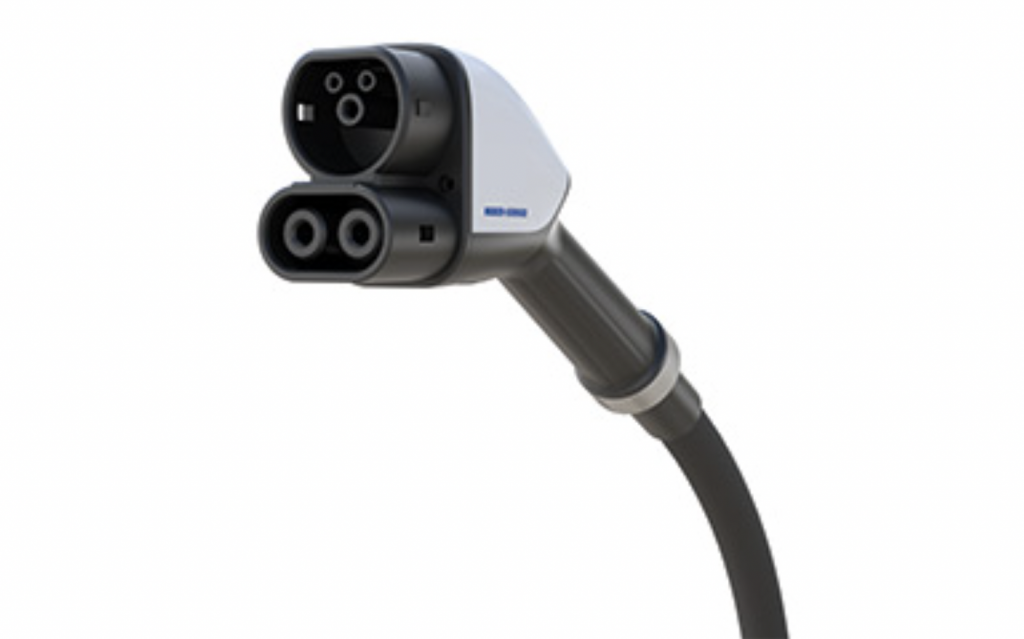
These power levels are too hot to handle for an on-board OBC: such a unit would be too big and heavy to house inside the car. So fast chargers do the AC-DC rectification off-board – in the big stationary box that you see at a Tesla Supercharger station, or at Electrify America’s equivalent fast chargers. These are large, powerful rectifiers taking the 3-phase grid supply, straightening it out, then presenting it directly to the car (and the battery) as a DC supply. That’s why most EVs have two connectors – an L1/L2 AC input, and an L3 DC input.
Now, at this stage some of you folks may be raising an eyebrow and thinking “This guy is talking crap. My Euro-spec Tesla has just a single connector, not like some crappy Nissan Leaf with its two ports.” Partly right. It may well look like a single connector, but in reality there are, functionally speaking, two connectors, cunningly disguised in one large plastic housing.
Peer carefully into the charge port of any EV – just avoid the temptation of sticking your fingers in there, OK? You’ll see a bunch of pins, but there will be two noticeably thicker, heavier ones. These are for the fast-charging DC supply that gets hard-wired straight to the battery, bypassing the OBC.
Now, charge port connectors are a damn nightmare. There are a bunch of types, and efforts to standardize them have only recently borne fruit, and even then, only partially. So I’m going to neatly side-step that thorny topic for now, leaving it for a later article. That one will need two cups of coffee and a strong stomach. But all will be revealed, and all the questions that you never thought to ask about CHAdeMO, CCS, J1772 and of course GB/T charge port standards will be answered. Take that as a threat or a promise, as you wish.
DC to DC Converter, 12-Volt Battery
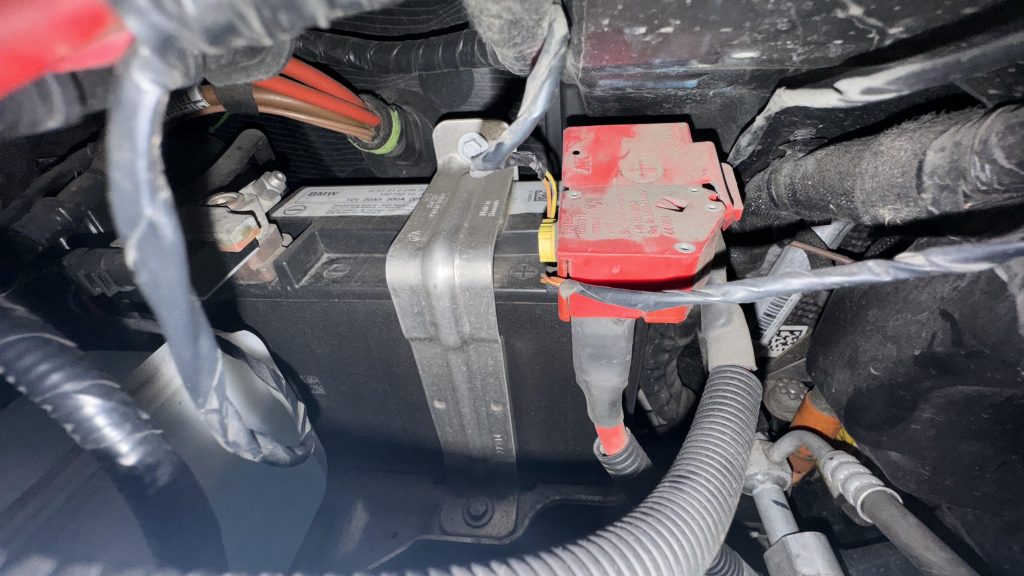
OK, the chip shortage has reminded us that all modern cars – piston-powered or no – have a bunch of electronic control units (generically, ECUs) in them. You are also probably aware that all but the simplest cars these days uses multiplexing systems such as the well-known CAN (Controller Area Network) bus standard. So E/E systems are hellishly complex, whether your vehicle is fueled by gas, diesel or electrons.
But EVs have a few specific electrical and electronic features. First and most obviously, those thick orange cables snaking here, there and everywhere in the trunk, underfloor and “engine” bay areas – although very rarely inside the passenger cabin. These are the cables carrying high tension current – 400 V in most EVs we’ve already mentioned. These are orange for the same reason that many venomous snakes are orange and black – to suggest that you should not mess with them. Trust me – it’s a Very Bad Plan to pull out your hunting knife and strip back the insulation in order to wire another sub-woofer into your kick-ass system.
But EVs still have a bunch of low voltage 12V systems, in large part because it’s still cheaper and simpler for car-makers to use off the shelf 12V lighting, wipers, entertainment and other systems that are often shared with their non-EV vehicles. So we need a source of 12V power on board. Step up the next of our unique EV systems – the DC:DC convertor. This is yet another ‘box’, this time – as the same suggests – a piece of power electronics that steps down a DC supply, turning the high-voltage output form the battery, often nominally 400V or 800V, to a (still DC) 12V supply – usually calibrated closer to 14.2V in reality.
Here’s a look at the Volkswagen ID.4’s DC-DC converter, which you can see is liquid cooled:
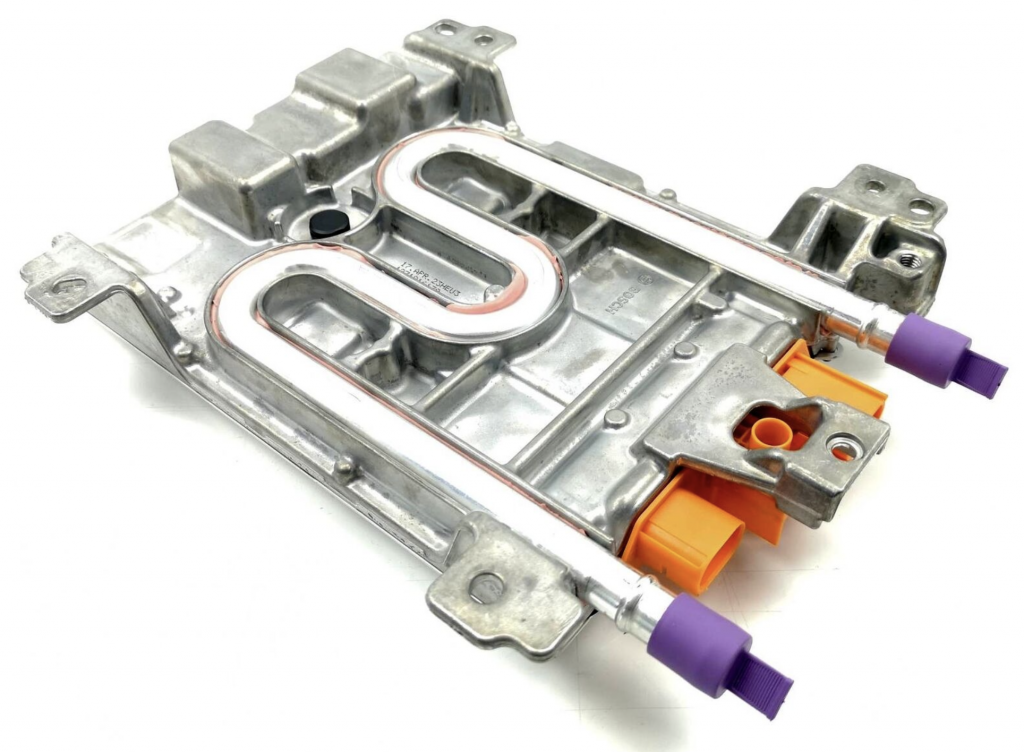
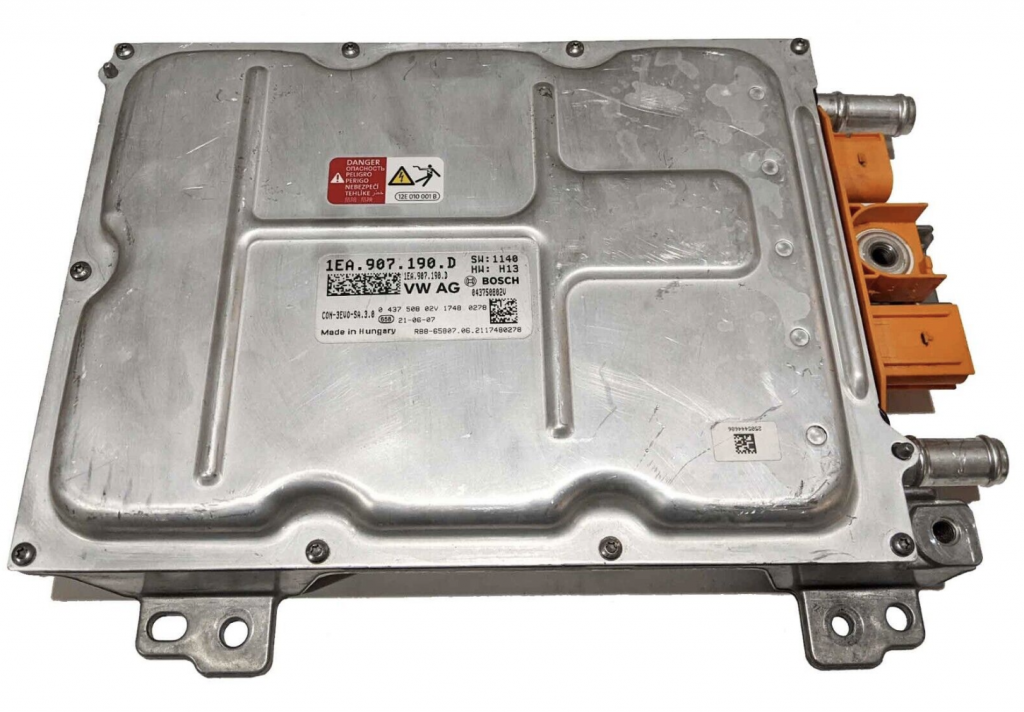
Here you can that it’s packaged at the rear of the Volkswagen ID4, behind the rear drive unit:
A DC-DC converter’s analogy in an ICE vehicle is the alternator – this is the unit that keeps the 12V battery (or batteries in certain EVs) topped up, and the lights and wipers on. If it fails, the failure is similar to blowing an alternator belt on your ‘regular’ car – you have a limited time left before that 12V battery will drain, your lights will start to look like yellow piss-holes in the snow, relays will start to click sadly, and you need to look for a safe place to park up and call the rescue truck. It’s so critical that many EVs will actually have two, redundant, DC:DCs.
High Voltage Junction Boxes (HVJBs)
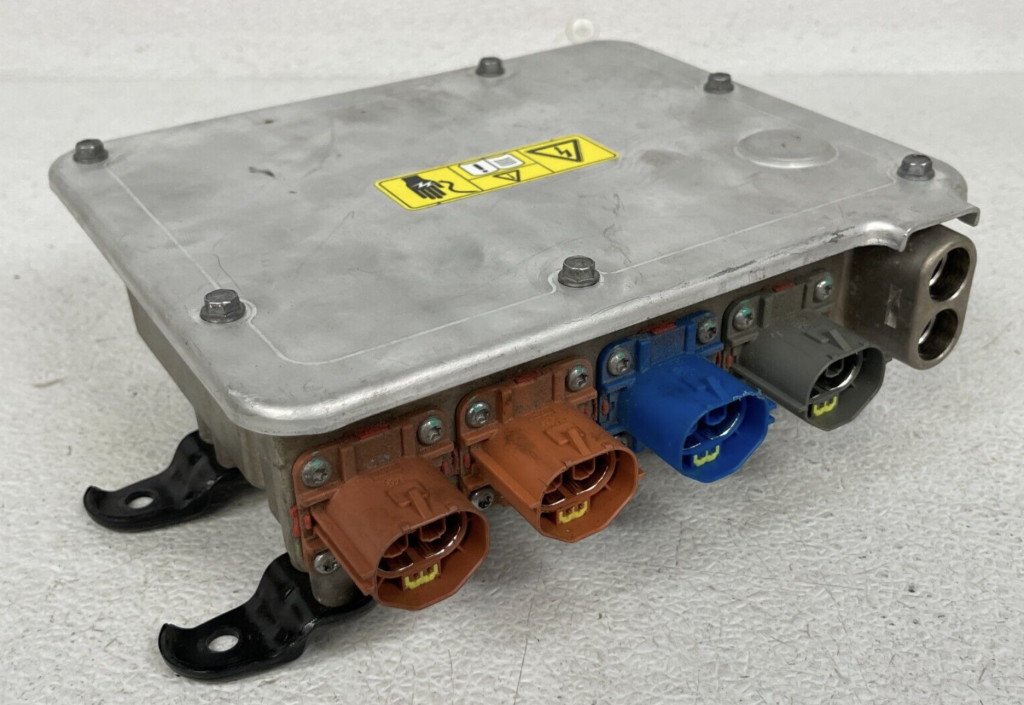
I’m just throwing this one in for the sake of completeness. With high voltage cables running around the vehicle, from charge ports to battery, battery to inverter, battery to DC:DC(s), EV designers often build in specific junction boxes or JBs to safety connect or branch the heavy orange cables together.
These can be simple passive connection boxes – think those connector blocks that you have in your house wiring – but they often contain some active electronics to monitor current and voltage levels in the HV systems. We’ll talk a lot about safety throughout these articles, but the reason for this active monitoring is, indeed, electrical safety.
EV engineers are paranoid about something called leakage currents. Imagine the current in those thick orange cables is water (a really bad analogy, by the way, but bear with me). Engineers want all the water to stay in the pipes. If one of them springs a leak and starts to leak a few drops (milliamps) there is always the possibility that those milliamps are finding their way to earth through that wet, squishy resistance known as the human body. This must be guarded against at all costs – so engineers build in multiple monitors of voltage (water pressure) and current (water flow) to make sure that all of the water remains in the pipes, and none of it threatens to kill the EV’s users. HVJBs can provide a good opportunity to engineer to build in some extra monitoring…
Right, enough water-electricity analogies, that will just confuse the hell out of us. We’re done. Move on.
A Note On ‘Power Electronics’
It’s worth mentioning “Power Electronics,” because it’s a term that gets thrown around a lot in the EV space. According to the U.S. Department of Energy, Power Electronics is defined thusly:
Power electronics convert and distribute electrical power to other vehicle systems such as heating and ventilation, lighting, and infotainment. Power electronics components include inverters, DC/DC converters, and chargers (for plug-in electric vehicles).
While not wishing to contradict the DOT (who are no doubt technically correct), I would suggest that in real use, in an EV context, ‘power electronics’ is really used for ECUs that control the HV components. ECUs that control normal 12V systems, I suggest, are merely ‘electronics’.
To wit:
Power electronics (400V): inverter, onboard charger, DC:DC converter, Battery Management System, HVJBs (High Voltage Junction Boxes) and usually, air conditioning compressor (which we’ll get to soon).
Electronics (12V): lighting controller, body control modules, door control modules, infotainment.
This might be “technically” wrong in some sense, but to me makes practical sense.
Brakes
I don’t really need to explain the equivalent part on an ICE car here, do I? But EV braking systems are significant different than those in ICE vehicles. We’ll delve into the details in the article that will be dedicated to the stoppers, but suffice it to say for now that there are two main differences. First, all EVs worth the name use regenerative (or ‘regen’) braking. You might remember from high school physics that a motor, working in reverse, becomes a generator. Well, we’ve got a big, powerful electric motor, or motors, so it would be a damn shame not to use them as generators when we take our foot off the accelerator pedal to allow the car to coast to a halt, right? [Ed Note: Because the motors are AC, when your car activates regenerative braking, the current output is AC, and because the battery can only be fed DC, the power inverter is used as a rectifier to change AC from the motor-acting-as-a-generator to DC to go into the battery pack. -DT].
All EV designers build this feature into their vehicles. But the e-motor itself cannot always provide the stopping power we need: we’ll come back to the reasons for this in a later article. So EVs still need conventional friction brakes. But here’s the tricky bit – these two braking systems need to work together, to blend the regen and friction braking smoothly, all controlled by one pedal, ideally so smoothly that the driver has no idea what’s really stopping the car – the EV motor or the discs/drums.
Second, braking assistance, and specifically brake assistance backup. An ICE engine – especially a gasoline ICE engine – provides a really neat, free source of energy known as manifold vacuum. The natural ‘suck’ of the engine’s intake manifold can be connected to what’s called a brake booster, which is a sealed diaphragm that can store energy in the form of a vacuum. And this is the energy that helps us in the case of engine failure. If the engine were to fail in an ICE vehicle, the vacuum booster has enough energy in it to allow us to pump the brakes once or twice, and bring the car to a safe halt.
So, what if I have no vacuum – ‘cos I have no intake manifold, and no “suck,” so to speak? Well, we’ve got to figure out another way to arrange brake assistance. This is almost always in the form of electrical assistance – and it’s usually 12V, not 400V. We’ll delve into this in a later article when we come back to brakes. It’s a truly fascinating area…the complexities will blow your mind, I promise.
Steering
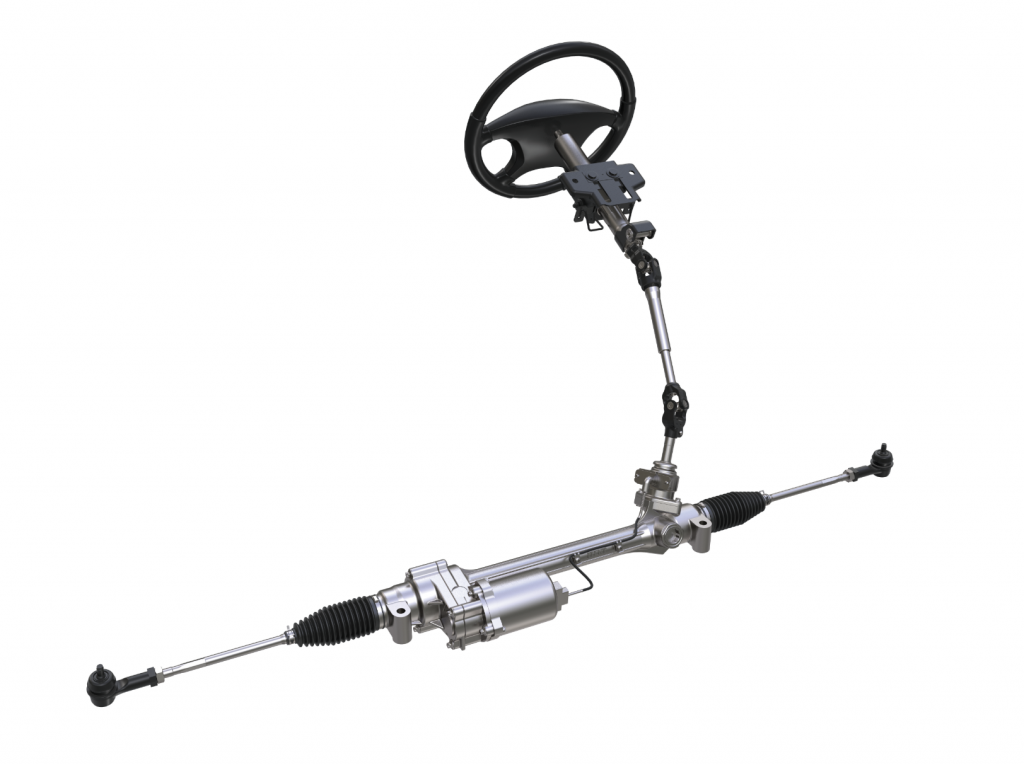
I’m going to surf over steering systems pretty quickly here, because I’m going to assume that our starting point is EPAS or Electrical Power Assisted Steering, as opposed to hydraulic or electrohydraulic systems. Given this assumption, the steering system in an EV is not significantly different from that in most cars and light trucks that are already equipped with EPAS. Let’s keep moving.
Thermal Systems
Easy one, right? Everybody knows that EVs don’t need cooling. Those electric motors are so efficient that they hardly need radiators. Just look at a Tesla Model S with that super-smooth front end: There are hardly any air intakes required to flow air through the radiator like on those dirty old ICE cars. Right? WRONG. This is one of the most persistent myths about EVs, and your crew The Autopian are going to blow this one right out of the water, folks.
Sadly, even some EV designers still believe the ‘EVs don’t need much cooling’ BS, and keep trying to design EVs with simply insufficient air intakes up front. For example, a Tesla Model S has to have up to 17 radiators, and a whole bunch of cooling fans to compensate for the inadequate openings in its front end. In fact, cooling (and heating) EVs is highly complex. Electric motors do need to be cooled – as do inverters, on-board chargers, and many other of the power electronic units we’ve mentioned above.
The battery also needs to be cooled – but here’s the kicker: it also sometimes needs to be heated. It’s a fussy thing that performs best in a certain temperature range. Finally, the human beings in the cabin are even fussier the batteries they’re sitting on – sometimes those bald apes need to be heated, sometimes they need to be cooled. And they change their minds all the time…grrrrrrrr. And their comfort needs can have a significant affect on range.
Cabin Heating And Cooling
Like brakes, you might be forgiven for supposing that the HVAC systems in an EV are not all that different to the Heating, Ventilation and Air-Conditioning systems in your fossil-fueled sled. But they are. The ICE engine comes with a second free gift – a lot of waste heat. The thermal efficiency of a good ICE engine is maybe 40% – that means that almost 60% of the money you paid for that gas gets blasted out into the atmosphere in the form of waste heat.
It’s been a no-brainer for automotive engineers for over a century to use that waste heat to warm the occupants of the vehicle on a cold winter’s day. Basically, as liquid coolant is pumped through your hot internal combustion engine, it warms up; that warm coolant is then sent through a heater core in your cabin, and air is blown over it and through your heater vents, warming you up. But warming a cabin is a lot trickier for EV engineers. OK, they could take the easy way out and just use the energy stored in the battery to run a bunch of electrical heaters. Some do. But this would be a pity – we want to use that energy for forward motion.
Luckily, EV engineers are creative folk, and not above a bit of flattery by imitation. They have taken a piece of technology that existed for decades in building HVAC systems called a Heat Pump, and this baby provides a much more efficient way to heat an EV. I’ve been working with heat pumps for nearly 20 years now, and they are so clever that I still think there is a bit of black magic and witchcraft in there. So put on your best witchy cosplay gear when we come back to them, OK?
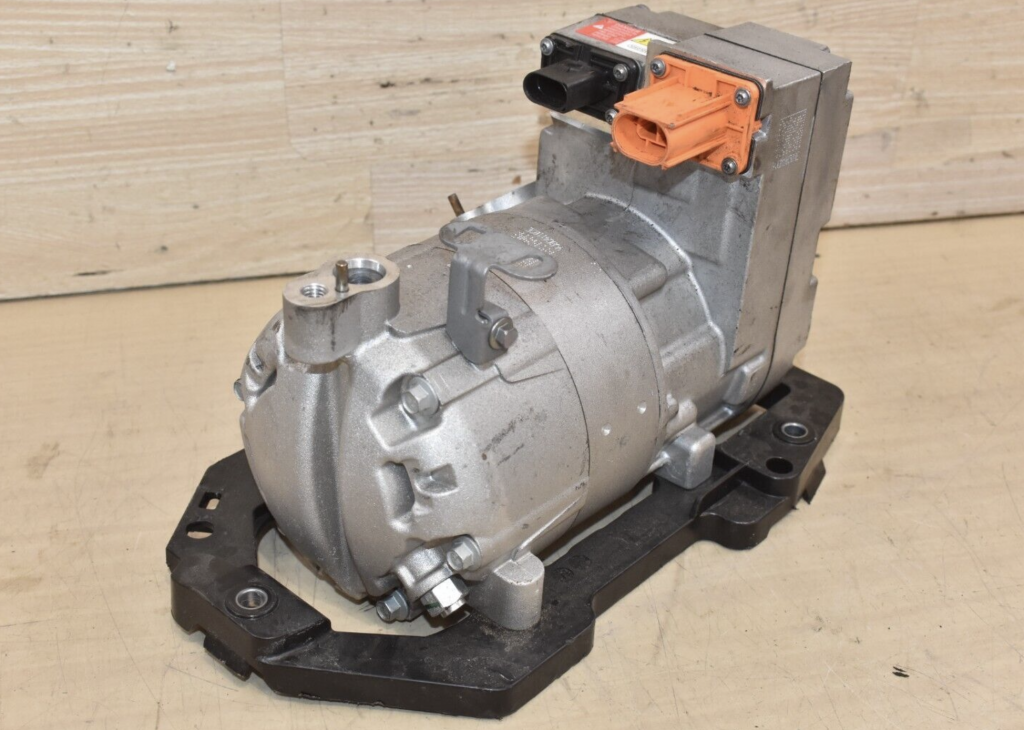
It’s also worth mentioning cooling in addition to heating, and on that front an EV uses the same thing a gas car does: an AC compressor. But instead of the AC compressor being powered by a pulley spun by a belt driven off your idling combustion engine, an EV’s compressor is electric and powered by the high voltage battery, meaning you’ll see an orange cable going to it like you do here (this is a VW ID.4; the compressor is located right at the front of the vehicle):
That compressor is doing so much more than a compressor typically does in a gasoline car. Not only is it a critical part of the aforementioned heat pump system that helps warm the cabin, it’s also in charge of keeping batteries and electronics cool via a coolant-to-refrigerant heat exchanger called a “chiller.” We won’t get into details now, but expect to get nerdy in a subsequent article.
Approaching Vehicle Alert System (AVAS)
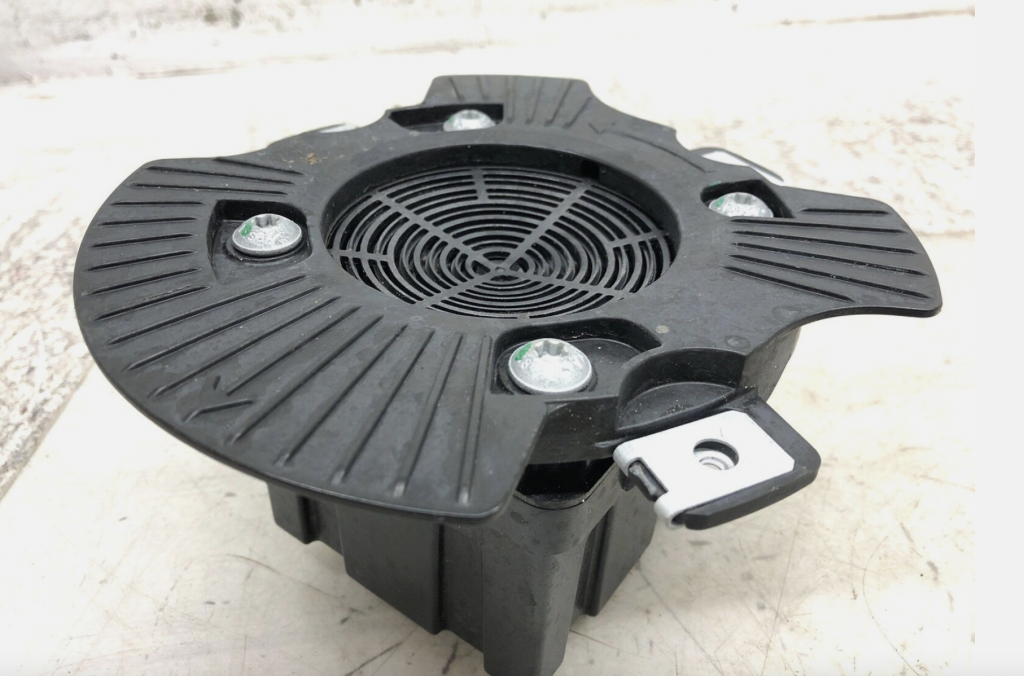

OK, one final “box” that has no equivalent at all in your ICE vehicles. This is the unit that generates sound, to alert pedestrians, cyclists or other vulnerable road users that an EV is approaching. That nice rumble of your Hemi at idle does this job automatically. But silent EVs, especially when moving at slow speeds in urban areas, could present a risk to folks – especially the elderly, the visually impaired, or those that are heads down with AirBuds in, playing whatever game the kidz play these days. An AVAS is basically a smart speaker, that generates noise outside the vehicle, to alert people around them that the car is in motion. And yes, we’ll do a deep dive into these too, as there is a stack of regulation, debate, and even some cool stories about cute service/guide dogs to share with you.
Tires
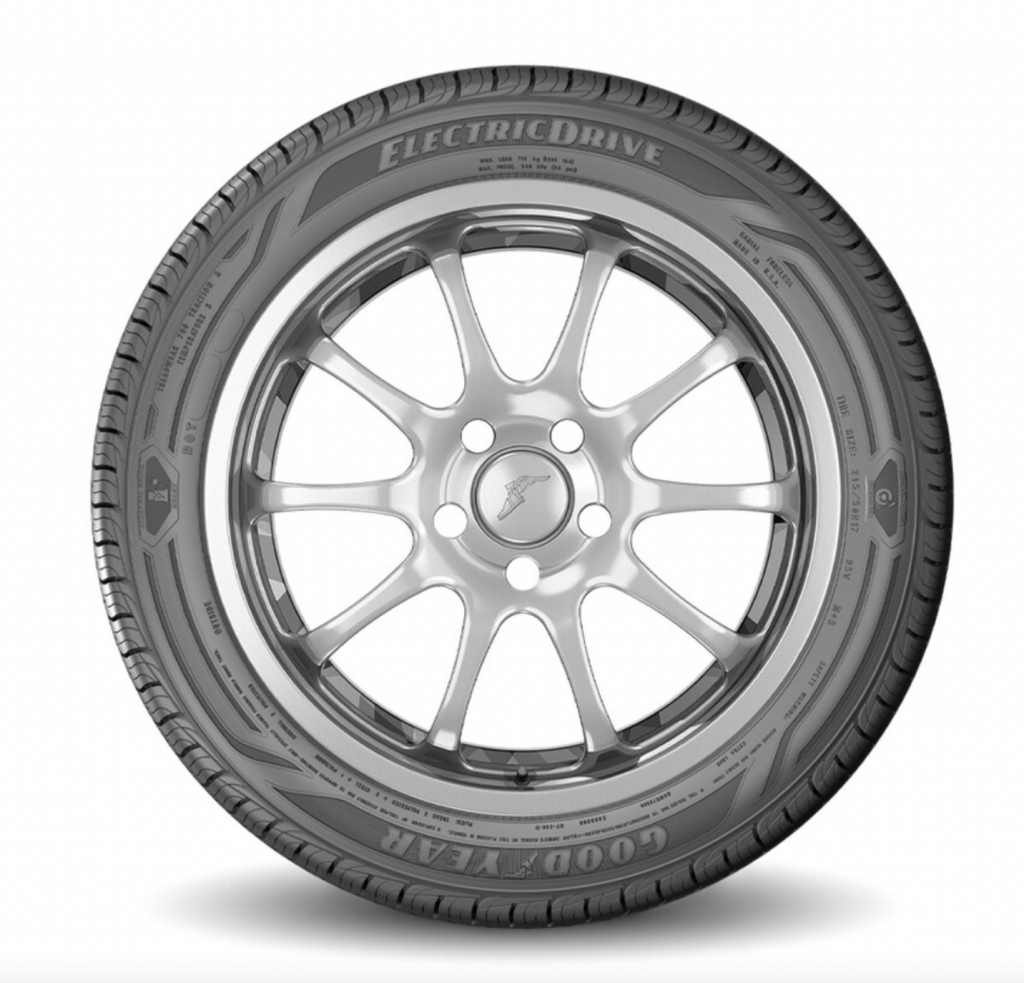
Yup, we’re talking about the four round back things that you will find, reliably, on the corners of your vehicle. And yes folks, EV tires are sufficiently different from ICE tires to justify us geeking out on them. They need to have a lower rolling resistance and a higher charge rating, perform better in rems of NVH, and also help out with aerodynamic optimization…all while providing good braking performance and milage. They may be round and black like any other tire, but under their sidewalls, there is a lot of cool stuff going on…
Woooo. Deep breath. Well done if you’ve waded through all that lot. But trust me, there is a lot more to come. This series of articles will not simply stick slavishly to linear list of systems/components. We’ll talk about all of the above, sure, but also about a lot of other ‘system-level’ stuff – passive safety, electrical safety, vehicle packaging or layout, ride and handling, and of course the whole topic of the optimization of energy usage and hence vehicle autonomy or “range”: topics like mass reduction, aerodynamics…and a whole heap more.
We hope you’ve enjoyed this first tour of the property (we know this wasn’t a 100% exhaustive list of EV parts, and this will likely be tweaked as time goes on). In our next few articles, we’re going to get deep into the individual systems – so if you want to learn about motors, about inverters, about cooling systems, and about that big box of fun (and energy) that we call the battery: Get ready for some fun!
[Ed Note: If you’re an automotive engineer who wants to contribute to the “How EVs work” series, please consider joining our EV Task Force by emailing david@theautopian.com. We’d love your help putting these stories together, as input from engineers is going to be paramount. -DT]
Imagines and some significant edits by David Tracy
I do enjoy the news and the menagerie of other article topics, but these technical article series are AMAZING (this one and the suspension series so far?). They’re so good I pretty much have to become a paying member; well done.
fascinating, thank you..
had no idea that EVs are using heat pumps. I have a degree in physics and like you, find heat pumps to be borderline magic.
‘any sufficiently advanced technology is indistinguishable from magic’
Clarke’s third law.
I have interest in STEM topics but don’t have any formal education or experience in STEM. I find heat pumps intensely fascinating to the point of trying to explain them to some friends
I usually ask them to think of it as “an air conditioner that can run backwards,” but the basic working principles are still hard to explain because it involves entropy and thermodynamics, two topics I don’t know anything about beyond the movie TENET
“This is the unit that generates sound, to alert pedestrians, cyclists or other vulnerable road users that an EV is approaching. That nice rumble of your Hemi at idle does this job automatically. But silent EVs…..”
In my opinion, that’s another very pervasive yet untrue myth. Electric cars aren’t silent, and gas engines don’t make that much noise. The noise coming from cars in parking lots is almost exclusively cooling fan noise or tire noise if you pay attention. Meanwhile, Teslas and some other cars make a very noticeable motor whine from the outside that is louder than many gas cars if the electric fans are off.
I think the speakers are really just for the relatively limited situation of cars traveling on neighborhood roads between 20 and 30 mph. This is fast enough that they can sneak up on kids or people who aren’t used to looking for cars, but slow enough you don’t get a lot of other car noise. Additionally, as you say, parking lot noise is a lot of warm-up, cool-down, and tire scrubbing noise that EVs are also exceptional at producing. On a relatively straight road with smooth pavement at low speeds, though, they can be stupid quiet. An ICE car producing more than idle torque produces a lot more noise, and also that thing that’s not quite noise (too low frequency), but is the fundamental exhaust pulsation frequency that you feel more than hear.
All that said, I don’t think any of my EVs have ever had the sound-maker, and the sound-makers sound stupid.
I’m very excited about this series. Been learning all I can can about the one I got, and this has already been informative. Can’t wait to see the deep dives into the components.
I’m going to be super pedantic and point out that kWh is not technically an SI unit, that would be the Joule (J). Which is the same as a Watt Second (well, a watt is one joule per second but it’s easier to compare to kWh this way).
It also reminds me how much easier life is that at least Americans use standard metric units for electricity, and not something like ‘gallons of electrons per fortnight’ etc.
This is great – would love if the series delved into various tradeoffs on things related to battery range & charging (motor size, impact of charging speed, etc.)
Good stuff!
Thanks, man.
We have a whole portfolio of engineering classes related to High Voltage for the company I work for (We make HV components like cables, junction boxes, on board chargers) and this article is the perfect summary of all of these classes, even better.
I would like to add the reason to use high voltage is the relationship of current to losses. Except for super-conductivity any current flow will incur losses, these are P(loss)=U(loss) X I (current), or related to the square of the current (if you keep the resistance constant). Therefore it makes sense to increase the voltage rather than the dimension of the conductor (so it doesn’t just melt).
Excellent article. Brought back nightmares from my power systems courses. Did an EE degree but went for Telecoms and a bit of control systems. Also did a Comp Sci degree and as a result ended up in software land. Still enjoy it. Power systems scared the heck out of me.
Another difference between EV and ICE you missed: Yokes v.s. steering wheels.
Excellent start, thank you David! Looking forward to the next installments… I wonder when a project like the Zoe E was getting fired up: what was the ratio of engineers with an automotive background vs a non-auto oriented electrical engineering background was? I have to imagine that things were pretty well mixed?
Don’t you mean alternator rather than generator here? I think alternators displaced generators in the automotive world back in the 1960s so the term is familiar. They even have rectifier diodes!
“Well, we’ve got a big, powerful electric motor, or motors, so it would be a damn shame not to use them as generators when we take our foot off the accelerator pedal to allow the car to coast to a halt, right? “
Other that the instant headache induced by the mere mention of newton meters (I’m sure they are more intuitive outside of earth’s gravity but still) this is a really great article and I am looking forward to the rest of the series.
I think generator is the correct term here as they are fully engaged to generate at the point of braking v.s. parasitically charging with ICE engine power. I’m sure I’ll get slammed for that, but that’s my take.
One thing about regen I would like to know more about is how does it get tuned for freewheeling or coasting? As an MT driver there are plenty of times when I coast ahead of an expected stop.
I understand that electric car regen is usually tuned so that when you lift off, it brakes. No coasting. Really the same as driving a manual car if you never put it in neutral.
It depends, but on most electrics it’s user-adjustable. Coasting is still better than regen for efficiency, but regen is much better than friction brakes.
depends on the car. Some cars (Rivian/Tesla) default to heavy regen with a heavier option for 1 pedal drive.
Some cars (Kia/Hyundai) have paddle shifters to adjust from true freewheeling (the most efficient) to heavy regen (the most efficient braking) to maximize energy recovery minus conversion losses
Amazing content presented in amazing writing. Thank you very much!
I really hope this series finally provides a definitive answer to Doug DeMuro’s idea that BEVs are naturally aspirated.
(We know they are, except for the Taycan Turbo of course.)
Awesome article. I work in an industry linked to the auto industry and I think this high view of EV components will go a long way to helping many people better understand what we are dealing with. I’ve shared a link to this article with various co-workers already. I really look forward to the deep dives.
Ignore me. Reading comprehension fail.
“Bald Ape?”
“I WAS bald!” George Costanza
Very interesting article…I did learn a lot! Thank you
Thank you David this is great.
And thank you Autopian, this is great.
Good introductory article. I’m looking forward to the article on chargers and charging.
The electric “handshake” between the charger and the car is something I’m interested in learning about. It seems to cause a lot of problems when it come to public charging reliability.
Yes there is a lot of data being exchanged during the handshake process, quite different than gassing up an ICE.
Just an enthusiast here so what I say may not be entire correct or complete…
From what I’ve read, the DCFC (DC Fast Charge) initial handshake involves safety checks on both sides so the enormous amount of power that’s about to go through can be safely dispensed without arcing, etc. because a fire is super bad
Great intro, thanks, I’m looking forward to this series.
Also looking forward to the article-length comments from Toecutter.
Just an editorial note, think these parentheses are meant to say ‘advise AGAINST trying this’:
Nice primer! Maybe add some gif animations for things like power/coolant/etc flow? Actually come to think of it can Autopian have gifs in articles?
haha. Definitely AGAINST!
I bet we can figure out .gifs in the stories. They USED to work.
Excellent — a thorough breakdown by someone who’s been on the front lines of EV production.
Yes. Oh yes. Finally, an EV primer I can link to instead of doing it piecemeal in the comments whenever EVs are mentioned!