With just hours to go for the current United Auto Workers’ contract, I’ll spend a lot of time today talking about unions, but first I want to address the word that has taken over the car industry: Gigacasting. It’s one of those terms we can thank Tesla for popularizing and yet another example of the company forcing automakers to radically rethink how they do business.
How much of it is Elon Musk’s grandstanding? How real is it? What’s the future of it? Let’s dive in and see.


Tesla Bets Even Bigger On The Future Of Gigacasting
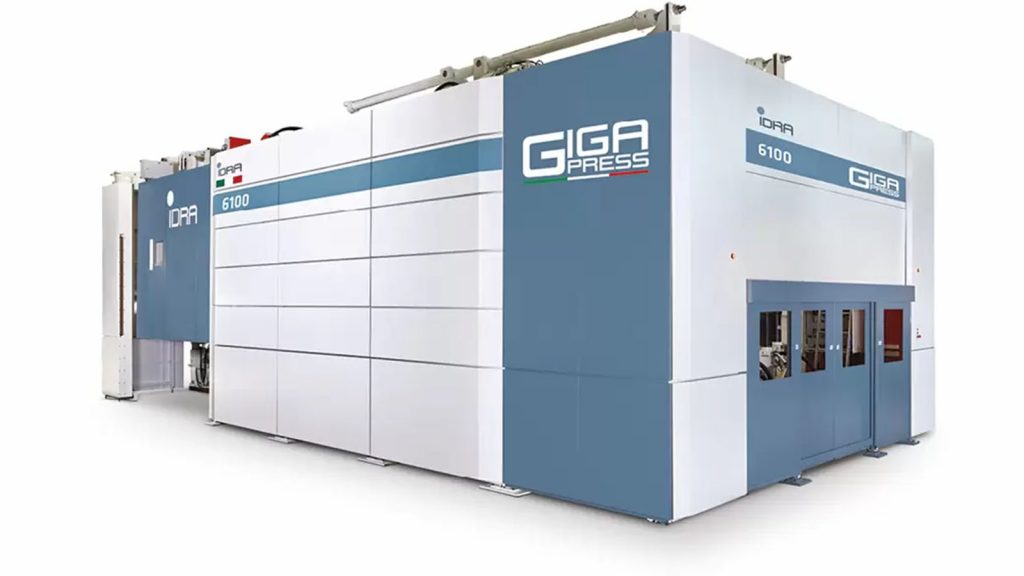
Most of you are likely familiar with the process of casting, which is basically pouring super hot metal into a mold and then cooling it to make a solid metal thing in the shape you want. Humanity has been doing this for thousands of years. It’s also a key part of making cars, though the version of it in use for the last century has mostly been making a lot of small castings and binding them together in some way (bolting, welding, gluing, et cetera).
Gigacasting—which is technically a Tesla term catching on in the wider world—does away with the lots-of-small-castings part by, instead, casting one giant piece. In theory, this has a lot of advantages. If you can make one big cast and skip the labor and energy involved in making a lot of little parts and putting them together you can make cars a lot faster.
This process is key to making electric cars affordable. EVs, as our own David Tracy pointed out to viewers of WJRT-TV yesterday, are not designed like normal vehicles. One key bit with electric cars is that the battery pack in a modern electric car is likely to be a structural element spanning most of what is often referred to the car’s “platform” in a way a gas tank generally is not. It’s an ideal design for gigacasting.
There are big challenges, of course. For one, gigacasting requires giant machines that have to generate 1,000s of tons of pressure to force liquid metal (usually molten aluminum) into a mold that, itself, has to withstand that pressure.
Additionally, modern cars use a lot of hollow structures, both to reduce weight (important for EVs) and to dissipate the energy of a crash. Gigacasting to make hollow shapes is super difficult.
Telsa, in its constant rethinking of the automotive production process, bet big on gigacasting as its method of lowering the cost of creating electric vehicles and, thus far, has been successful in reducing the number of individual parts by hundreds and thousands between models. (Editor’s Note: You think the sparse cabins of the Model 3 and Model Y are because Musk is really into minimalism? Maybe on his spreadsheets, he is. —PG)
So, as the company often does, it’s doubling down. Rather than making a few big pieces out of gigacast molds, they’re hoping to make the entire main structure in one big stamp, like a giant industrial JELL-O mold.
I highly recommend reading this Reuters piece, which gets a lot of sources to talk on the record about the future of Tesla’s gigacasting:
The sources said Tesla’s upcoming small car has given it a perfect opportunity to cast an EV platform in one piece, mainly because its underbody is simpler,
[…]
The sources said, however, that Tesla still had to make a call on what kind of gigapress to use if it decides to cast the underbody in one piece – and that choice would also dictate how complex the car frame would be.
To punch out such large body parts fast, the people said Tesla would need new bigger gigapresses with massive clamping power of 16,000 tons or more, which would come with a hefty price tag and might need larger factory buildings.
The challenges are myriad and, as the article points out, if you screw up the mold it can cost hundreds of thousands of dollars to fix and more than a million dollars to replace altogether.
If it works, though, the savings could be enormous and could help Tesla halve the price of its cars, as Elon Musk has said the company wants to do. This has forced other automakers to try and build cars the same way. Chinese EV brand ZEEKR is doing it. Cadillac is basically doing it with the Celestiq. Toyota is making a huge bet on the technology too, as it tries to keep up with Tesla and the Chinese.
Sure, it’s another example of Tesla hyping a technology that existed before it came around, but in vision and execution, it’s difficult to imagine any other automaker attempting such a big bet without the push.
Also, adding Giga- to everything is silly, but also seems to work. So, in case anyone is curious, we’ve now invented GIGABLOGGING. Please enjoy the GIGABLOGS.
[Editor’s Note: It’s important to reiterate that vehicle body castings are not at all a Tesla invention. I could give you dozens of examples of cast aluminum sections in vehicle bodies, but the one I have on hand is the 2019 Porsche Cayenne (I wrote a deep-dive on it a few years back), which has cast aluminum sections at the front strut towers (a typical location for cast aluminum) and in the rear near the wheel housings. Have a look:
In fact, Tesla started out a bit flat-footed when it came to vehicle body design, with legendary vehicle manufacturing engineers Sandy Munro and Cory Steuben — both from Munro and Associates — noting major problems with the early Model 3 design. Here I am at their facility with my colleague Jason witnessing the unnecessarily complex body comprised of far too many components, which make assembly difficult and costly, and also lead to tolerance stackup problems that could contribute to body panel fitment issues:
Munro suggested that Tesla consolidate all those body pieces into fewer, utilizing a cast design to do so. Tesla took that idea and, as Sandy and Cory make clear in the Gigacasting-themed clip below, turned it up to 11. Instead of just reducing the number of pieces in the rear section by a few parts, they sought to make almost the whole damn rear floor of the car a single cast piece.
“I said ‘This should be one part. One part. And I was talking basically about half this,” Sandy says about his suggestions after seeing the rather suboptimal early Model 3 body design. “And guess what? And guess what? One part,” he continues, showing an updated design.
“But Elon is one of those guys who’s never really quite satisfied, so the one part and the connecting parts, and the other part — the other casting — he felt should be one part. And guess what? That’s what he did over here. This is the …casting for the Model Y. And you can see this is all one part…so he went from no castings to two castings to one casting in the back, and then we move to the front of the car,” he continues, clearly impressed.
“And here we have the front casting…so incredibly well designed. And then he went one step further, and that’s why you see this gigantic hole where a floor usually sits, because again, these guys at Tesla — they take everything that you say literally and then they go and basically implement it…it’s amazing!”
So while Tesla didn’t invent vehicle body casting, it did implement it on an absurd scale, which is why the world is talking about Gigacasting. When was the last time the world cared about casting? That’s just cool in my eyes.
-DT]
Ford CEO: Is Shawn Fain Being Serious?
The impending UAW strike seems even more impending today, with various reports that the strike will probably be more of the strategic variety (i.e., only shutting down specific plants) than a massive walkout.
Credit to Michael Martinez over at Automotive News who has, thus far, done some of the very best reporting on the strike. The story he wrote that dropped yesterday and was updated this morning is no exception, especially for this little bit here:
Ford CEO Jim Farley said the company had put four “increasingly generous” offers on the table since Aug. 29 and had yet to receive “any genuine counteroffer.”
Farley, speaking later to reporters at the Detroit auto show, noted that Fain was not present when he and Executive Chair Bill Ford met with the union’s bargainers.
“There’s still time left,” Farley said. “Whether there’s room in there or not, we won’t know if we don’t get feedback. We don’t understand why we can’t get feedback to make this deal to forge the future.”
Asked if the UAW was negotiating in bad faith, Farley asked rhetorically: “How can you negotiate if you don’t get a well considered, genuine counteroffer?”
There’s a lot to unpack here. First, I want to go back to a TMD I wrote last month with the headline “Is Detroit Ready For A Union Fight With Everyone’s No-Nonsense Uncle?“
But is Detroit ready for this guy and his volunteer JV baseball third base coach schtick? I’m not so sure. I’m wondering if Detroit automakers aren’t going to start missing the older, corrupt generation of UAW leaders.
It seems like the answer is “no,” though I’d like to amend my thought a little because while Shawn Fain is definitely not here to make friends, he’s also at risk of becoming the uncle who seems to be more interested in going on Facebook to rant about his beliefs than actually, you know, doing something about them. A commenter in one of these posts compared what Fain is doing to kayfabe, which is pretty funny.
The question remains how much of this is an act and how much Fain feels, ultimately, that he’s better off striking a bit in order to unify his union.
The Teamsters Won’t Cross Strike Lines To Move Cars For The Big Three
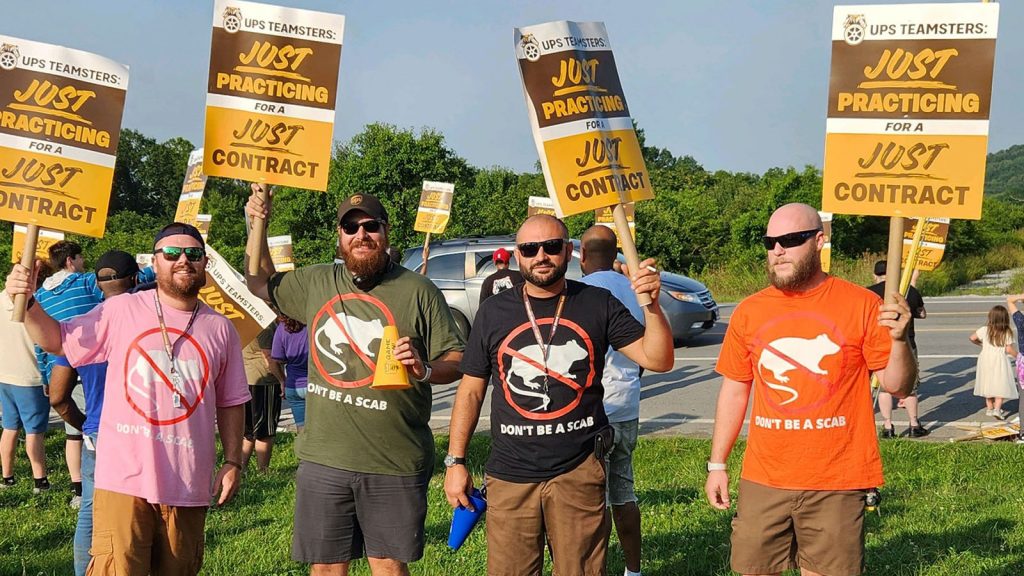
The Teamsters Union has its reputation for a reason, and as someone who is part of a union that is currently on strike (the Writer’s Guild of America, East), I’ve been impressed with just how good they are at striking. I don’t want to get into any details but, yeah, Teamsters know what they’re doing.
The organization is also fiercely loyal to people on strike and, therefore, will not cross a strike line to deliver vehicles for the automakers.
From today’s Detroit Free Press:
“We are 100% supportive of UAW workers and Shawn Fain’s positions,” said Kevin Moore, president of the International Brotherhood of Teamsters Local 299, home of James R. Hoffa in Detroit, which represents 5,000 members and most freight car haulers. “Our Teamsters will not cross strike lines.”
Fain and Moore, a third generation Teamster, spoke at the Labor Day parade in Detroit. Moore’s wife Kathy is a member of UAW Local 245 Research and Engineering in prototype engines. She has worked at Ford 40 years.
Basically, the strike can have a much wider impact than many initially anticipated.
Chinese Government Not Super Pumped About European Tariff Threat
Yesterday we mentioned that the Europeans were looking at ways to use tariffs to make cheap Chinese car imports more expensive. You’re going to be shocked, but this idea was sort of unpopular in Beijing. And by “sort of unpopular” I mean it’s like what happens whenever I wear my Astros hat in Los Angeles. Here’s a fun bit from the Reuters wrap-up:
“China will pay close attention to the EU’s protectionist tendencies and follow-up actions, and firmly safeguard the legitimate rights and interests of Chinese companies,” it added.
Eurasian Group analysts warned that should Brussels ultimately levy duties against subsidized Chinese EVs, Beijing would likely impose countermeasures to hurt European industries.
Other analysts said the probe could slow capacity expansion by China’s battery suppliers, although the move should not pose a big risk for Chinese EV makers because they could turn to other growing markets like Southeast Asia.
“Protectionist tendencies” is hilarious to me as a phrase for some reason.
- This Word I Deleted From A Headline Sent Our Whole Staff Into A Heated Debate
- I Rode A Japanese Bullet Train For The First Time And It Was Nothing Like I Imagined
- What Brands Could Have Really Cool ‘Mascot Cars’? (You Know, Like A Weinermobile)
- Canada’s New Hot Rod Business Jet Is The Fastest Passenger Plane In The World
The giga presses are impressive machines, and there are vids on them. One of the main challenges was not the pressing, but stopping tons of steel in a controlled manner and a short distance. These things pump out an entire front or rear car casting in about 26 seconds.
What Tesla did, was create an alloy for such a large casting, that would cool both in a dimensionally stable way without any internal flaws. They created that alloy. Musk might be an idiot at best, but Tesla has done impressive things.
I haven’t had time to read the comments yet, and I’m sure it’s been mentioned already, but as impressive as this is from a manufacturing standpoint, it looks terrible for repairability and probably also lifecycle cost, given that I can see this leading to lots and lots of easily-totaled cars that will then either sit in scrap yards or require a new ecosystem for recycling.
This is a form of encheapening that is not specific to a particular product or fuel type.
I am fascinated by the celebrity of Sandy Munro, as the things he suggests and advocates are to the benefit of the manufacturer, not necessarily to the customer. Some of the things happen to benefit both the manufacturer and the customer, and some favor the manufacturer at the expense of the customer.
In this case there is a tradeoff and the benefit from OUR perspective – assuming we are car buyers and not auto manufacturers – is a judgement call. This will make the production of cars cheaper, and in theory those savings could be passed on to us – but they might not be! It can also improve the precision to which cars can be built improving performance. However it will also make the car less reparable – you can now damage an entire un-fixable aluminum undercarriage instead of just some parts.
Even steel unibodies can be repaired at some expense, but this casting will be completely and utterly disposable in the case of any damage. That’s not just a problem for your insurance company (or your premiums). It’s a problem for the cost of USED cars. The more fragile and disposable a new car is, the fewer used cars there will be available on the market.
So that’s the tradeoff. Do you like the idea of possibly cheaper new cars (if Tesla doesn’t pocket the difference as profit) but more expensive used cars? Or a possibly cheaper new car that will almost certainly be a total loss in the case of a minor accident?
The only clear winner here is the manufacturer.
This is exactly what I wanted to write but I don’t think I could put it more eloquently.
I’m a manufacturing engineer and to me it is so painfully obvious that this will make cars even more disposable than they would be already with the over-complicated ADAS and electronics costs WAY more to fix than the car is worth in 10 years.
Well with teslas it has always been the case, want more power, pay subscription, want this, pay up, and speaking of disposable, if this owner bought all the jizz and jazz, the next owner in the used market gets nothing…apparently the “license” is non transferable. .. on top of the fact that the battery will have half the range.
So yes single use disposable is the way to go for them to make more money – just like the BIC bllade:))
That’s something I’ve noticed about Sandy too– he focuses on the manufacture of a single product as if it were the only thing a company makes. It makes sense, because his business has is in the optimization of a single product’s manufacture
I’ve never heard him take into consideration things like platform/product strategy, repairability, supply chain considerations, etc. Usually, it’s him getting cranky seeing fasteners instead of welds
I think the gigacast will make it more difficult to repair crash damages as you can t unbolt or rivet a piece on
I mean, that’s the thing with negotiations: you have to overshoot a bit because there will inevitably be some back-and-forth on a final deal. Sounds like Fain has some hard-nopes in the demands he won’t negotiate on, but otherwise, you gotta shoot for the moon to reach a fair deal. In his case, he’s gotta hype it up and play hardball.
Like, you’re not going to start negotiating with the salary you’d just like, accept to scrape by. You’re gonna highball the top end of a plausible range for the role and hope they either meet it or drop a more acceptable number in the middle.
And yet, despite you having a harsh opinion, Tesla, by all metrics, appears to be thriving:
2% of all car sales globally in 2022, including 30 year old VW models produced in Brasil, and 40 year old Renaults produced in Iran. The forecast is close to 3% for 2023.
Highest gross margin for any car company in the world.
Stock hovers around 270 USD at the moment.
Not bad for a company that you claim makes bad decisions.
So, I find myself both disagreeing (shocking! /s) with you AND agreeing with you (actually shocking!)
Specifically, I think that Tesla is more likely to succeed at monocasting an entire car frame than you expect, but I also think you are spot-on about Ford’s bullshit “generous offer.” I fully expect that what they call a “generous offer” is just “the same contract as before, but we’ll throw in a single bag of pre-9/11 airline peanuts”
Got a tiny home? Roll it around on gigacasters!
For the ultimate in Omega 3 Fatty Acids, get Gigacastor Oil.
Wanna catch a great white? You’re going to need a bigger gigacaster.
“Guess what happens when you have a 10% reject rate (anything over 2% is ‘stop everything, we’re fucked’) on a single part like that? Yep! You are super fucked. “
Nope. You get your Industrial Engineers together and put them on the task of reducing the reject rates to nothing or next to nothing.
I personally know actual Industrial Engineers who have done that and have caused money-losing products to become money-making products just by getting rid of excessive waste and the cost associated with that.
“Yeah. Which is the definition of super fucked,”
No it doesn’t. It’s simply an engineering problem waiting to be solved.
” because you’ve already spent $150M on your silly stupid ‘ULTRAMEGAGIGAPRESS’ and the Industrial Engineers who designed and built it, and it churns out scrap.”
Except that’s not reality. Typically it’s the Mechanical Engineers that design the newfangled stuff. And it’s the Industrial Engineers that come after to make it work well… and part of that is analyzing all the associated processes to find out the root causes and find solutions for those root causes
That’s not the definition of being ‘super fucked’. It’s the definition of ‘working out the bugs’.
“NEVER underestimate the importance or costs of doing shit right the first time.”
That’s a nice fantasy-idea. But when it’s something as new and complex as this, there is no such thing as “100% right the first time”. It’s more like a lot of “trial and error” and “tweaking things until it’s right”.
And the reality of this situation is that Tesla got the big casting thing working well for front and rear sub-assemblies of the Model Y.
So now they are saying “we are doing this well, now let’s try to take it to the next level”
So things are not nearly as terrible as you depict. If they were, we wouldn’t be hearing about this and they would still be futzing with the current gigacastings used in the Model Y
Tesla also did it in stages
1st the rear model y structure was many many parts
2nd it was 2 large castings with I think 2 additional parts
3rd the rear casting was 1 damn casting for the entire rear structure
4th they did the same thing with the front casting (one part)
If Teslas attempt at this we’re ‘such a manufacturing shit show’ conservative companies like Uber conservative Toyota wouldn’t even consider it.
Now on how to repair a crashed model y where the front or rear structure has been compromised?
I have no idea, I certainly would love to hear feedback from collision repair center people that specialize in Teslas
The rate of total loss claims on Model Ss was in line with other luxury sedans. The rate on Model Ys is reportedly “remarkably high” except there isn’t any real data because Tesla offers their own insurance at a discount to customers.
It isn’t clear whether this is because the salvage value of the vehicles is high relative to the cost of a replacement, or because it’s expensive to repair the castings, or something else.
This is super rational and technically correct and completely irrelevant when your valuation and ability to print capital are based on your EBITDA instead of the bottom line. The ‘B’ in EBITDA stands for “before”, and the money you’re worried about ends up in ‘A’ (amortization). So the people giving you money never look or ask about how much you wasted getting the process right. All they care about is future cash flow.
You might think that it all comes back to bite you in the end, but the ‘D’ is “depreciation”. So you don’t count that money coming or going.
If your earnings can’t service your debt at the end of the day, you can just shed the debt in bankruptcy and institutional investors can be left holding the bag.
Why doesn’t Europe require Chinese companies to partner with their automakers so they can steal their intellectual property, just as China has done. What a joke, they’re upset about the impending tariffs. FUCK CHINA. Their head start in tech and manufacturing is all stolen IP, developed through billions invested by Western countries in education etc. and corporations.
I really wish more people understood this. I’ve worked in manufacturing in some capacity or another for almost 30 years, and I’ve seen this shit play out multiple times… As you said, you are basically forced to “partner” with a Chinese company – a company which will eventually just cut you out of the equation, steal your IP, produce knockoff versions of your products, and you have absolutely zero recourse.
It’s literally the prisoner’s dilemma. If you don’t do it your competitor will and you’ll be out of business now instead of later.
I doubt that, just meld it down and cast again. Only major cost are energy and some time.
Time (labor, facilities utilization) and energy are the most valuable inputs into aluminum casting. The raw material cost isn’t particularly significant in the grand scheme of things, on the order of 25 cents a pound of cast aluminum scrap.
The energy is the most expensive part of an aluminum casting.
Maybe Tesla is onto something.
Mattel has been “die-casting” HotWheels cars since 1968. And they’ve stayed the same price (about a buck) for over 50 years.
https://www.npr.org/2022/12/16/1143282569/why-hot-wheels-are-one-of-the-most-inflation-proof-toys-in-american-history
And they are virtually indestructible.
Where do you think they got the idea?
Die-casted toy cars is literally this idea (whole car die-cast) origin
Pierce-Arrow was building cars with cast aluminum bodies. Not because it was cheap I don’t think.
Excellently covered. Even if I believed the claim that Tesla’s prices could halve with this method, it’s likely insurance payments will more than make up the difference in price for the average consumer.
These points about castings all sound intuitively correct to me and i can’t think of any reasonable rebuttals. I don’t think much of Musk, but the fact that a number of other legacy OEMs seem to be getting in on the large-scale-casting action indicates to me that there might be more to it, particularly a company as conservative as Toyota. What’s the other side of this argument? Anybody know?
Has that changed? On the older gen Toyotas it was pretty simple (albeit time-consuming) to swap the battery. Sure, not every dealer would sell you just the battery, but there are plenty that would. There are also a number of third-party sources for new cells these days if you don’t want to fight with a dealer or roll the dice on a refurb (which I agree is never a good idea).
Here’s a neat article about the pros/cons of giant castings. There’s a few rebuttals and caveats in there about cost savings, weight, tool wear, etc.
The process alone isn’t a game-changer–it’s another available tool in the tool chest. Whether or not there’s any benefit or cost savings, is determined by looking at how it fits into the big picture
Castings require a different layout and a building height that can accommodate cranes for the dies, so it makes more sense for Tesla or any company building out a new facility, to look into using them. The architecture of an EV chassis also lends itself better to the large-casting method more than ICEs
Makes sense for Toyota to look into it if they’re planning on building a dedicated EV production line. Toyota comes off as conservative because they want to be absolutely sure a new technology, whether in a car or in manufacturing, can be economically scaled up, while keeping to their quality/durability standards
I stand by my position 5 years ago that Trump’s trade war with China was the right decision, and we should have done it then for both economic and environmental reasons. This asymmetry cannot continue indefinitely, and the longer we prolong the correction, the worse the consequences for everyone involved will be.
RE unibody castings- yes, this is a hilariously terrible idea. If actually implemented, I will be very happy because I will retire early shorting the fuck out of Tesla.
The problem with Trump’s trade war was never that it was bad from a big picture perspective, it was that he executed it so poorly it ended up further harming manufacturing in the US and simultaneously made us look like the jerks, which is honestly hard thing to do when the other side is the genocidal Chinese government.
The media painted your picture, obviously.
Obviously. It couldn’t be the people I know in manufacturing whose companies accelerated their offshoring due to the tariffs on raw materials making it uncompetitive to manufacture things in the US. Definitely the media’s fault.
Gosh, it’s as if governments should consult people who know what they’re talking about and who would actually be affected by new tariffs/rules/etc. before blindly shoving them through and hoping for the best! Novel idea, that.
I don’t really have anything to add, though I have wondered about the exact issues you’ve addressed on gigacasting. Seems like a fast way to total cars. Insurance is going to S-U-C-K.
Yes, agreed, my thoughts exactly. Insurance rate increases are due in large part to the imbalance paid to totaling and repairing Teslas. I hear it all the time from insurance industry management.
Is it too early to vote Rootwyrm for President?
Insurers won’t insure salvage titled cars in CA.
I was well bummed prior to this. Thanks?
6 months for whole body panels? 6 months for battery controllers on PHEVs, or EGR valves on basic GM engines. It’s better than 2022, but it’s still bad.
The problem with the gigacast is that it makes the car disposable. Tesla doesn’t have a method of repair for cracked or broken castings, so they can’t be put back on the road after even a small accident.
“Why not replace the front or back casting?” you ask. Well, the castings are joined with structural glue, which is impossible to separate without damaging the pieces. So now these cars get written off, and isurance rates go up. I’ve heard they’ve doubled on Teslas. As more of this becomes apparent, insurance costs are going to be areal issue for buyers.
I think large castings are OK, but Tesla’s are so big that damage to any section means the entire vehicle is trash.
This. Exactly this. Every time I watch a Munro video about Tesla cars, the only thing I can think is that they’re cutting costs at manufacturing time at the expense of making their cars nigh-unrepairable.
Absolutely agreed. A theoretical $25K Model 2 hatchback is all well and good, but if the car is totalled after anything more than the most minor of fender benders, what good is it?
Could this be a source of cheap tesla drivetrains that could then be stuffed into retrofitted cars, boats, etc?
Maybe they should make the Gigacasting they’re already doing work first:
https://www.thedrive.com/news/tesla-model-y-owner-finds-scary-cracks-in-gigacast-front-end
This looks like stress corrosion cracking based on the photos. Might not be Tesla’s fault here, but hard to tell for sure without investigation.
I would like to see your sources on this.
Only if you’re designing for specific environments would it be the manufacturer’s fault.
What would you describe as use cases where this occurs in a vehicle that is not related to a failure on the manufacturers side?
I can see hardcore offroading or on track racing as potential over-stress scenarios, but if the vehicle is a regular daily driver, what arguments would you make that its not manufacturer related?
It wouldn’t necessarily be from over-stress. It would be from exposure to a chemical that would cause the corrosion in combination with a stress. I’m not putting blame on either party without knowing more info because if it was somehow being exposed to something weird that a car would never be expected to see, something like this could happen. I’m not saying the owner is at fault, but this seems like a weird failure here.
Got it. Not directly stress cracking but strange chemical exposure or somesuch is your thought. I misunderstood. I was hung up on “stress”.
I would say that this is true for conditions around room temp, humidity, and pressure. High pressure/temp systems can have big non-manufacturing issues with SCC. Also small bits of contamination can get embedded and create initiation sites.
This is the thing I do not understand about these big castings – how are they eliminating inclusions and porosity – I assume they are not x-raying everything, and even then you are likely to only find larger defects. Also are they doing any heat treating – this will make field repair virtiually impossible. The two issues with inclusions and porosity are initial strength can be lower – hence cracks noted (and when machining often big chunks get flung out wrecking the part), and more importantly fatigue life gets screwed – see the Audi R8 frame cracking pattern failures. As others have noted, this is where I totally disagree with Munroe – these big castings are not a good feature for the car – sure the initial piece price (after you have paid for tooling) may be low, but they make the car very difficult to repair and put it in danger of failure. These are reasons why most engineers were expecting aluminum to be primarily implemented as space frames using mostly extruded aluminum for the frame – much fewer issues with extruding aluminum than casting. Not sure why we have not seen more space frame vehicles.
When was the last time the world cared about casting?
Wow, that hurts. I work in an industry that supplies the casting industry. Castings are in more things than you would think.
Are we sure the Musk Melon didn’t just say “giggity?” I could easily picture him saying that.
“Basically, the strike can have a much wider impact than many initially anticipated.”
A strike of more than just a few weeks is going to have massive effects in an already fucked up supply chain. Small shops will close. That will lead to an increase in acquisitions, which means the industry further consolidates into fewer, bigger companies. Supply shortages spike again and car prices spike from their already inflated values.
But in the end, if labor can get a big win, I think it will be a net positive.
Just here to continue singing the praises of The Autopian! As Matt linked above, David and Mercedes were more than generous with their time to help ABC 12 with our coverage of the Detroit Auto Show. If you’d like to see Mercedes in action, here’s her interview with Kevin Goff on the Grounded G1 electric camper van she wrote about yesterday.
A fully cast car structure?
Bye, bye collision repair. Any collision that is more than a literal fender bender is going to total the car.
Castings tend to crack before bending and castings do not repair well, if at all.
A loss for the environment.
Agreed – it’s almost as if car companies don’t care about the environment…?
Came here to say the same. Wasn’t there just an article about the Rivian being crazy expensive to repair for that reason? “Oh, your Model Y got a fender-bender to the rear quarter? Gonna have to order a casting that won’t even fit on a standard shipping pallet, and then take the entire back half of the car off.”
We’ll all pay through higher insurance rates but I guess there’s something to be said for plentiful batteries to reuse from totalled cars.
It’s a secret plan to spur EV conversions of old cars! I like it.
Consumers will pay for this through their insurance premiums. It’s just shifting cost from the car to the insurance. It’s possible that consumers actually pay more in the long run. It just depends on how prone these castings are to damage and the cost to repair.
Wow, they’re innovating new kinds of externalities here!
Somewhere, an executive just read the words “innovating new kids of externalities” and got a huge raging boner.
COTD!
This has been my concern from the first time Tesla mentioned these castings. Car repair will require complete subframe replacement, so while I get that it makes making the car the first time cheaper and faster, it makes these repairs unaffordable. Tesla’s are already being totaled super quickly, this I expect to only exacerbate that problem.
Is TIG welding the aluminum possible? I’m imagining someone with a plasma cutter or Sawzall cutting out the necessary part of the casting, shipping it where it’s needed and someone welding it into place. Or making dedicated cutting areas that could be safely welded back in. It would be nice. If it’s possible.
Should be, assuming they don’t use an unusual alloy. I wonder if the high-pressure casting increases strength which would be lost at the weld?
Welding Cast metal takes a specialist. Yes, it can be done, but the people who can really do it structurally are not common, nor typically found in a body shop. They can be found in a Lambo/Ferrari body shop likely, but not the Maaco down the street who fixes “normal” cars. Combine factors like the Model Y is Tesla’s best selling vehicle, the blue collar trades are already suffering from lack of skilled workers, and the fact that this is a difficult to achieve specialty, and you have a recipe for a lot disposable cars. Now add in that car accidents have been high for the last couple years. Not pretty.
Hell, Maaco doesn’t do much of any welding to begin with, fiberglass filler is their go-to for basically everything
Yeah, perhaps Maaco wasn’t the best example 😀
Welding is a lost art, the masters of the trade are aging out, and very few young people learning the skill, unfortunately alternative methods are more prevalent today.
Ford has some amazing glue that the new magical tailgate is built with that might do the job though. It doesn’t even need consistent or complete coverage, according to the former Tesla engineer behind the project at Ford.
Generally the aluminum alloys that cast well, don’t weld well (or at all), and vice versa. – and aluminum is quite difficult to weld to begin with. You’d likely have to remove the entire part from the car while doing it, as so much heat would be conducted away from the puddle by the aluminum (it’s used for heat sinks, after all) that anything else attached to is going to get cooked.
If someone were to come up with a super-alloy that worked well for both welding and casting, that would fall into the “disruptive innovation” category. It would be a really big deal.
A different take on this: much of what you pull out of an electric car is recycled into other things — there’s a very robust market for the batteries and drive-trains for conversions, and the other parts join the spares stream. However, somebody is going to make a ton of money rebuilding these “write offs” with new castings. Ease of manufacturing (single piece parts) also can translate into ease of disassembly if labor is cheap enough. Then you simply recycle the damaged casting. Hmm.
There’s something to be said for either ladder frame and space frame chassis. While not as light weight, inexpensive to manufacture, or as safe, they are repairable. I’m a big fan of ladder frame precisely because it is easy to repair and easy to modify.
That’s the genius of Tesla. They will vertically integrate the casting repair/replacement into their already robust service business.
It’s sad to admit that in spite of all of Tesla’s screwery, they still have the most reliable and repairable EVs on the market in the U.S. The other auto manufactures should be able to dominate them, but they’re playing catch-up instead, constantly, with products that don’t work.
EVs shouldn’t be this hard. The technology offers the promise of 1 million mile cars that last the better part of a century with minimal maintenance and repairs. Leave it to the captains of industry to figure out how to make them unrepairable nightmares in the quest to constantly nickel-and-dime everyone, so that we can keep filling landfills with crap, all in the name of the almighty dollar.
I think tesla is trying to figure out how to manufacture them to a high level of quality (insert pannel gaps jokes here) and as simply and inexpensively as possible.
The better they get at lowering the cost to manufacture the lower they can (could) make the purchase price And the more quickly they can manufacture more and more units for sale thus speeding up the transition from ice to ev.
Of course repairability is a big concern and should be for a durable good that we should expec5 to have a 10-20 year useful life… however lowering manufacturing costs of evs is a bigger concern bc tesla had surpassed TOC over a 5 year time span (at least model 3 vs Toyota camery), they have not yet surpassed up front out the door unit costs to consumers vs ice vehicles.
How they solve repairability when the whole front and whole rear structure are one part each? IDK, I’d guess via (magic like) metallurgy innovation but as someone else said that would be one he’ll of an innovation in itself
That’s the genius of Tesla. They will vertically integrate the casting replacement into their already robust service business.
But, but… all of these cars will have full self-driving… so they will never get in an accident.
Talk about a giga-editor’s note!
Haha!
Giga-editor’s note from a GigaChad editor!
I gigahate the gigaadding of the giga prefix to gigaeverything
Gigaseconded.
This is as gigadumb as i-everything 10-20 years ago.
Yeah, well I TERAHATE it!
don’t even go there.
Yeah, the constant tendency toward exaggeration is a real “peta”. (betting the amount of praise I get for this stupid pun will be less than an atto-boy)
Giggity
All of these Prefix and suffix-isims need to die out. I want the most monotonous names for things. Ironically Tesla already did this with the model 3
Eh, I think they’re ultramega OK.
Are you saying this tendency is doubleplusungood?
When the Gigapress method proves a mess, will it be called Gigagate? And I hate when every scandal has “gate” at the end.