“Son of a bitch!” I yelled, cursing whichever J-hole had apparently run the lug nuts on my $700 Chevy Tracker’s right front wheel down with an impact. “Just torque it to spec you cretin!” I shouted into the sky, picturing that R-hole holding the trigger of that pneumatic impact, banging the lugnuts down until their threads plastically deformed. For hours I toiled to undo the that Y-hole’s dastardly handiwork, and for hours I failed. But, being the stubborn bastard I am, I didn’t give up. Here’s how I triumphed above one of the worst foes in all of wrenching: the seized lugnut.
If you haven’t experienced a stuck lugnut in your days of wrenching, thank the car gods immediately, for it is a traumatic experience from which you will emerge a different person. A hardened person. A person who, when someone mentions brake work or suspension work or swapping out summer tires for winter tires, just stares blankly out into the distance, quivering ever so slightly before “coming to.” It’s bad; it’s really bad.


The last time I dealt with a stuck wheel nut, I never did manage to get the thing off. It was holding an aluminum five-spoke wheel to, if I recall correctly, a Jeep Cherokee XJ’s Dana 30 front axle; I don’t remember what I did to solve that issue — I think I just removed the whole wheel hub from the knuckle, and recycled the hub/wheel together. I really can’t remember. Anyway, that experience stuck with me, so when I went to yank the right front wheel off my recently-acquired $700 Chevy Tracker, and was met with a lot of resistance, terror shot through my veins.
This was a corded DeWalt impact I was using to loosen these nuts — it had been undefeated up to that point in lugnut removal bouts, but I was 15 seconds into holding its trigger and nothing was spinning. “Oh hell no,” I thought as I held onto that trigger for a few more seconds. I then liberally sprayed on my favorite penetrating lubricant, “Cleveland’s Finest,” as I like to call it — PB Blaster. I left the nuts to soak for a day, and returned yesterday to finish the job.
Use Penetrating Lubricants
I threw the 19mm socket onto the lugnut, popped the nose of my DeWalt impact into the square end, and hit the trigger. “Bumbumbumbumbum!” I heard as I felt the socket let go, no longer requiring me to hold tightly to that impact wrench to counter the torque. The socket was now just spinning, bouncing lightly on what was left of the six points of the hex nut. I removed the socket:
Oh crap. What the hell! A two-piece lugnut?!
I have for years been cursing the two-piece lugnut, a regular open acorn-nut with a cheap sheetmetal beauty cover over its end. That sheetmetal cover can not only break, like it did here, but it also very frequently just slides right off, leaving the bare open acorn nut underneath. That acorn nut, by the way, still does the job, but it lets moisture into the threads and, more importantly, it’s a smaller size since it no longer has a cover, so trying to use your regular socket will just cause you to round the acorn below.
I knew this, of course, so I went down to an 18mm. Shoving that onto the bare acorn nut resulted in, well, more peril. I rounded the acorn. Sonuva bitch!
From there, I decided to break out the big guns. First, I grabbed a sledgehammer to break the tiles in my kitchen, revealing secret bunker doors. Then I grabbed my bolt cutters to get through a lock, and pulled — gripping with two hands, and leaning back hard — the two doors, which opened about their outboard hinges. “BANG” the cast iron closures went as they landed, breaking even more tiles. I then hopped into my climbing harness, hooked into a carabiner, and slowly lowered myself 200 feet to my secret lair, which was really nothing more than a humongous dirt cave. It was pitch black down there; spiders and rats abounded, and a tiny light flickered 500 yards away in a corner. I deactivated the booby traps, and pushed over the barriers marked “WARNING: DANGER AHEAD. TURN BACK.” I was now just feet away from the tiny light, which stood directly above what looked like a small cylindrical object.
I knew that continuing my approach would knock at least seven years from my life expectancy, as the potent smell that I’d come down here for began triggering my nasal receptors. But I continued on, wiped the grime off the cylinder sitting upon a marble perch, and read a name I hadn’t seen in years: AERO KROIL.
It’s the most potent penetrating lubricant in all the land. Many, including I, fear it, as one shot of the pink liquid creates a smell so powerful it feels as if it’s penetrating your very soul. I try to avoid it whenever possible, but the Tracker’s lugnuts gave me no choice. Upon gripping the can, I sprinted across the dark, dank floor of my underground lair, hooked my harness back up to the cable, and hoisted myself up to my kitchen, which was now covered in shattered tile.
If You Round Your Nut, Hammer On A Slightly-Too-Small Socket
I then ran out to the Chevy Tracker in my driveway, slowly removed the can’s lid, and pressed the trigger. A pink stream impacted the lugnuts, I dropped the can, and ran as far as I could, hoping to avoid wafting in The Kroil. I returned six hours later, expecting a 50 foot crater where my Chevy once was, but luckily, the fluid must have focused its energy on the corrosion between the lugnuts and the wheel/wheel studs. Knowing that there was still residual Kroil on my wheel, I tried making quick work of my operation. I grabbed a 17mm socket (a 12-point might have fit on there better; I used a six-point), placed it over the rounded 18mm nut, and hammered the crap out of it with a sledgehammer. The socket cut deep into the nut, forcing the steel to flow and subside like a liquid, creating grooves that the socket could use for grip. I shoved my DeWalt into the socket and hit the trigger.
” BANG BANG BANG” went the impact wrench. But no movement. How was this possible?! The Kroil! I’d sacrificed part of my life expectancy to use it, and it had… failed me? I tried again. “BANG BANG BANG!” Still nothing.
Desperate times called for desperate measures, so I reached for my two-foot breaker bar. Then I grabbed my MAPP gas torch. The added leverage along with the heat along with the Kroil, I reasoned, would conquer this situation easily. After removing the 17mm socket, I applied the flame to the rounded nut, hammered the socket back on, and installed the end of the breaker bar. I pushed, but nothing happened. So I pushed more; still nothing. Then I gave it all I head, and finally the bar moved. I looked down at the lugnut and was shocked; The socket was rounding the nut!
How?!
The undefeated DeWalt, the undefeated breaker bar, the undefeated Kroil, the undefeated heat! I had assembled The Avengers of seized fastener removal, and they were being shellacked!
I was now growing deeply concerned. If I couldn’t get this lugnut off, I’d have to drill out the lug and replace the stud. This would be a gigantic pain in my ass, as I’d have to remove the hub, which isn’t exactly trivial on these Trackers. But I was running out of options. I’d now broken the outer lugnut shell, rounded the 18mm nut, rounded the rounded 18mm nut with a 17mm socket, and now the acorn nut looked a lot more like an acorn than it had when it had flat sides.
After carefully replacing that AeroKroil — which, I’m convinced, is basically nitroglycerine — back into the dark cave below my kitchen, I searched my garage for something, anything, that could bring me relief. Luckily, I found my rounded-nut removal tool kit (also called a bolt extractor kit).
Hammer A Bolt Extractor Like One From This Irwin Kit
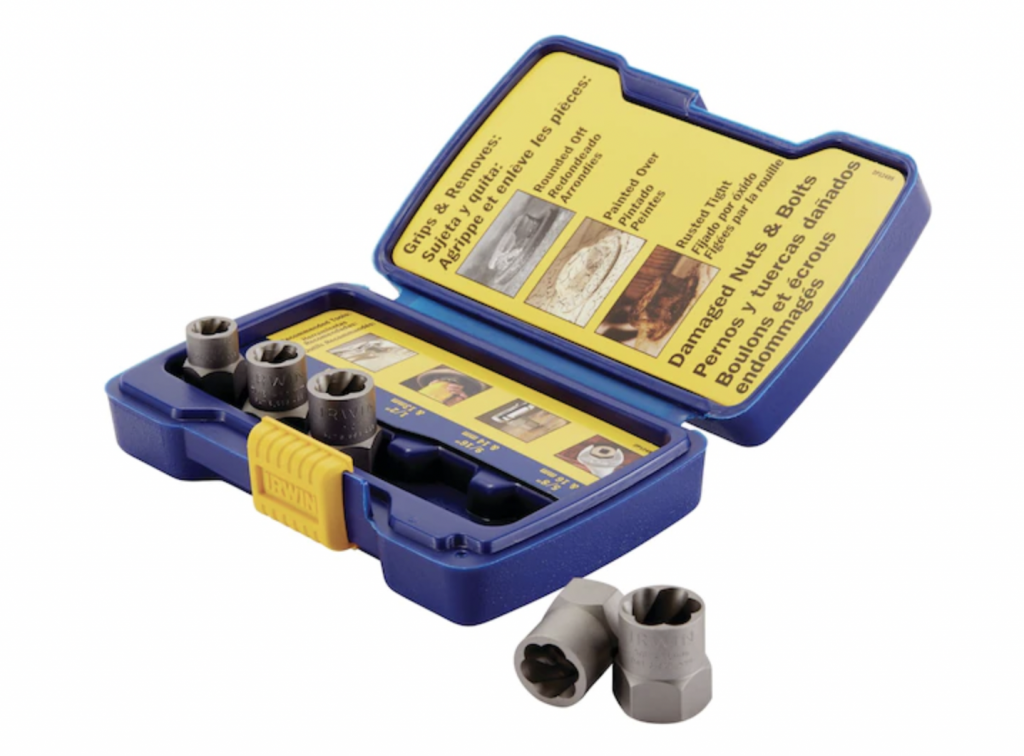
The biggest one in my collection was a 16mm, and though I’d just rounded the nut with a 17mm, the fact is that I was now about to try to drop three millimeters from the nut’s original size, or two if we discount the sheetmetal shield. I didn’t have a 17mm rounded-nut removal tool, so — after heating up the nut — I placed the 16mm one over it, and whaled on the tool with a sledgehammer until it bit into the nut a few millimeters. I then grabbed my breaker bar, installed a 1/2-inch-to-3/8-inch adapter (since my rounded nut removal tool was a 3/8-drive tool), and shoved that into the tool now locked onto my lugnut. As soon as I started pushing the breaker bar, I could feel plastic deformation; I knew right away what was happening:
The half-inch-to-3/8-inch adapter tool sheared right off.
Luckily, the rounded nut removal tool has a hex on its outer surface, so a 21mm socket went right over top. Pushing the breaker bar further, I felt it spin, though nothing “broke free.” I was just tearing up the outside of the nut. Ef!
Use LOTS Of Heat
My rounded nut removal tool had only slid on a few millimeters, since – again — it was a 16mm, which was much smaller than the nut’s original size. I knew I had only one final choice: I had to hammer that tool all the way onto that nut. It wouldn’t want to, because it’s too small, but with enough whaling on that tool with my sledgehammer, that bastard was going to get on there. First, though, I had to heat the nut up far more than I had so far. I had to let that flame just linger.
I watched as my aluminum wheel’s clearcoat literally caught fire; I had to let it go, because this was the only chance I had. For about a full minute, I held the MAPP gas flame over that nut until it was hotter than magma; then, after really giving it everything I had, I managed to get the rounded nut removal tool to slice through the nut and seat itself all the way to the nut’s base.
Use A Big-Ass Breaker Bar
I inserted the socket that was at the end of the breaker bar over the tool, laid the breaker bar level, and then jumped on its end. BANG! The 340 lb-ft of torque that I’d created, along with all that heat, along with all those penetrating lubricants, along with a rounded nut removal tool had finally defeated that develish lugnut that some R-hole had installed, possibly to spite some misbehaved customer.
Of course, this was just round one. I had four more lugnuts to go.
I ended up breaking one more sheetmetal beauty cover, and in one case, I had to install a jack handle over my breaker bar (see above) to give me three feet of leverage instead of just two, but ultimately I managed to get all five lugnuts off thanks to copious — and I mean copious — amounts of heat from that MAPP torch. That really was the ticket; I had to be okay with destroying my wheel’s clearcoat so that I could really heat those nuts and studs up, then I had to just get enough grip and leverage to break the nuts free.
The whole ordeal of removing five lugnuts took me a few hours; normally, it’d take me about 30 seconds. So to whichever U-hole is responsible for really ugga-dugga-ing the crap out of those five nuts: I hereby place an very specific automotive curse on you for all of eternity: May all of your vehicles saddle you with peeling clearcoat, squealing serpentine belts, and sagging headliners.
Never underestimate taper tension, like the connection a tie rod end has to a steering arm or on a ball joint. Case in point. Was removing a front wheel off my Elise to replace the brake disc when I snapped off the small, splined end of the adapter tool provided. The Elise uses wheel bolts, not wheel nuts, and there is a good amount of taper or cone shape where it mates to the wheel surface. The wheels were off regularly enough, so it wasn’t corrosion, and I (or the dealer where I took it for inspection) always torqued the bolts to spec. So, I quickly made a roughly correct shaped tool out of a large allen wrench or hex shaped piece of bar stock, and then got ready to apply some force with a breaker bar extended with a jack handle. This time, however, as I was leaning on the jack handle, a friend gave the head of the breaker bar a couple of really good whacks with a hammer, essentially applying small shocks that for a fraction of a millisecond deformed the wheel surface and the bolt came free. Just like the trick of hitting both sides of a steering arm with hammers at the same time to cause the hole to deform and free the taper of a tie rod end.
I can’t believe no one is talking about the massive revelation in this article: Tracy’s “Secret Lair”!
Raise your hand if you already suspected that he had one (if not here, then at least back in Germany under the army base).
The unfinished quality of The Lair feels authentic (dirt floors and no electric lights), but I’m questioning whether there’s really a marble plinth at the back.
More of this, please.
I’m assuming there is a tunnel to his folks’ house in Germany too.
Nah,David isnt fooling anyone. He’s too normal to have a lair.
Torch on the other hand- you know he’s got some high grade weirdness happening somewhere!
My question is this, ( and it is probably why you seem to want to avoid heat ), what are you doing to the heat treat in the aluminum ( I presume ) rim when you hit it with the rtorch? In a former life, before my life as a programmer, I worked in various Bicycle repair shops ( so, lots of aluminum involved ).
David – those studs are probably toast. I hope you decided to bite the bullet and mount new ones all around on that hub. heck, you probably toasted the entire hub and should replace that.
i thought i had it bad when i did rear pads on the cadenza a few weeks back – the lugs all came off just fine, but the wheel was rust-welded to the hub. fortunately for me, the ol’ “hold an 18″ 2×4 against the rim and and bash the wood with a sledge” trick worked. IIRC there was one or two lugs that required some liquid encouragement (PB blaster for them, single malt for me although, it’s possible i needed a shot of encouragement for each lug, even if they were loose). seems like many problems in life are solved by two fingers of scotch, and in some cases (like yours) lotsa fire.
I’m a little disappointed in your automotive curse David. Sagging headliner? Squealing belt? That’s amateur hour. Try this:
“I curse you to a 9 hour road trip; in a minivan, with five 14 year old girls. Three of whom do not get along, and one of whom gets car sick. And they are in charge of the radio.”
Go big, or go home.
“I curse you to a 9 hour road trip; in a minivan, with five 14 year old girls. Three of whom do not get along, and one of whom gets car sick. And they are in charge of the radio.”
Based on my own childhood experiences the solution is to tell them the A/C is busted and the radio only works on AM. An hour into the trip they’ll all have passed out from the drone of talk radio and heat exhaustion. Then turn the A/C on (all vents pointing to you, obviously) and quietly listen to whatever you want.
In all my years of wrenching on stuck and rusty bolts and other car parts, not one single time has any sort of penetrating oil done jack squat. I don’t know why I even bother keeping a bottle of that stuff around.
On the other hand, a nice hot torch works nearly every single time. Sometimes just a propane torch will do, sometimes I gotta go full-on MAPP. But it works and it works fast.
That was my main takeaway from the Project Farm video about penetrating oil. None of them were particularly miraculous, but heat made a drastic difference.
That said, even if it doesn’t help that much with seized parts, it is sometimes useful to soften up the rust on threads before you back a nut off. I’ve also used it to clean rusty threaded holes. And it works nicely to lubricate things like the pivots on a snowblower. You can spray penetrating oil into places you might otherwise have trouble reaching.
Is it “whale” or “wail”?
I was previously and blissfully unaware of the two-piece lugnut. WTF?
The worst issue I’ve had with a lugnut was at a NASA time trial event at Mid-Ohio. I kept multiple sets of tires in rotation, and I often swapped them in between sessions. I tended to use the impact to spin the nuts on and off, and a torque wrench to tighten them down evenly. Easy-peasy.
On this day, I was spinning a lug nut off when it seized halfway up the stud. I have never seen such a thing. Working the nut back and forth with a breaker, I was able to make a little progress. That is, until the rocking action worked the stud out of the hub. So then I was stuck with a freely-spinning stud with a nut seized on it.
Luckily friends leapt to my rescue. We drilled out the stud enough so that we could break it off, then we filed off the head of the stud enough to fit it in through the back without having to pull the hub.
Experienced something similar in my first real foray into wrenching… baby steps… but the brakes on my boat trailer seized and I needed to remove/replace the calipers and pads, which obviously means removing the wheels. Unfortunately the boat was still on the trailer and was the only thing keeping me from launching for the season Panic ensued, followed by a 30 second internet search and voila, this is easy. Until… one G-D lug nut didn’t turn… eventually sheering off the thin aluminum casing leaving the “acorn”, which I now know is a real thing. After a broken 3/8 – 1/4 extension, half a can of penetrating oil, and half-a-dozen PB-Blaster filled open wounds, I hammered on a sacrificial socket that was a size too small and, without a breaker bar that fit over my socket handle, rigged up a pry bar and stomped on it like I was putting out a fire (all the while anticipating a massive shin injury which thankfully never happened). Long story short, F salt water, and F lug nut casings. The silver lining, aside from launching on time, was the satisfaction of actually solving this problem… and thus my love for wrenching has been born. Thank you Autopian!
Ok dramatic, Kroil doesn’t smell that bad. It’s certainly no worse than any other penetrant spray…
Why not just drill it out?
I did the small size socket on my Dakota, on the GS1150 I had a seized, rounded bolt on the fork, I went with a bolt extractor and breaker bar. After about 5 min of dread a quick youtube search led me to the bolt extractor.
I have similar experience.
Trying to undo the front sprocket nut on a Kawaski ZX6R years ago.
IIRC it was a 17mm nut, with a 1/2″ socket on it, and wrapped over the breaker bar: a 6-foot length of scaffold pole: “give me a long enough lever, and I will move the world.”
We turned the pole through (I swear) 90 degrees (from vertical to horizontal), with 2 people holding the bike steady and me (14 stone of ape) literally hanging off the end of the pole before the nut broke loose and I fell flat on my back!
If you like the results of Kroil, but not the smell, try Mouse Milk sometime. I keep a bottle on hand for those times that PB Blaster isn’t enough.
How do you milk a mouse?
I used to know how that joke went….
A $700 vehicle is never $700.
Also, get rid of the Pittsburgh stuff. Maybe you won’t break as many tools
How dare you speak like that to David Tracy!? This is the man who dyed his clothes with used oil, the man who cleaned engine parts in his dishwasher, the man who lists a salvage yard as a secondary residence. Asking him to use tools not from Harbor Freight would be akin to asking the Pope to perform a bris…
Aero Kroil is the s&!t. Works great on big threads like control arm and strut bolts.
Order of usefulness-
1.Aero Kroil
2.old bubble gum
3.My dog’s slobber
4.Some blood
5.PBR
6.WD-40
I will never understand why people think WD40 works as a penetrant. It doesn’t.
And by PBR did you mean PB Blaster or Pabst Blue Ribbon? One of them will eat through rusted nuts. The other is available at auto parts stores.
There’s also Penetrol available at HVAC supply houses. I’m amazed at some of the things I’ve broken loose with that stuff.
Of course, I’m not 17 anymore: when I go after something that looks like it might dispute my mastery, I always just squinch it a bit in the wrong direction first. Also, I give a few taps to the socket on the fastener first just to appease the automotive gods.
WD-40 is GREAT for keeping wasps from building nests: pre-treat area a month before they really start buzzing around, and hit it every 2-3 moths after that. I haven’t been stung anywhere I treated in the 20+ years since I learned this. Also takes bumperstickers off. I have no other use for it.
Several decades ago we needed to remove a front wheel from a bus. Luckily this was at a workshop and not on the side of the road as one of those nuts was definitely not playing the game. Ended up after some time of having no luck with a bar and socket, two of us jumped up and down on a six foot length of steel pipe, that had been slid over the bar, while the third guy used an oxy to heat the nut up, eventually it gave up and came loose. It was scary thinking of getting a flat tyre out in the middle of no where and having to deal with this.
No kidding. When I went to rotate the tires on my new old car two of the wheels were seized to the hubs, one so badly that I had to drop the car repeatedly with the lug nuts loose in order to break it free. That would have been a problem if I’d been using a crappy scissor jack on the side of the road instead of my nice floor jack.
Before they went back on, each hub face got a good application of grease to hopefully keep it from happening again.
Very entertainingly written David.
Next time i get a seriously stuck nut i’ll find a way to mount the drill press on it’s side.Try arguing with THAT you miserable piece of sh!t nut! *evil laugh*
I hope you pressed new studs into that rotor.
Most definitely! My guess is they toast, even if the threads would accept a new lug nut. They all needed to come out after all that heat and torque. One good pothole and that wheel would be driving off on it’s own.
You can buy an “emergency nut remover” that works pretty well when used with a lubricant or heat and a breaker bar.
It’s got reverse screw threads on the inside, so you tighten it onto the nut, and when you turn to remove, it digs into the nut.
You have to pound the nut out later, but it works.
Bought one after my Focus’ oh-so-pretty 2-pieces crapped out twice (first time, I thought it was my having stripped the nut. Second time it happened, I was suspicious…)
That’s literally what he used on this. That’s the Irwin kit he mentioned.
There’s a very good reason why for my tire changing toolset everything is half inch drive at the minimum, even the speeder and the sliding T handle. David Tracy Demonstrated that.
I’m built like a toothpick so when it comes to loosening and tightening stuff I use as much mechanical advantage as I can get, and with that I need something that can handle a ton of torque.
Have you tried “Busty” (yes, that’s really what it is called.) I would like to attach a photo, but that’s not possible. I would google for a photo to link, but …..
It is made by Herdor’s Inc in Mokena, IL.
I ran in to that on my wife’s former 2002 Nissan Sentra. The guys that did the tire swap were a good shop, but one lug would NOT yield to my electric impact. So I then broke my breaker bar. Finally I went to the super long pipe on the lifetime-guaranteed 1/2 inch ratchet. That got’er done.
I stopped by the shop later that day to let them know what had happened, and the owner was adamant that they torque to spec. I told him that I know, which is why it was odd, but I wanted to give him a heads up.
Also, once again, Liquid Wrench is vastly superior to PB Blaster — every time I used PB, I got nowhere until I got mad and busted out the Wrench. Hit the offending fastener with Liquid Wrench, whack it with a hammer, and leave it for a couple of hours. Then come back and do it again, but leave it overnight. I’d bet it comes off the next day pretty easily. I know we don’t always have that kind of time, but when you do, this seems to work well. It has for me.
Just be careful, I have seen the Wrench eat into an asphalt driveway. The Wrench don’t fuck around.
I should add that I hope the stud isn’t cross-threaded. That would definitely suck.
Deathwheel either vertical or horizontal which ever way you have better clearance.
or an Oxy-Acetylene heat it up red hot and hit it with a 3 lb sledge if you have clearance or 3lb Sledge and chisel.
Or just go straight in with the Oxygen and take out the stud the entire way.
Can’t be stuck if its a liquid
Jason needs to get David and Oxy-Acetylene and a good set of safety equipment and fire extinguishers
They have 17.5mm sockets for this exact reason. There are cheaper options, but I’m lazy, so here’s one of the first search results:
https://palmac.net/koken-18317m-17-5-1-sq-drive-rear-wheel-nut-sockets/
And I’ll raise you a CV axle galvanically corroded into the wheel bearing which was galvanically corroded into to knuckle.
They had to melt the axle stub and bearing to get it out. They would have torched the knuckle off, but it was unobtanium at the time.
What was a $300 dollar quote to replace a CV axle ended up being $1200 + 2 extra days waiting on the bearing.
A big FU to the Mitsubishi engineers who couldn’t be bothered to google “galvanic compatibility chart”.