I just got back from the Easter Jeep Safari (where I blasphemed in a Ford Bronco Raptor — more on that in a later article). While there, I had the chance to drive Jeep’s EJS concept vehicles, and without a doubt, the most technically interesting was Magneto 3.0, the third iteration of Jeep’s Magneto concept, which debuted a few years back, and which I made fun of in an article titled “The Electric Jeep Wrangler Concept Looks Like It Was Designed By A High School Shop Class.” I think I ticked some folks at Jeep off, but I don’t think I was totally out of line — Magneto is not a production-viable machine, and for Jeep’s first EV debut to be something so primitive felt a little silly given the then-current auto climate. Or maybe I was being a jerk. Regardless, I got to (briefly) drive this concept Jeep off-road, and it was phenomenal. Here’s why.
Okay, let’s just get straight to my “High School Shop Class” dig: The Jeep Wrangler Magneto, especially the version that first debuted in 2021, is a very basic electric vehicle. It does not have a separate drive unit (which integrates a motor and gear reduction into a single housing, sometimes along with power electronics), it doesn’t have a skateboard platform with a flat cabin floor, it doesn’t have a huge battery pack tucked between the axles, and it isn’t aerodynamically optimized to reduce drag. It is an internal combustion engine-powered Jeep Wrangler JL modified, arguably rather crudely, to be electric. Despite this, as I will note in a minute, it’s phenomenal off-road, as I found out when I got to drive the vehicle for the first time.


I said “crudely” modified, because what Jeep has done is essentially just bolt an electric motor to a manual transmission — something that shop classes around the world have been doing since the 1980s, and probably earlier:
The transmission is a Tremec out of a Challenger Hellcat, which is a good thing, because it has to handle up to 850 lb-ft of torque (and 625 horsepower).
Here’s a look at a thick stack of adapter plates between the motor and transmission bell housing:
You can see in the image directly above a “SEVCON” DC-DC converter, which takes the lithium ion battery’s high voltage (800 volts, 70 kWh, per Motor Trend) and steps it down to power the vehicle’s 12-volt accessories (like the dash lights, wiper motors, headlights, and so on). You can also see a custom crossmember to hold up that transmission, and in the background are the battery cells, taking the place of the gasoline vehicle’s fuel tank and exhaust:
The image directly above shows that the Wrangler’s four-wheel drive transfer case remains, sending power via driveshafts to the solid front and rear axles. There’s a beefy “Dynatrac 60” up front and a beefier “Dynatrac 80” in the rear, both with 5.38 reductions in their diffs. Wheels are 20-inchers wrapped in 40-inch tires, and spaced away from the body with a three-inch lift.
High-Volume Vehicles With Two Live Axles Will Likely Die Off As The World Goes Electric
Anyway, if it’s so crude, then why does it even matter? Why write about it? Well, it matters because it may be the only live-solid-front-and-rear-axle-equipped electric car ever built by a mainstream automobile manufacturer, and it may stay that way until the end of time. That’s because solid axles — beloved among hardcore off-roaders — have no place in the EV world, as our suspension engineer Huibert Mees has made clear in his article “The Surprising Ways Electric Car Suspensions Are Different Than Gas Car Suspensions: Ask An Engineer.”
Here are the main bits from that article:
You may have noticed that there are no EV’s at the moment with live axles. This may change in the future, but there are very good reasons why live axles are not ideal for EV’s.
The first is that live axles need a drive shaft that moves up and down with the suspension. Unfortunately, this driveshaft runs down the middle of the car in the same place where it would be ideal to package batteries.
Batteries take up a lot of space and are heavy so you want them to be mounted low and as close to the center in the car as possible. Unfortunately, that’s also exactly where the driveshaft is. Having a moving driveshaft would take away too much space for the batteries which would hurt range too much. A perfect example is the new Ford F-150 Lightning. Ford ditched the live axle (shown above) and put in a new independent rear suspension just for the Lightning (see below). I think Ford knew it could never make the Lightning work well enough as an EV without going the extra mile designing a whole new suspension. Believe me, Ford would never have spent that kind of money on the F-150 if it didn’t believe it was absolutely necessary. I think you will see this happen more often as existing vehicles are converted to EV.
Huibert’s piece continues, stating:
The other reason is that a traditional differential with the typical ring and pinion gear — a pairing that turns the power 90 degrees — is not a very efficient beast. The ring and pinion depend on a sliding action between the gears in order to minimize noise, and this adds friction. Friction is an energy loss and EV’s are all about minimizing energy losses so that you get as much range out of a battery charge as possible.
I will say that there are some companies out there developing electric motors that are mounted on a live axle (see below) but as a suspension engineer, I would be very concerned about the increased mass from these motors. Unsprung mass is the enemy of good ride and handling and is the reason live axles are not in use much anymore. Increasing unsprung mass with the addition of an electric motor to the axle would be the wrong way to go, in my opinion.
I don’t think we will see many companies building EV’s with live axles unless they are desperate to get into the EV market with an existing product and they just don’t want to spend the money on a new suspension. I highly doubt the resulting product will be as competitive as it could be.
Though there are some solid axles with motors integrated into the diff housings, and there are some with hub-mounted motors, the reality is that the live front axle is almost certainly going to die with the internal combustion engine, as it just doesn’t make a ton of sense with an EV. Hell, it’s pretty much already dead, other than in the Wrangler and in heavy-duty truck applications. Even the live rear axle alone is likely to start dying off (again, we may see some hub motors like in the Lordstown prototype); remember, when Ford modified its F-150 platform to create the Lightning, it didn’t just clear out the crossmembers to make way for a big battery, it also changed the solid rear axle to independent suspension.
The death of the solid axle is a shame if you love off-roading, because a live axle is brilliant in the most treacherous conditions; the reason for this has to do with roll centers and durability, as Huibert mentioned in his article “Our Suspension Engineer’s Take On The ‘Solid Axle vs Independent Suspension’ Off-Road Debate.” Pair such a superior suspension design with an electric motor and you have something truly magical off-road — something that will likely never exist in production, but that absolutely dominates on the rocks.
I found this out when I drove Magneto — specifically Magneto 3.0 — for the very first time in Moab last week.
It May Be A Primitive EV, But It’s An Off-Road Beast
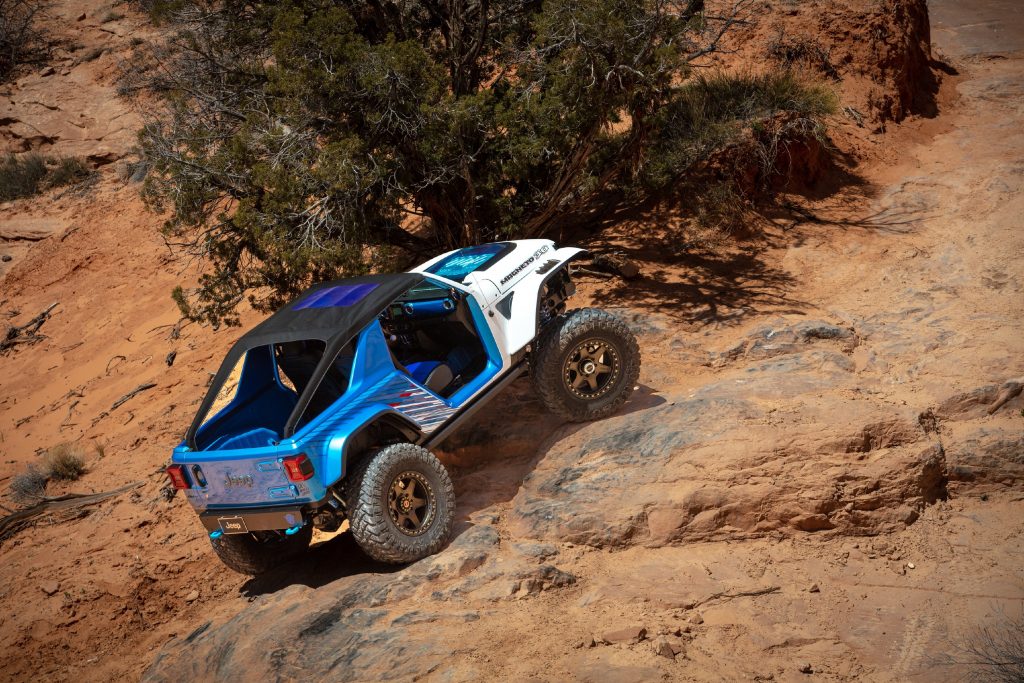
To start Magneto, you press in the clutch and then hit the power-on button — just like you would if the vehicle had a gas engine. From there, you can let off the clutch, since there’s no “idle” necessary with an electric motor (with a gasoline engine, you have to turn the engine over to build compression to get combustion — at zero RPM, there’s essentially no torque other than that of the starter motor. An electric motor builds torque to propel your vehicle at zero RPM). Then you simply put the transmission in gear (I like to clutch in when I do this), and tap the accelerator pedal.
My friends at Quadratec get into the “starting”/driving experience in this video:
And here are my friends at TFL showing off the last iteration (2.0) — you can really get an idea for how silent this machine is on the rocks in this video:
Changing the position of your foot on the accelerator pedal of an electric vehicle changes the current sent to the electric motor(s). How the pedal’s position relates to the current output from the battery to the motor (and thus torque output at a given speed) is dependent upon how engineers have calibrated that pedal (via the controller — you can see some of the power electronics in the video above the Quadratec one).
Like with an ICE car, when you change gears, you’re altering how much your motor’s torque is multiplied before it gets to your wheels — and it’s torque at the wheels that affects acceleration/climbing ability. So the gears on Magneto 3.0 behave somewhat like you’d expect them to. A low gear allows you to hold your foot lightly on the pedal, and still crawl up a grade easily at a low speed. To go faster, you have to dip into the pedal further, and though you can go quite fast in first (unlike in an ICE, whose RPM is limited due largely to reasons associated with rotational inertia — also, torque tends to drop at the top end), second gear lets you do that without dipping as far on the pedal. In fact, second gear works fine from a stop to probably highway speeds, though I never drove above about 15 mph.
My shifting was a bit clunky, as matching the motor speed with the wheel speed was tricky, and though an electric motor has less inertia than an internal combustion engine does, slowing it down and speeding it up does come with a bit of a shudder. And trying to get the pedal position just right for a smooth shift is not easy; I often found myself too deep on the pedal, such that when I upshifted, the Jeep would want to take off, forcing me to back off. Maybe I’d have figured it out over time — and certainly it’s something that could have been baked into the software to make it feel smoother — but I found that just stopping the Jeep, then dropping it into first gear when I got to a steep obstacle, was about the only time shifting out of second made any sense.
That first gear is where Magneto shined; what makes this machine so unbelievable off-road is its incredible low-speed control. Truly, it felt like I could pilot this Jeep up a steep grade at 0.2 mph; it was unlike anything I’d ever experienced off-road. Generally, to drive that slowly up a steep grade, even with a Jeep that has a high 70:1 crawl ratio, one has to carefully modulate that throttle based on the change of severity of the slope/obstacle. On most vehicles with lower crawl ratios (which I explain in detail here), one has no choice but to left-foot brake, as the vehicle wants to drive too fast. Wranglers, especially automatics, are a bit better about that, but the fact of the matter is: Torque is dependent upon engine speed, so if you need more torque than you have at the engine speed that corresponds with your desired vehicle speed, you have no choice but to speed up. That can cause you to lose control.
Magneto, which also adds to its low-end torque and beautifully calibrated pedal with a crawl ratio of somewhere around 100 (multiply the 5.38 axle ratio by a ~4.7 first gear ratio by a 4:1 transfer case low range ratio), doesn’t have this issue. It lets you crawl in a way that only a Mercedes Unimog can really understand:
With all that gearing, even driving down a grade at half a mile an hour with your foot off the accelerator means that motor is spinning quite quickly, and offering heaps of regenerative braking. This makes it so that, eve on steep downhill grades, one has to actually press the accelerator pedal to move, allowing for precise speed control even downhill.
So sure, Magneto is a fairly primitive EV, but to combine its silent torque with all that control with all that suspension articulation afforded by the soon-to-be-departed solid axles — it’s just an astonishingly-capable thing of beauty. As an off-roader who has been obsessed with crawl ratios, low-end torque, and Ramp Travel Index scores for over a decade, I’m in awe. And a bit sad that such a contraption will likely never exist on the U.S. market.

Car is not appealing in the least design wise to me. A manual electric is super appealing and I really like the idea. If they smooth out the shift I’m in! Electric is super fun for some things but really removes some of the driver experience, this is a great middle ground for enthusiasts
“Unfortunately, this driveshaft runs down the middle of the car in the same place where it would be ideal to package batteries.”
I can see a solution to this little problem… mount the electric motor toward the rear the same way the motor in a VW Type 1 Beetle was.
So that would enable a bunch of unobstructed space between the axles for the battery.
OR… just have the electric motor integrated with the differential.
A beetle doesn’t have a live axle, live axles need a room between the diff and wherever the power is coming from to move up and down.
And you can’t mount the motor on the axle, that’s unsprung weight which was mentioned througly in the article
That “Unimog in supercrawl” video was zen AF.
I could watch a Unimog creep along for hours, as a form of meditation.
I dream of Unimog 404 ownership. Alas they are very expensive and I really have zero use for one. They are great because you can go anywhere as long as you don’t need to get there fast.
The world needs to get over it’s efficiency high-horse and just start doing more of this exact thing. Even this is still WAY more efficient than any gas powered solution.
Until you factor in driving someplace to do this, and driving back.
Efficiency doesn’t help you when you’re on the side of the road with a dead battery because you tried to drive two towns over. The problem isn’t efficiency except as it pertains to range. And this wouldn’t have a whole lot of range unless it had a 6000lb, $40,000 battery. Aka what the Hummer has.
The beauty of it is, it’s a simple enough formula that it could probably be reproduced pretty easily. Someone should start a shop that modifies your Wrangler into a Magneto.
If a motor was incorporated into each live axle, integrated with a differential, it might prove interesting. Un sprung weight would be high, but would that matter crawling rocks?
Like the rear axle on the Changli? (-;
You just invented the Clod Buster!
You freaking win this one!!!! What a beast it was!
The first concept was the best. This vehicle would never see production, at least the first concept could easily mass produced.
Just wondering why batteries cant be placed low but leave enough space for a drive shaft in the middle, or why does the drive shaft have to be in the middle? I mean instead of half axles you cant have a 1/4 and a 3/4 axle? I just dont know enough about this part of the car.
Speaking of Jeeps and upcoming Fords, hows the fording with that one? (-;
https://www.npr.org/2023/04/11/1169209369/jeep-lake-woman-alive-rescue-texas
So an EV Jeep with solid axles isn’t very efficient, can’t fit all that much battery, and so would have a disappointingly short range. However, it has some very real advantages over a gas Jeep when it comes to off roading.
Sounds like the Jeep Hurricane needs to be a production side by side. The 80 mile range is much less likely to be an issue, and the awesome crawling becomes even more of an asset.
Agreed!
I think my CJ7 with a 15 gallon fuel cell generally only gets maybe 80 miles to a a tank, but 6.5 to 1 first gear and 4.3 to 1 atals with somehwere around 120 to 1 crawl ration means you can start the thing in first gear and it will just idle away at around 2 miles per hour.
Do you ever abandon ship and leave the passenger or is it too tall for that game?
I typically do not like to criticize writing as I am no poet myself but this article left me feeling like it was accidentally cut off. What makes the Magneto 3 better than the Magneto? Was your first take on the simplistic approach just wrong? What did Jeep improve on that made you fall in love?
That being said, after reading through the article the following thought keeps popping into my head:
Since torque and low speed modulation is key in offroading, couldn’t you achieve the same result as magneto with a plug in hybrid of sorts. Think a jeep 4xe but with a dedicated electric crawl gear. That gives you the best of both worlds and let’s you maintain your axles. Also, the ICE can act as the generator to keep you electric crawl gear running similar to a Chevy volt range extender.
My view of its simplicity remains unchanged. It’s primitive, but incredible off-road.
Agreed that with plug-ins, we get the same advantages! (but for a limited duration/range).
Neither here nor there but damn the new Jeep grille makes it look like a Mahindra.
We’ve come full circle!
You mean to tell me that Jeep has found a way to get even less use out of the snorkels that everyone mounts on their Wranglers?
There is nothing stopping live axles. The electric motors can be placed ahead of the FWD axle and behind the rear axle leaving space for a reasonable size battery between the axles.
The tricky part would be driveshafts from the motor to the diffs. We’d probably have to move away from universal joints and use high angle CV shafts with slip joints to get good axle movement. Maybe tipping the motor down and tipping the input of the diff up may help.
I think my colleague Jason and I went through this exercise. Hmm; I can’t seem to find the drawings he made of various motor/driveshaft configs.
Are you guys still thinking of EV-ing something?
I wonder if a DeDion tube would behave like a live axle? Then you could mount the motor, gearbox and diff to the frame between the wheels.
I’ve often idly wondered about swapping a Tesla drive unit into my truck while retaining the leaf-spring setup.
That’s exactly what Ford did with the 1998-2000 Ranger EVs, DeDion tube at the rear axle for leaf spring suspension, rear electric motor with cv joints to drive the wheels.
This is SO cool! Most of the rigs I off road with are trailer queens that also do not carry extra gas with them on the trails and many are running smallish fuel cells, at the off road parks. this would be fantastic at an off road park. The “if it can’t tow a 40k pound trailer up a 20% grade for 1000 miles one one charge every day for a year then it should never be built” comments do not need to be directed at this EV.
I am interested, at least from an off-roading perspective, what the charging infrastructure will be for these types of vehicles in the future.
Just use a hybrid V12 Lambo to charge it
or your Lighting with Pro Power on Board
most likely the trailers would have a dc to dc connection or the air up/air down stations would have a DC fast charger connected to some solar to catch the sun while providing shade.
Did they give you an estimated range in and out of crawl mode (1st gear)? Were they charging it out in the field between letting writers drive it?
I don’t think they had to charge it while journalists were present, as we were only driving about half a mile each. Off-road, I too would be curious what it’s range is. On range, even with a 70 kWh pack, I bet it’s in the low 100s. (That’s a total guess).
Often at off-road parks and events I use most of my gas idling waiting my turn on the obstacles not an issue with an EV.
My concern would be using up the range getting to the trail and then taking the risk of bricking it with a dead battery out in the middle of nowhere. I am thinking solar/wind powered charging stations near popular trailheads ¯\_(ツ)_/¯
Interesting. Is there an analog to a tachometer for an electric motor to gear box setup that would aid in shifting? Old guys like me rarely use a tach even when available, relying on a calibrated, mark II ear canal to guide up/downshifts, but that, too, goes out the window with silent motors.
A tach gauge is do-able, but most homebrew EV conversions leave out the clutch. The driver just treats the transmission like a hi-lo transfer case and only shifts when fully stopped.
An oldschool 3 speed would be ideal for EV’s each gear could be made larger and sturdier and still save weight over a 5-6 speed. If spaced far enough, you could omit the low range transfer case. Just make the 3 speeds ‘crawl’ ‘low/town driving’ ‘highway’.
You can hear nature. Nice.
Had the Wrangler 4xe been available with a stick and 2 doors I would have bought it just for this reason. Cruising a forest road in electric mode would be fantastic.