Large component casting, known as megacasting in some rare cases and “gigacasting” in Tesla parlance, has become a controversial technology in the automotive industry. It’s touted as a grand way to speed up manufacturing and slash costs. It’s also decried for supposedly making cars unrepairable after an accident. But how true is that?
Concerns around “gigacastings” are widespread; we’ve covered them in these very pages, too. The common belief is that large castings are fundamentally impossible to repair. The fear is that if a vehicle is involved in an accident, it could be an instant write-off if parts of the cast structure are damaged. It’s understandable that this would cause some concerns for car buyers—nobody wants a fragile, easily damaged car, after all! Are these assertions valid, though?


Fundamentally, there are a lot of assumptions involved here. The truth is that castings aren’t magic items that can never be fixed. As such, cars with large cast structures are not “uninsurable” or prone to being totaled in the slightest collision. Today, we’re going to explore the reality of the matter, getting into the nitty-gritty of how Tesla gigacastings are actually repaired. Let’s dive in!
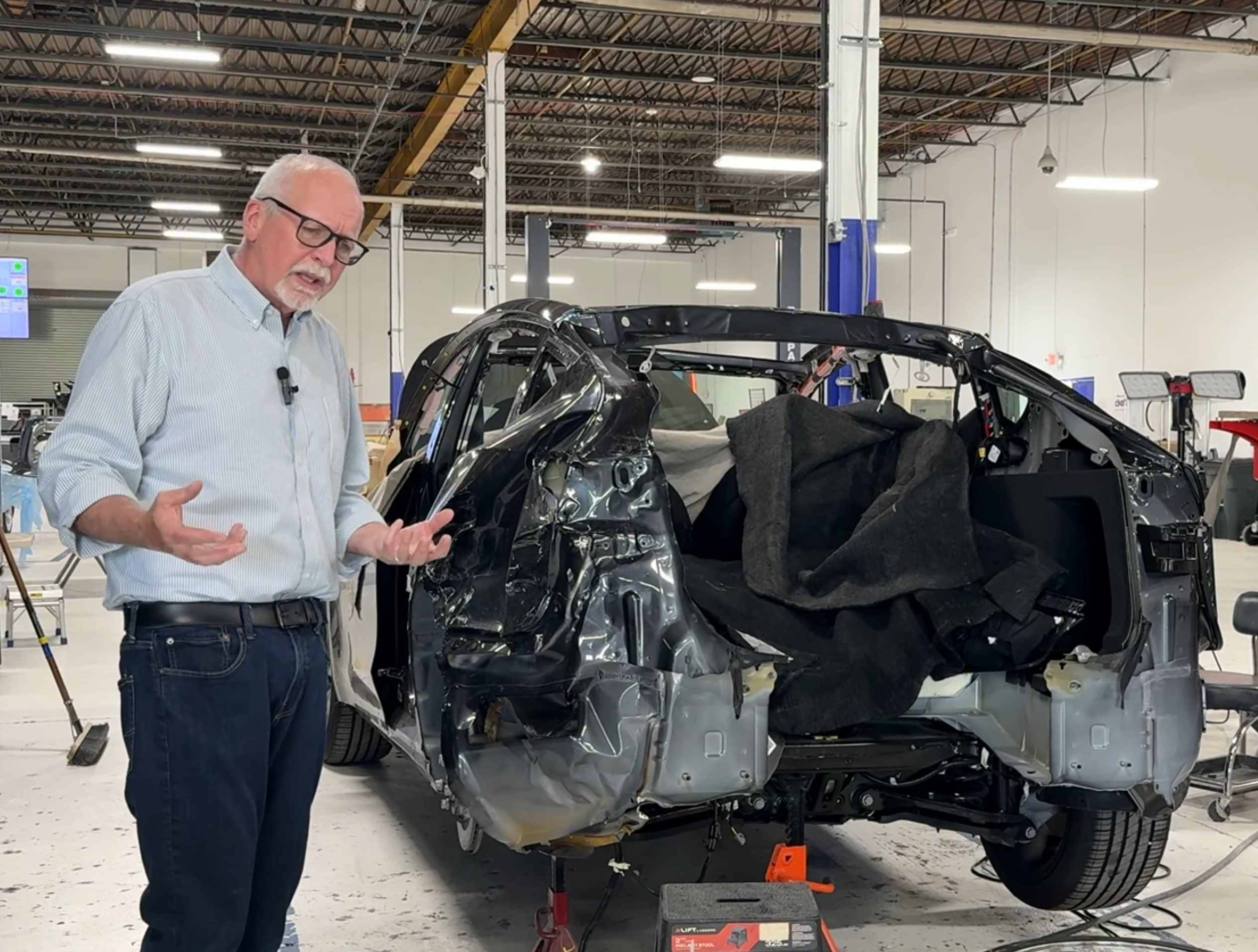
Get The Real Information
We all know why Tesla loves gigacasting. Replacing multiple smaller components with a single, large casting drastically slashes the number of manufacturing operations required to build a vehicle, with massive savings in cost and complexity. But we’re so often told that this comes at a cost. Some auto news outlets will tell you gigacastings can’t be repaired, and the idea has strongly taken root. You’ll find offhand mentions of repair issues in gigacastings in many articles on the topic. But while repair for large castings can be tricky, it is by no means impossible.
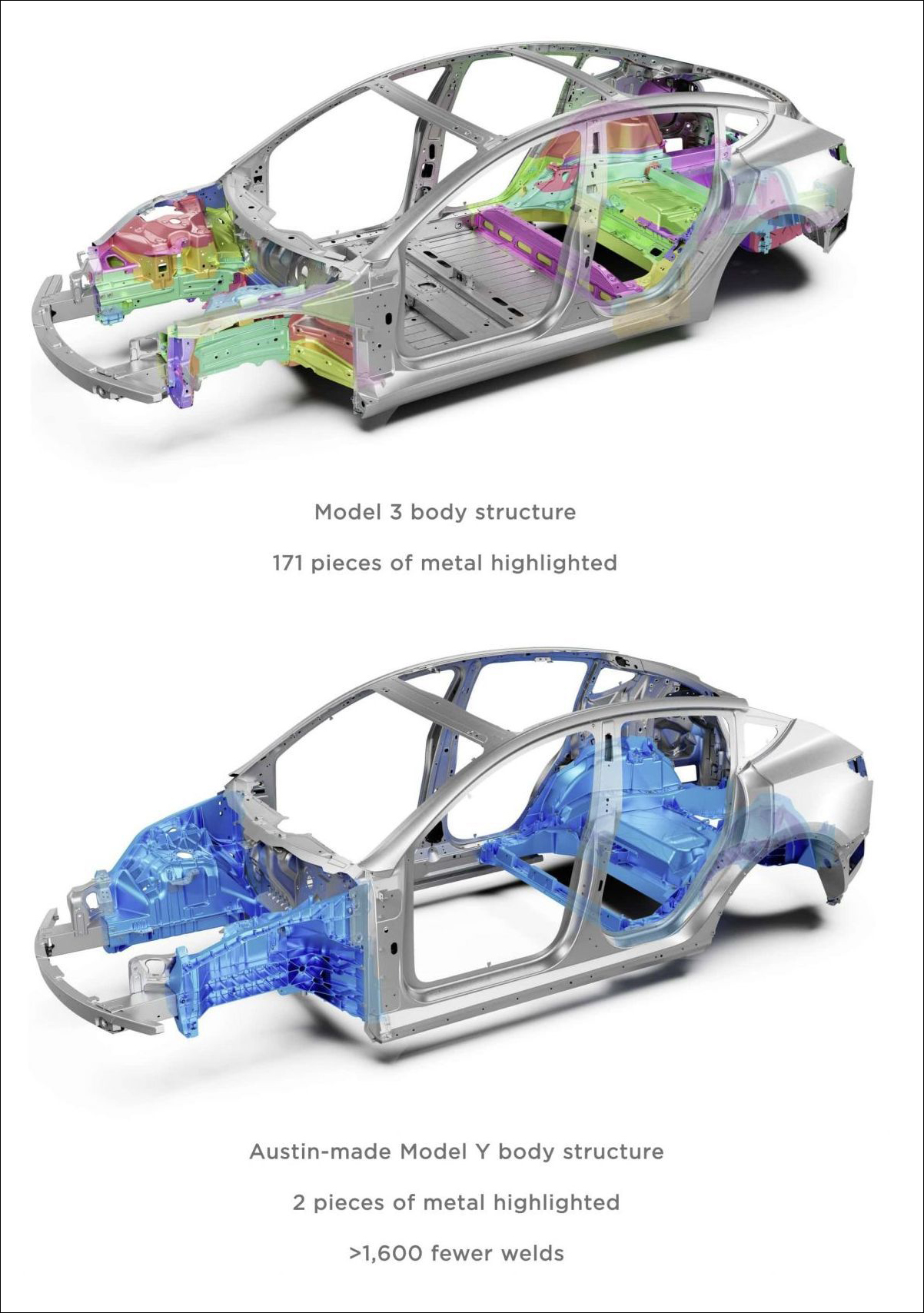
You have to go to experienced sources to get real information on this topic. A great place to start is looking at what actual crash repair experts are saying, like those at Evolve EV Experts. In May this year, CEO John Sweigart put out a video on this very topic, aiming to clear up some misconceptions around repairing vehicles using megacast body components.
The video concerns a crashed 2024 Tesla Model Y. This model uses a large casting to form the rear structure of the vehicle. The vehicle can be seen to have significant damage to the driver’s-side rear quarter panel and wheel well, with the sheet metal crumpled and bent. It’s clear the vehicle took a sizable hit to the rear end.
“There’s some myths about what happens with gigacastings,” says Sweigart. “The important thing is you can repair a lot of the gigacasting.” He notes that when large component castings first hit the automotive market, replacement of the casting was the only viable option for fixing damaged parts. However, things have changed in recent years. “Since then, there’s lots of repair methods that have been developed,” he explains.
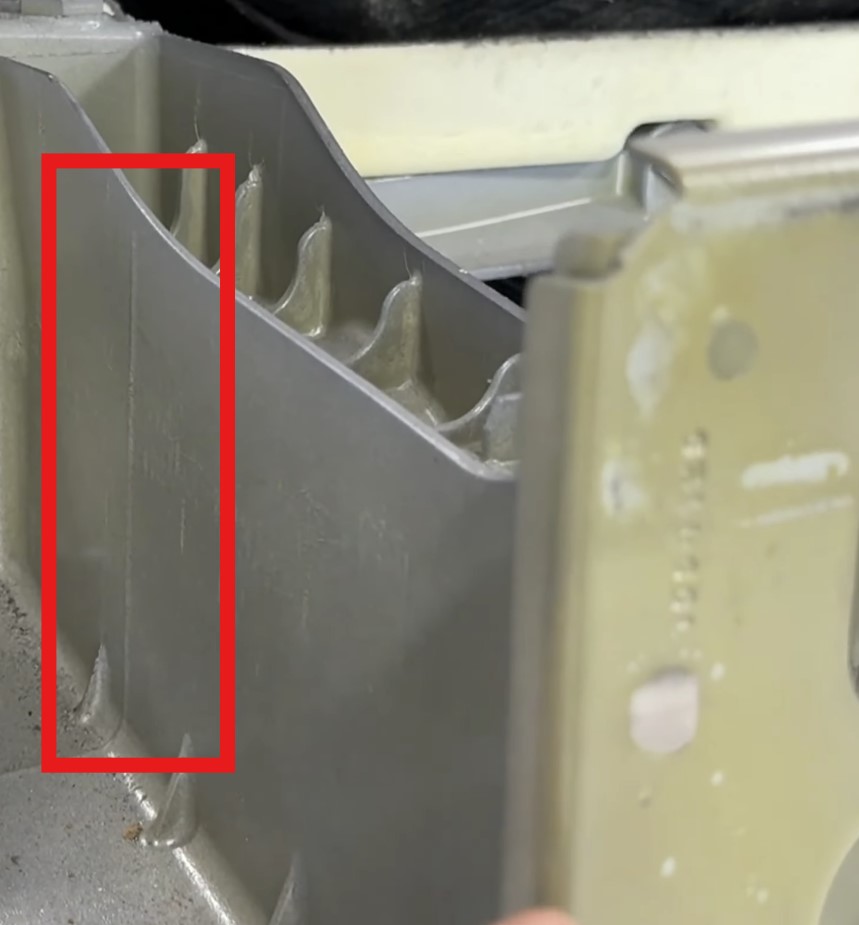
The fact is, there are numerous bonding and welding techniques that are perfectly applicable to these castings. They’re quite different to anything you might use on a vehicle made of stamped steel sections, but that doesn’t make them any less valid. Sweigart points this out, highlighting a rear section of the casting, where there is an obvious vertical line in the metal. “If this was hit and fractured, we have the option to literally cut this off and attach a new piece of cast aluminum on this spot,” he explains. “It would be done with rivets and structural adhesive and a backing plate on the join.”
It’s worth noting that castings are more likely to fracture rather than bend or crumple like sheet metal parts, as Sweigart explains with regards to the Model Y. “This may crack or move a little bit, but in most cases, this will just shatter or break,” he explains about the rear crash structure. However, despite the hard hit to the rear, this example has fared well.
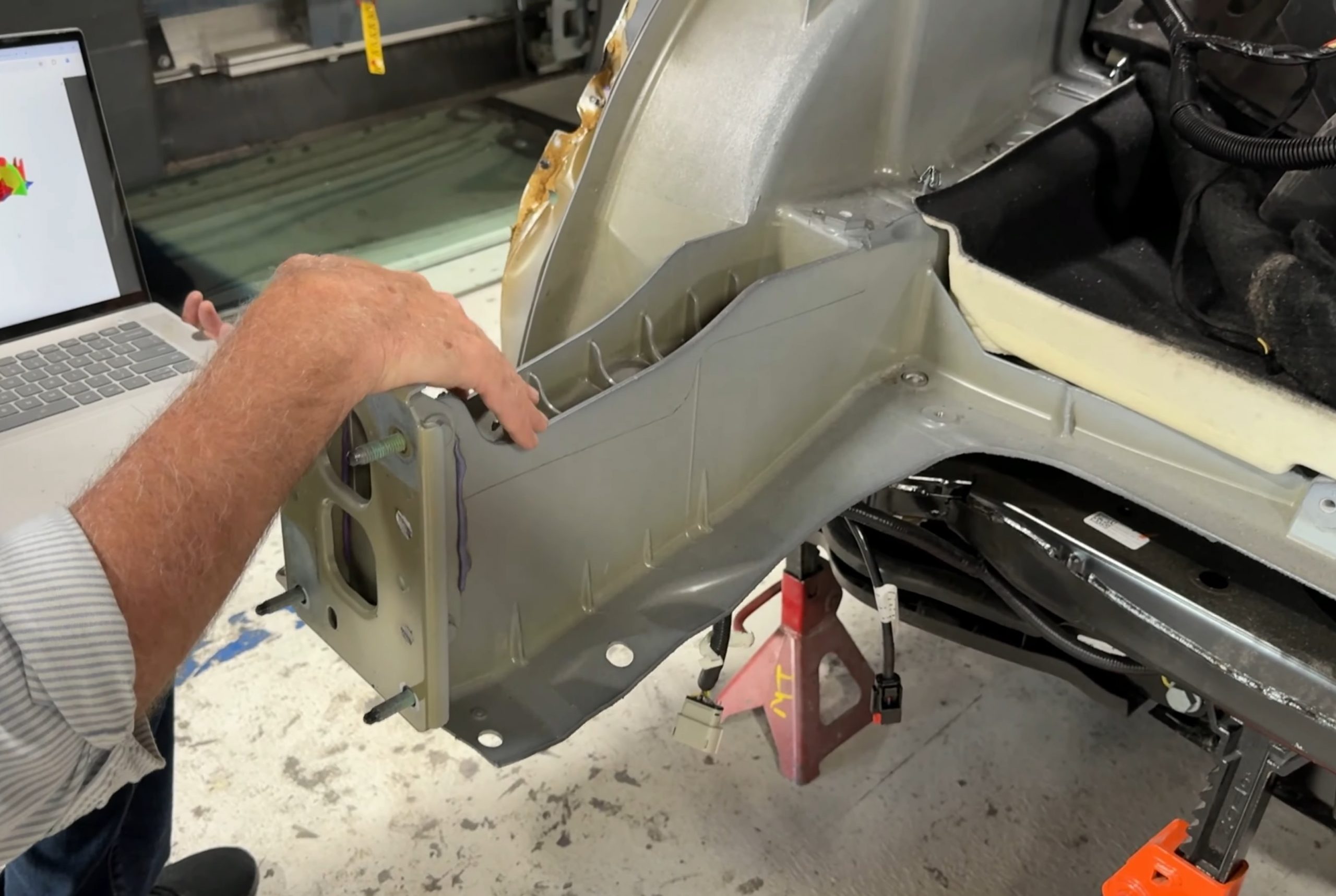
“We have measured this vehicle … all of these control points are in the right position in space.” Moving in closer, the casting seems virtually untouched. “This is the area of impact, this is probably the most important area, and as you can see, there’s really no issues,” he notes.
That’s not to say a casting that looks right at a glance is still fine. Cracks are quite possible in cast aluminum parts, and can weaken a structure significantly. However, that doesn’t mean they’re a death sentence for the whole cast part. They can often be welded to restore the part’s integrity.
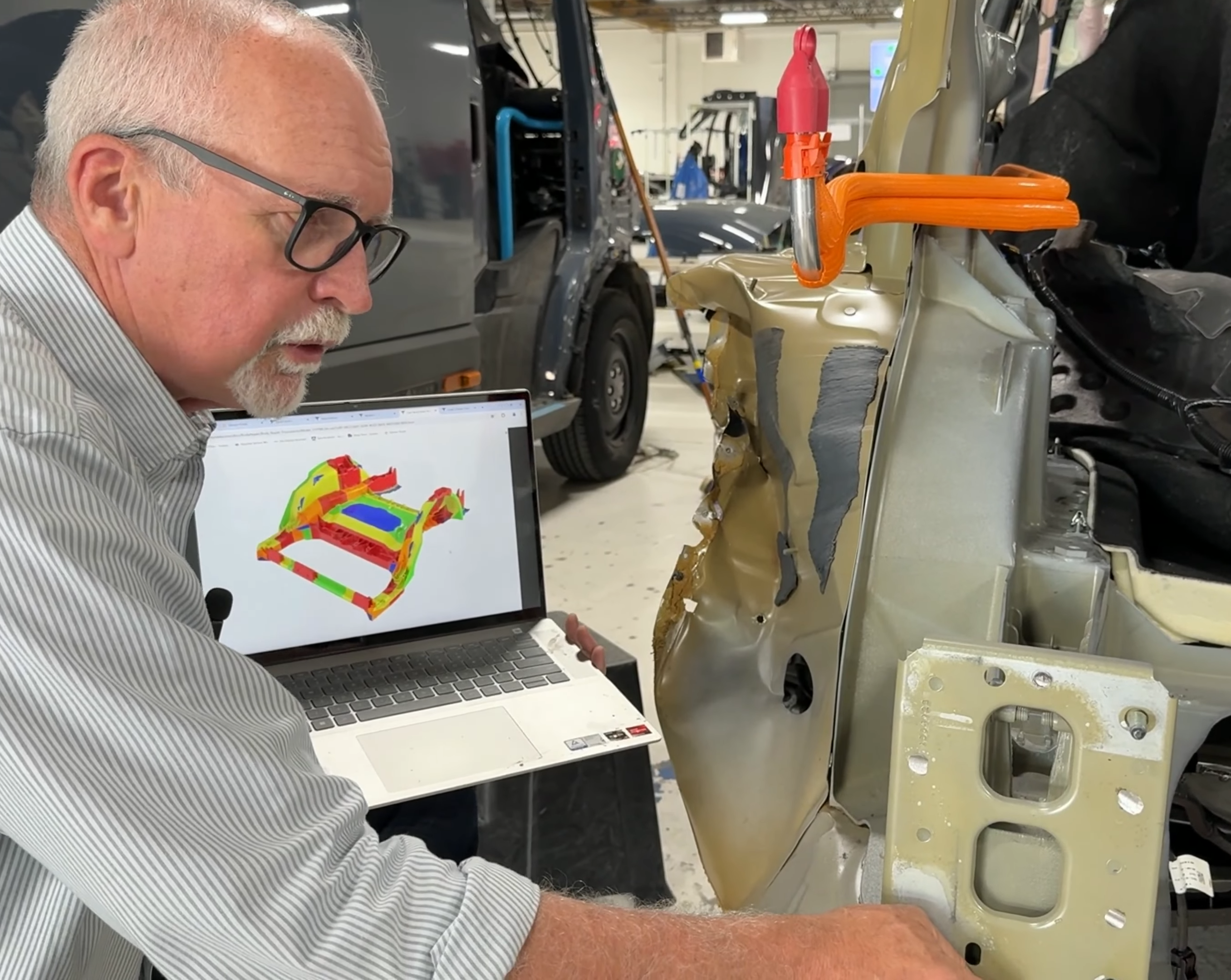
“If a crack is less than 50 mm long (~2 inches), you can weld it up in some of these areas.” says Swiegert, pointing to a digital model of a Model Y rear structure. “In some cases, depending on the zone, you can weld a crack that’s up to 30mm (1.2 inches), but you might have to put a backing plate behind it for support.” He’s referring to a map of the casting that shows what areas can and can’t be repaired in various ways. Where did Sweigart get that model? Why, from Tesla itself!
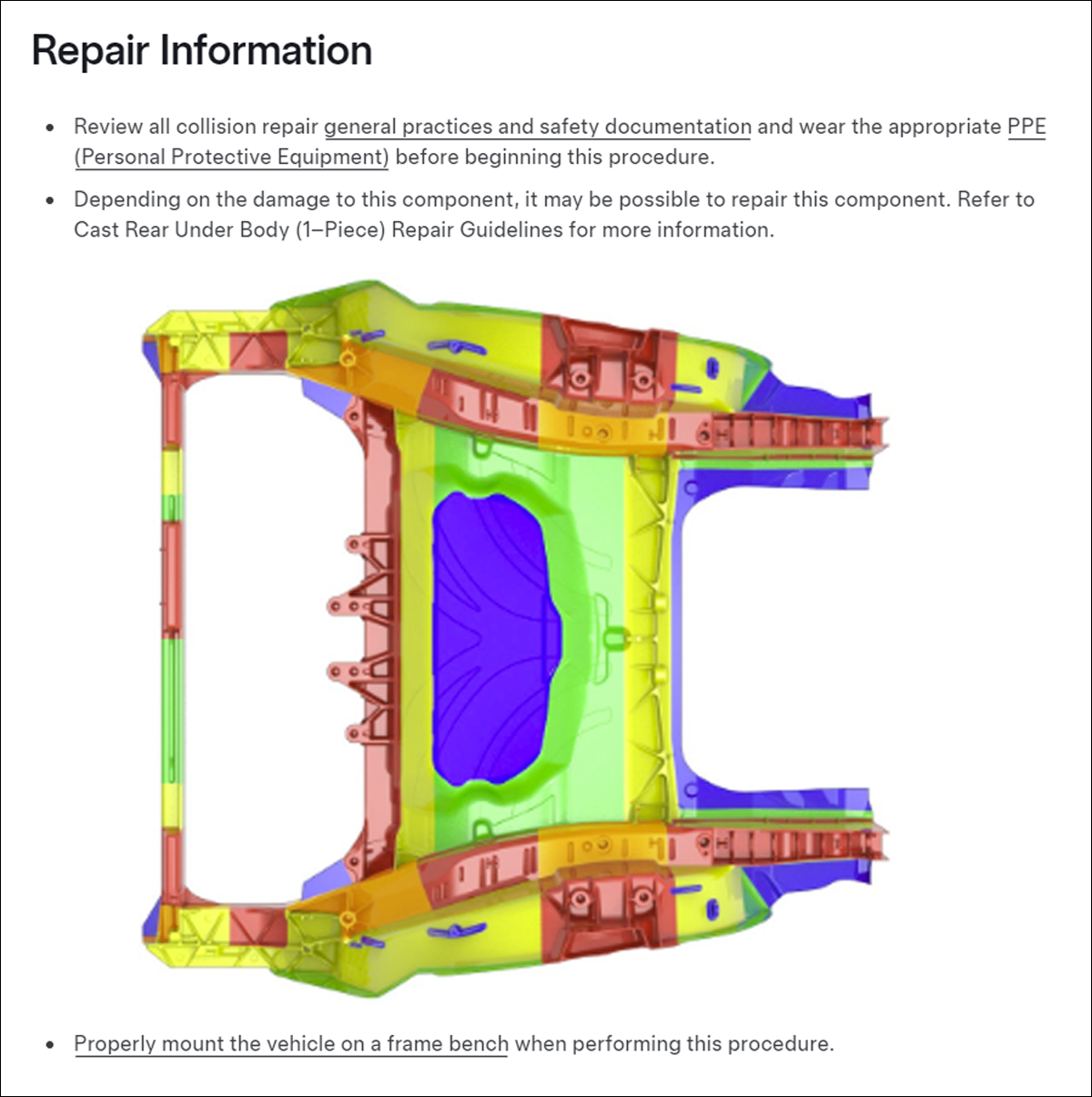
Listen To The Experts
Indeed, if you listen to Tesla itself, you’d know that repairing the brand’s gigacastings isn’t just possible, it’s going to become pretty much routine. The simple fact is that millions of Tesla vehicles have been sold with megacast components, and some of those vehicles will sadly be involved in accidents. While some will be totaled, many won’t be.
There are actually many possibilities repairing large cast components. Tesla has already released repair guides that cover this very topic, and the entire Cybertruck Collision Repair Manual is available online. It’s full of diagrams explaining what repairs are possible on which areas of any given cast component.
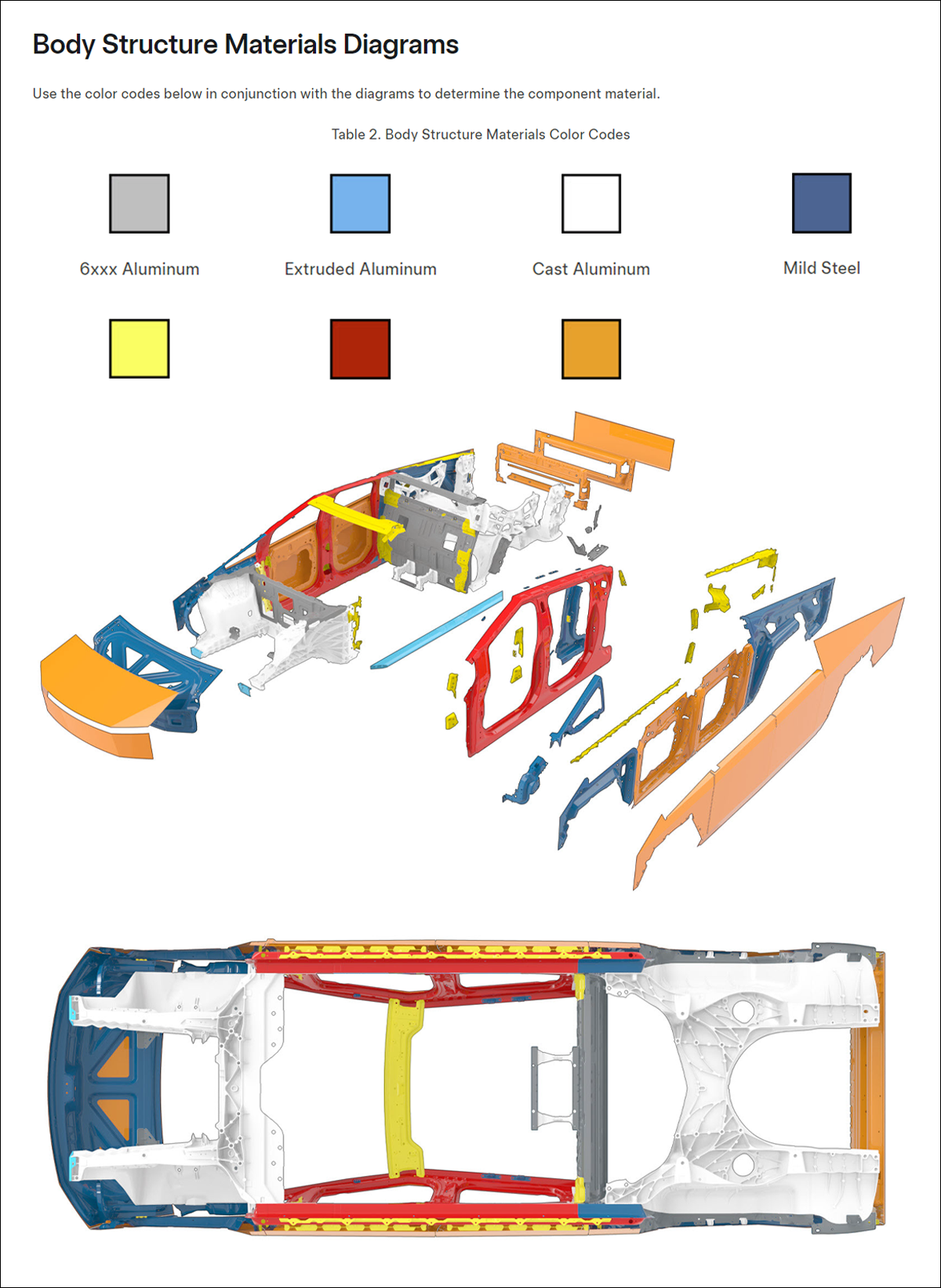
A color-coded system is used to delineate allowable repairs. Blue areas concern protruding tabs on the casting. Areas marked in this color can be welded back on if they have broken off or cracked, while bent tabs can be straightened with cold methods only. Basically, if you can hammer a tab straight, that’s cool. Just don’t use a torch.
In green areas of the casting, damage up to 50 mm (2 inches) can be fixed via welding. For longer cracks or damaged areas, collision repairers should check in with Tesla prior to proceeding. Meanwhile, bent webs in the casting can be similarly straightened out using cold methods only. Broken studs may also be replaced with welding or by using self-tapping double-ended studs.
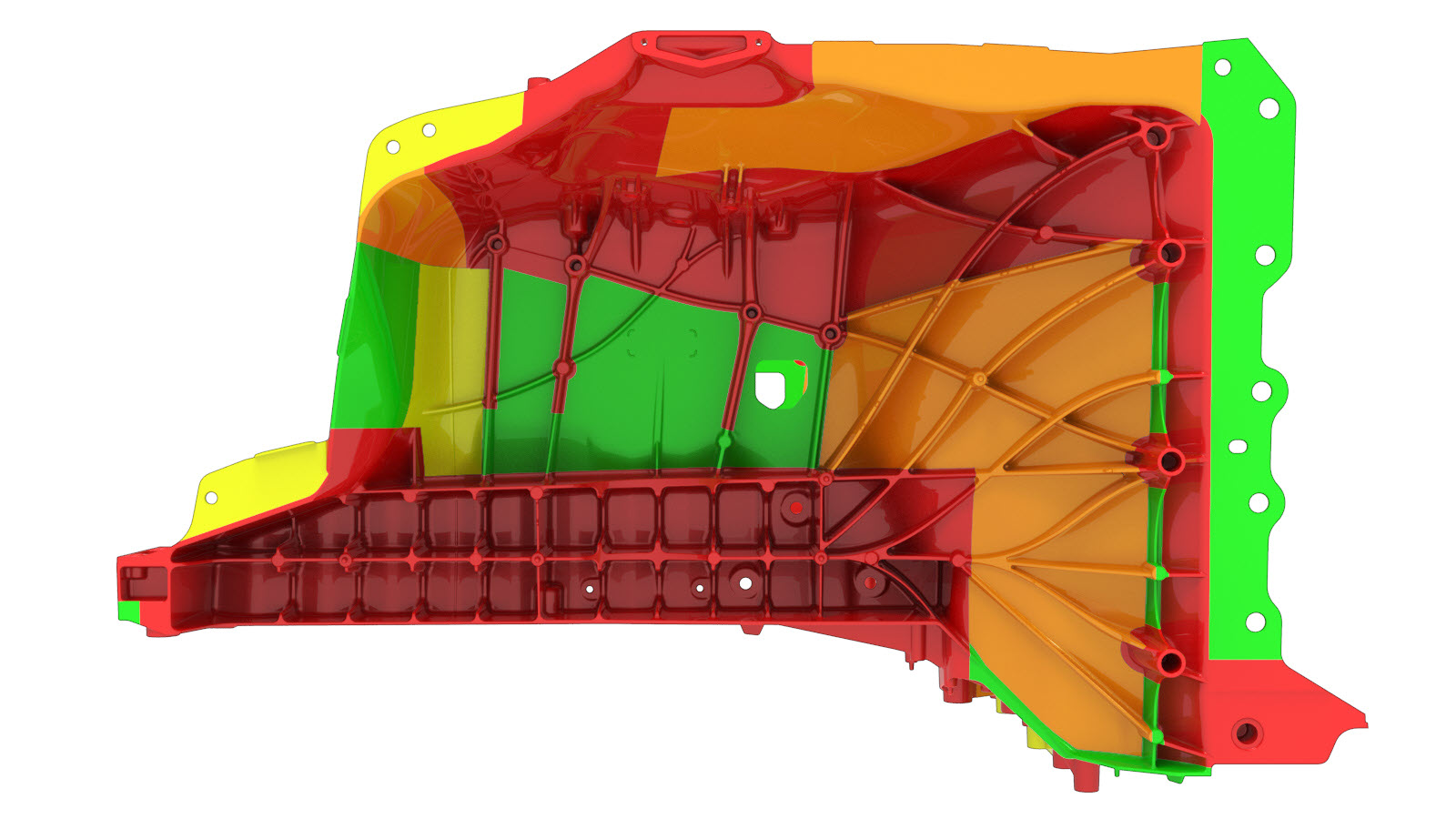
Yellow areas are more delicate. Damage up to 30 mm (1.2 inches) can be simply welded up. Damage from 30 mm to 50 mm (1.2 to 2 inches) can be welded, but a backing plate must be installed. This is done by trimming reinforcement plates to size, and then installing them with structural adhesive either side of the damaged area.

Orange areas allow for welding cracks up to 30 mm (1.2 inches), but reinforcement plates must also be used. Anything over that length requires consulting Tesla’s collision repair experts. Broken studs may still be replaced in these areas, either by welding or with double-ended studs, and bent webs can be straightened with cold working methods.
Red areas, meanwhile, are more delicate. Welding repairs are typically not allowed in these areas, and it’s recommended that repairers contact Tesla directly for assistance in these cases. As for cracks or damage that span multiple colored areas, it’s again recommended the repairer reach out to the automaker before proceeding. In some of these cases, it may be difficult or impossible to safely repair the casting, and replacement might be recommended.
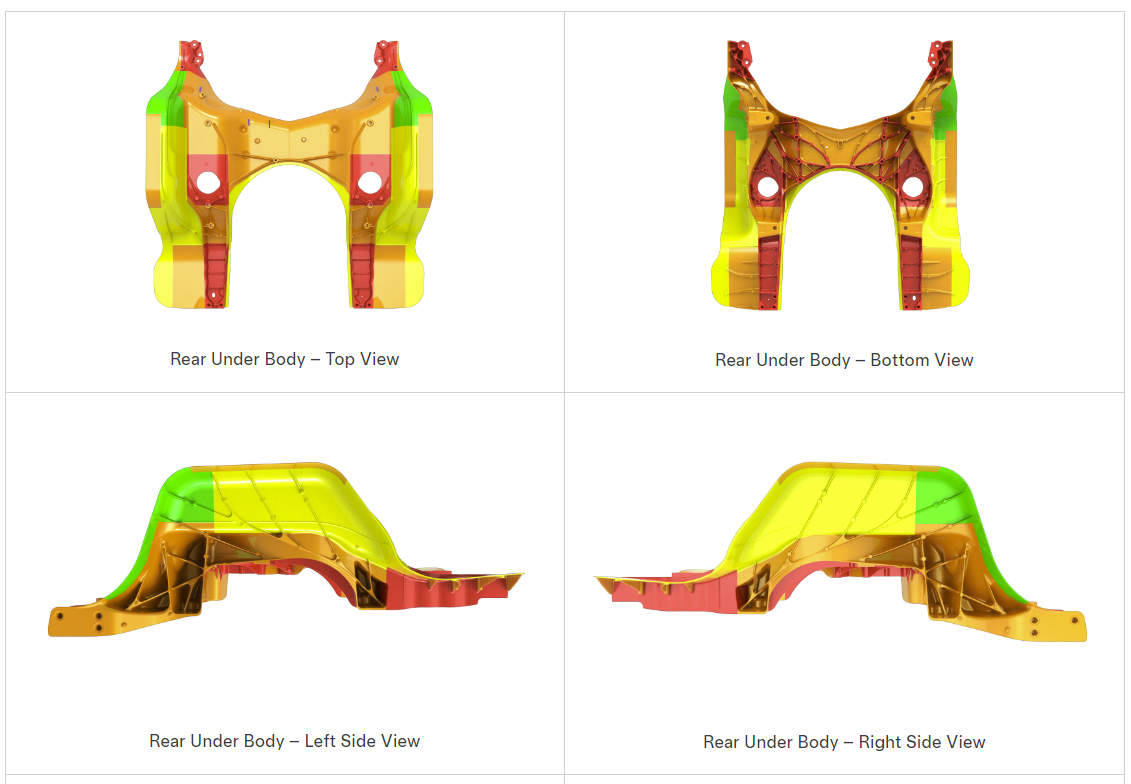
Tesla’s guides are thorough and cover the basics, highlighting precisely which components are made of which materials. It’s trivial to identify cast, stamped steel, stainless steel, or extruded aluminum parts. The EV-maker will even tell you how to weld up cast parts. There’s a useful chart on its website. It recommends MIG welding (aka GMA) for butt joints on cast parts, using ER4145 wire.
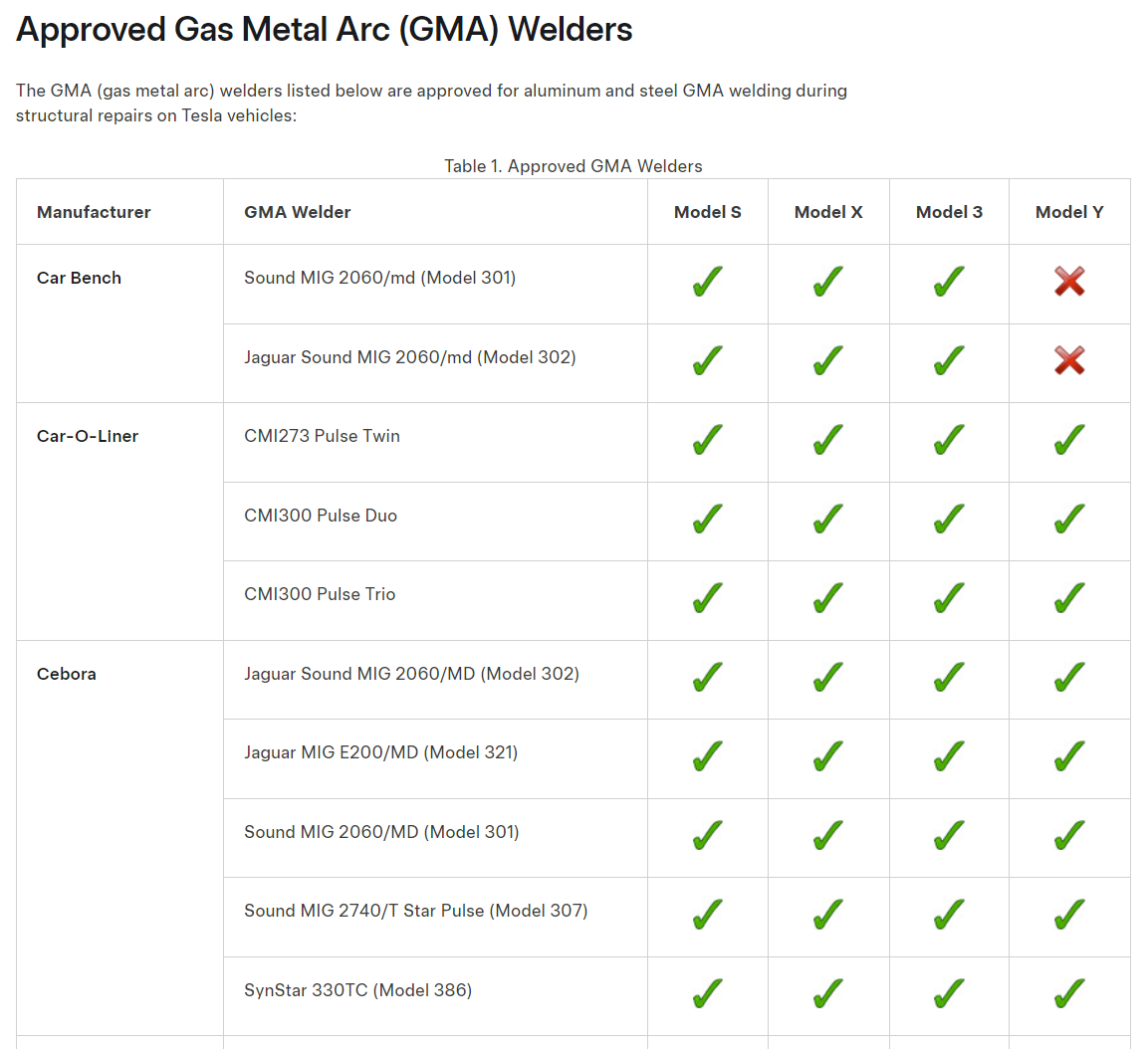
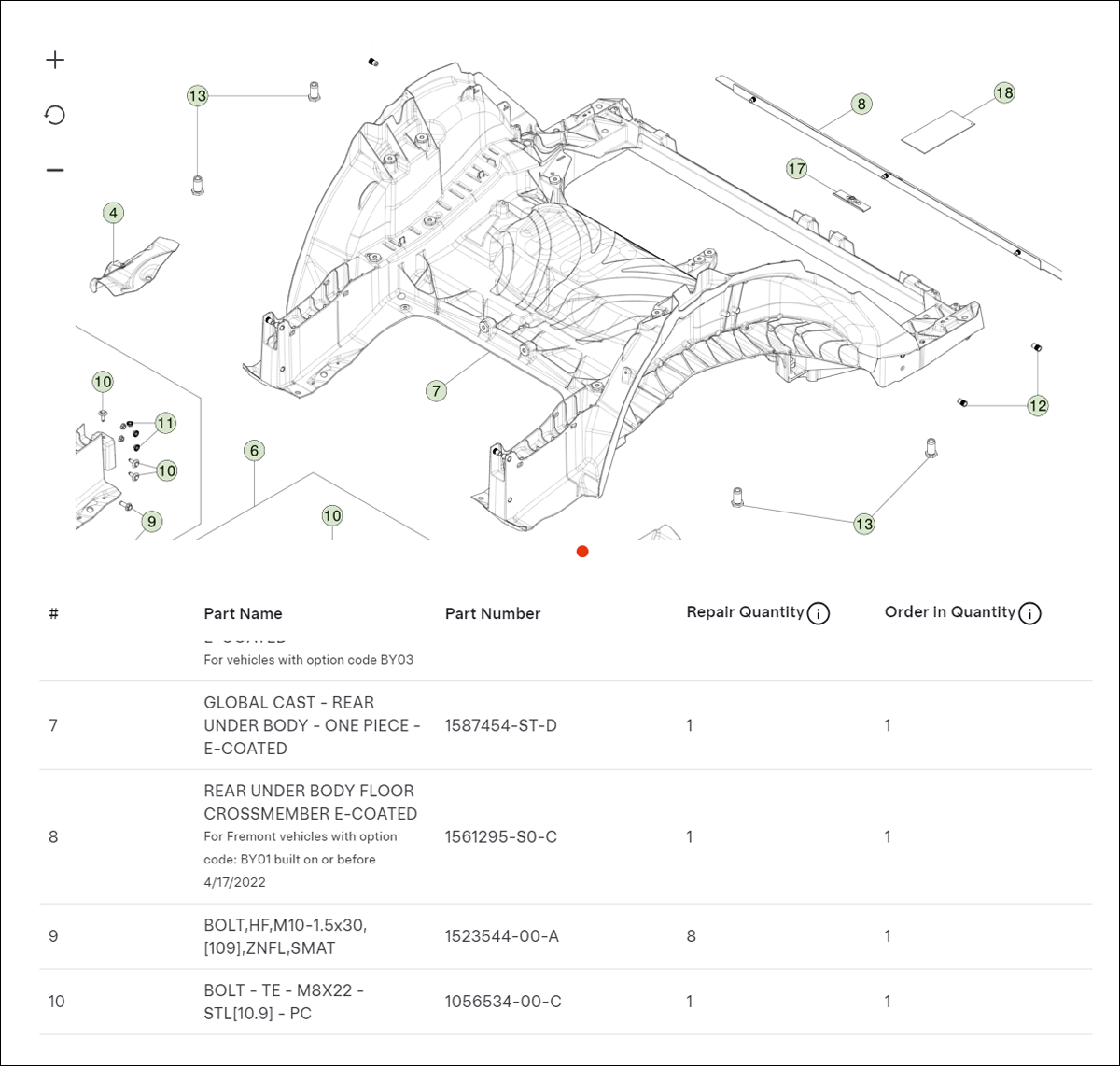
Even in cases where a large cast part can’t be repaired, that’s not necessarily the end for the vehicle. It’s possible to replace the entire casting as a whole part. This may not always be economical, depending on the cost of the casting and the labor involved. However, in some cases, it’s potentially a benefit for vehicles that incorporate gigacastings.
Imagine a conventional unibody vehicle with heavy damage to the steel body at the rear. Cutting the back off the car and welding in a new section would be prohibitively expensive, time consuming, and result in poor structural rigidity. In contrast, a car with a unibody comprised of gigacastings may be able to be repaired by removing the body panels, dropping the rear casting, and installing a fresh cast component in its place. This can be expensive and fussy, at times requiring the removal of rivets, fasteners, or even adhesive bonds between the casting and body panels. Regardless, it can still be a bit simpler than cutting and welding back together parts of a steel unibody.
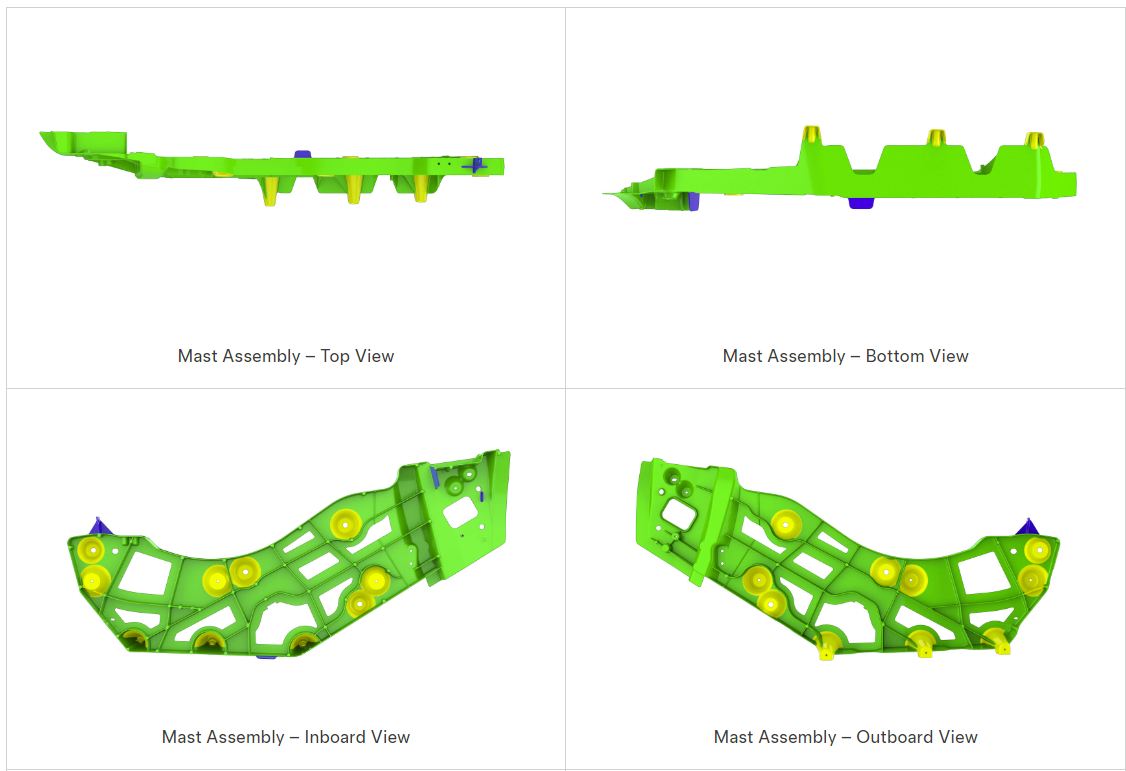
None of this is secret information, and Tesla has published these guides for its vehicles for some time. It’s just not something you come across if you’re not in the collision repair business. Despite this, the idea that gigacast components are “unrepairable” remains a common assumption in the public consciousness. All the while, the collision repair industry is getting on with the business of fixing these vehicles and putting them back out on the road.
Besides, if gigacastings were unrepairable, we’d have heard a great hullaballoo about it by now. Tesla has been using gigacastings in its vehicles for years. If these vehicles were routinely totaled in minor accidents, surely insurance companies would have stopped covering them by now. Thankfully, for millions of Tesla customers, that hasn’t happened.
We can see this has happened by looking up insurance quotes. You can buy a Tesla Model Y tomorrow, and get insurance at entirely favorable rates comparable with any other conventional automobile.
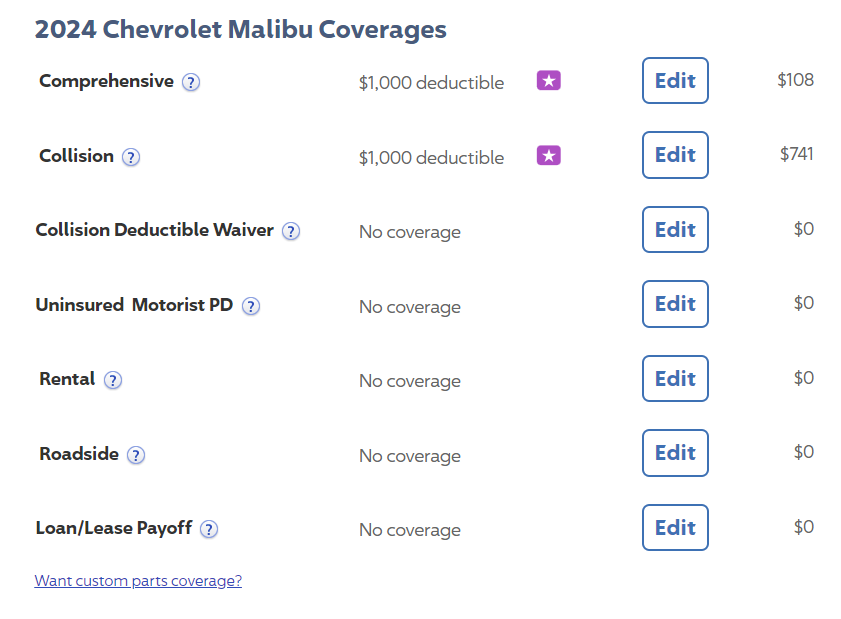
Misconceptions Reign
“A lie can travel halfway around the world before the truth can get its boots on,” goes a common saying often attributed to Winston Churchill or Mark Twain, depending on who you talk to.
In our case, the line that large component castings are unrepairable is passed around regularly in the press and in comment sections across the web. This is typically based on simple notions that monolithic cast parts cannot be welded or otherwise repaired. That assertion actually isn’t true, and neither are the extended assumptions that stem from it.
A cast aluminum welding demonstration. It can be done.
Many cast parts can be welded successfully, regardless of their size. That’s not to say there aren’t challenges – porosity and entrapped gas can cause difficulties, and you need to use the right methods and materials. But the idea that cast parts can’t be welded is totally false. Plus, there are other techniques, like using structural adhesives, which are perfectly valid to use as well.
A great deal of misinformation has come about on the topic of gigacastings because the technology is still new and unfamiliar. Anyone can look at a steel unibody car, or a body-on-frame truck, and understand how it could be repaired. Hammers and dies and simple welding techniques do the work, and we’ve all seen examples of panel beaters at work a million times before.
In contrast, few of us have seen anyone tackle a welding job on a gigantic load-bearing cast part. It’s a job that needs to be done right, of course, and with the right knowledge. Trying to weld a crack in a critical load-bearing area might be very dangerous, for example. But done properly, there’s no reason a properly repaired cast component can’t be perfectly safe in its original application.
Welding cast parts is by no means impossible.
Some owners out there are even trying their hand at their own repairs. YouTuber 519Kustomz was able to weld a fender mounting tab that had snapped off a casting on a recent-model Model Y. Checking the latest Model Y collision repair manual, we can see this area is designated orange and green. In the orange area, it’s only appropriate to weld damage up to 30 mm (1.18 in) and a backing plate should be used. In the green area, it’s only appropriate to weld damage up to 50 mm (2 in). Given the damaged area is longer than 2 inches and spans both areas, it seems like a simple welded repair might not be appropriate in this case.
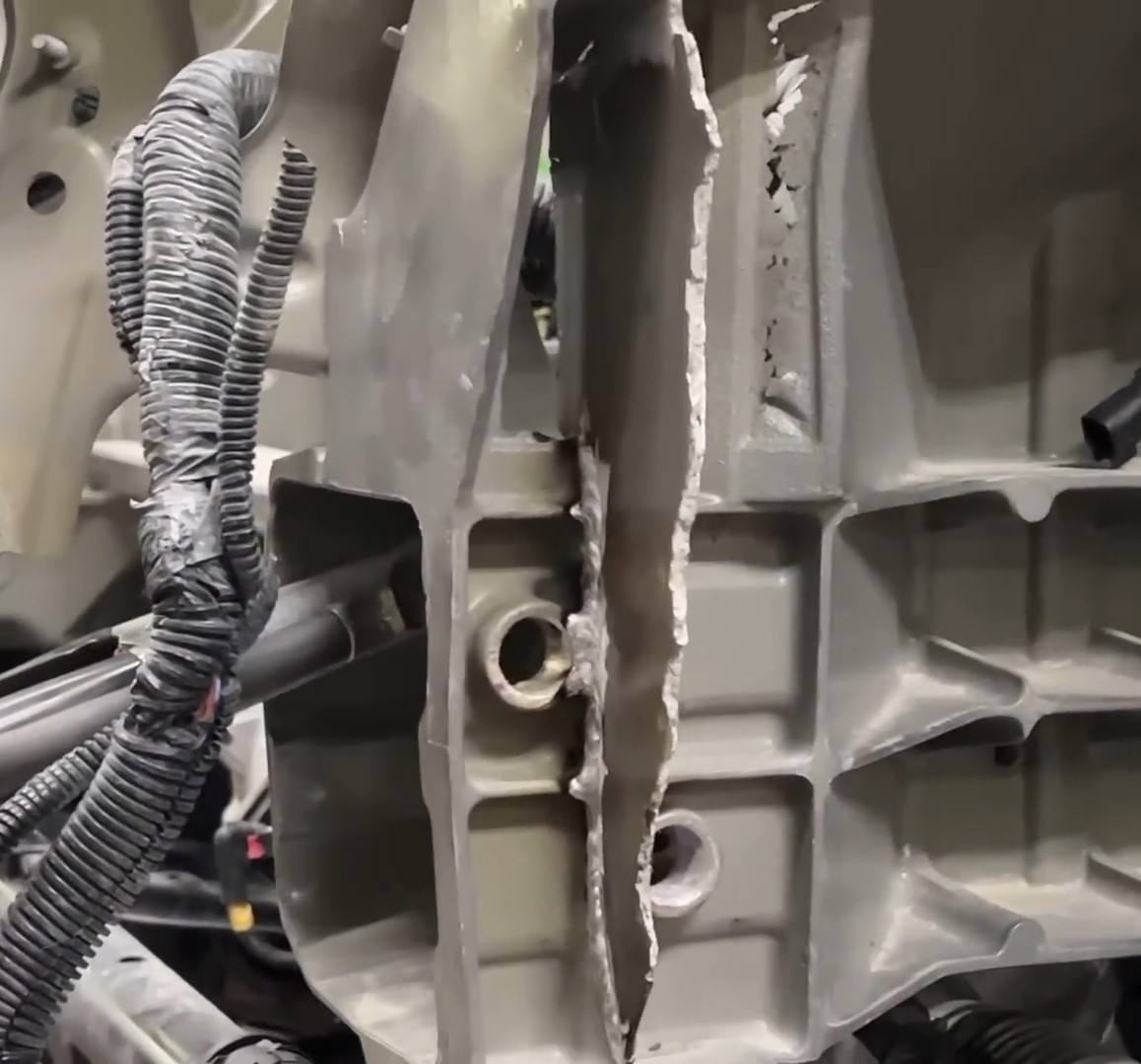
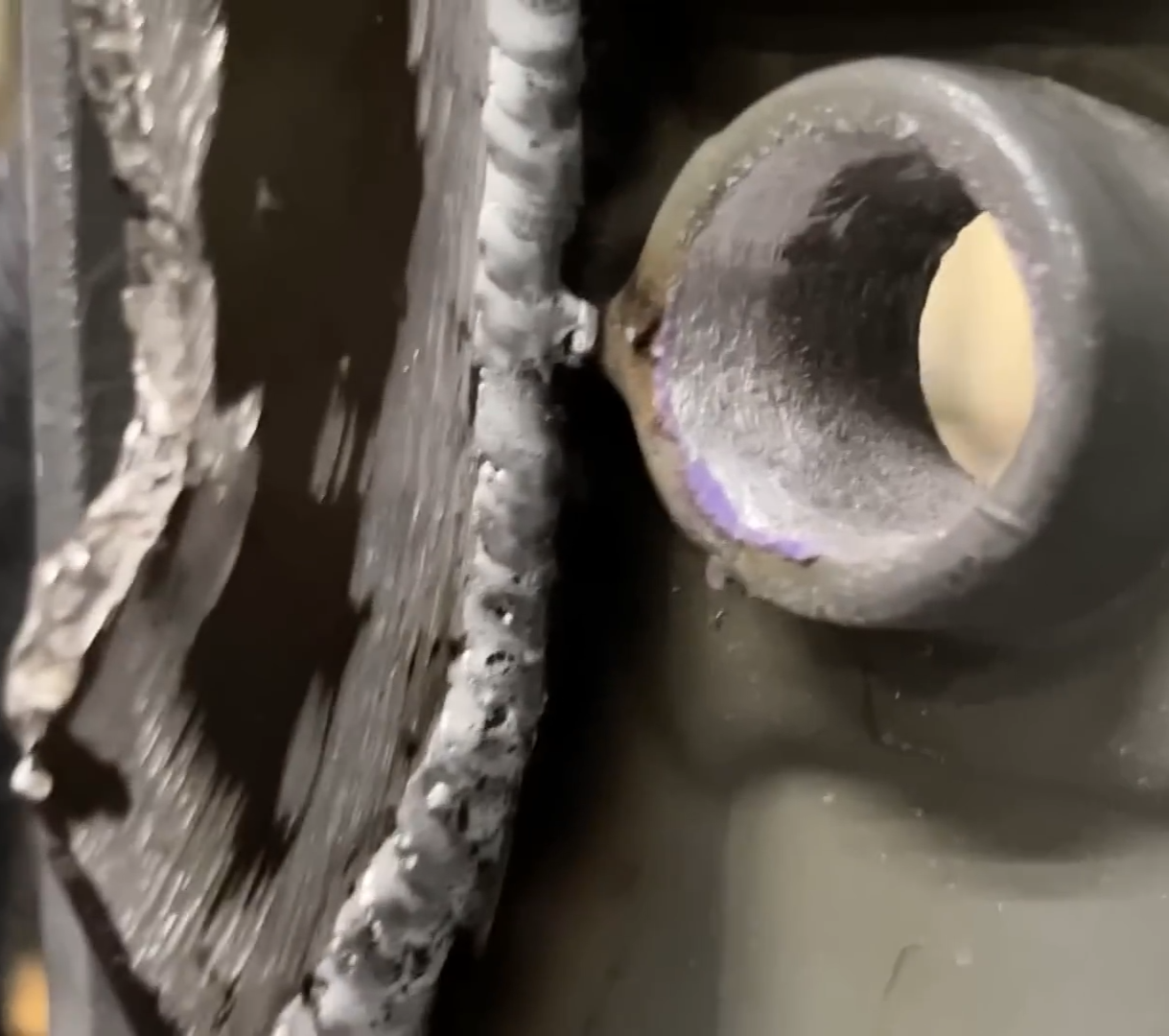
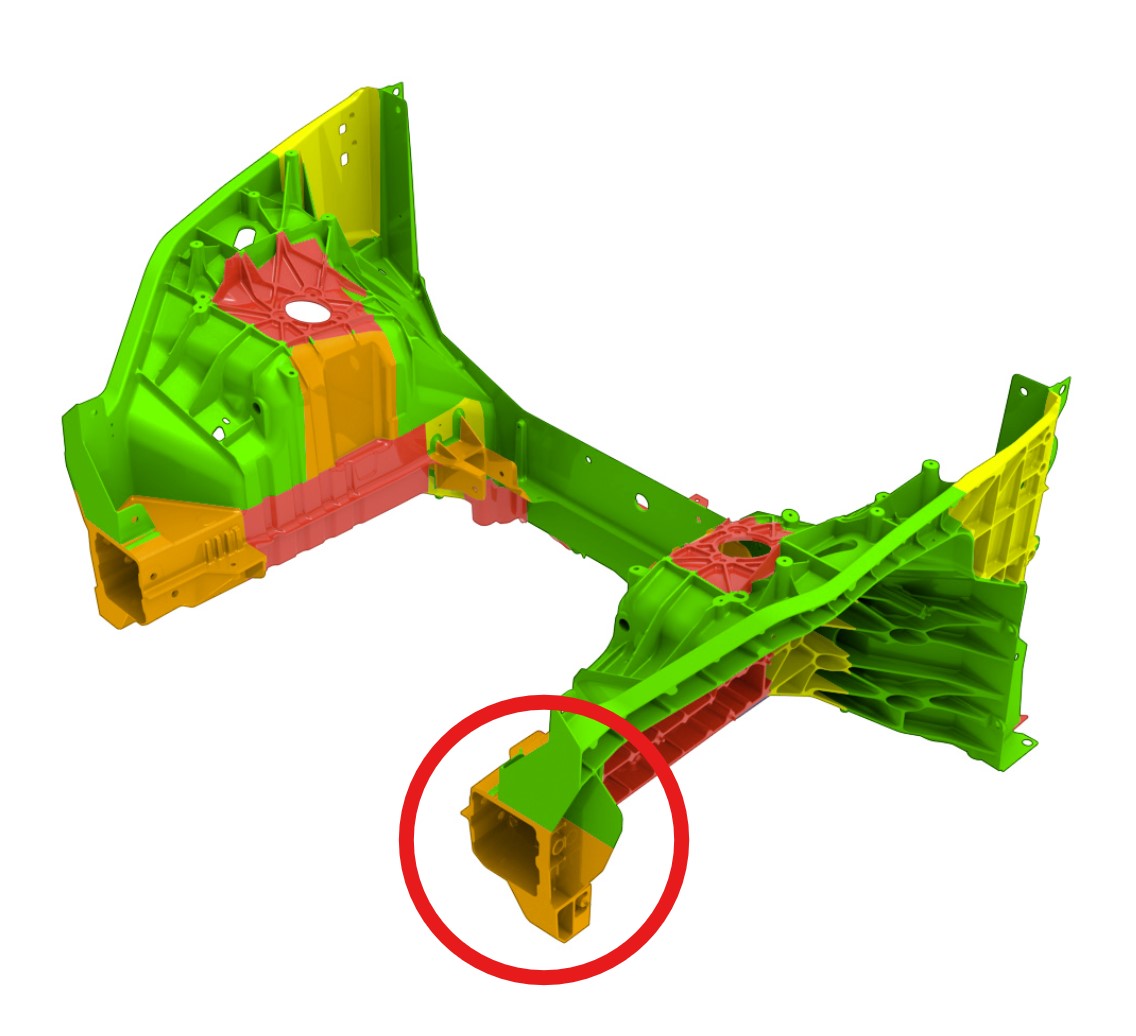
The broken piece appears to be in excess of 2 inches long, so this repair should really only have gone ahead after checking in with Tesla. The owner deemed this fender mounting section to be non-critical, and was able to weld it up regardless. In any case, it should do fine as far as holding the fender on the vehicle is concerned. As for crash worthiness, well, that’s a more complicated manner.
An embarrassing sabotage attempt against Tesla and Giga Press technology
???????? The French Automobile Distribution Federation (FEDA) calls on the government to assess the risks and to take measures against Giga Casting "dangers" for the environment and families
The letter begins… pic.twitter.com/UvyaITKRfQ
— Luca Greco (@lucagrecoita) October 4, 2023
It’s also worth considering the possible vested interests involved in the narrative. For example, last year saw the French Automobile Distribution Federation (FEDA) make a report calling on the government to respond to the “dangers” of gigacasting. The coalition of French auto distributors called for the government to regulate gigacasting. Its prime demand was that cars should be able to be repaired after being damaged by impacts at up to 60 km/h (37 mph).
The FEDA press release hit all the usual talking points. It suggested that gigacast cars would be far too costly to repair and that there could be negative consequences for the environment, as “entire blocks” of vehicles need to be replaced. There is also the oft-repeated statement that insurance costs would skyrocket. It quoted a repair costing €12,154 ($13,545 USD) for 6.5 days of work on a Peugeot 2008, versus a “comparable” repair for a gigacast vehicle of €15,402 ($17,165 USD) for 11 days of work. More expensive, certainly, but not exactly a horrifying difference.
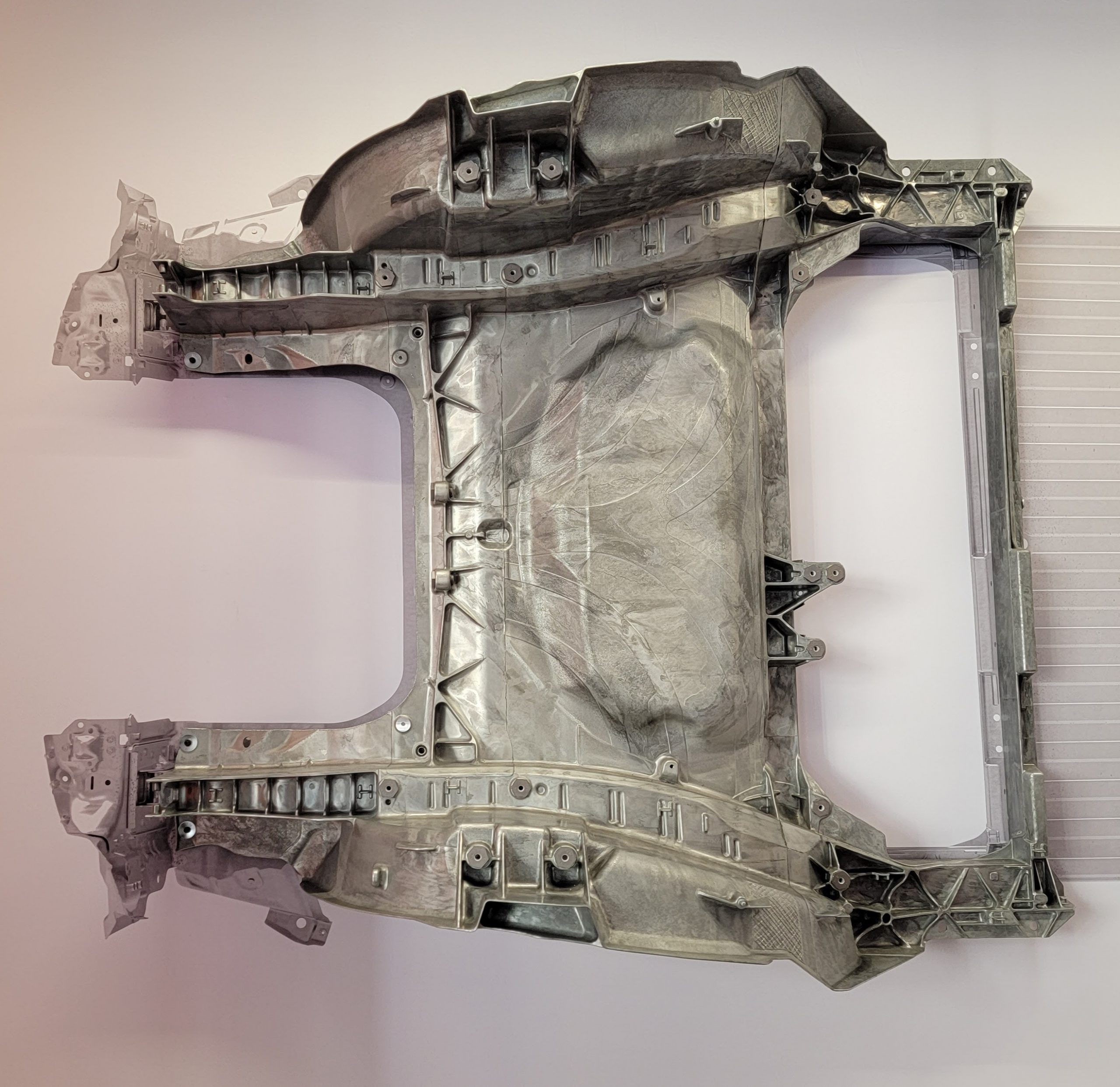
The bottom line is this: Gigacastings and manufacturers that employ them are not some big scary boogie monster out to ruin the automotive industry. These vehicles can survive crashes. They’re subject to the same crash tests as everything else on the road. And they do remain repairable after crashes. Obviously, it is possible to total a car with gigacast components—but you need not worry that they are excessively fragile compared to any other vehicle.
Ultimately, the key is to look at what the industry is doing—not what people are saying. Understand what’s really going on, dismiss fearmongering, and know the truth. My opinion as an engineer is that gigacastings — especially if used in the right places — are fine. Don’t believe the hype that says otherwise.
Image credits: Tesla, Evolve EV Specialists via YouTube Screenshot, Votpuske via CC BY-SA 4.0
I’m fascinated by the French Automobile Distribution Federation letter.
Repair a Peugot 308 in 6.5 days for $13,545 = $260/hr. (assuming 8hr/day)
Repair gigacast car in 11 days for $17,165 = $195/hr.
So the Peugot is faster overall but requires proportionally more expensive parts, more highly skilled labor, or both. Interesting.
Possible, yes. Affordable, no.
-You talk about panel beaters, but when was the last time that an insurance-funded body shop beat out a custom steel panel to fix a car? 1960?
-Highly skilled welders can weld and patch structural cast aluminum. But where does one find those for anything less than an arm and a leg? Welding is a diminishing skill, and skilled welding even more so.
For reference, just link to all of Mercedes’ articles looking for someone to fix the rust on her (now sold) BMW. The one old shop that was initially interested closed down before she got it done. And that BMW rust wouldn’t even take a particularly advanced welder!
Also: “get insurance at entirely favorable rates comparable with any other conventional automobile.” then you show an example of Tesla comprehensive coverage ($1377) costing almost double (1.9x) another conventional automobile ($741).
Replying to myself to add.
This is good article, thank you for writing it! I really do appreciate the amount of thought and content that you put into it!
This is good Autopian!
They are also the main reason why insuring electric cars is very expensive, and getting more so.
Horror stories on French TV about electric car insurance costs are one of the reasons why sales have slowed.
This is the exact article i’d been hoping someone would write.Well done Autopian!
inb4 duct tape and bondo
A-hem “duct tape”?
Shirley you intended to write “speed tape” 😉
I’ve been wondering about this exact subject for a while now, so thanks very much Lewin! Much appreciated. 🙂
Thank you! Many hours well spent.
Great read Lewin. Thanks so much for the education!
You’re welcome!