Large component casting, known as megacasting in some rare cases and “gigacasting” in Tesla parlance, has become a controversial technology in the automotive industry. It’s touted as a grand way to speed up manufacturing and slash costs. It’s also decried for supposedly making cars unrepairable after an accident. But how true is that?
Concerns around “gigacastings” are widespread; we’ve covered them in these very pages, too. The common belief is that large castings are fundamentally impossible to repair. The fear is that if a vehicle is involved in an accident, it could be an instant write-off if parts of the cast structure are damaged. It’s understandable that this would cause some concerns for car buyers—nobody wants a fragile, easily damaged car, after all! Are these assertions valid, though?


Fundamentally, there are a lot of assumptions involved here. The truth is that castings aren’t magic items that can never be fixed. As such, cars with large cast structures are not “uninsurable” or prone to being totaled in the slightest collision. Today, we’re going to explore the reality of the matter, getting into the nitty-gritty of how Tesla gigacastings are actually repaired. Let’s dive in!
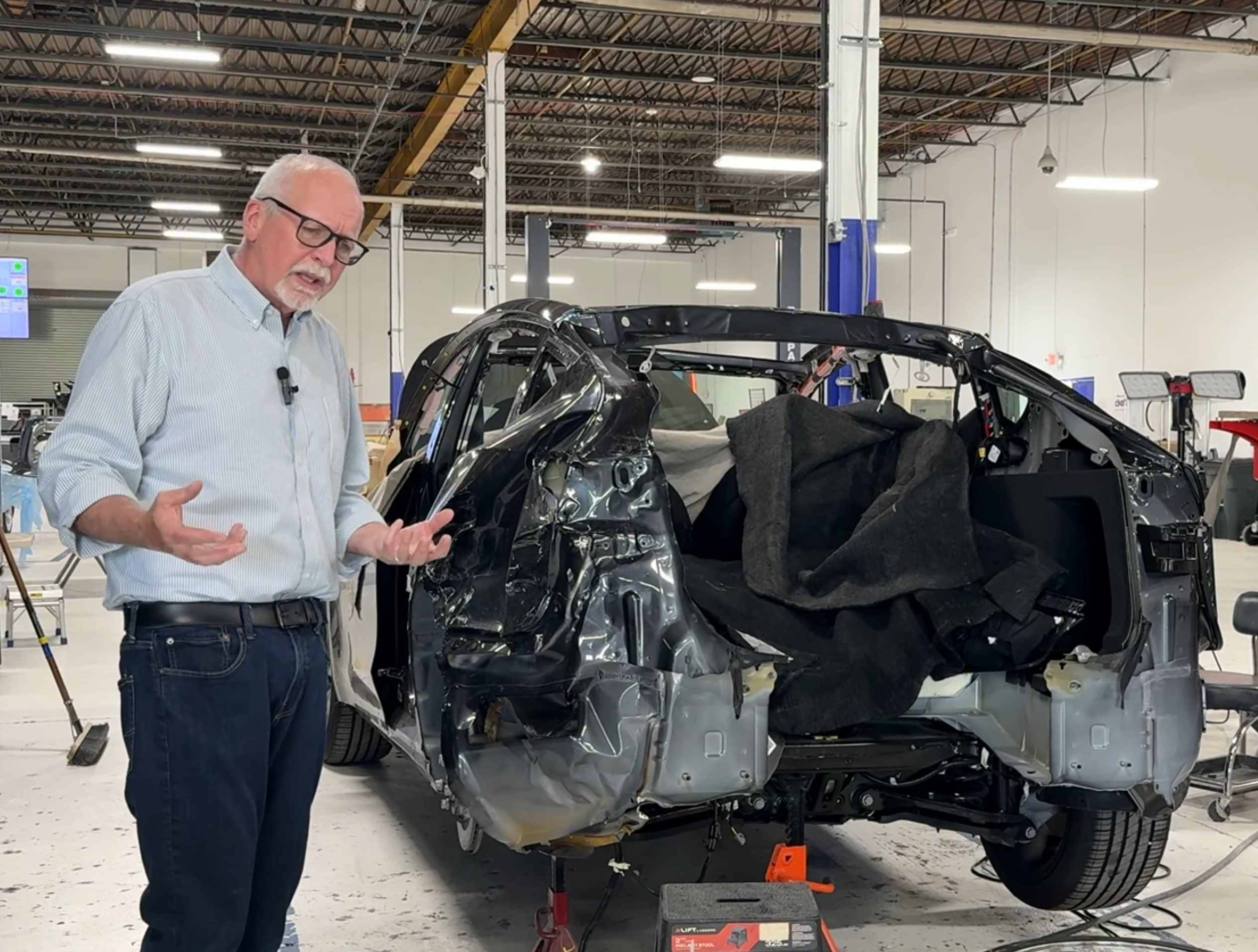
Get The Real Information
We all know why Tesla loves gigacasting. Replacing multiple smaller components with a single, large casting drastically slashes the number of manufacturing operations required to build a vehicle, with massive savings in cost and complexity. But we’re so often told that this comes at a cost. Some auto news outlets will tell you gigacastings can’t be repaired, and the idea has strongly taken root. You’ll find offhand mentions of repair issues in gigacastings in many articles on the topic. But while repair for large castings can be tricky, it is by no means impossible.
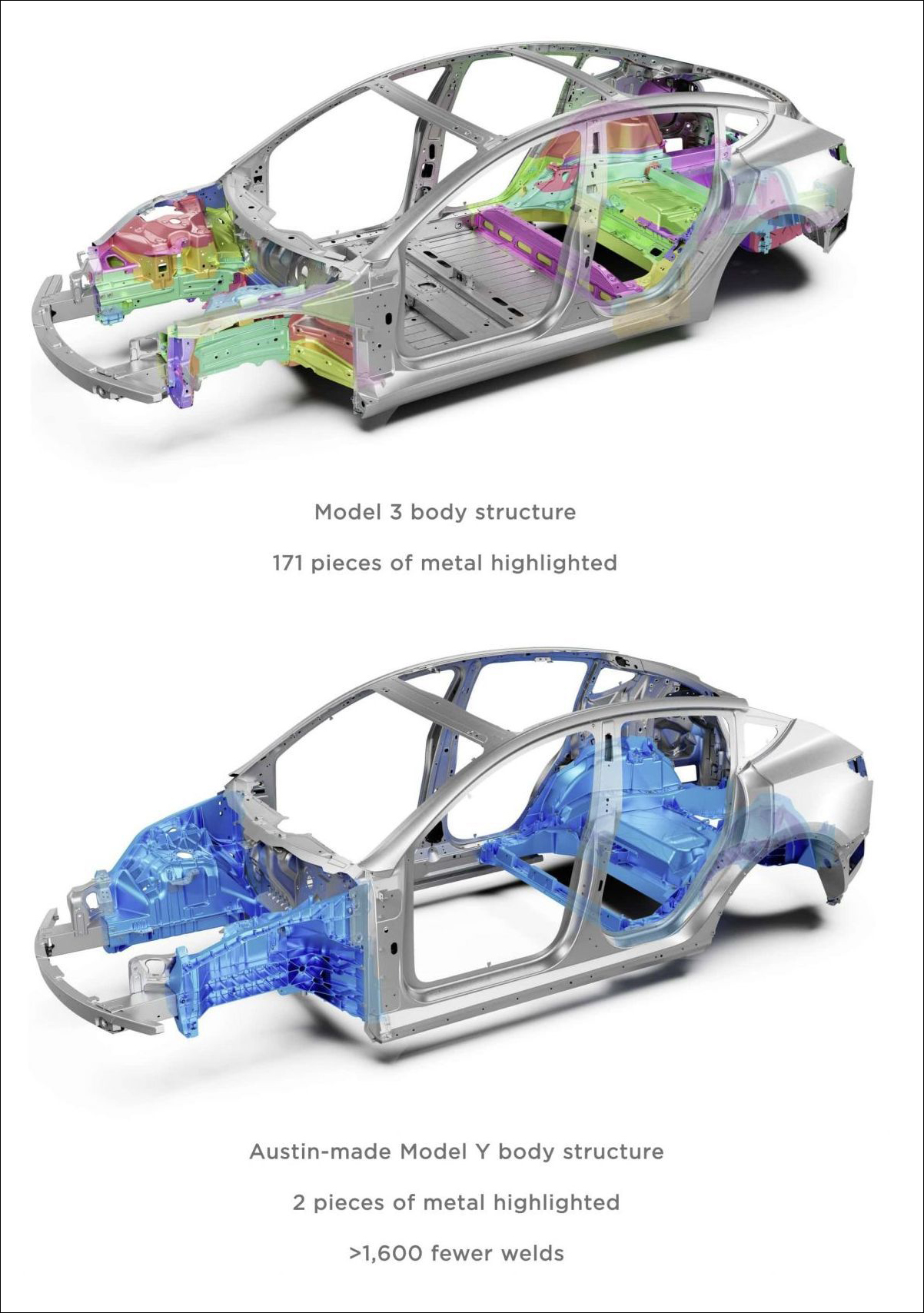
You have to go to experienced sources to get real information on this topic. A great place to start is looking at what actual crash repair experts are saying, like those at Evolve EV Experts. In May this year, CEO John Sweigart put out a video on this very topic, aiming to clear up some misconceptions around repairing vehicles using megacast body components.
The video concerns a crashed 2024 Tesla Model Y. This model uses a large casting to form the rear structure of the vehicle. The vehicle can be seen to have significant damage to the driver’s-side rear quarter panel and wheel well, with the sheet metal crumpled and bent. It’s clear the vehicle took a sizable hit to the rear end.
“There’s some myths about what happens with gigacastings,” says Sweigart. “The important thing is you can repair a lot of the gigacasting.” He notes that when large component castings first hit the automotive market, replacement of the casting was the only viable option for fixing damaged parts. However, things have changed in recent years. “Since then, there’s lots of repair methods that have been developed,” he explains.
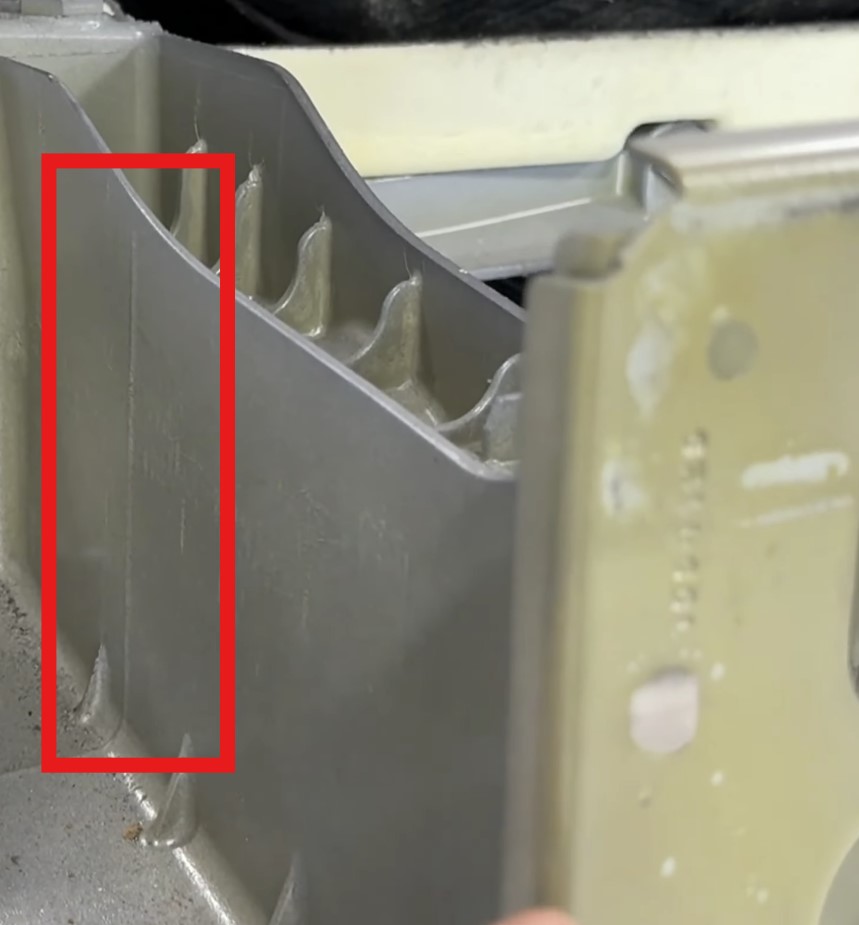
The fact is, there are numerous bonding and welding techniques that are perfectly applicable to these castings. They’re quite different to anything you might use on a vehicle made of stamped steel sections, but that doesn’t make them any less valid. Sweigart points this out, highlighting a rear section of the casting, where there is an obvious vertical line in the metal. “If this was hit and fractured, we have the option to literally cut this off and attach a new piece of cast aluminum on this spot,” he explains. “It would be done with rivets and structural adhesive and a backing plate on the join.”
It’s worth noting that castings are more likely to fracture rather than bend or crumple like sheet metal parts, as Sweigart explains with regards to the Model Y. “This may crack or move a little bit, but in most cases, this will just shatter or break,” he explains about the rear crash structure. However, despite the hard hit to the rear, this example has fared well.
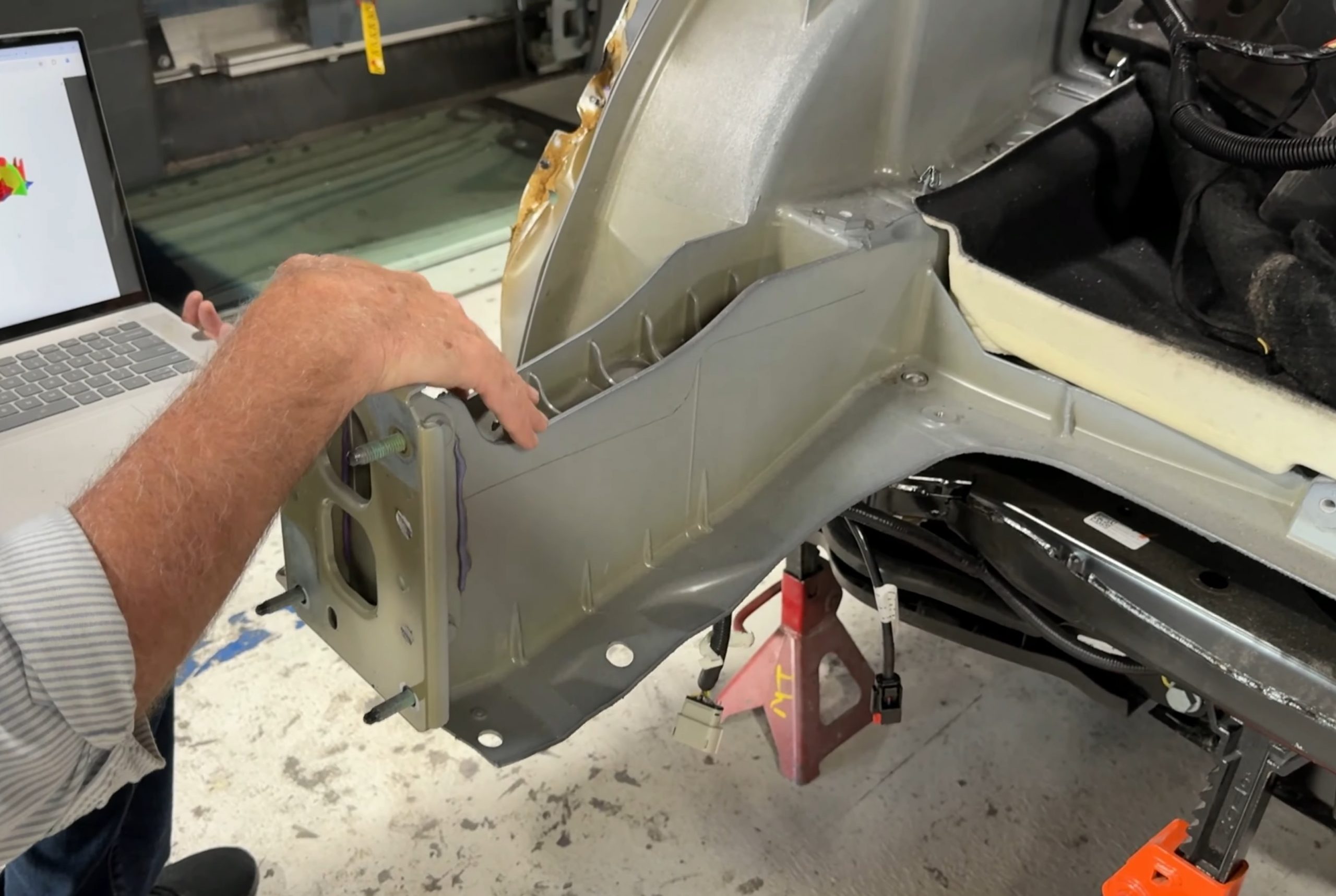
“We have measured this vehicle … all of these control points are in the right position in space.” Moving in closer, the casting seems virtually untouched. “This is the area of impact, this is probably the most important area, and as you can see, there’s really no issues,” he notes.
That’s not to say a casting that looks right at a glance is still fine. Cracks are quite possible in cast aluminum parts, and can weaken a structure significantly. However, that doesn’t mean they’re a death sentence for the whole cast part. They can often be welded to restore the part’s integrity.
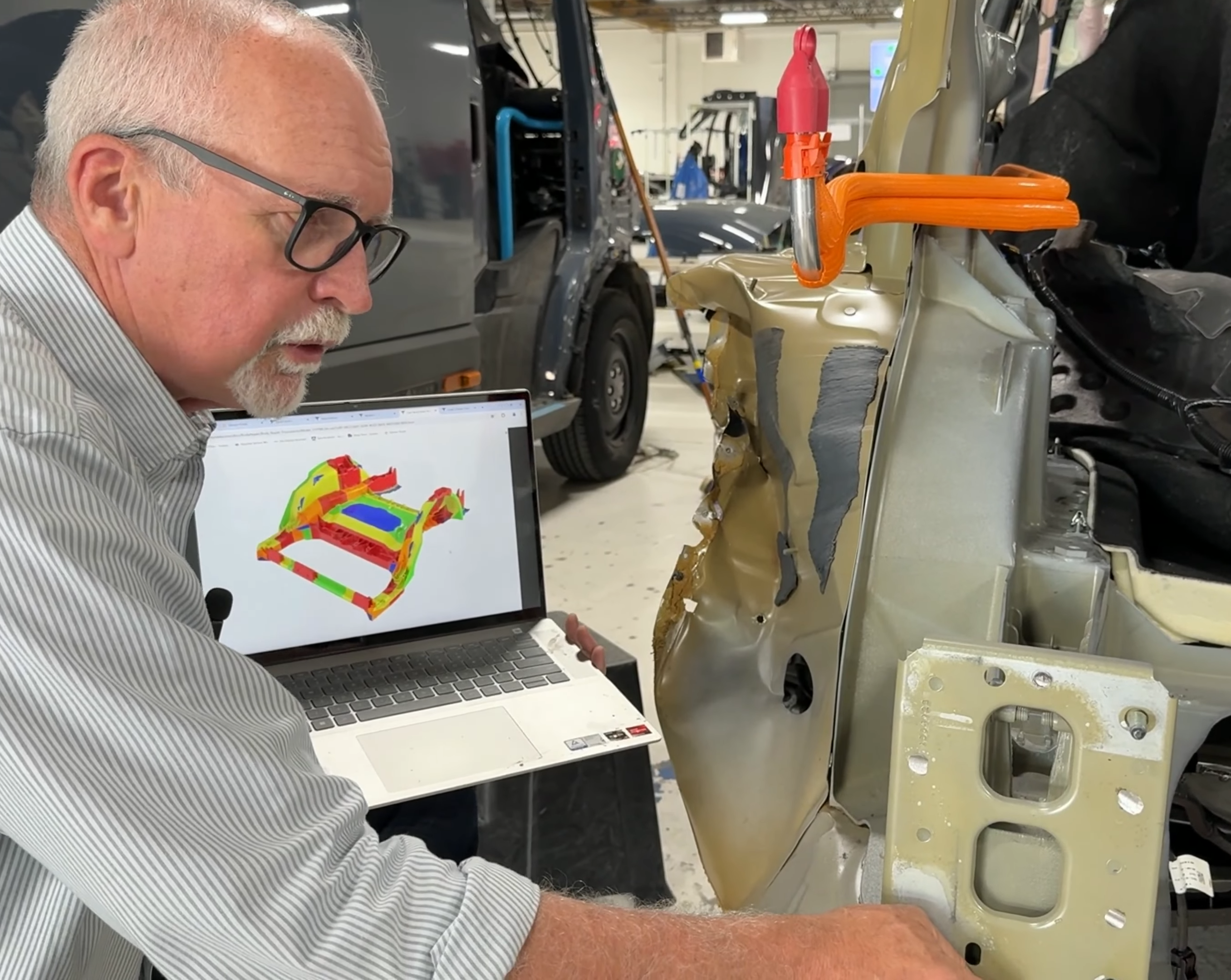
“If a crack is less than 50 mm long (~2 inches), you can weld it up in some of these areas.” says Swiegert, pointing to a digital model of a Model Y rear structure. “In some cases, depending on the zone, you can weld a crack that’s up to 30mm (1.2 inches), but you might have to put a backing plate behind it for support.” He’s referring to a map of the casting that shows what areas can and can’t be repaired in various ways. Where did Sweigart get that model? Why, from Tesla itself!
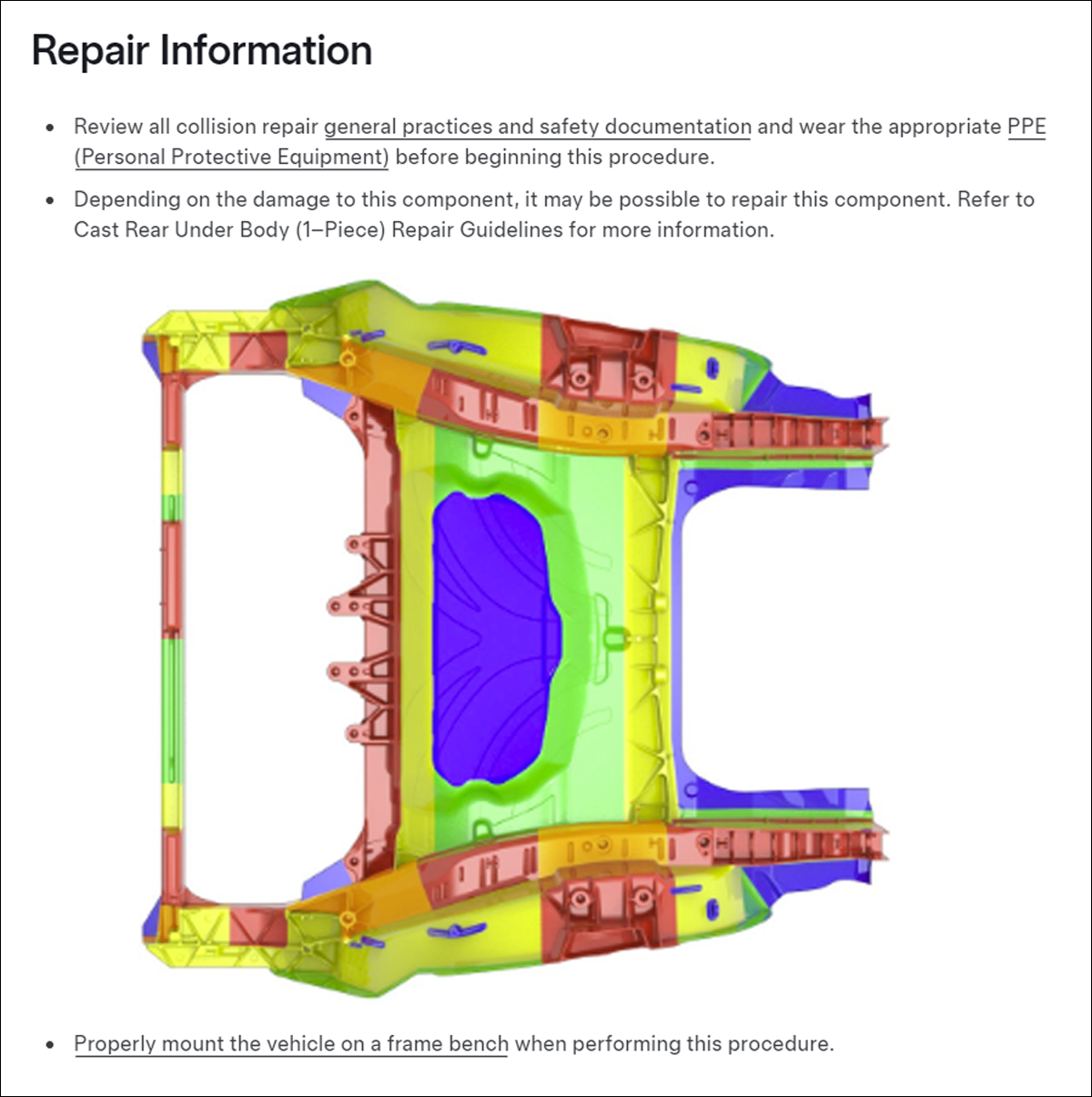
Listen To The Experts
Indeed, if you listen to Tesla itself, you’d know that repairing the brand’s gigacastings isn’t just possible, it’s going to become pretty much routine. The simple fact is that millions of Tesla vehicles have been sold with megacast components, and some of those vehicles will sadly be involved in accidents. While some will be totaled, many won’t be.
There are actually many possibilities repairing large cast components. Tesla has already released repair guides that cover this very topic, and the entire Cybertruck Collision Repair Manual is available online. It’s full of diagrams explaining what repairs are possible on which areas of any given cast component.
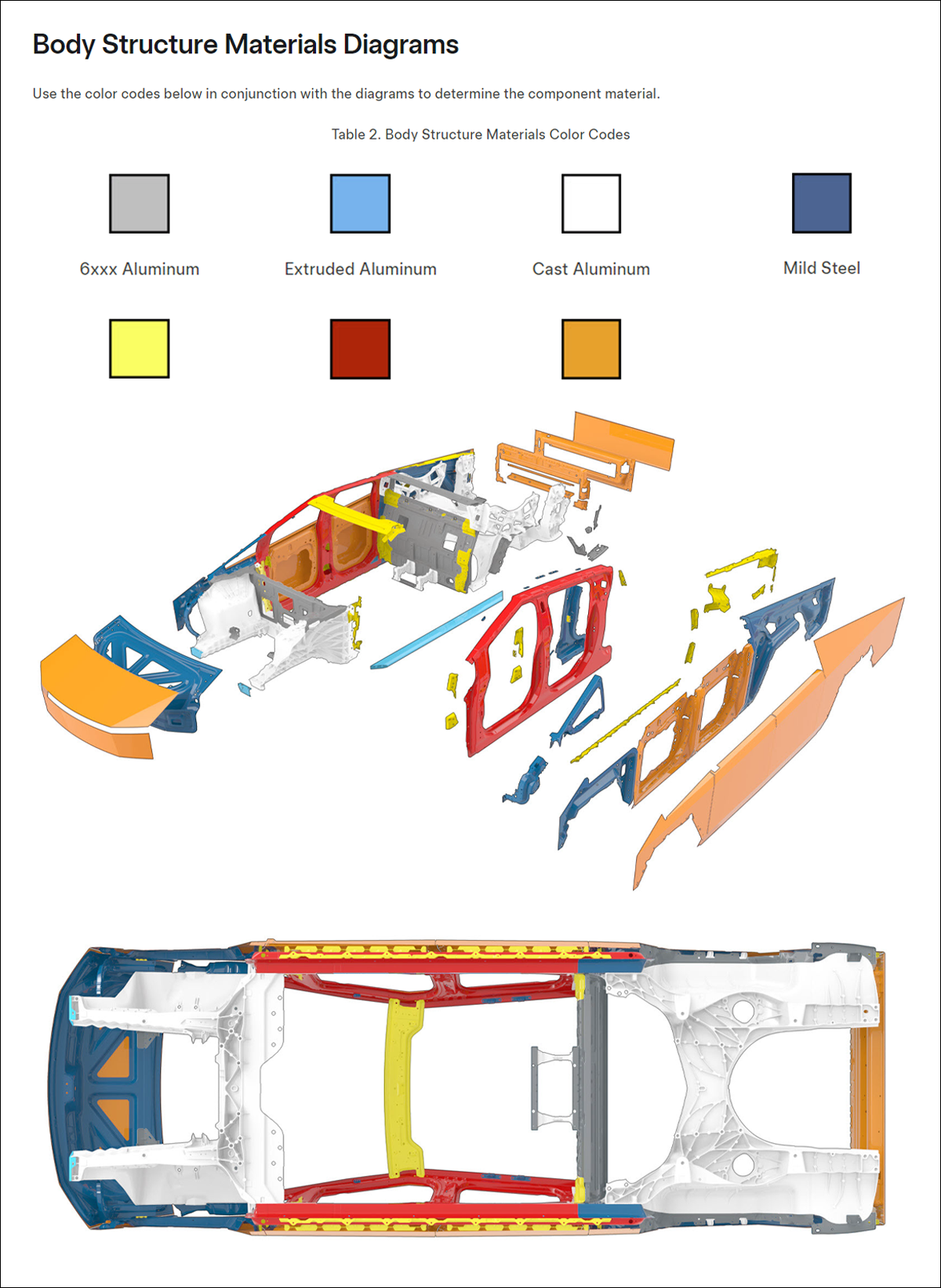
A color-coded system is used to delineate allowable repairs. Blue areas concern protruding tabs on the casting. Areas marked in this color can be welded back on if they have broken off or cracked, while bent tabs can be straightened with cold methods only. Basically, if you can hammer a tab straight, that’s cool. Just don’t use a torch.
In green areas of the casting, damage up to 50 mm (2 inches) can be fixed via welding. For longer cracks or damaged areas, collision repairers should check in with Tesla prior to proceeding. Meanwhile, bent webs in the casting can be similarly straightened out using cold methods only. Broken studs may also be replaced with welding or by using self-tapping double-ended studs.
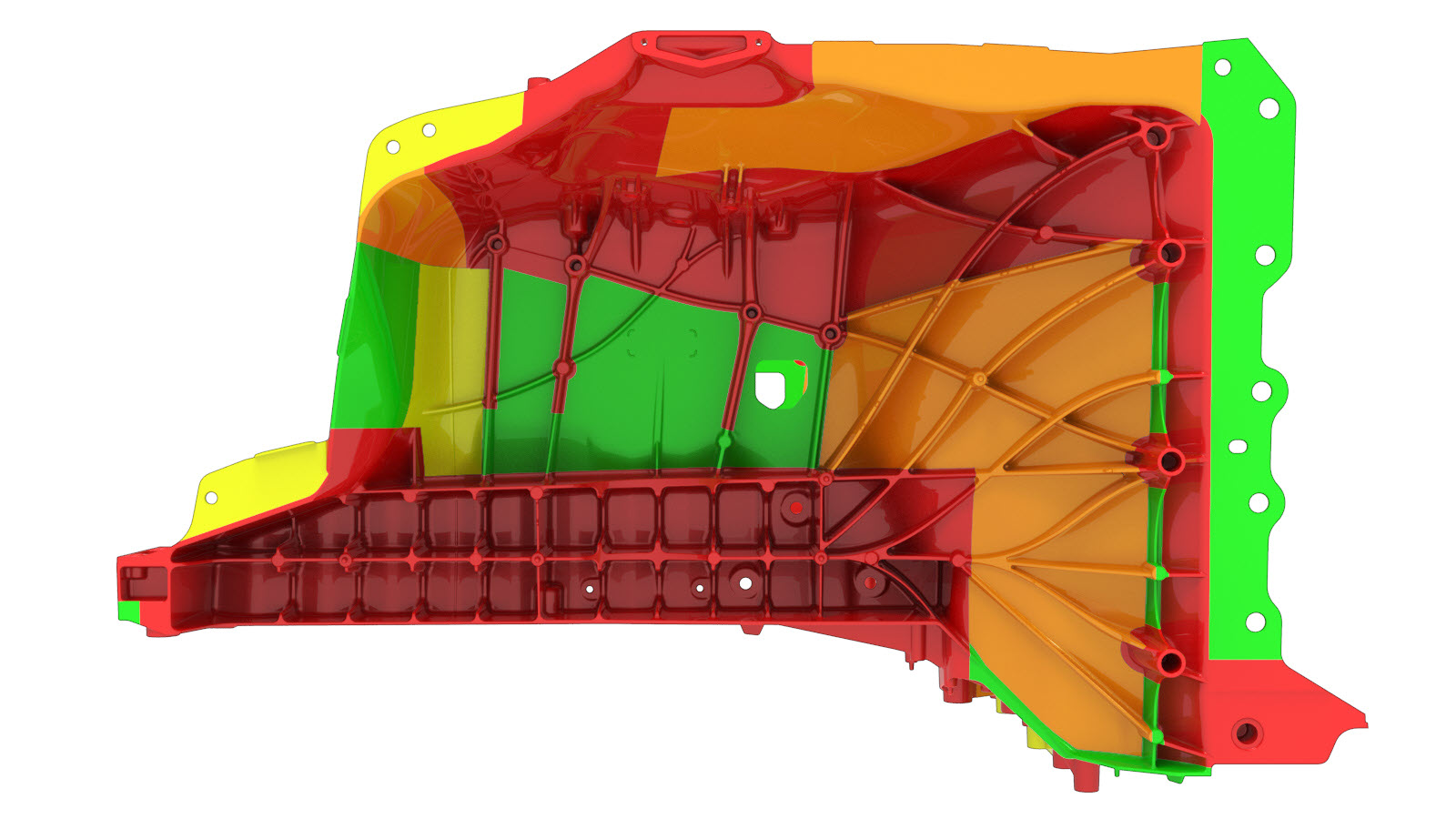
Yellow areas are more delicate. Damage up to 30 mm (1.2 inches) can be simply welded up. Damage from 30 mm to 50 mm (1.2 to 2 inches) can be welded, but a backing plate must be installed. This is done by trimming reinforcement plates to size, and then installing them with structural adhesive either side of the damaged area.

Orange areas allow for welding cracks up to 30 mm (1.2 inches), but reinforcement plates must also be used. Anything over that length requires consulting Tesla’s collision repair experts. Broken studs may still be replaced in these areas, either by welding or with double-ended studs, and bent webs can be straightened with cold working methods.
Red areas, meanwhile, are more delicate. Welding repairs are typically not allowed in these areas, and it’s recommended that repairers contact Tesla directly for assistance in these cases. As for cracks or damage that span multiple colored areas, it’s again recommended the repairer reach out to the automaker before proceeding. In some of these cases, it may be difficult or impossible to safely repair the casting, and replacement might be recommended.
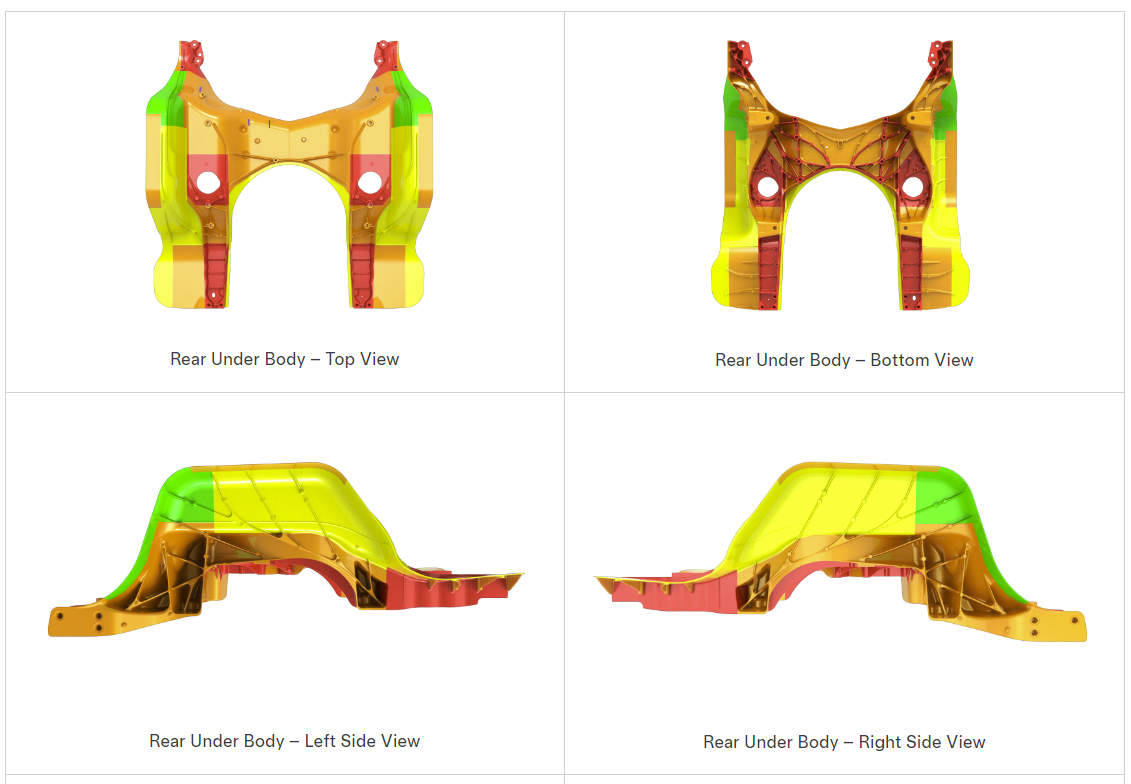
Tesla’s guides are thorough and cover the basics, highlighting precisely which components are made of which materials. It’s trivial to identify cast, stamped steel, stainless steel, or extruded aluminum parts. The EV-maker will even tell you how to weld up cast parts. There’s a useful chart on its website. It recommends MIG welding (aka GMA) for butt joints on cast parts, using ER4145 wire.
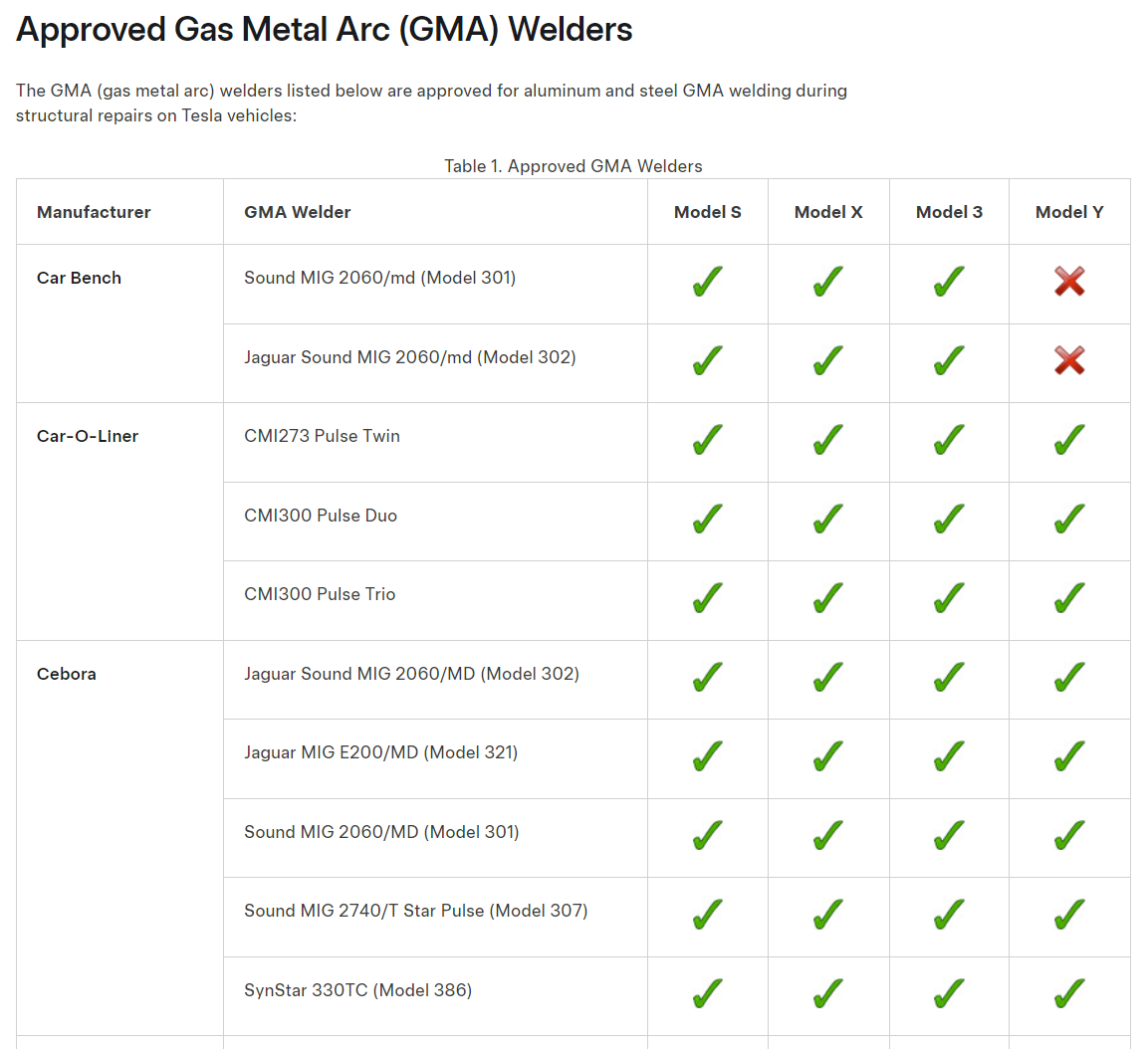
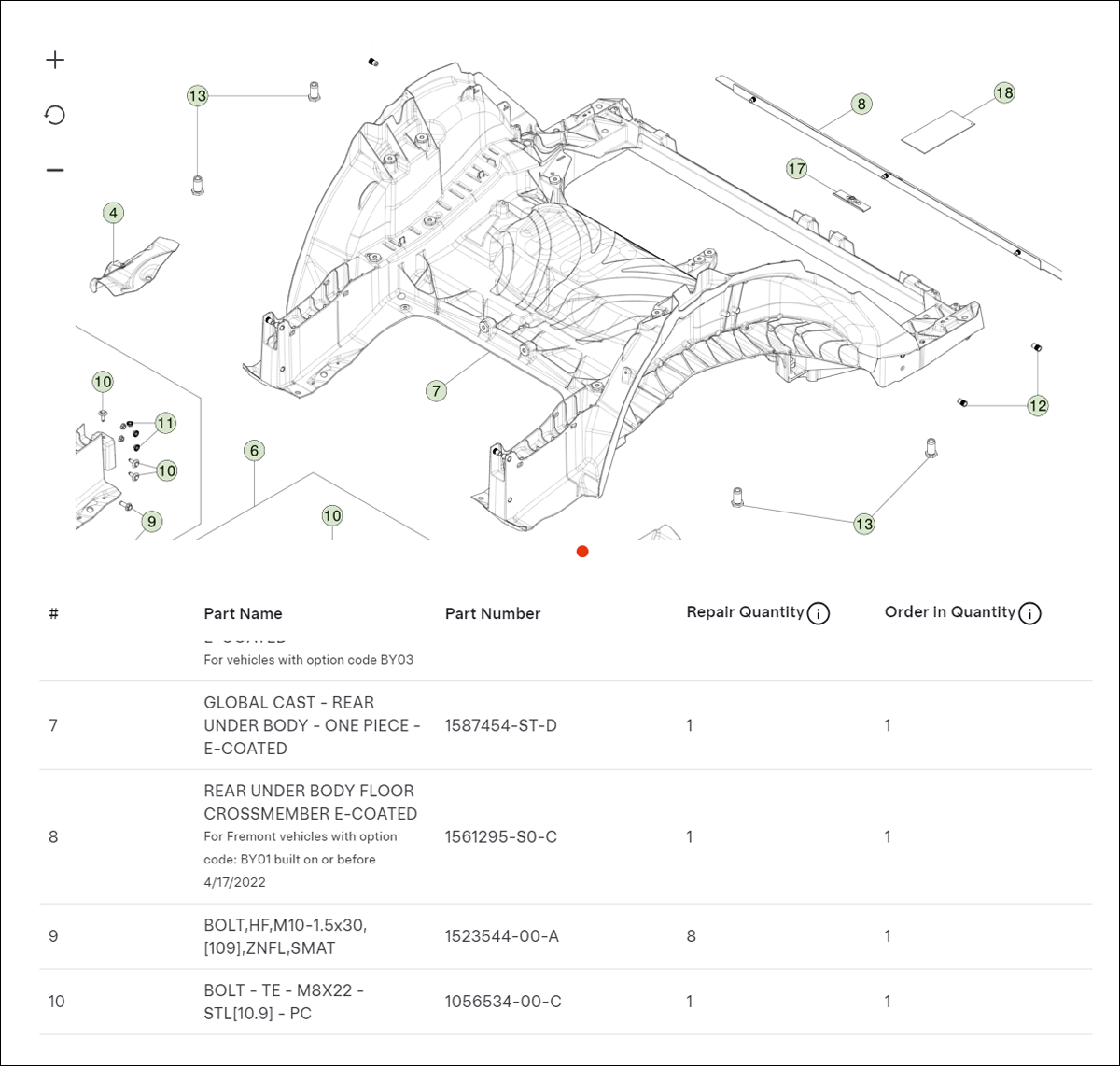
Even in cases where a large cast part can’t be repaired, that’s not necessarily the end for the vehicle. It’s possible to replace the entire casting as a whole part. This may not always be economical, depending on the cost of the casting and the labor involved. However, in some cases, it’s potentially a benefit for vehicles that incorporate gigacastings.
Imagine a conventional unibody vehicle with heavy damage to the steel body at the rear. Cutting the back off the car and welding in a new section would be prohibitively expensive, time consuming, and result in poor structural rigidity. In contrast, a car with a unibody comprised of gigacastings may be able to be repaired by removing the body panels, dropping the rear casting, and installing a fresh cast component in its place. This can be expensive and fussy, at times requiring the removal of rivets, fasteners, or even adhesive bonds between the casting and body panels. Regardless, it can still be a bit simpler than cutting and welding back together parts of a steel unibody.
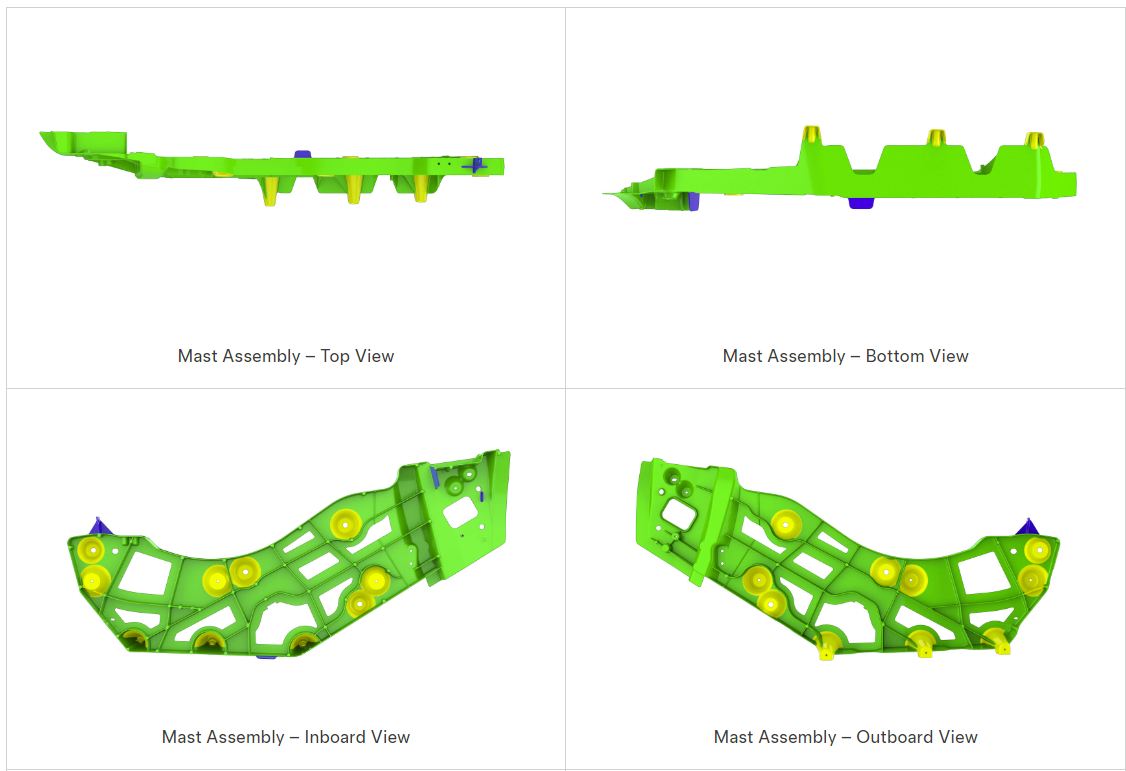
None of this is secret information, and Tesla has published these guides for its vehicles for some time. It’s just not something you come across if you’re not in the collision repair business. Despite this, the idea that gigacast components are “unrepairable” remains a common assumption in the public consciousness. All the while, the collision repair industry is getting on with the business of fixing these vehicles and putting them back out on the road.
Besides, if gigacastings were unrepairable, we’d have heard a great hullaballoo about it by now. Tesla has been using gigacastings in its vehicles for years. If these vehicles were routinely totaled in minor accidents, surely insurance companies would have stopped covering them by now. Thankfully, for millions of Tesla customers, that hasn’t happened.
We can see this has happened by looking up insurance quotes. You can buy a Tesla Model Y tomorrow, and get insurance at entirely favorable rates comparable with any other conventional automobile.
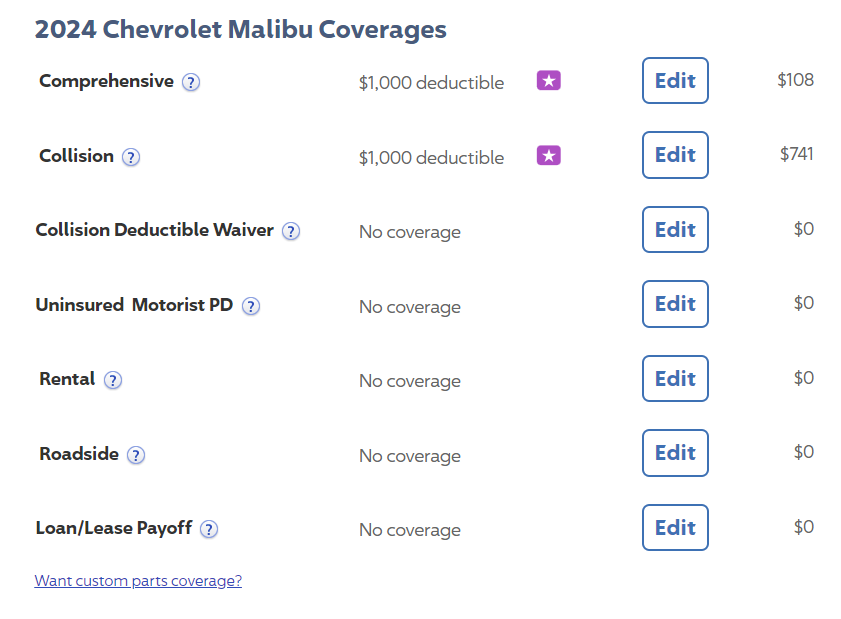
Misconceptions Reign
“A lie can travel halfway around the world before the truth can get its boots on,” goes a common saying often attributed to Winston Churchill or Mark Twain, depending on who you talk to.
In our case, the line that large component castings are unrepairable is passed around regularly in the press and in comment sections across the web. This is typically based on simple notions that monolithic cast parts cannot be welded or otherwise repaired. That assertion actually isn’t true, and neither are the extended assumptions that stem from it.
A cast aluminum welding demonstration. It can be done.
Many cast parts can be welded successfully, regardless of their size. That’s not to say there aren’t challenges – porosity and entrapped gas can cause difficulties, and you need to use the right methods and materials. But the idea that cast parts can’t be welded is totally false. Plus, there are other techniques, like using structural adhesives, which are perfectly valid to use as well.
A great deal of misinformation has come about on the topic of gigacastings because the technology is still new and unfamiliar. Anyone can look at a steel unibody car, or a body-on-frame truck, and understand how it could be repaired. Hammers and dies and simple welding techniques do the work, and we’ve all seen examples of panel beaters at work a million times before.
In contrast, few of us have seen anyone tackle a welding job on a gigantic load-bearing cast part. It’s a job that needs to be done right, of course, and with the right knowledge. Trying to weld a crack in a critical load-bearing area might be very dangerous, for example. But done properly, there’s no reason a properly repaired cast component can’t be perfectly safe in its original application.
Welding cast parts is by no means impossible.
Some owners out there are even trying their hand at their own repairs. YouTuber 519Kustomz was able to weld a fender mounting tab that had snapped off a casting on a recent-model Model Y. Checking the latest Model Y collision repair manual, we can see this area is designated orange and green. In the orange area, it’s only appropriate to weld damage up to 30 mm (1.18 in) and a backing plate should be used. In the green area, it’s only appropriate to weld damage up to 50 mm (2 in). Given the damaged area is longer than 2 inches and spans both areas, it seems like a simple welded repair might not be appropriate in this case.
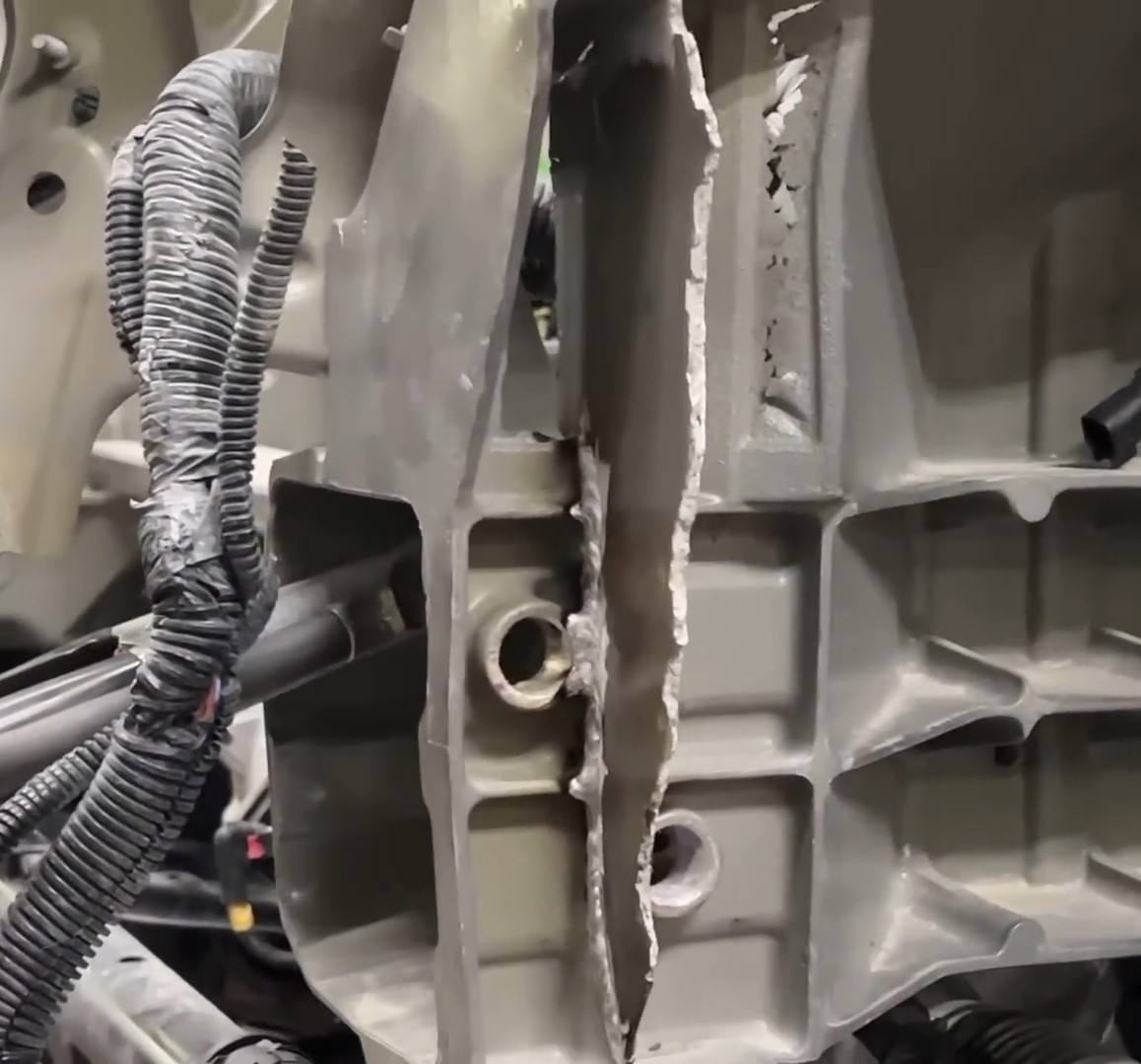
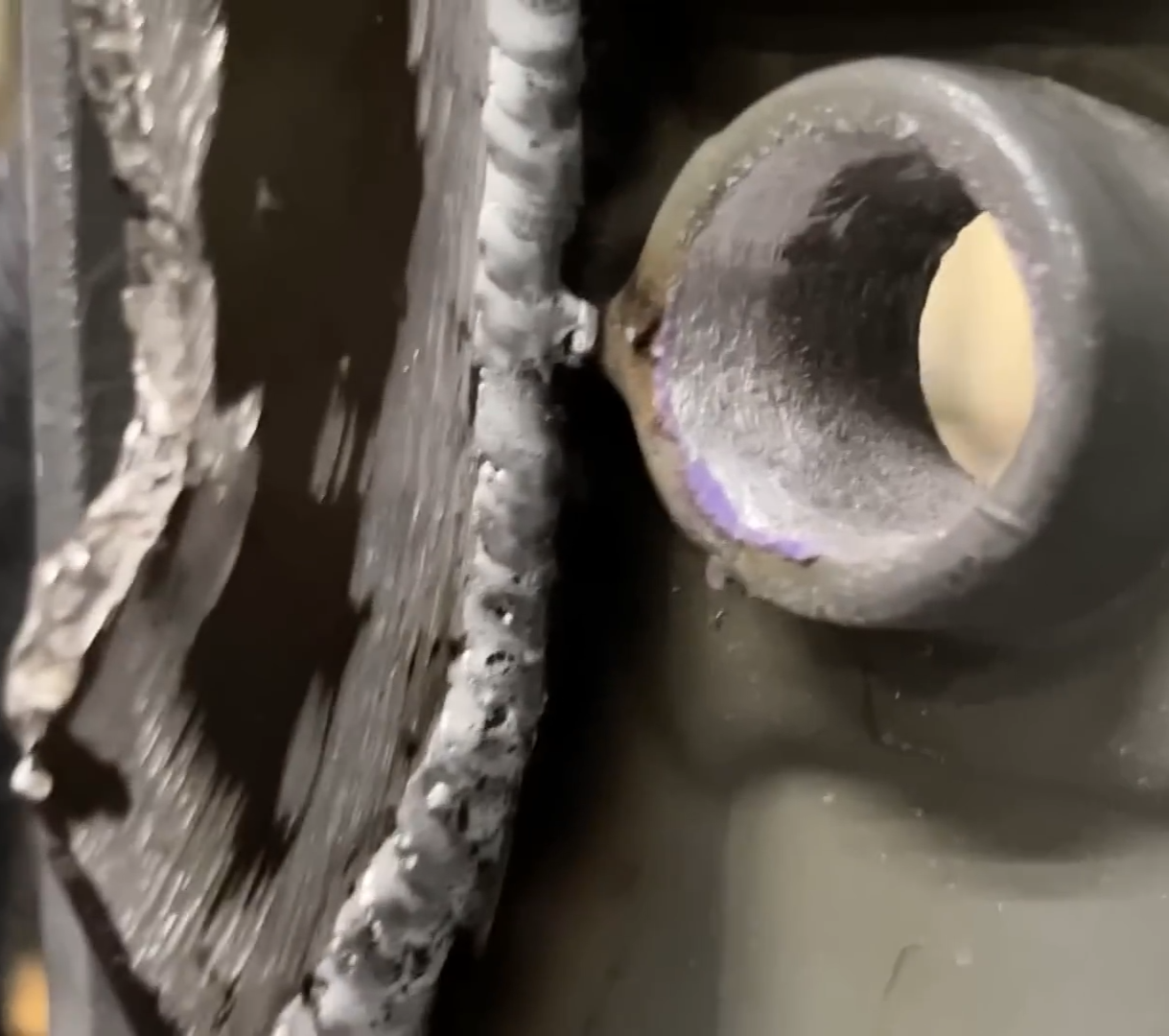
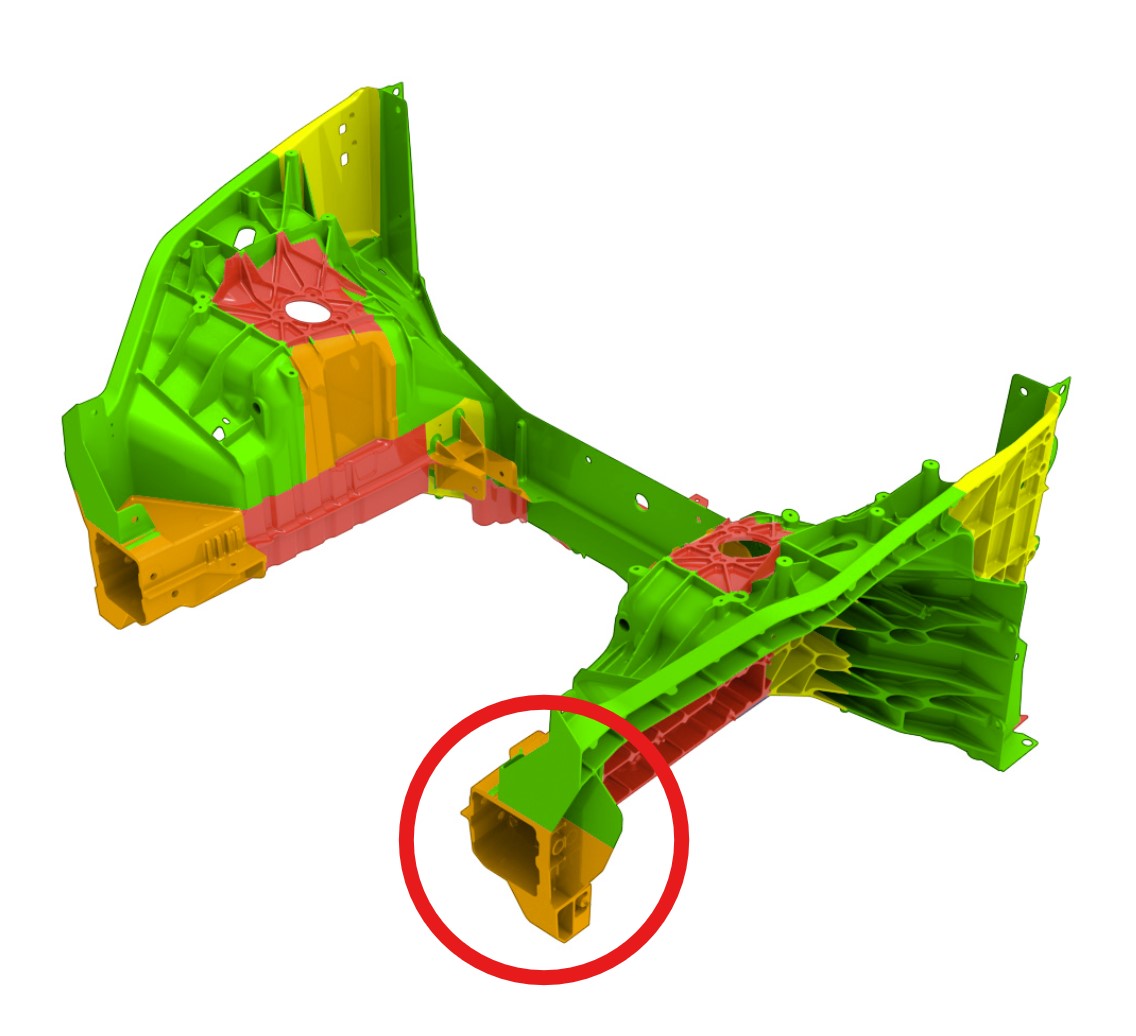
The broken piece appears to be in excess of 2 inches long, so this repair should really only have gone ahead after checking in with Tesla. The owner deemed this fender mounting section to be non-critical, and was able to weld it up regardless. In any case, it should do fine as far as holding the fender on the vehicle is concerned. As for crash worthiness, well, that’s a more complicated manner.
An embarrassing sabotage attempt against Tesla and Giga Press technology
???????? The French Automobile Distribution Federation (FEDA) calls on the government to assess the risks and to take measures against Giga Casting "dangers" for the environment and families
The letter begins… pic.twitter.com/UvyaITKRfQ
— Luca Greco (@lucagrecoita) October 4, 2023
It’s also worth considering the possible vested interests involved in the narrative. For example, last year saw the French Automobile Distribution Federation (FEDA) make a report calling on the government to respond to the “dangers” of gigacasting. The coalition of French auto distributors called for the government to regulate gigacasting. Its prime demand was that cars should be able to be repaired after being damaged by impacts at up to 60 km/h (37 mph).
The FEDA press release hit all the usual talking points. It suggested that gigacast cars would be far too costly to repair and that there could be negative consequences for the environment, as “entire blocks” of vehicles need to be replaced. There is also the oft-repeated statement that insurance costs would skyrocket. It quoted a repair costing €12,154 ($13,545 USD) for 6.5 days of work on a Peugeot 2008, versus a “comparable” repair for a gigacast vehicle of €15,402 ($17,165 USD) for 11 days of work. More expensive, certainly, but not exactly a horrifying difference.
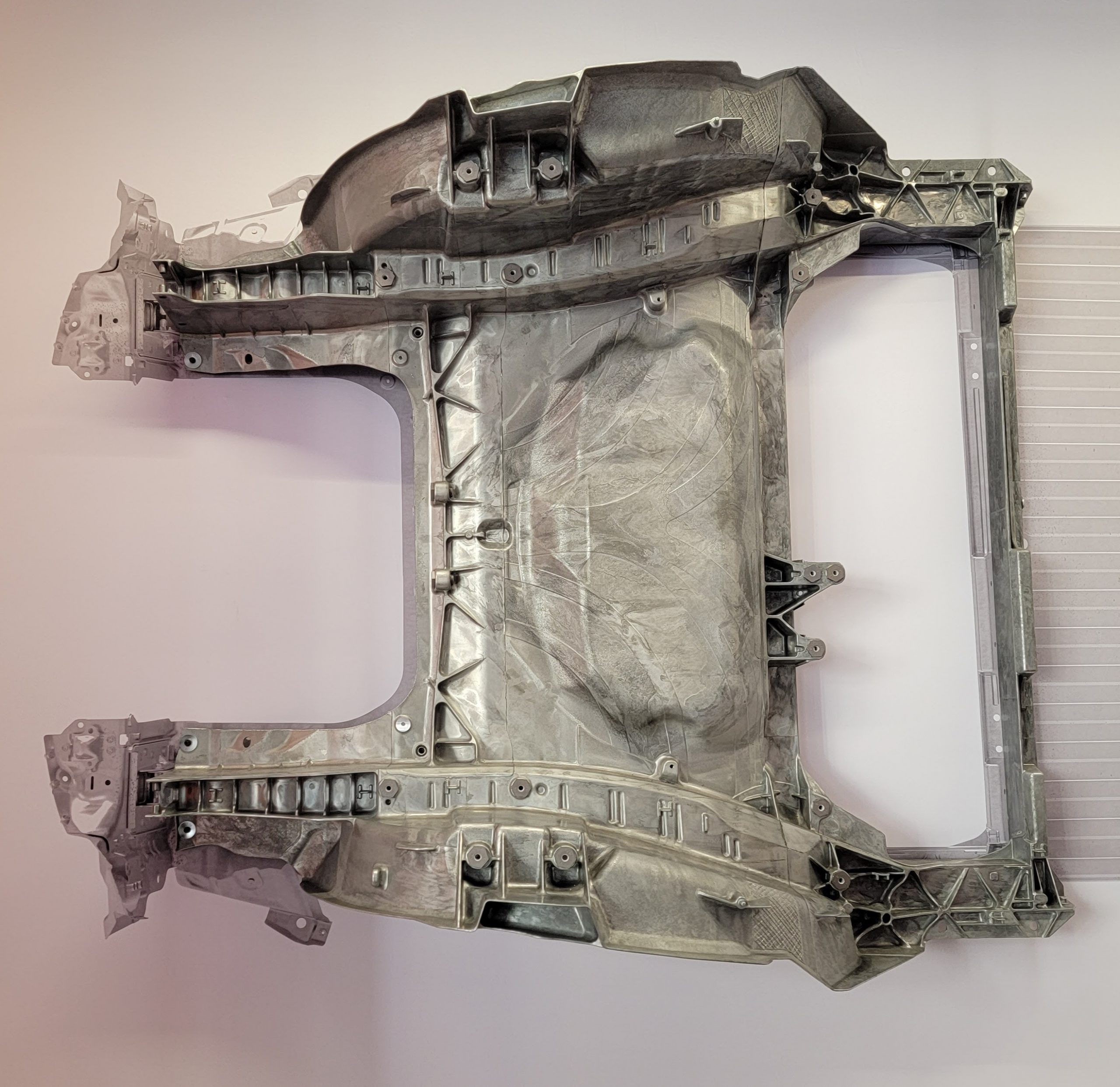
The bottom line is this: Gigacastings and manufacturers that employ them are not some big scary boogie monster out to ruin the automotive industry. These vehicles can survive crashes. They’re subject to the same crash tests as everything else on the road. And they do remain repairable after crashes. Obviously, it is possible to total a car with gigacast components—but you need not worry that they are excessively fragile compared to any other vehicle.
Ultimately, the key is to look at what the industry is doing—not what people are saying. Understand what’s really going on, dismiss fearmongering, and know the truth. My opinion as an engineer is that gigacastings — especially if used in the right places — are fine. Don’t believe the hype that says otherwise.
Image credits: Tesla, Evolve EV Specialists via YouTube Screenshot, Votpuske via CC BY-SA 4.0
So Tesla will gigacast a part, and also make different chunks of that part so people can do repairs with them? How readily available are these parts?
You want a legitimate insurance repair or a redneck repair?
Because you can bet in 10 years out of production those legitimate parts are gone.
Certainly +10 years past production people Will come up with creative ways to repair vehicles, “just rolled in” is a YouTube channel dedicated to mouth open janky repairs.
Above said representing a different kind of himan creativity… additive manufacturing has made it so that any metal part can likewise be reproduced & in some cases additive manufacturing is the only way some parts can be made.
Now of course additive manufacturing is currently pricey, it is a form of technology and costs will follow a cost curve & come down (like any other technology) as it scales and matures.
I didn’t get a chance to ask this on the previous megacasting article, but is there a way to pre-heat the casts so that the molten metal doesn’t lose temperature as quickly?
“The truth is that castings aren’t magic items that can never be fixed.” That would be a curse, not magic.
Are… you asserting that curses are NOT magic?
What about JB Weld
When I did autobody work a century ago, it was not uncommon to find variously crumpled paper and or aluminum foil, fiberglass, screen door mesh, hvac tape, plywood, 2×4’s, bondo, rivets, sheet metal screws, bed frame rails, sheet metal, rebar and other ‘creative solutions’ for frame and body repair.
I bought an MG that the sills were spray foam egg cartons and Dexion shelving uprights- I know British Leland had some low standards but this was definately not factory.
Yeah, it can be done, but the cost is so high, and the number of capable shops so low, and insurance companies much prefer to total something rather than repair it (I think this very website had an article on the topic). Just moving more and more to vehicles being disposable appliances, but that’s the direction most cars are going and there’s no stopping it.
The number of capable shops will increase, so there’s that.
I don’t mean to be too much of an ass here, but a lot of this is true for general aluminum repair work. It is not particularly difficult (in the scheme of true metallurgical workmanship) to weld and PWHT aluminum. It just simply isn’t. But it is something that if you don’t know what you are doing, you can much more easily fuck up than the types of hyper basic steels we have been conditioned to look at as trivially repairable (you should see what high alloy steels take to weld and repair….)
Likewise, procedures for welding to castings are nothing new in metallurgy. Not in the slightest. Sure someone should be taught/trained to understand what is going on with your vehicle and which regions are actually high load and where the material is most sensitive, but honestly steel or otherwise, I’d want my repair person to know that information regardless. I bet these castings are ludicrously more forgiving than the average 50+ yr old casting repairs done in manufacturing.
It is much more an indictment as to the general ignorance of the average ‘repair shop’ than it is saying anything about true cost or risk deltas.
—
But end of the day, obviously anything more than the cheapest least-knowledgable labor is going to be quite a large additional cost. Again more of an indictment on our value of labor situation than anything else.
I work in an industry where we weld cast steel and cast iron all the time. Komatsu and CAT use castings extensively in the frames of their off-road haul trucks. It takes skill and you have to follow the process (pre-heat, post-heat), but has been done for years. However, aluminum welding has additional challenges. One of those is that you don’t get a colour difference with heat like you do with steel. My brother has welded aluminum for years and says it is very challenging. If you get it too hot, you will see a slight sag and if you don’t get the heat off it, it will just drop. Mind you he isn’t welding cast aluminum, but extrusions and plate. I was surprised that Tesla recommends GMA – I would have expected them to use TIG.
Aluminum welding is challenging to truly free hand, but the properties and behaviors are actually pretty consistent so it lends itself quite well to automated welding, and if you do some quick math on weld pool heating and cooling rates, you can avoid most of the pain from not knowing if it is too hot or cold.
I really think that is why MIG is recommended actually. MIG feed rates and the rest (properly done) really force you to work at a certain set pace, which is the best way to do aluminum anyways. Plus casting repair I assume involves a lot of situations where additional material is being added at strategic points.
Honestly this article made me somewhat curious how one would get into repairing gigacast parts for a living… I certainly didn’t know that was a thing, but it sounds really interesting.
Nice read! Even with it being repairable to some degree, I have a feeling that it’s still going to be astronomically expensive and labor intensive (and thus a write-off).
But anywho, Gigacasting does seem promising in solving another huge problem that Rust Belt drivers face: rusted to hell subframes.
So, to recap: Gigacastings can be repaired, if
Have I got that about right?
*: FWIW, I’ve seen similar claims about carbon fiber, but when repaired parts were tested they failed lower than the original undamaged ones. Maybe that doesn’t always happen, but how do you know? You’re essentially left with a hand-built part and all the potential variations in quality that opens up.
Yeah I think you have that right, but I would add #5 applies to pretty much any structural repair regardless of cast vs stamped or steel vs aluminum. Of course that points back to #3 the current lack of those experienced in repairs of cast aluminum.
Yeah, I was also going to mention something about the Audi R8s (I think) that were prone to cracking strut towers or something, which resulted in a prohibitively expensive repair if it were done correctly. A lot of people just welded the crack and crossed their fingers.
Exactly. This in particular:
Good luck getting an insurance company to go along with this for any structural part.
I learned a lot from this article and it has challenged many assumptions I once had. Thank you.
Agreed
This is one of those “can we?” vs. “should we?” questions.
Absolutely you can weld and fix the broken part. Here is the part I didn’t see covered and that is how do you inspect the entire gigacasting to verify there are no severe hairline cracks that are not visible? Will every repair shop have an NDI specialist on hand to verify overall structural of the entire casting?
I’m not an engineer, but I’ve seen my fair share of damaged cars where the stress loads cause severe damage to areas not in the immediate impact zone. Personally, I’d never want to drive a car with a major structural repair of any sort, especially one to a complex cast part that was repaired by the insurance company using the lowest priced quote.
Eddy current would be the fastest way to check for cracks. I would also be interested to see how the insurance companies respond to this, as I have read of them declining battery pack repairs and writing the vehicle off instead.
They have been using ultrasound machines to find stress fractures in military airframes for decades
Certainly only a few shops will have the proper equipment and personnel to take on the work. As it is there are a lot of shops that won’t touch an EV or Aluminum vehicles. My son had a branch fall on his Lightning It left a small dent in the hood, in the roof and broke the windshield. Most of the shops refused it stating the fact that it was an EV but few also said it was because Aluminum. This is in the Seattle area which has fairly high EV adoption and Ford trucks are of course very popular.
I am surprised to see that Tesla has published such a clear and helpful repair guide.
I was never worried that much about gigacasting repairability, because even if it’s possible body shops are not very likely to do it. Unibody and ladder frames are very repairable, but most shops won’t touch a majorly damaged frame for liability/insurance/expense/specialized tools and skills reasons.
So what if you can’t repair major frame damage on a Cybertruck? You can’t find somebody to repair major frame damage on whatever else you might be driving.
Well with BOF trucks you can sometime source a service replacement frame, (especially certain Toyotas). Might not be done often but it is done occasionally.
I have a bunch of old IH service materials one of which is a labor guide where I was a bit surprised to see they do indeed list the times to do a frame replacement. Heck I pretty much did that with one of my Scouts, tearing the rolled body off of a V-8 4sp 4×4 and rolling it under my previously 6cyl 3sp 2wd body.
I had a 2002 Tacoma that had the frame replaced because of rust. The dealership had it for two days, it was supposed be 16 hours of labor.
They’ve made a concerted effort in this regard—something that came as a surprise to many!
In aerospace we have a saying- given time, materials, and money we can repair anything. And that’s true, we can repair anything (also, give me some lead and access to a nuclear breeder reactor, and I’ll turn it into gold). The question, inevitably, is “how much?” Looking at the cars shown in the article, at a minimum they start with significant stripping/removals of components and interiors to get access. Then you have structural aluminum bonding and welding, which is not a skill most auto body techs have. Then you have to properly heat treat the weld zone, and restore finishes. Also, probably get some sort of non-destructive inspection to ensure there are not still cracks hiding in the repair.
I am skeptical a good, structurally sound repair would cost less than whatever cutoff is needed to total the car.
I used to work at a manufacturing facility that has huge machinery with huge cast aluminum parts. Some of the machinery was 50+ years old, and the when the cast pieces broke it was always quite the repair. There were porosity issues, as one would expect on metal cast half a century ago, but the folks we hired for the repairs were amazing…and amazingly expensive. It was easy an easy business case on giant machinery that nobody makes anymore, but depreciating assets like cars is much harder to justify.
I’m completely with you that the repair can certainly be done, but I have a hard time seeing it being cost-effective enough to keep from simply totalling the car.
Maybe for now, but it’s a new technology, and new technologies eventually result in new professionals trained to repair them. Right now there’s a shortage of professionals trained to repair them, making repairs expensive, but if there’s clearly a demand for it then why wouldn’t the number of people trained to repair such things increase over time?
If you find a welder with the skills to perform this repair, they probably don’t work at an autobody repair shop.
I don’t know about the rest of the country, but here you’d have to wave a lot of money at those guys to get them out of the iron workers’ union with steady work, good pay and retirement benefits and into the cave of OSHA violations that is the average body shop.
Because welders who have the skill and certification to do repairs like this are in demand in a bunch of other areas, pretty much all of which pay a lot more than normal auto body work. I’m sure you could convince one of them to do the work, but very soon those buckets of cash you’re having to shell out exceed the economic value of your damaged car.
The economic threshold for auto body repair is “can someone nursing a massive hangover and working out their frustrations via percussive maintenance be productive here”. This isn’t to say there aren’t master craftsmen in the field, but you’ll notice they are rather pricey and tend to work exclusively on high end vehicles where the cost can be justified. Model 3s are, in this benighted age, ironically an economy car that can be had for nearly 10k less than the average new car costs, there’s not a lot of margin for repair bills.
Fifty years from now, some guy will drag a wrecked Tesla Plaid out of the woods. This article will be like gold to him… lol
Well it would be Derek Bieri, right?
I sure hope a guy’s been retired by that time. Last I heard he has like 150 cars and spends most waking moments creating content. Eventually, that’s gotta eat away at you, right?
“a guy”. Nailed him.
I mean, his name is David. He owns this very website. Not exactly “some guy.”
The phrase “by no means impossible” doesn’t give me much confidence that body shops are going to be making these repairs quickly and cheaply anytime soon.
“Let me try, boss. I always wanted to fix a gigcasting.”
https://www.youtube.com/watch?v=14yL8zW4ybc
I somehow expected this to involve a lot more spray foam and drywall screws
And one of those rivet gun sets from Harbor Freight.
Don’t forget your self tappers and roadside signs (acquired legally)
And license plates!
Nope, that’s just in the tent they build them in. Except I think it was wood corner molding and packaging straps.
The main issue the FEDA probably has is that, for various reasons, not many car mechanics in France are trained to weld…Training people to weld Aluminium and those gigacast pieces is going to cost them money. And they see the writting on the wall that a fair number of the people trained wll then ask for a raise… or find a place with a beter pay.
Since it’s the kind of job where it’s already quite hard to find people willing to do it ( and trained to do it ) anything that change the way the work is done is seen as potentially disruptive and dangerous for the business.
And last the difference is not that high, especially when you consider the actual price of both cars given as an example ( 2008 base price is between 27K and 35K Euro depending on the trim, I took a Tesla Model 3 for the gigacast car, which stands between 42K and 58K Euros depending on the trim for the base price ).
It doesn’t have to be impossible and I’m not sure how many people who may have been stating such were doing so in a literal way, it just has to be too expensive.
How many people are trained in these repairs? How backlogged will these far fewer and more highly paid people be and how well distributed are they or does one have to ship a battered car hundreds of miles to get to them so it can sit in a holding lot where they are assailed by vandals and vermin until they can work through their backlog to get to it? That’s all money up and down, which means more totaled vehicles for minor crashes.
How many of these gigastructures are they building for crash repair purposes (Tesla is notorious for under-building repair pieces already)? Assuming they actually build the parts, they have to be warehoused and they take up a lot of space per part number and then there’s shipping and handling of a large bulky piece to the repair facility. All more money. Now you have to buy an entire structure to apparently precisely chop up and glue onto the existing damaged part that needs the damaged section precisely removed or—what will probably make more sense much of the time—just replace it with the new part incurring what’s very likely to be more labor, if less specialized. Money. Insurance is already more expensive for EVs. Oh, and that’s not even including future repairability for after the platform is replaced and the castings are retired (with however many or few cycles that may be left on them) and no more replacement parts will be made unless some aftermarket buys them, but how many could they conceivably buy and maintain and operate and warehouse completed parts? These aren’t print-on-demand operations. Seems like, again, too much money.
Almost anything can be done, it’s whether it’s practical and economical to be done that determines whether or not it actually gets done (like recycling, another private enterprise method of pawning off corporate responsibility onto the public by touting a technically true possibility as a solution to a problem they created knowing that the proposed solution sits somewhere on the spectrum of impractical to practically impossible to implement in the real world, dumping that cost on the public, and blaming them for that inevitable failure).
Malibu = $849
Tesla = $1445
You’ve got an interesting view on what is considered “favorable”. If I saw insurance rates $600 higher for one car vs another, in this case nearly 75% higher, that would absolutely factor into a decision whether to buy.
The Malibu is one of the cheapest ICE cars on the market, isn’t it? That feels like a deliberate “worst-case” comparison to what might be one of the cheapest new cars to insure.
Purchase price is not necessarily indicative of insurance cost. However, if I was going to compare insurance costs and I wanted to eliminate the cars’ prices as a factor, I would pick two cars with a similar MSRP, not two that are wildly different.
Lewin’s point seems to be that insuring a Tesla doesn’t cost significantly more than an ICE car, but his example contradicts the argument.
I think the waters may be murky here since we implicitly have to separate how much of that difference is because it’s an EV, and how much is because it’s gigacasting.
Really, the most objective insurance comparison would only be between two vehicles, similarly mass-produced, identical save one being gigacast and the other not.
But EVs, especially for the short-term, are going to be more expensive and that throws a wrench in making a good insurance comparison, especially at the cheaper (purchase price) end of the market where there aren’t a ton of choices to begin with.
Then perhaps it should have been compared to a similarly-priced non-gigacasted EV, but that’s not what he’s doing. He specifically states that he’s comparing the Tesla to an ICE car. Nothing murky about that. If you’re going to tell me that I can insure a Tesla for the same or better (favorable) price than an ICE car, you better not present evidence to the contrary.
Fair point. My final thought, I guess, is that assuming those are annual insurance rates and not semi-annual like I pay, I think the difference is reasonable (jumping to both EV and gigacasting).
I also assumed they were annual, but my assessment still stands. A 70-75% increase may be reasonable or appropriate considering the increased cost of repair, but it’s not “favorable” or “comparable” by any stretch of the imagination. Those are the words Lewin used.
To your point of eliminating variables would be to compare a recent model e (made with traditional manufacturing) vs. The model Y which of course uses gigacastings front and rear…
Well, I’m sure an Altima isn’t cheap to insure. Too many people taking advantage of the exhilarating performance capabilities allowed by the Jatco Xtronic CVT, at a price that’s affordable for everyone.
Pay attention to the collision section, which is almost double for the Tesla. But, this can be based on the value difference of the cars.
Regardless of the cost to repair one type of car vs. another, collision insurance is capped by whatever they determine to be the value of the vehicle at any moment. They may total a Malibu at $20,000 in repairs while they could be on the hook for a lot more money with the Tesla (or any other vehicle worth more).
All true. Which makes it an even stranger comparison to use, not better.
Agreed. But I’m not seeking insurance quotes for fun on cars I don’t own to get a more direct comp.
Me neither. But Lewin is, assuming his job is fun.
Repair being possible is great. Now find a bodyshop thats willing and able to do it…
This has same vibes of saying; all car frames are repairable*
*if you can find the shop that has the right jig for it
It’ll take time, but sooner or later it should be more widespread. Doesn’t that happen with lots of technology adoption in vehicles?
I wouldn’t count on this becoming very widespread. There are very few body shops that will touch frame repair as it is, what motivation do they have to buy a bunch of specialized tools and train on aluminum welding?
It shocks me that there wouldn’t be more demand.
Hell, I don’t even know if I can find regular mechanics around me open on Sundays or 2nd shift on weekdays, and I would think there’d be lots of demand for that.
This is a lot like aircraft. You have the SRM, structural repair manual that gives all the “basics” about what and how to repair. Beyond the SRM, you call the aircraft manufacturer to be sent a repair instruction.
The catch, the department that manages the repair instructions is very expensive to operate. It will be interesting to see how automakers absorb this new cost center. Hint, they’ll charge for it, increasing the cost of repairs.
These large casting do make a ton of sense, but the extremely large ones do a much higher risk of repairs exceeding the value of the car. More modest castings bolted together can change the risks.
Yup, was going to say this looks very much like the SRM for a commercial airliner. Repair is absolutely possible, provided you’re willing to pay aerospace repair prices.
I doubt the question was ever about feasibility. The issue is how much such repairs would cost (and how long, and how much skill is required, and how available replacement parts are, etc), compared to similar repairs in a more conventional vehicle. And this is ignoring the fact that insurance companies are already more likely to total EVs over concerns on the battery and drivetrain.
Plenty of people with no specialized crash repair knowledge spouting the same old lines that you can’t repair these castings. So many articles on gigacasting from the past two years repeat this common talking point; I linked a few in the article.
Considering the cost to make repairs on these “shattered” cast pieces, will a vehicle be a total loss anyway due to man hours/skill set?
Ignoring GIGA, has this been a problem with other cast parts in the past?
Back as a 1950s kid I remember watching my handy neighbor gas braze a patch on the cast iron crankcase of his tractor engine where a broken connecting rod had punched through. IIRC it ran for many years after the rebuild.
Well yeah, engines are cast, and they crack occasionally, and few people try to repair them even though it’s possible.
Hey Vern! Come with me to Auto Zone to pick up a tube of JB Weld!
Just gonna leave this here:
https://www.youtube.com/watch?v=aVLoJe3JbFI
This article kicks ze butts. awesome deep dive!
I’ve posted on here a number of times. Forget college for your kids, heliarc welding is gonna be a booming occupation.
$$$
Interesting to me, the recommended aluminum repair technique for these isn’t TIG, its MIG.
And why couldn’t you just say TIG? so i don’t have to google?
Until they roll out the repair bot. It will never work as anything but a deterrent to organized labor, but it will work to keep wages down (like the Burger bot they dust off every now and then to scare fast food workers).