Electric motors have been around for the better part of two centuries now, so you might think there’s nothing new left to discover about them. That’s not the case, however, as it turns out Kia has pulled off some nifty tricks with the propulsion unit for the EV9.
The team over at Munro & Associates has been pulling apart Kia’s new full-size electric SUV. Now, we get to see a teardown of the EV9’s rear motor which reveals something special. The Korean automaker has pulled off a bit of a world-first that could net some serious efficiency gains.


The video gives us a quick montage to show the disassembly process for the rear drive unit. Ultimately, though, it’s the motor’s windings that are the primary focus. To explain why this it’s so special, Munro tapped lead electric machine development engineer Paul Turnbull to give us the low-down.
Cleverly Using The Motor To Boost Voltage From 400V To 800V
Before we start, we should just cover off some terminology. First, when Turnbull says “electric machines,” he’s basically saying “motor.” Beyond that, you should read our deep-dive on how EVs work, and you may want to brush up on some basic motor terminology; I explained it in last week’s article on the Ford Mustang Mach-E, but I’ve quoted it here for your convenience—along with diagrams!
What’s a stator? Well, it’s the big metal part of the motor that is, as the name implies, stationary. A stator is typically made of laminated plates of special steel that reduces eddy current losses, and is the structure that holds the windings. The stator windings are basically coils of copper wire wrapped around the stator core to generate the rotating magnetic field that makes the motor spin. If you’ve ever wound a coil of wire around a nail to make an electromagnet, you’re familiar with the concept. Windings in EV motors tend to use more advanced geometries and thicker wires, but the concept is the same. Wrap a conductor around some metal, run some current through it, and you’re generating a magnetic field.
[The rotor] is the central spinning part of the motor. The rotor has permanent magnets on it, so when the changing currents in the windings create a rotating magnetic field, the rotor spins in turn. It’s the job of the motor’s control electronics to energize and de-energize the separate windings in the right sequence to make the rotor spin. There are usually three sets of windings, or “phases,” that have to be switched in the right order to make the motor turn.
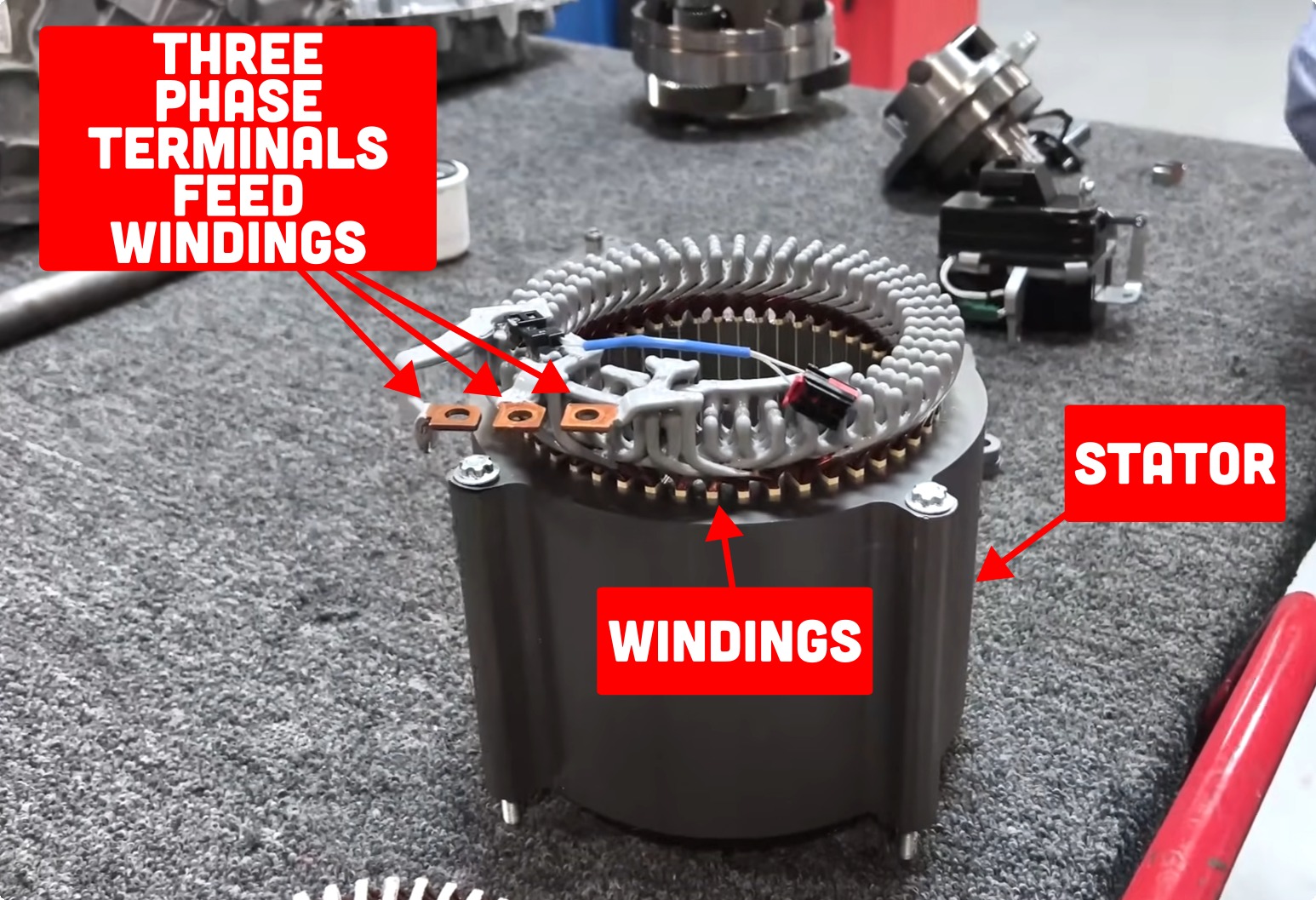
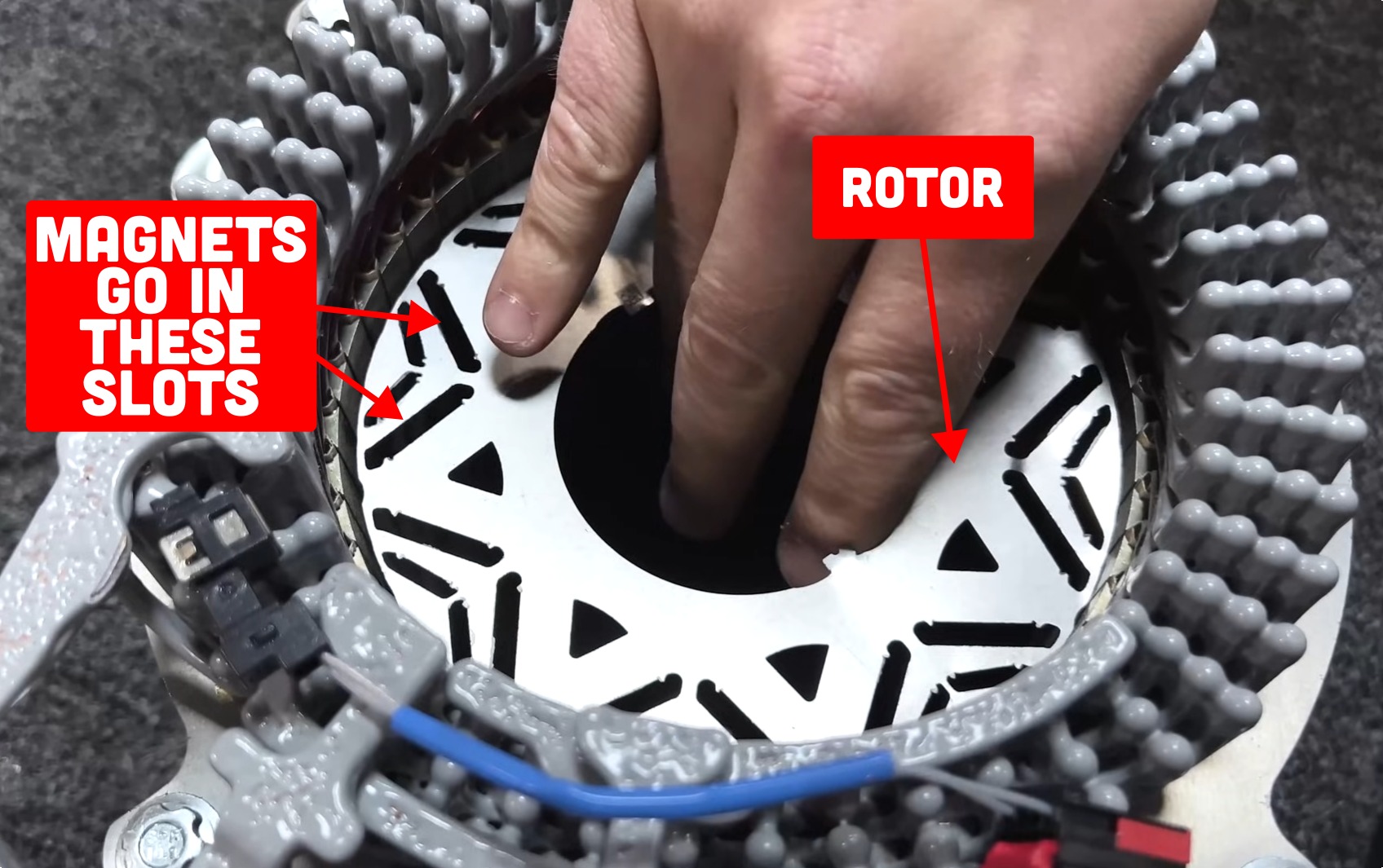
Okay, so back to the video. It begins with some interesting context — Turnbull shows us a motor out of the Hyundai Ioniq 5. He notes that while most such EV motors have three terminals, this one has four. It allowed Hyundai to pull off a nifty trick. “They’re using the inductance of the motor as a part of the boost converter in their charging system,” Turnbull explains.
Confused? It’s actually quite simple. Basically, Hyundai’s EVs were using 800-volt battery systems, but many chargers only put out 400 volts. To charge properly, the needed to use a device called a “boost converter” to step the 400 volts up to 800 volts. The boost converter typically requires a large inductor—basically, a big coil of wire. Hyundai realized the motor was full of large coils of wire, and thus the windings could act as this inductor instead. The motor isn’t otherwise used when the vehicle is stopped and charging, after all. It just had to add an extra terminal to make it possible. This saved the company the cost of including another expensive inductor in the boost converter circuit.
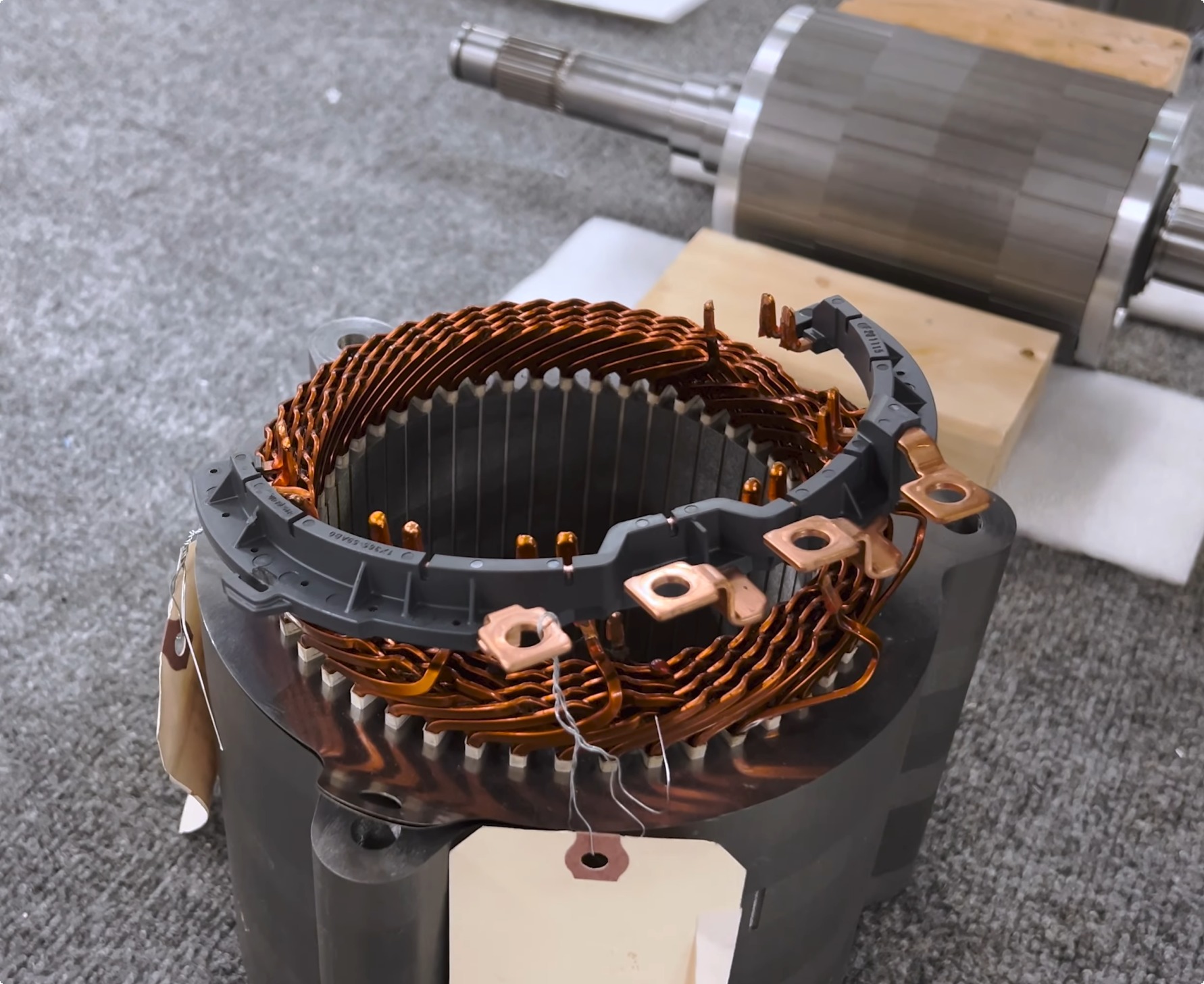
What’s a Dual Stage Motor?
Look at the Kia EV9, though, and things have gotten even fancier. It’s now got six connections! “They have both the beginning and the end of each of the three phases connected to the inverter, and that gives them full access to the winding configuration of the motor,” Turnbull explains. “What this system does when you have all six connections coming up to the inverter, it allows you to reconfigure the motor in one of two different configurations – either wye, or delta.” So what does that mean? Well, it’s all about how the windings are connected.
The EV9 rear drive unit. The rotor has already been removed in this shot.
A motor has three sets of windings—or phases, if you will. Each winding is essentially a long length of copper wire that’s been wound around the stator to create a magnetic field to turn the rotor. Normally, you have three connections to the three windings on the motor. These hook up to the inverter/motor controller. The other ends of the windings are usually permanently connected in one of two configurations—delta or wye. In delta configuration, the end of each winding is connected to the start of the next. It makes a triangle if you draw it as a schematic, so it’s called “delta.” Alternatively, you can connect the other ends of the windings together in a single point. This makes a Y shape if you draw it out, so it’s called “wye.”
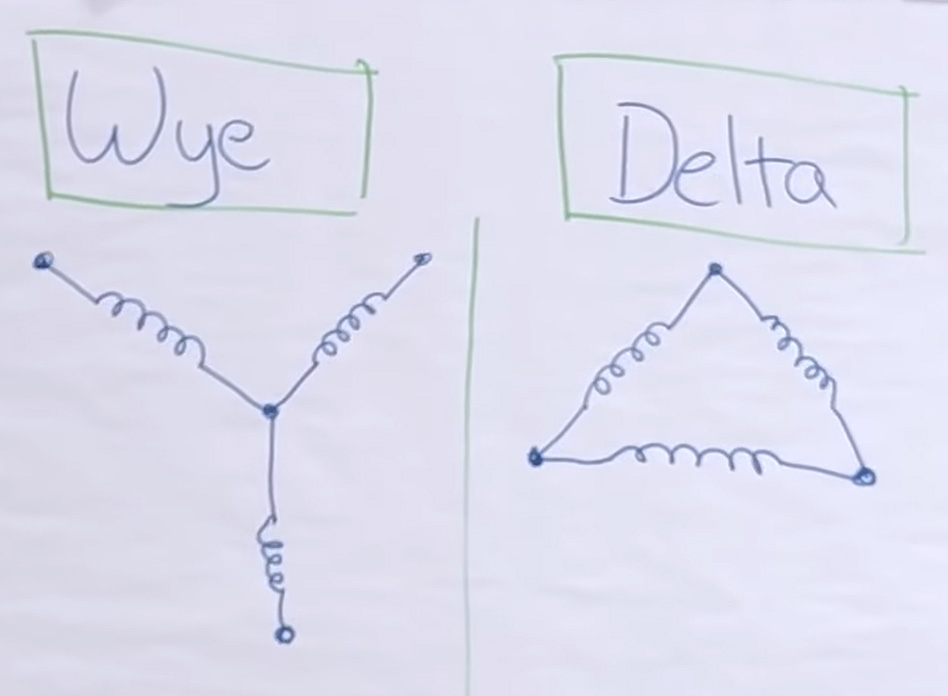
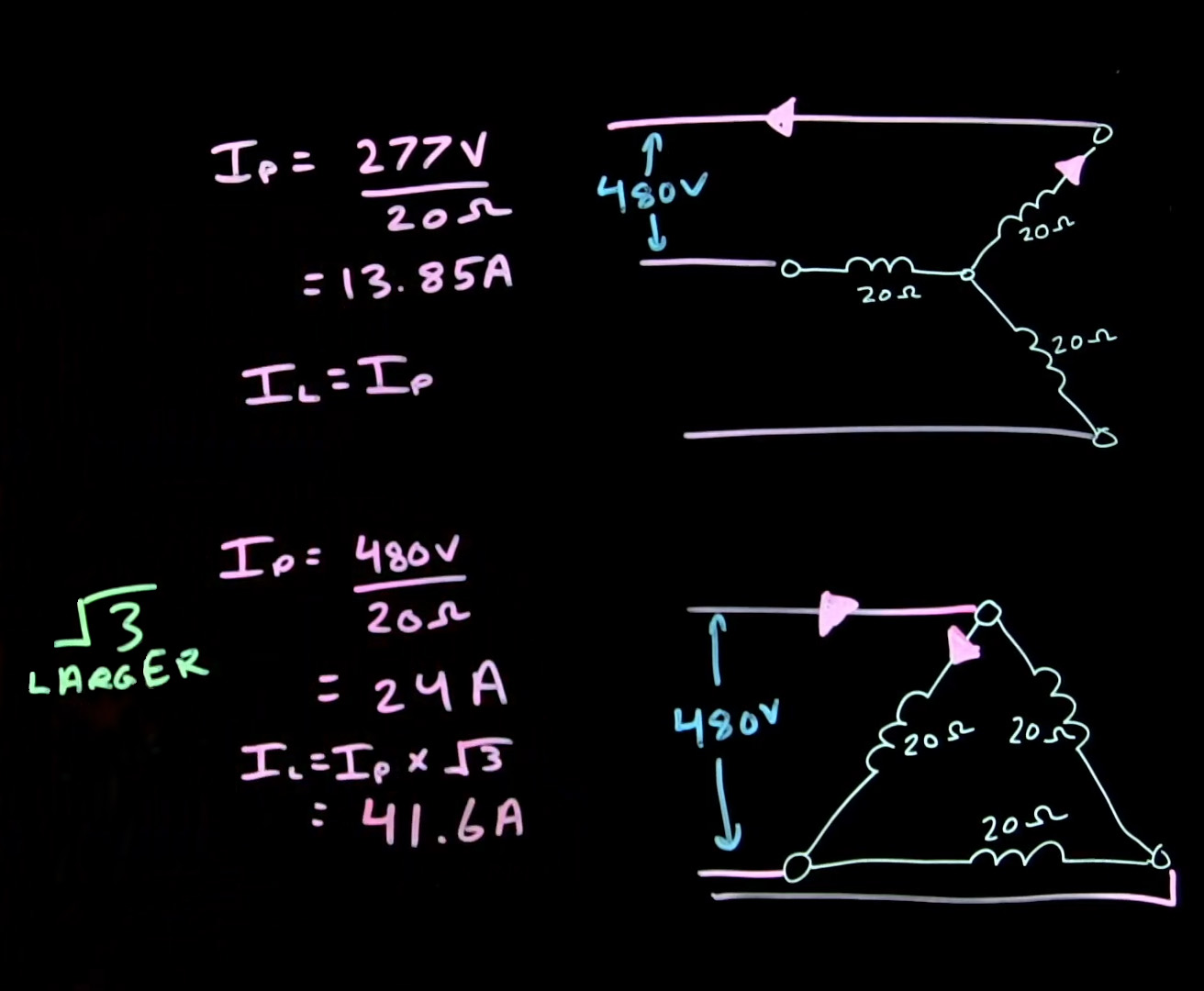
If you want a deeper explanation of the differences between wye and delta windings, I can recommend these videos from Electrical Trades Instructor/podcaster Zack Hartle. However, they’re intended for an audience already very familiar with electrical topics. If that’s too complex, I’ll spell it out in simpler terms below without all the electrical mumbo jumbo.
An Electric Motor ‘Changing Gears’
Depending on the winding configuration you choose, the motor will have different characteristics. Here’s a simplified explanation. For a given input voltage, you would typically choose a wye winding for a motor that’s more efficient at low speed. You’d choose a delta winding for more power and efficiency at high speed. However, Kia realized that if it exposed both ends of the windings, it could use switching hardware in the inverter to change the winding configuration on the fly.
Munro’s Turnbull notes that wye-delta switching is very common on industrial machinery. It’s often used on large motors in heavy equipment. They are often started with the windings set to the wye configuration, which limits the amount of current drawn by the motor. As the motor gets going, it can then be switched into the delta configuration, which draws more current but also offers more power and efficiency at higher speeds. It’s almost like an electrical equivalent of shifting gears.
Thus far, EVs haven’t used wye-delta switching due to the added complexity, but Kia has found a way to make it work.
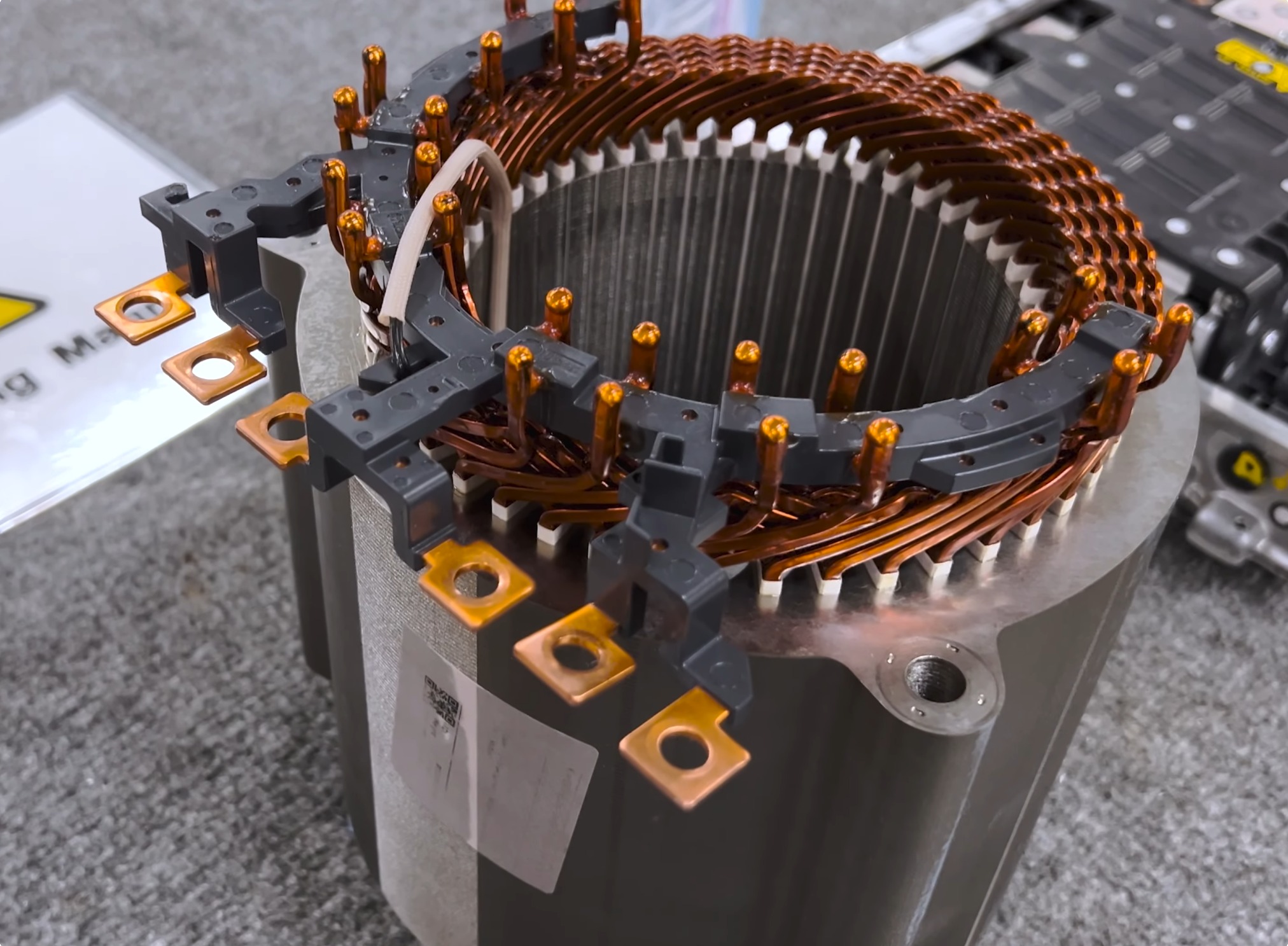
Turnbull refers to it as a “dual stage” motor as an easy way to understand it. “When you switch from wye to delta, the personality of the motor completely changes,” he explains. “When you connect the machine in wye configuration, it gets high torque, and it’s really great for low-speed efficiency.” Meanwhile, the delta configuration behaves quite differently. “If you connect it in delta… you end up with lower resistance in the winding, and you get much higher power from the motor, about 1.7 times the power,” says Turnbull. “You shift the high-efficiency point from low speed up to high speed.”
The result is a motor that performs better over a wider operating range. “Typically you have to design a motor with one physical connection and then you have to compromise between this low-speed and high-speed performance,” says Turnbull. “But with the EV9, they’re able to optimize for city efficiency in the wye connection, and then on the fly, this inverter is able to switch—with power running—to change it to a high-power [delta] configuration with high efficiency at highway speed.”
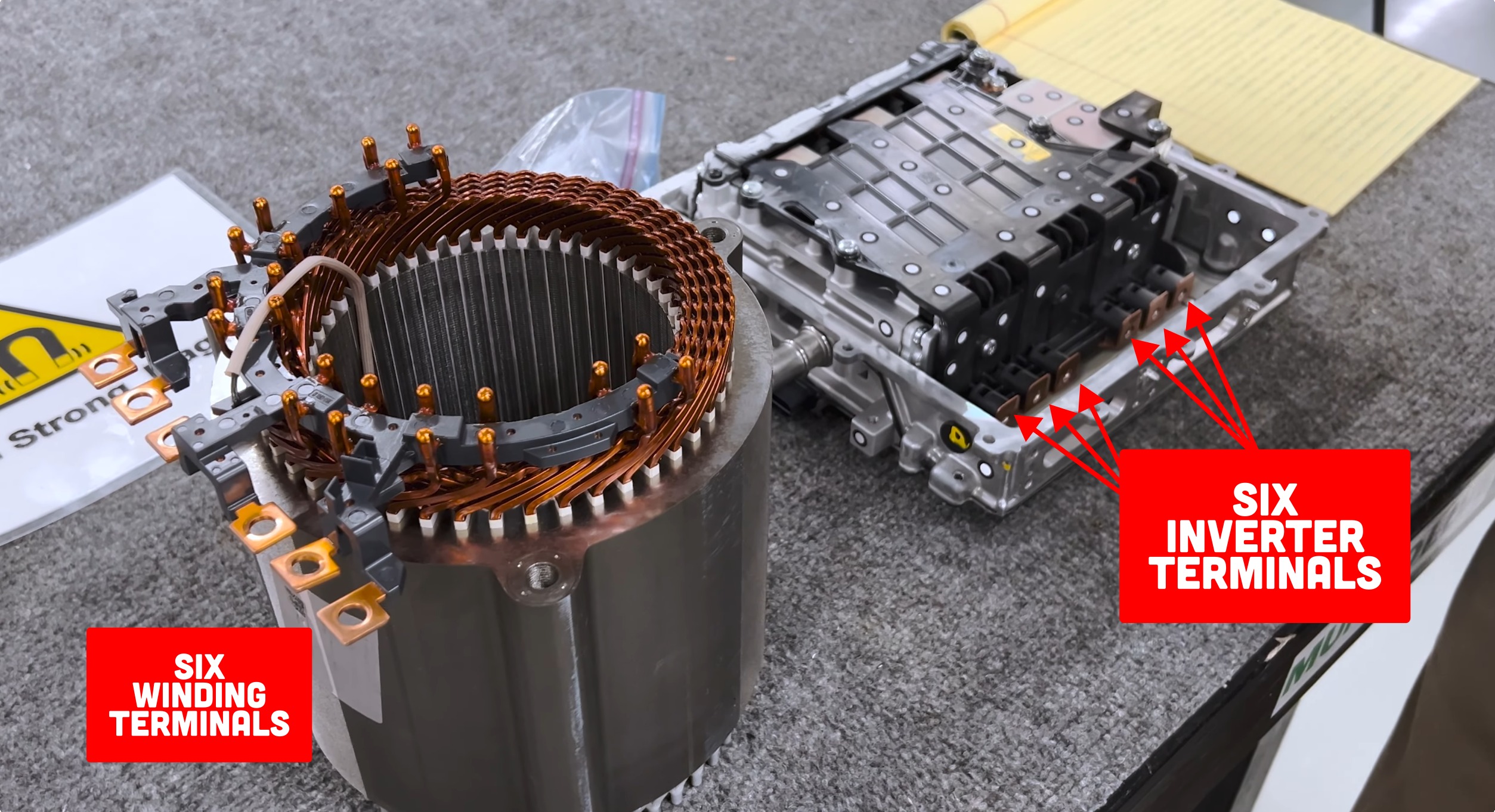
The switchover is handled by the semiconductors in the inverter itself. “It’s just a reconfiguration of the winding, and the inverter is able to smoothly transition from wye to delta.” Turnbull explains. “That smooth transition allows you to go from the high-torque, low end, get-off-the-line performance that you get with a wye connection, to, when you get up around 45 mph, you switch to delta… and then you get the high efficiency performance for better highway electric range.”
‘Brilliant’ and ‘Groundbreaking’
Noting that it’s “absolutely brilliant,” Turnbull expounds upon why we haven’t seen this before. Basically, it comes down to costs. “In the past, it has never been practical, because in order to do it, you have to have, in the inverter, two completely separate sets of switches,” he says. Basically, inside the inverter, there are a bunch of semiconductor switches, normally Insulated Gate Bipolar Transistors, or IGBTs. They’re responsible for switching battery power to the windings of the motor in the right timing to spin the rotor. However, if you have a six-lead motor, you need more IGBTs to control the connections between the other ends of the windings.
“The switches are the most expensive part of the inverter, and so there really hasn’t been a cost effective practical way to do that,” says Turnbull. “But now, these switches are coming down in cost.” Basically, now that EVs are becoming more popular, economies of scale are kicking in. It’s not cost prohibitive for Kia to throw in some extra semiconductors to pull off this neat little winding reconfiguration trick.
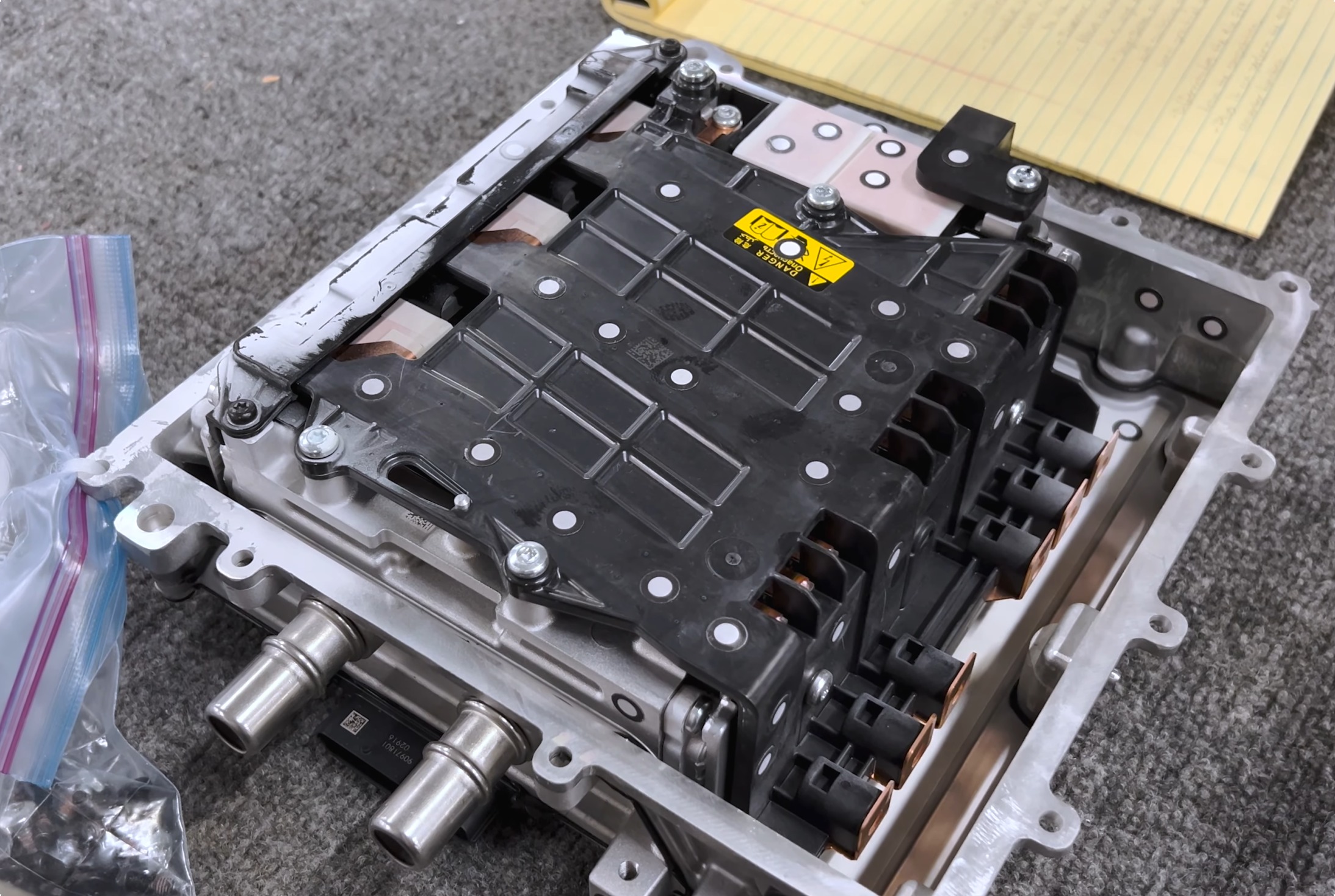
Oh, and remember that trick on the Ioniq 5 with the boost converter? Kia’s doing that here, too. Turnbull notes that the cost savings of using the motor’s windings instead of another big inductor really help. “With all that functionality built in, it more than pays for the extra set of switches in the inverter,” he says.
“This is an idea that has been kicking around in the industry for twenty-plus years and no one’s been able to come up with a practical way to actually implement this for a traction machine in an EV,” Turnbull explains. Basically, Kia’s pulled off a bit of a game-changer. “It’s the first that we’ve seen in the industry, a groundbreaking innovation that Kia has put on the road for us,” he says. “It’s something that I think a lot of the other automakers now are going to be looking at.”
Turnbull also credits the Kia motor for the quality of its construction. “I wanna give a quick shoutout to the supplier that made this motor… the supplier is Vitesco” he says. “Not every electric machine developer is able to do these bar wound interior magnet machines with this kind of quality.” He particularly highlights the construction of the windings themselves. “I want to point out the uniform spacing between the conductors, and how every single conductor has the same exact bend in it,” he explains. He also credits the quality of the welding, noting that these two factors are key to building a motor with excellent durability.
The laminations on the stator are solid, too. “On the older design [on the Ioniq 5], you can see that the lamination around the mounting points can sometimes bend up,” he says. “This has happened during our handling, but it can happen in [the manufacturing] process and that can cause some trouble.”
On the Ev9 motor, though, Vitesco has taken measures to improve things. “What they’ve done here is they’ve added four little… what we call stitches… where they indent the material to make one lamination lock into the next, to make sure the laminations stay put,” says Turnbull. “Little details like that are a sign of a supplier that knows what they’re doing.”
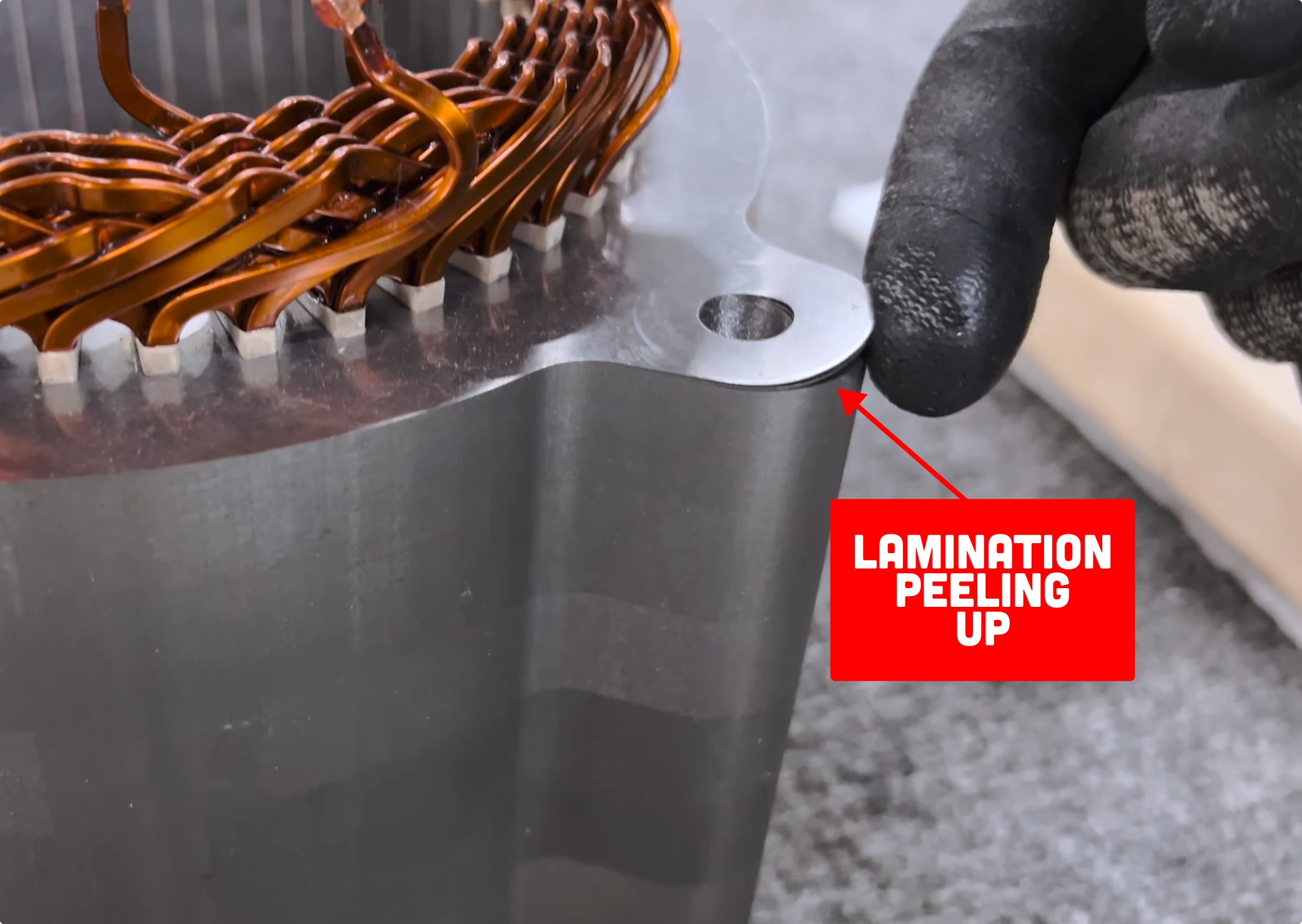
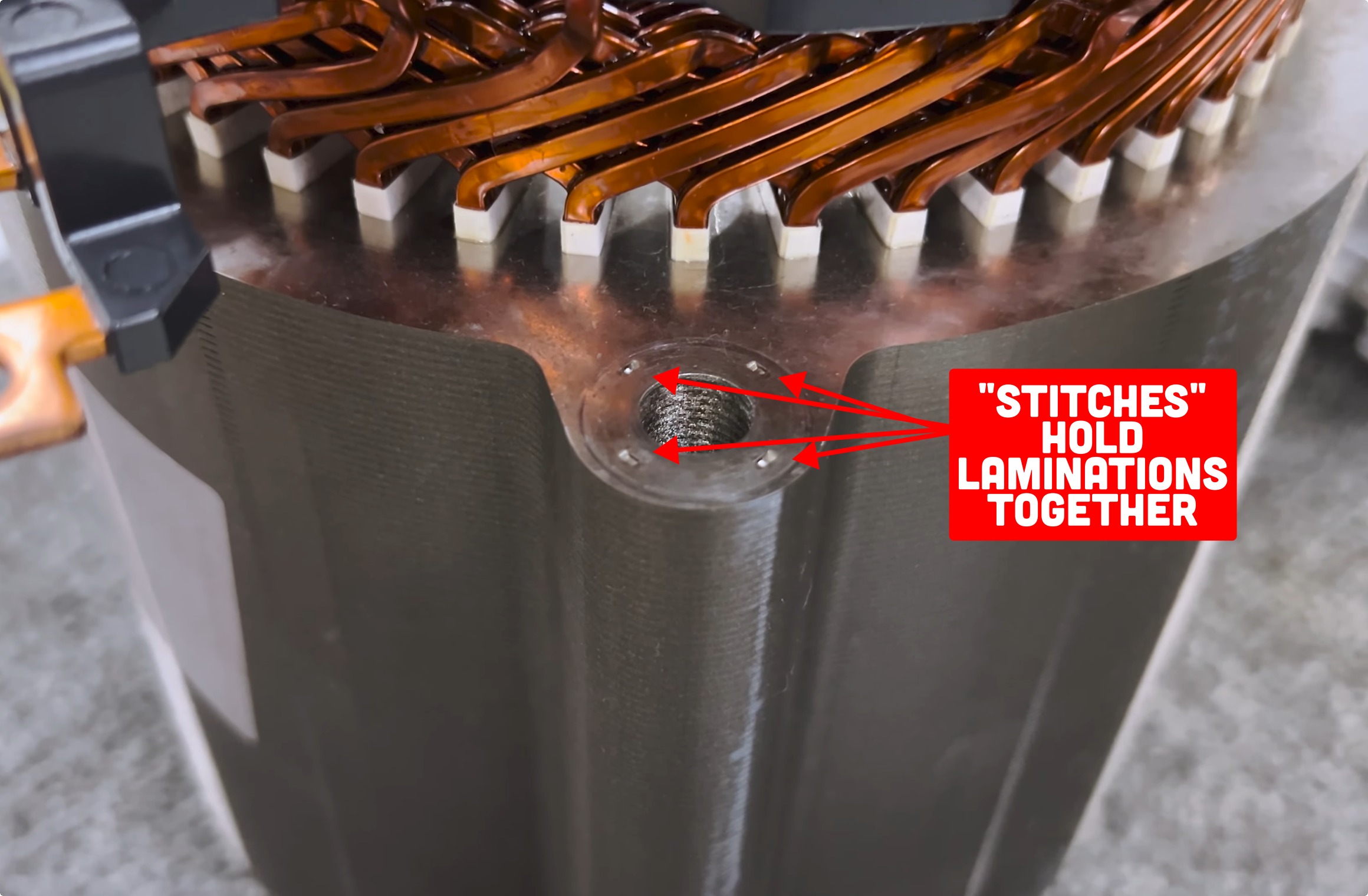
Ultimately, it’s no surprise we’re seeing innovation like this in the Kia EV9. It’s an important product for the Korean automaker, and it helps to be on the cutting-edge to do well in the marketplace. It’s also the kind of thing you’d never learn unless you completely pulled the vehicle apart. It’s hard to argue with the value of a good teardown!
Image credits: Munro Live via YouTube screenshot, Zack Hartle via YouTube screenshot
I enjoyed reading this so much. Like carburator-disassembly-manual much. After some hesitation I am on a full catch-up swing on electric propulsion.
Thank You Lewin! Your best article yet! Kinda surprised this is the first production EV application since it’s proven tech. Just reinforces my position that it’s too early for me to consider an EV purchase, as fundamental advancements are happening at a rapid pace. I’m also allergic to spyware, bloatware, and piggish SUVs, and pretty much everything currently offered.
Agreed but uhhh I wouldn’t hold my breath on the first 2 for even longer. Spyware especially is here to stay, as our government does not care about digital privacy unless you’re China.
Still hoping for a resurgence of sanity.
Ok that’s pretty cool
I’m going to guess that by combining the propulsion and induction functions they are also saving on copper, which should reduce cost.
Thank you for explaining this, since the video failed to do so. Maybe this is obvious to the Munro people, but we’re definitely at a point in the EV lifecycle where regular people may be interested in how EV motors work but don’t know all of the electrical stuff that goes along with them. I’m certainly in that category and wished they would explain this more when I first watched this.
This may be new in the automotive traction OEM market, but railways have been doing Y-Delta switching for decades and large industrial motors (like giant mining rock tumblers and paper mills) have had the capability for probably over a century at this point.
The potential described in the article/video is real though!
Yep, the first thing I thought of was the delta-wye setup that Haas Automation uses for their direct-drive spindle cartridges to avoid needing a gearbox to switch between low RPM/high torque and high RPM/high HP.
Hobbyist EV conversions have been doing something similar for decades.
On method was to take two or more series-wound DC motors, couple them on the same shaft(John Wayland’s Datsun 1200 “White Zombie”) or with a belt drive(Datsun 280ZX “Silver Bullet” shown in the TV show Sucking Amps from 2004), and then use a series of contactors to shift the motors between series and parallel.
For a limited power input, this allows you to shift between high torque low speed(series) and high speed low torque(parallel), giving the EV a two-speed transmission without having a mechanical transmission present.
Great to read about innovation happening in the EV field, exciting stuff. Thanks for yet another interesting article Lewin and the Autopian gang. Vaugely recall this stuff from EE classes decades ago. Have ridden the Montreal metro which as some of the comments mention uses this tech.
Hyundai/Kia also equips Tucson/Sportage and Santa Fe/Sorento HEV and PHEV models with a six-speed automatic transmission, driven by the electric motor and augmented by the SmartStream ICE, in a full-parallel hybrid configuration.
Interesting ideas arise from a multi-mode electric motor and how that might scale out to extend range, or for specific applications as well.
Seems like a game-changer! Here’s hoping it actually is!
Very interesting! And good for Kia, I wonder if they’ve patented this and locked it out for anyone else to implement?
It’s OK, everyone else can just unlock it with a USB cable.
eh give it a few years, it will be like the transmissions. 8 and 10 speed motors will be the norm, but nobody will have adequate software to ensure the things don’t hunt and shudder trying to figure out what part of the motor to use.
It’s usually not possible to patent something so broad. As others have noted, this is used in other applications. A patent is usually limited to a specific method of implementation. Like this: https://patents.google.com/patent/US10283297B2/en
Good. It may not have been apparent by my comment, but I think it only helps everyone to be able to implement this.
Didn’t Toyota open up their hybrid tech to everyone at some point? Or am I having a brain fart?
Toyota has licensed their hybrid technologies to Ford, and Mazda and Subaru could possibly be in a similar boat with their CX-50 and Forester hybrids. However Mazda is different from Ford in that they are using a fully Toyota drivetrain (including the Dynamic Force engine), while Ford uses their own engines (Ford-Mazda MZR) while using Toyota designed or supplied transmissions, and strangely something related to the gas tank evap system. Subaru hasn’t released the details of their hybrid system other than that Toyota has some level of involvement. It’s also worth noting that Toyota has a minority stake in both Mazda and Subaru.
Lucid has a series of tech talks about building their cars. One is on the motor. I thought they did a decent jobs of explaining all the bits of a motor. It spends a bit too much time talking about how they are better than everyone else but still worth watching.
They did something with the rotor that really surprised me. Maybe it’s common but I hadn’t heard or thought about it. I won’t spoil it, but this queued up at that point:
https://www.youtube.com/watch?v=U7IHZxNC6hc&t=2980s
I remember hearing about one of the EV startups putting the differential before the gear reduction, it could’ve been Lucid or Rivian iirc.
It’s at least Lucid, that video is queued up right before they show it. It’s not just before the gear reduction. It’s literally in the center of the rotor.
Thanks for the link. That video is really impressive. I’ve seen the same facts in writing multiple times, but these guys are both enthusiastic engineers and expert presenters. I expect to spend several hours over the next few weeks watching all their videos.
I haven’t looked at electrical engineering stuff in over two decades (and I just did enough there to get a passing grade) but would it make sense once you have a bunch of connections and switches to try for other geometries beyond Y and delta in certain use cases?
I know very little about electrical engineering, but quite a bit about geometry. There aren’t a lot of geometric solutions to three straight lines that each connect to the other two. It’s a triangle and a Y.
There can be more phases than three, mainly for smoothness in power delivery (e.g., think about turntable motors), but it would come with significantly more complex control requirements, not to mention getting away from the 3-phase production volume of the supplier community. Since no one in the auto world even notices the minor cogging going on with 3 phase motors, smoothness (vs efficiency and power) is really not a selling point.
Makes sense, although I wonder if a hexagonal setup would work well for highway cruising as an extension of the delta setup.
I guess it’s one of those things that no one thinks is going to be better enough to justify the engineering, but if EV makers keep having to seek efficiency maybe they’ll play with it.
It’s important to distinguish between poles (of which a motor can have an arbitrary number, related to torque requirements and fineness of control, ie, a stepper motor in an old floppy drive), and the number of phases, which is almost always one or three, except in some very limited historical experiments with two-phase power.
The basic advantage of three-phase AC power with respect to motors is the ability of the stator to produce a ‘rotating magnetic field’ around the rotor. A single-phase, two-pole motor, by contrast, produces a static magnetic field that expands and collapses in tune with the voltage at each pole. Imagine trying to start something heavy turning only by pushing directly towards the pivot point – it’s impossible. So single-phase motors typically involve a ‘starter circuit’ that generates a secondary magnetic field less than 180 degrees away from the primary field.
3-phase power can also deliver three times the power of single-phase with, at most, twice the number of wires (2 wires for single or split-phase; 4 wires for a 3-phase wye configuration). And because of the gains in efficiency of the motor itself, less current is required and smaller wires can be used to carry it.
Now all they need to do is connect a relay to some kind of giant lever in the cabin to turn this on and off and let you pull it with a really satisfying thunk 🙂
Okay, I can’t edit this any more, but wanted to elaborate a bit, in regards to the hex-motor comment above – the relationship between motor poles and torque is that increasing the number of poles increases torque and efficiency to the detriment of speed. Essentially, the further apart the poles, the further that the rotor will travel for each complete AC cycle. The rotor will try to align with the closest energized pole. The closer the poles, the stronger the magnetic field at any given point in time – but the rotor has less distance to spin. The consequence of this is that the power supply unit has to alter the frequency of the supplied power to increase the motor speed, which can put strain on the power electronics. It’s counterintuitive if you’re accustomed to gas engines, where reducing the number of cylinders and adding boost decreases friction and inertia losses for a given gas/air charge. Anyway, this is long enough…….
Nah this was great to read, thanks!
Hahahaha
That would do it. 🙂
Great article. But it was kind of weird to hear how amazing Kia was until the end when we finally learned the name of the supplier (i.e., the actual designer and manufacturer of this motor). I get that it’s a Kia vehicle and most people haven’t heard of Vitesco, but the praise specifically for Kia’s genius w/r/t the motor was weird.
Also this: “Electric motors have been around for the better part of two centuries now, so you might think there’s nothing new left to discover about them.”
Come on. There is always something new left to discovery about everything. There is a shitload left to learn about (and improve upon) when it comes to electric motors.
That is a question I would like to know did Kia have any insight with the design of this motor, did their engineers work hand and hand work Vitesco engineers? Or did Vitesco do all the work?
I would suggest that Vitesco knew of the concept, but also figured out how to make it cost effective enough to sell. Then, they communicated this possibility to Kia, and Kia was smart enough to recognize the benefits. This really is super clever from every standpoint. And, as an engineer, I would gladly accept this if it was cost effective, which it was, otherwise this wouldn’t be used. It’s really a giant KUDOS to both sides of the equation, and a testament to how great of a team both must have to make this happen.
Vitesco make the motor, but the concept and intellectual property may well be Kia’s.
Sometimes Tier 1 suppliers come up with something clever and sell it to the OEM, sometimes the OEM does the clever bit.
It’s not weird to praise an automaker for a part on their car. It’s actually less common to see praise for the supplier, but I’m glad we did that here. As someone who worked in the auto industry, I’ve seen the reality: Most true innovation happens at the supplier level.
Fair. I suppose by “weird” I don’t mean “unusual.” I wouldn’t expect Car and Driver, for example, to focus on (or to your point, even mention) the Tier 1. I suppose I have different expectations of this site, since you guys delve deep so often. Either way, it was a great article.
THIS I expect is a Huge part of the challenge with evs from legacy auto companies. Legacy auto companies are Very mature and in their ice cars typically any innovation comes from tier 1 suppliers. Legacy auto likes it this way bc innovation can both be expensive And includes uncertainty.
In short ev tech. (Either existing tech. Applied to auto sector or brand new innovations), are scary and not what legacy auto typically is used to, so they all either wait for someone else to do it 1st or they wait to be sold on some new tech. from a tier 1 supplier, much better for the tier w supplier to take on the risk & uncertainty being the mindset.
Challenge is… the more that is outsourced the less actual differentiation value is created by the legacy auto company…
I was told there would be no math. (Maths for Adrian.)
I’m sure there’s a great technical breakdown in here but after a bit my eyes glazed over and I am just going to go with “that’s cool.”
I largely glossed over the math as AC electricity specifics is a bit much for the general audience. I’m a embedded/DC/logic person, but I can follow along with an expert source
Anyone else reminded of a flux Capacitor?
How else are you going to efficiently convert those 1.21 GW of nuclear or Mr. Fusion power?
But not so efficiently as to incite flashover…
this is really fascinating and well written! It’s great to read about a manufacturer actually making useful innovations in EV tech.
Anyone know if this motor design is common to all EV9 variants? The rear motors have 3 different power configurations (source: 2024 Kia EV9 Specifications (kiamedia.com)) but I’m curious if that’s due to different calibrations / battery configs, or if there are different motor designs.
The RWD short range strangely makes more power than the RWD long range version (maybe due to higher battery pack voltage on the shorter-range variant) while he RWD long range appears to be more efficient, even though it’s >200 lbs heavier. The AWD versions have less rear motor power vs. the RWD versions, but I’d assume that’s just due to how they split power between the two e-machines.
“Game Changer” is the new “GOAT”, apparently
They’re all “Disruptors!”
Strange how you can innovate when you are tying yourself up in trying to develop your boss’s vanity project.
The thing that’s gotten me about the CT is that it’s barely relevant production tech to the rest of the lineup. It’s crazy to think they probably would have been better off dumping a bunch of money into the Roadster
More like that supposed $25k EV. But it would be interesting to see what they would actually do with the Roadster when they remove all the vaporware features.
Funny that I went to the VW projects article on the Veyron and Phaeton. Not the same, but I bet they rhyme.
Very cool Lewin! Seriously nerdy, which is par for Autopian.
One thing I still don’t get is why you can’t just hook an electric motor to a manual transmission for added acceleration and efficiency.
Modern EV motors already do so well on both fronts that any potential gains are going to be fully offset by the added weight, complexity, and drivetrain losses.
You can hook the motor to a transmission, it just doesn’t result in an increase in efficiency. Because the motors can already operate over such a broad RPM range, and the torque is all there at zero RPM, a transmission mostly just adds weight and resistance to the system. However, there are a few 2 speed transmission EVs out there, not like this, but actually changing gear ratios. I believe the Taycan is one of them.
Would like to know how this would compare to say a geared turbofan engine on jets. I’d assume that since you aren’t dealing with issues like the speed of sound, it just doesn’t make sense in the automotive space.
You can, but this is basically doing the same thing “solid state” with no added moving parts. Why add more mechanical complexity and weight when you can achieve an even greater result with semiconductors and 100+ year old AC motor technology?
Lots of restomod EVs like old Beetle EV conversions bolt an electric motor directly to the original manual transmission. You don’t need to use the clutch, and you can typically leave it in second gear most of the time (since the electric motor can rev so much higher) unless you really want to row your own.
Another thing not mentioned is the required strength of the transmission. With EV torque being so high from a stall and generally in a heavy vehicle, the forces on the internals of even a mid range EV are a lot higher than most ICE, so the transmission would have to be very strong, add even more weight, cost, presents a packaging issue (assuming just one electric motor, never mind multiple motor configurations), and is an expensive potential failure point.
Technically, at startup the torque of an electic motor tends towards infinity… as well as current going through.
the amount of torque would wreck any transmissition.
That’s the basic reason for the wye & delta configurations in industrial motors. The wye configuration reduce the amount of current to a manageable level, once the motor has started rotating (generally after a few seconds) it can be changed to the delta configuration.
It even predates the dawn of IGBT.
30+ years ago Elecrical engineering courses taught you how to cable an electri motor with wye and delta modes controlled by a timer driven set of relays of the motor.
(and making a cabling error usually resulted in magic smoke being released by various cables.)
Formula E is an electric racing series where both speed and efficiency is a priority, and the tracks they race don’t have long straights or very high top speeds. After initially using a spec chassis and powertrain with a 6 speed transmission, teams were allowed to develop their own motors, inverters and gearboxes starting with the second season. The teams quickly started reducing the number of gears, and everyone had converged on using single speed transmissions by the 4th season. They may not even use the wye/delta style of motor since they don’t spend enough time at low speeds, but I don’t know for sure.
As the Porsche Taycan demonstrates, additional gears are only really necessary if you want to push top speeds higher, as most EVs top out in the low 100s.
I would argue there is no reason for anyone ever to have to go over 100mph, anywhere. And, companies designing past this speed is pointless and wasteful. The only reason is racing, or the autobahn. What percentage of the population would use any of those speeds on a regular, safe environment. 1/1000?? Maybe? And, please don’t follow up with “I drive over 100mph all the time, and I’d use it.” No, you don’t, or you shouldn’t.
Very clear, plain but engaging writing about one of the harder topics in electrical engineering, you’ve done it again Lewin!
If you’ve ever ridden an older SkyTrain in Vancouver BC (or I think the Detroit People Mover) you can hear and feel the linear induction motor “shift” between modes kind of like this.
Any word on what exactly this translates to in terms of an efficiency increase?
You would probably need Hyundai or Vitesco to publish something on this to get a feel for it, but as a very basic ballpark idea (this is probably way off), the most comparable vehicle I could think of would be the 2025 ID.Buzz, which is about 10% worse MPGe in the city compared with the Kia (comparing RWD trims). Comparing AWD trims though the difference is less than 5% so who knows how meaningful this all is (also, it’s not clear to me if this same tech applies to the front axle drive unit, which might explain the more pronounced AWD efficiency drop, compared with VW which sees very similar range/efficiency between their RWD and AWD variants for the ID.Buzz). Again take all this with a grain of salt, the nifty motor design is only one piece of what I’m sure is an enormous efficiency puzzle.
There really aren’t many other 3 row SUVs that are comparable… R1S is heavier, less aero with all that ground clearance, and presumably has more rolling resistance with a bigger wheel/tire package, and Tesla Model X is sleeker, less spacious, and maybe has some magical Tesla special sauce (or juiced numbers) for better MPGe. Volvo EX90 numbers haven’t hit the EPA website yet.
I don’t know many of the factors that go into this, and as Olesam said you’d probably need the manufacturer to publish some kind of torque/RPM or efficiency/RPM graph to get a good idea on things. But we can probably make some broad conclusions based on what they said:
— If the motor’s gear reduction ratio is kept the same compared to a conventional delta-only motor, the efficiency gain from the wye/delta motor will only come at low speeds like in the EPA city cycle, and should barely affect the highway ratings.
— In cases where the gear ratio was made shorter as a compromise to make up for a delta-only motor’s worse low RPM torque, a wye/delta motor can utilize the wye mode’s high low RPM torque to make the gear ratio taller, allowing for the delta mode’s efficiency sweet spot to be at higher speeds, potentially improving high speed efficiency. This might improve EPA highway ratings, or it might only improve real-world scenarios like Car&Driver’s 75mph range test, since the EPA test cycle doesn’t exceed 60mph.
— Performance EVs might stick with delta-only motors since low speed torque and efficiency is not a priority. They already have enough torque to be traction limited at low speed anyways, so there’s no need to for the additional costs unless the efficiency is desired. However, I don’t know how the wye configuration’s current limiting properties play a factor here (could the lower peak current allow for lower rated components to be used?).
I’d dearly love to know but I couldn’t say specifically. I suspect it could be a big boost to highway range, though, somewhere that EVs usually suffer.
The Montreal Metro has motors that switch between wye and delta windings to get extra power to move from a stop.
Between the sound of the motors during the switch and the noise the power converters make under the different loading loads leads to the unique do-do-do sound:
https://youtu.be/HBxbX6RbovY?si=8v-ZieC8TMFGALFM
It became so engrained in the Metro users heads that the newer rolling stock has a fake noise inside and out to emulate it. We users learn to listen for it to figure it if the train is leaving and stop running for it.
Wait! I thought Tesla was the one and only innovator here, with King Elon himself designing the motors. Sarcasm aside, this sounds like a neat piece of engineering and manufacturing. Hopefully, the cost cutters don’t get too far in and ruin the design and build.
“Great, now which parts can we replace with plastic? All of them?”
-procurement