Tesla is finally shipping and installing the LED light bar accessory it showed in the original concept. The brand has to apply “blackout film tape” over the light, and Tesla won’t connect the light for owners for legal reasons. Another thing Tesla service center won’t be able to do? Easily remove the light bar once it’s installed. That’s because it’s glued into position.
Offhand, that might sound like a terrible idea as AutoEvolution initially pointed out. And yes, it is a bit strange considering that this is an accessory and that lots of similar light bars bolt into their intended application, but at the same time, the commentary on the glued-in lightbar has proponents on both sides.


Let’s jump into it. Here are some pictures of the bar itself.
You can see the black tape there, which Tesla mentions in its installation instructions thusly:
The blackout film tape must be installed on the lightbar prior to delivering the vehicle to the customer. Only the customer or a third-party entity is permitted to remove the blackout film tape.
Installation of the bar requires cleaning and prepping the windshield surface for adhesion:
Then, after adding primer, an installer lays down urethane adhesive between the lightbar and the windshield.
“Apply masking tape across the off-road light bar to secure the lightbar to the windshield. Allow the urethane to fully dry,” says the instruction guide. Tesla then keeps the vehicle overnight so that the adhesive can cure before the customer drives away.
Actually wiring the Cybertruck lightbar isn’t something Tesla can do, with the company saying in its lightbar-installation instructions:
The Tesla Lightbar for Cybertruck is designed only for off road use. Tesla by law cannot install the lightbar electronics and configure the vehicle for lightbar control.
Still, Tesla does show how to route the lightbar wires into the cabin; this requires pulling up some trim and holding it with a hand-pumped air bag:
Â
And voila: You have your light bar.
Of course, if you want it to, you know, actually work, you have to have a third-party handle it. Tesla has instructions for them, too, and they involve installing some jumper wires in a fairly, uh… simple way — stripping wires, soldering, and installing heat shrink:
Anyway, back to the glue.
The design of the Tesla Cybertruck doesn’t have any real provisions for a lightbar — no place to bolt to, no latches or fixtures. I suppose you could drill into the truck and install rivnuts like some Toyota Tacoma owners do when mounting a lightbar:
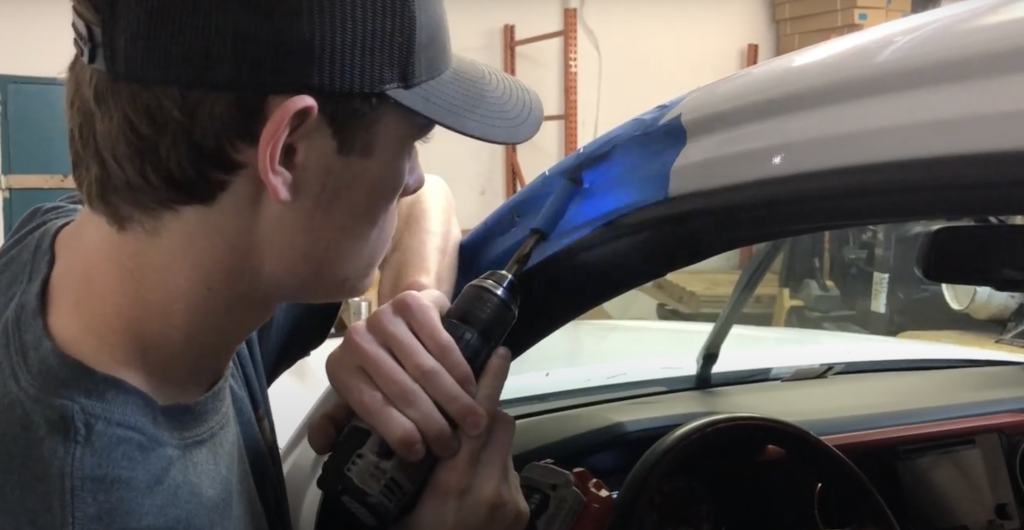
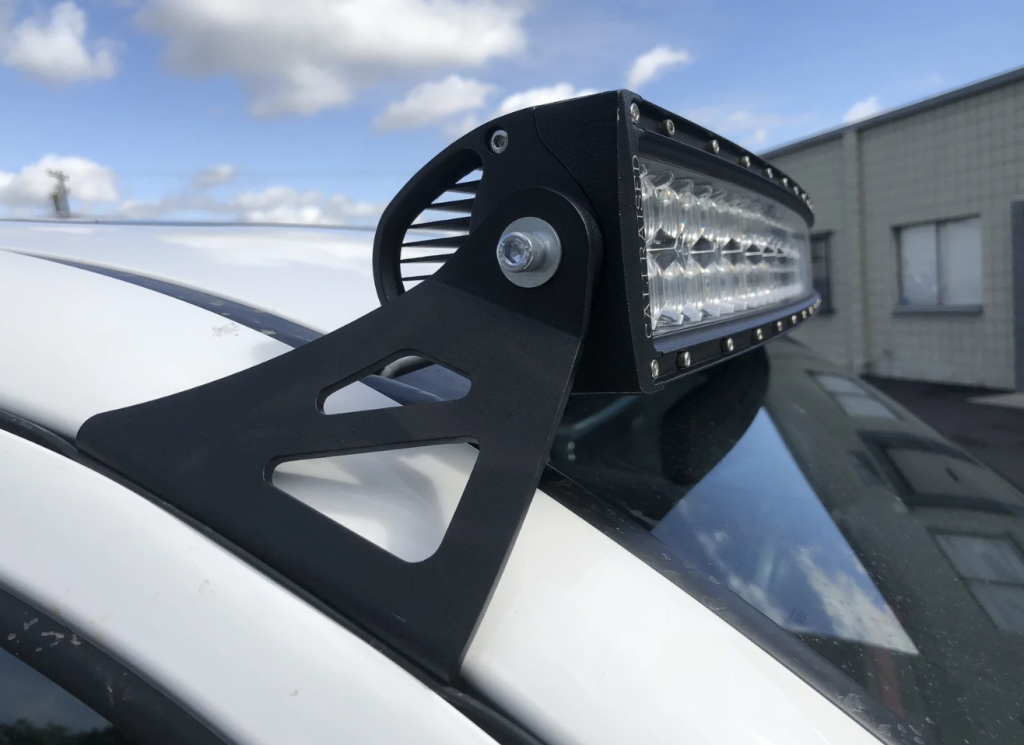
Or you could do what Tesla did and use an adhesive. The downside is obvious to anyone who likes to change up their accessories regularly. Removing this thing is going to take time and effort. Based on photos of the urethane in a calking gun, this appears to be a Dupont Betaseal product. If correct it has a tensile strength of over 700 PSI and is waterproof, too. It’s used to keep heavy windshield bonded to metal cars even in extreme crashes, so it should have little trouble keeping a relatively lightweight lightbar bonded to a windshield.
The upside of the installation method is that it gives the truck a seamless/aerodynamic look, it seems like it’s easy enough to do, it should be more easily reversible than drilling, and, with the right prep, it almost certainly won’t fly off while you’re cruising down the highway in traffic. Still, replacing it or the windshield should the original get damaged would be a lot harder than just unbolting that Tacoma lightbar above.
This is a good time to discuss just how strong modern automotive adhesives are, because why not? A decade ago, their use was only just becoming more and more important as cars became more complex. General Motors has used structural adhesive on cars like the Chevrolet Corvette and Cadillac CTS since 2013. The next year it started using them in full-size pickup trucks. This article surrounding the BMW i3 provides a perfect example of that. Adhesives provide a lot of benefits over other methods of adhering one thing to another. Here’s a video of exactly that process.
In the case of a car like the i3, adhesives allows engineers to join pieces of different materials like carbon fiber to aluminum or steel more easily and without as many rattles, squeaks, or stress points.
An article on GardnerWeb.com also highlights another benefit.
One of the things that is somewhat simplified in terms of assembly is when there are mixed materials—such as steel and aluminum—the joining can be performed with an adhesive. While these materials can be welded, it is trickier than when it is steel-to-steel or aluminum-to-aluminum. And while they can be readily fastened, there is the issue of galvanic corrosion that can result at the interface of the materials; the adhesive forms a corrosion barrier. One vehicle that has a combination of two materials is the Polestar 1, which brings together composites and steel. There is some 50 meters of adhesive used in the bonding of the vehicle body.
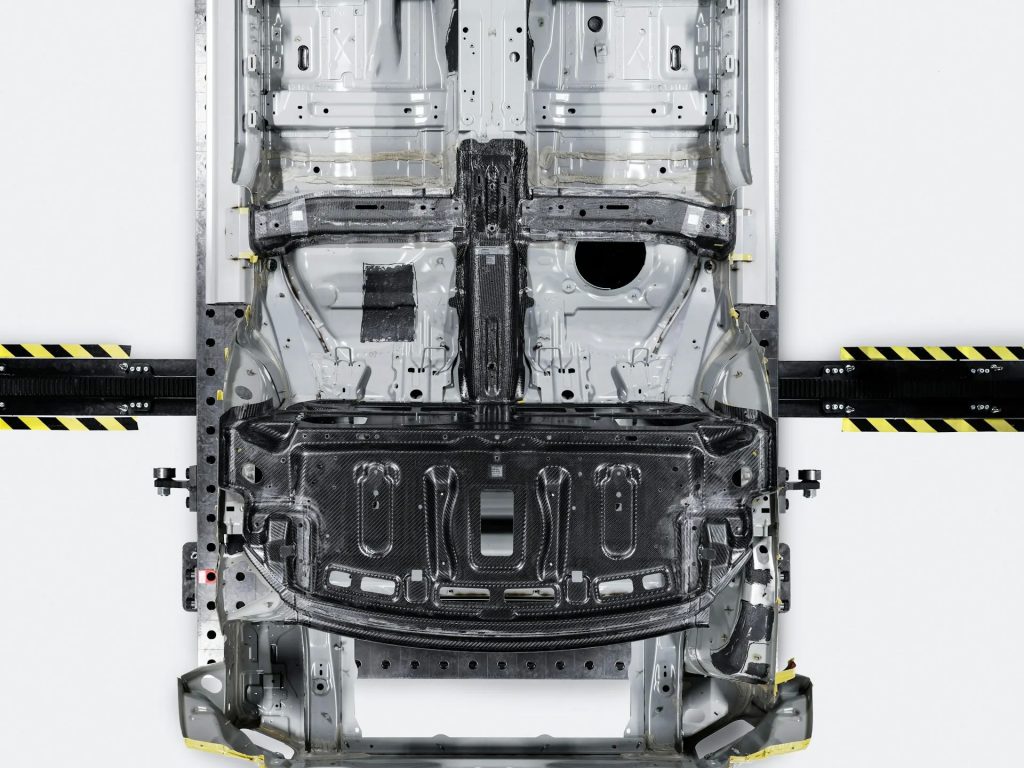
Last September, Toyota mentioned the additional 108 inches of structural adhesive it used on the GR Corolla over the regular people mover. When the latest Subaru BRZ arrived the automaker pointed out that it was now 60 percent more rigid laterally and boasted a 50 percent increase in torsional stiffness.
All of that is to say that adhesives have been used in much, much more critical applications than a lightbar on a windshield. Customers who plan to keep the bar installed for good shouldn’t worry too much about it falling off if it’s installed right. I’d be more concerned about the windshield cracking.
When it comes to removing the bar, some solvents, a few feet of fishing, maybe a few razor blades could come in handy — windshield repair specialists deal with this all the time, so it shouldn’t be impossible.
The splicing strategy’s sketchier than the mounting method, I’d say. Why soldering instead of a marine-style butt crimp with heatshrink and sealant? Would be more resistant to both moisture and vibration.
That lightbar will probably not survive being removed from the windshield. so a windshield replacement will include a new lightbar, probably cost as much as a Fisker Ocean
I was coming here to say this as well. The billboard of a windshield, should that ever get cracked/chipped/break, will require a new light bar too.
Or when some of the individual LEDs inevitably fail…
How fun would that be to explain? Well I need a new windshield because I took a stone coming down the highway and it broke my light bar
As stated, structural adhesives have been around a long time and are used heavily in modern vehicles for good reason. Most assembly lines putting together chassis parts with adhesives use a cold plasma pre-treatment step to raise the surface energy of the two parts being bonded and this creates a much better bond.
I know GM uses it prior to gluing windshields and rubber door seat parts.
I doubt the light bar adhesive will ever have an issue, but how reliable the bond is will be entirely dependent on how well the surfaces are prepped. With Tesla, that sort of thing seems to be very hit or miss.
good thing it’s the customer or a third party is doing all the work. 🙂