Last night, a reader and I did some high-quality wrenching on my 1954 Willys CJ-3B ahead of my wedding next month, and something happened that has ruined far, far, far too many days in my life. So here I am venting, and giving you, too, an opportunity to lament your worst wrenching annoyances.
This is something I’ve had trouble with for years, especially since I spent the better part of a decade in Michigan: Brake fittings seizing to brake lines.


If you’re unfamiliar, with what I’m talking about, you see this brake line fitting slipped over this brake line?
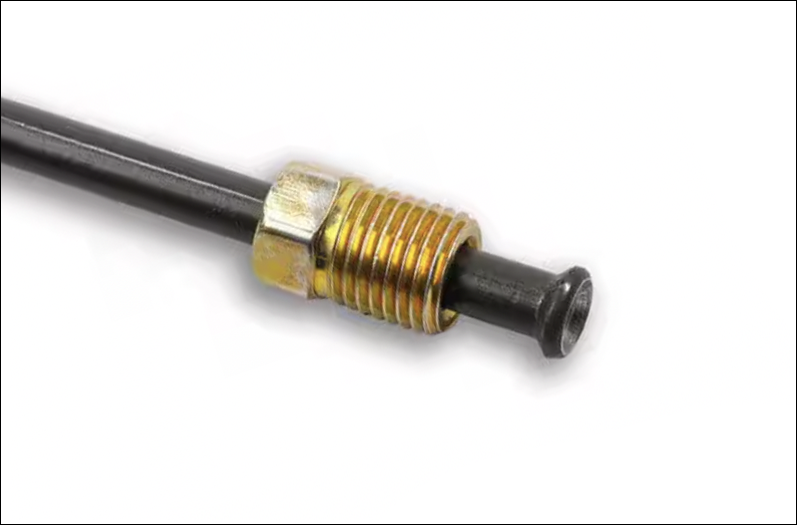
Its job is to squeeze that flared part of the brake line against the inverted flare in the master cylinder or wheel cylinder. Here you can see where the fitting threads in, squishing the flare you see above against the conical surface you see below:
Notice in the photo of the brake line that the fitting is separate from the line — it just slides over top. This is important, because you don’t want to twist the brake line, or it will brake. So when you tighten that fitting in the master cylinder (or wheel cylinder like the one shown directly above), the brake line doesn’t spin at all, it just gets squished against that conical surface to create a seal.
The problem is that those brake lines often will seize to the fittings, and if that happens, you aren’t able to loosen the fitting from the master cylinder or wheel cylinder without twisting, and thus shearing, the brake line. The result? You have to replace the brake line, which is a huge pain in the butt.
I’ve had various levels of success using heat and a vice grip to get the brake line to stay in place while I hold the fitting, but like last night, it doesn’t always work, meaning the small job of replacing my master cylinder just became a significantly bigger job.
D’oh!
This is among my least favorite annoyances that occur while wrenching. I also hate breaking bolts, to be clear, but at least with bolts you can heat them up cherry red, get vice grips on them, and be a bit rougher without worrying about squishing them like you do with a brake line.
Anyway, let out your wrenching frustration in the comments!
TImeline disruption to parts being incorrect or in the wrong box.
Reman cylinder for your Z? Oh, that’s actually from a Sentra; someone ‘upgraded’ their Sentra and returned that core. Even if you catch it at the counter, it ruins your timeline.
Broken lines are no fun, but the loss of brakes is even less fun.
Please tell me you are upgrading to the dual-circuit master cylinder.
I mostly get annoyed by the shoddy work done by previous owners.
Sometimes rust will get me really annoyed if it makes life really hard.
The rest of it is just solving problems; and that’s what I enjoy about wrenching on stuff.
If the fittings are stuck on the lines, they probably need changing anyway…
I like making my own new brake lines, takes some time, but it’s rather cheap in materials and easy to get right.
Oh and for the question, for me it’s when you just want to be a decent guy and tighten things properly – and then they break!
I hated brake lines when I broke one on a Sunday that I needed to get me to work on Monday.
I love brake lines when I have the time to do them the way I like to. One of my favorite jobs was completely replacing every bit of the brake system in a ‘52 Pontiac Chieftain.
My fondness for tubing became relevant in my current job where I get to run refrigerant piping
Lower end of the rear shocks on my Mazda 3 attach to the knuckle with a stud in the knuckle. The stud is M10x1.5 threaded into the knuckle. The strut bushing slips over the stud, and a nut holds it on.
However, the stud rusts and rust-welds the shock onto the stud. Even once I cut the nut off, the shock still wouldn’t come off. Maybe I can unthread the stud from the knuckle? Nope. The end of the stud is a 6mm external hex, which quickly rounds off dealing with such rust.
I had to remove the entire knuckle from the car, on both sides (!), removing 5 or 6 other bolts, cut off the shock and use a pipe wrench and a torch to finally remove the ruined stud. This turned a 60minute endeavor into a week long slog of grinding, cutting, and ordering new bolts.
I replaced the easily rusted stud with a Grade 8 yellow chromate bolt, with an actual Hex head equal to the torque required. And lots of anti-seize.
fixing something and then another thing breaks the next day. That’s the WORST. your all excited about your finally non broken car and then WHAM now it’s broken again!
I hated doing the front struts on my Mk V Golf. Instead of studs with nuts, VW used bolts through the towers into threads in the strut bearing. But whatever those threads are in spins, so turning the bolts left does nothing.
I ended up breaking out the Sawzall on that SOB.
I’m getting ready to do this on my Sportwagen (same exact set up) and really not looking forward to it. Replacing a coil spring in the rear was a nightmare, so I know this is going to be worse. What’s funny is that I did the front struts a couple of weeks ago on my son’s Explorer, and while the parts weighed loads, I don’t know that I’ve done an easier job on a car. Take off 6 bolts, swap part, put 6 bolts back on. It was so stupidly easy that it made me finally understand why you would buy an American car- sure parts will break and wear down, but 15 minutes later you have a new part installed and you’re ready to go. Brilliant.
Oh yes every other car I’ve done struts on was really quite easy. My wife’s Sienna was a little silly because I had to remove the wipers and cowl piece to get at all of the nuts.
I’ve really only ever worked on VWs, so the idea that things could be easy was a revelation. Everything I’ve done on that Explorer has been dead simple, and it just kind of baffled me why everything else I’ve ever had to do to a car was so absurdly complicated. My neighbour had to fabricate a tool for me to change the thermostat so I didn’t have to put my car in the ‘service position’, which is VW for ‘remove entire front of car’. It’s just crazy.
This is the miracle of VW ownership: it’s like Stockholm syndrome but automotive.
I hate how correct this take is
you mean you don’t have to remove the intake manifold or the front crossmember just to replace the oil filter???
Ask me how much I had to remove to do the timing belt, good lord
I had that on my mk4 and got lucky with a spark plug socket that fit over the outer bolt and was sized to allow a wrench on the outside of it. I then ran an allen key through where you normally put the socket and used that to tighten the inner bolt.
https://cdn4.pelicanparts.com/techarticles/Volkswagen_Jetta_MkIV/137-SUSPEN-Front_Strut_Replacement/images_med/pic09.jpg
Ford “quick disconnect” fuel lines annoy me no end. When my truck need a new fuel sender disconnecting the fuel lines took a trip to the parts store to get the good anodized aluminum tool because the plastic tool only released one of the two fuel lines. Dropping a 2/3 full 25 gallon tank with a transmission jack was the easy part.
I’d rather splice a fuel line with a janky plastic coupler that deal with quick disconnect fuel lines. They are such a pain.
Especially frustrating since they used to use these extremely simple clips that if you broke, didn’t matter because they came new with the new fuel filter.
When the parts from the parts store look right visually, but you find out they are the wrong ones when they won’t fit.
Why don’t the manufacturers use banjo bolts? On my motorcycles they use them on the master cylinder end. I’ve never had one seize.
Cost. Not just because you’re adding more parts, but also because to get a banjo to seal you need a flat, smooth surface machined on to the master cylinder that’s perfectly perpendicular to the thread.
You’re also increasing the number of leak paths from 1 (the crushable pipe flair) to 5 (each side of both washers and your pipe fitting).
Where I live we thankfully don’t have to fight rust so I’ve never done it, but is there a reason not to put a little anti seize on the end of brake lines/fittings?
Holy christ. I actually had to *drill holes* to access one of the unlock tabs on the Z4 headlight assembly. It was horrible.
Our Kia Soul requires removing wheel and liner to change the bulb in the fog light. Not bothering with that.
When you drop something, but it never hits the ground…
It’s always lodged someplace dark and inaccessible by hands. If you try to use a magnet, that’s when you discover it’s either nonferrous, or it’s completely surrounded by ferrous metal, so the magnet just sticks to that instead.
And of course, whatever it was that you dropped, it was the last one. The last one you needed to install, maybe the last one the parts store had, maybe the last one in existence. It’s just the last one.
*clang sound in engine bay*
Nearby radio: “This just in, no 10mm sockets are in stock in any stores for 500 miles away from [exact town you’re in]. That’s right [your first and last name], specifically, that 10mm socket that just fell into the infinite void in your engine bay, is the last one for 500 miles. Except for these ones owned by [several specific people you hate].”
And Amazon is completely out, the factory in China burned down, and all your imperial sockets in a somewhat close size are missing too
Next to nearest imperial socket: down this path only madness and ruin lay. That’s how my neighbor turned a 17mm into a 9/16 into a fine, round bolt.
Came to comment something like this, and yes the drop no concrete plonk sound is a guhhhhh.
When I had my Mk7.5 Sportwagen, I had installed an aluminum skid plate, and bought an oil extractor for easy oil changes, so I’d never have to get under the car. It worked great! Right up until my hand slipped and dropped the oil fill cap that got stuck on said skid plate. I wasn’t pleased. I got it out, but many 4 letter words were said that day, and I had to jack up the car anyways.
My Lotus Elise had a aero panel under the engine. If I dropped anything at all I had to take the floor panel off.
However, the floor panel also covers the rear jacking point, and is held in place by the diffuser which is bolted on with a dozen tiny bolts, all of which has to come off without jacking the car up.
Bastards.
Having kids. I barely have time to keep my regular cars doing good, let alone work on my old Lincoln.
Just this morning; driver’s side headlight is out. Unfortunately, modern crash structures, and I only have one wrist per arm. I am happily paying someone to actually do it tomorrow.
I don’t like your attitude
I agree. This shouldn’t get him all out of joint.
Wow, some people will get all bent out of shape over nothing.
Needing a unique tool and then not being able to find a reliable version of that tool.
I bought my Mini Cooper used and it had aftermarket wheels with Bimecc 10-spline lug nuts. There was no lug bolt key/socket with the car, so I had to buy one. Apparently Bimecc is the only maker of the 10-spline design and they make shitty sockets. Any version I found included reviews that the sockets split the first time the reviewer used them.
So naturally, I just bought the best reviewed version I could find on Amazon. Got the tires off for rotating without issues. I was extreeeeemely fortunate that I got all the tires bolted back on before the socket split on the very last bolt. I was using a torque wrench, so I know I wasn’t being careless on the last one and over torquing. But damn, that was close.
I have not found these stupid keys at any brick and mortar store, so I have to buy it online. If I was smart, I would have bought replacement hex lug bolts. Next time I will.
My used Kia came with aftermarket lock nuts and at least has the key included. Replaced those with standard nuts when I put snow tires on.
Also the joy of ford 2 piece nuts. The ones on my mustang lasted 8 or so years before I tossed them when I struggled getting one off.
Ford is not the only one. My wife’s 94(?) Chrysler LHS had those 2 piece, swelling lug nuts. Of course no socket fits them, either 2 big or 2 small.
Two things:
1) Finding the engineers designed a part that requires a highly specialized, dealer only tool for no reason other than to frustrate home wrenchers.
2) Breaking a part that is expensive or worse, unobtanium. At least most brake lines are dirt cheap and can be easily sourced even if they need a bit of customization.
Edit:
OK three things:
Finding the guy who was there before rounded off every single hex because he tried to get away with using standard tools on a metric car (or vice versa). Or forced a coarse threaded bolt into a fine threaded hole. And of course locktite or grease being an extra step never happened so now add rust or galvanic corrosion for extra fun.
It’s not so much of a problem now but back in the day I ran into it a few times.
Thanks DAD!
Damnit, now it’s FOUR things:
Haynes/Chilton manuals that glaze over the hard stuff or leave out key details. Like DRAIN THE TRANSMISSION OF FLUID BEFORE REMOVAL!!. Because when you tilt the transmission to get it out all the oil will otherwise get dumped out the driveshaft onto your head.
Oh and those old cars used oil made from sperm whales. And that shit does NOT wash out! Which my friends is why Cheap Bastard had to go to school the next day with a head full of greasy, frizzy hair smelling like a rotting dead whale.
My manuals are filled with margin notes I make to try to capture all the stuff that went wrong/wasn’t covered in any detail. I even draw little triangle-exclamation point symbols like in owner’s manuals to remind me of something really critical I learned the hard way. Also, lots of notes on which size wrench to use, as the manuals almost never cover that.
One of the reasons I resist buying electronic versions of them, no matter how much Haynes tries to get me to do it.
“One of the reasons I resist buying electronic versions of them, no matter how much Haynes tries to get me to do it.”
Counterpoint: You might be able to convert those manuals into an editable format and write in the corrections directly in whatever font or color you like.
Most of my marginalia in my manuals is literally written in blood.
It’s a fair point and I probably should try one out, just to see how I like them. I guess I just enjoy the tactile nature of the physical books and being able to quickly leaf back and forth.
But I do use a hybrid approach as I think a few others here do, utilizing Google Keep as well; I like its simplicity and it’s great for notes on things where you end up having to go to the autoparts store during the course of your repair or where you might get delayed.
Like I currently have an extensive write-up with pics on the correct order in which to reinstall the the underbody paneling on my Porsche. I haven’t touched it in months, and I’d have forgotten if I hadn’t put it all down at the time.
Another advantage to digital format: Imbedded pictures and video.
Disadvantage: using my phone or tablet with greasy gloved hands isn’t ideal.
Paper wins this one when you’re in the middle of a job.
So print a copy. And when that printed copy gets too greasy to read anymore throw it out and print a fresh copy.
As a San Franciscan, you really should have known better than to put it quite this way.
In the olden days, I’d photocopy relevant sections of the Chiltons, cut out the pieces I needed and arrange them in those plastic page-protectors. In slightly more modern times, part of my payment for doing an IT guy’s clutch was an old laptop running Windows10 solely for the Mercedes Workshop manual. I covered the old clicky keyboard in Saran Wrap before each procedure
Chilton manual has bitten me in the ass more than once!
One, what you describe with the tranny. Removing a manual 4 from a Datsun 510 sedan to rep[lace the clutch, I figured that the tranny couldn’t weigh more than fifty pounds, so just got under there on a creeper and went to lower it to my chest. Twenty-year-old transmission oil not only stinks, but the stink never washes out.
Two, Chilton never mentioned that the chain tensioner for the 1600 OHC of the aforementioned 510 had to be blocked out before separating the chain. My simple afternoon head gasket job became a week long odyssey of cursing and improvising how to get that chain back from the depths of the housing without pulling the engine–not an option at the time.
I hear you. Most of my HS friends were into 510s.
“ 1) Finding the engineers designed a part that requires a highly specialized, dealer only tool for no reason other than to frustrate home wrenchers.”
It’s never just that reason, although it is fun.
Twice now I’ve designed a system that needs a special tool. Once because using a standard socket would have required hundreds of thousands of dollars in tooling (so far zero complaints on the internet, and I do keep checking), and once because it was a unique assembly that needed an alignment jig to put together right (the tolerance stacks were just too big to have the parts self align).
I designed the jig to be a flat symmetrical plate with two slots in it, so it would at least be cheap, and easy to copy.
Well Honda didn’t get your memo when they designed the front ball joint on the Gen7 Accord to be 0.5mm thicker than the maximum span of a standard Autozone ball joint separator. Instead Honda makes tool 07AAC-SJCA120 for $500 IF you could find it. Today its not so hard or so expensive, but years ago this was dealer and specialty shop only and not available to purchase or borrow locally. To add insult to injury the Honda tool looks EXACTLY the same as the standard tool.
I can’t imagine that extra thickness on the ball joint did anything but demand that tool. Certainly other cars did just fine with joints that fit the tool.
You nailed it. Screw specialty tools.
Although… My father is a tech and he has a bin full of specialty tools for GM cars. A fun game is to point at one and ask “what is this”. The answer is usually a 10 minute story about how this one car with a specific engine and transmission requires this specific tool for exactly one thing and that after trying 100 other ways with normal tools (usually some combination of at least 3 other tools but always including vise grips) he broke down and bought it, usually from the Snap-On tool dealer at lunch in a fit of rage.
At least I have access to those specialty tools, but it usually means leaving the car sit in parts fwhich is no bueno when you have to go drive to get the tools.
Damn, you are making me feel bad – while not due to using the wrong size wrench, I did a bit of corner rounding on the rear caliper bracket bolts on my G37x. Before doing this job I had ordered some new caliper bracket bolts – but I ordered the ones for the front because these were the only ones available and I guessed they were the same as the rear bolts. Now I am debating if I should go to the dealer and get replacement bolts – but the car is 15 years old with 120K miles and this is the first time these brackets came off – you can replace the pads without taking off the bracket, you only need to take these bolts off if you are replacing the rotors. I did replace the caliper pins, which O’Reilly’s had in stock. So have I made the next owner’s life more difficult or should I not worry about it because at 30 years old and 250,000 miles is it likely this car will go to the junkyard before these bolts have to come off again?
Tough call. I guess it depends on how much those bolts are and whether you can quash that guilt.
Finding out what you planned on doing won’t work. The older the car, the more likely you are going to find something you don’t expect. Ends up you either don’t have the right tools or parts, completely derailing the project.
Older cars sometimes it’s just lack of good documentation on what was done with year to year changes of available options. But it could also be due to a prior owner changing the part once already with a different one.
Either way, stops the project in it’s tracks until you can come up with a new plan/tools/parts.
I’ve been told “always try and undo the hardest bolt first”. That way, you’ll have all the tools on hand for the easy ones or you’ll know that you’re going to need a different tool, but won’t have to put al the easy bolts back in.
I experienced this changing injectors on my 914. One of the four had been rewired to a different connector than the other three. Argh! I made a short inline adapter by splicing together the appropriate parts from each type.
Cross threaded bolts or nuts in impossible locations. Every other fastener except the most inaccessible location has been loosened. That last one….”Bleep, bleep that bleeping bleep!” My tap and die set has saved my tail enough to make me forget how much it was. Whatever it cost, it was totally worth it.
What I’ve found is to always loosen the hardest one first so that the easier ones are still holding the pieces together, and install the hardest one second it third but before the other fasteners are fully tightened to give you some wiggle room. Doesn’t help if previous repairs damages something, but it does seem to keep me from doing it myself
”you don’t want to twist the brake line or it will brake” classic!
I can’t decide if that was intentional.
It will arrest all progress in the repair job, thus braking!
And if it breaks, then it won’t brake.
Sheared off a total of 4 head bolts in one wrenching session on my Olds 442. Of course it would happen on a weekend. Learned how to use an extractor once the stored one on Monday. Great fun. Also snapping off bleed screws, and brake line ends. Then discovering the brake lines were all so rotted they had to be replaced.
Know what’s worse than a brake line fitting seizing? Finding out that no one in this country carries that oddball British thread fitting last used on a production car in 1973.
Yeah, we used to use inches back then, sorry.
Worse than that… BSPT or 3BA or something like that. Not a UNF or UNC.
https://britishfasteners.com/threads-ba?srsltid=AfmBOoq7IPpqRpezKu9G6aMay82yu96G9KjDIrJeU37FN11csutXArvY
This seems to becoming more and more common, at least in my experience: aged plastic parts held on by clips that invariably don’t survive removal. The functional element of whatever the part still works fine, but there’s now no way to keep it where it belongs when you put it back.
Feelings range from annoyed at having to replace an otherwise working part to dejected when it’s some piece of unobtainium trim or whatever, even if you’re the only one who’ll actually ever know.
Those half-done repairs bother me the most, where functionally it looks ok but I’m the only one who knows it wasn’t completely fixed or can’t be undone or whatever. Cognitive dissonance is my favorite!
And I’m the kinda guy who’s doing his best to learn to live with things not being perfect, after too many times of trying extra hard to get it just right, only to irreparably damage things and then being upset I just couldn’t leave well enough alone in the first place.
Plastic fasteners and clips are way too fragile in most cases that I’ve encountered. I have never figured out if they are actually engineered/designed to be one time use only or if that happens with age.
One time use is very difficult to engineer right. Too fragile and it breaks during assembly, too stiff and something else breaks. Most of the time it is designed correctly for snap fits, but it is hard or impossible to operate/manipulate the snapper in the correct way after installation.
Aging is a big problem of plastics. I have headlight connectors on a 20 yr old volvo that will crumble in your hands when you have to install a new headlight bulb.
Early Subaru connector plugs, and especially vacuum fittings were really bad about falling apart after a few years under hood. I learned early to first try on a parts car—and to always cut vacuum lines off anything plastic
My Polo has a brake pad warning sensor (basically just a wire behind the friction material, so that if you go through the entire pad, it’ll break the wire and trigger a light), on a single brake pad, on a single wheel.
Nevertheless I went to replace it, and of course the plug on the wiring loom shattered to bits.
I just chopped it off, soldered the wires together, and tied the wires up out of the way. It was a useless system anyway.
Running 80s Subarus in the 90s & Aughts, I learned to try procedures involving finicky bits in the junkyard first so I a) broke shit that wouldn’t stop me driving mine and b) figured it out—with the bonus of extra bolts & fittings
The corollary to this is the intense joy I felt when I discovered that the broken plastic body clips on my Prius were a replaceable, bolt-on part. My bumper no longer pops off every time I go over 55 now.
A worth addition. A friend with a Toyota FJC recently called me all distraught that part of her rear bumper cover had fallen off and could I fix it? I expected to have to ruefully tell her sorry, but I was pleasantly surprised to find the culprit was, like you cite, just replaceable plastic clips.
One time my dad and I were trying to change my brakes on my 2003 civic (this was like 4 years ago so it wasn’t ancient but aged a bit) and a cop walks up with a giant tire iron after seeing us struggle with one of the lugs. I don’t especially love cops and what happened next would have happened to me regardless but: “Heh, now THIS is how you get a stubborn bolt loose-”
And like that, the bolt had snapped, head still in the rotor. (We asked our mechanic about fixing it and he told us that while it’s not something they could legally do, it’d be easier and cheaper to dremmel out a little bit of metal covering it from behind and swap the bolts from there. It fucking sucked.)
A big long lever on a rusty fastener is a great way to shear it off, rendering you USCWAP. Short impact shocks work way better.
“What Are The Most Annoying Things That Can Happen When Wrenching On An Old Car?”
I would have thought running out of money and skin on the knuckles…
Good answer!
If I don’t sacrifice blood at least once every time I work on my car, I will anger the car gods.
Blood for the car gods!
It’s a requirement of wrenching. Blood must be spilled for a successful session.
The car gods are old gods who found new purpose. But they still demand blood sacrifice! Which is why I keep a chicken coop behind the garage. And for some reason my neighbors want nothing to do with me…
I don’t practice Santeria
Jeep needs Quetzalcoatl
I always tell my kids, you aint working till you bleed.
It always find it amusing when I find blood on parts and have no idea where I cut myself. I mean, I curse and complain that I don’t have time to bleed before dumping on some rubbing alcohol and making a bandage from electrical tape and paper towels as I never have anything else at hand, but there’s humor in the source of the blood being unnoticeable in the chaos of general bruises, scrapes, and so on.
Wait until you get old. With skin as thin as tissue paper and having the same strength, bloodletting is a common occurrence. Like when trying to remove the turbo coolant lines from the side of the block with no room and nothing to pry on.
O-rings on steel fittings held into an aluminum block seem to be vulcanized into place. While I’m on a rant, the plastic quick connect coolant fittings that are keyed into place so you can’t rotate them to break the stiction are another source of frustration. There has to be a tool to pry them off, but I haven’t been able to find one.
Level 4 cut gloves are my friend. Good ones allow me decent dexterity, and I don’t miss the the ritual of finding out what new cuts I have as I wash up after by getting solvent in them.
Note that you CAN still be stung through them: they resist cuts, not small penetration
Where are Level 4 gloves obtained. I do have 7 & 9 mil gloves.
Not sure where our company orders them from, but easily found them on the net—and reasonably cheap compared to the pain of multiple small, slow-healing cuts. Pyramex GL603C5 are what we settled on. They do conduct electricity, and have less rubber than some. While that does allow the gloves to absorb liquids, it also gives us more fine dexterity.
I restrung over 100 pianos up into my early 50s, and bled on every one due to the sharp springy piano wire. Did one last restring job on the side after changing careers using these gloves, and, while I did get several pinpricks from wire, the gloves stopped the former ‘penetrate and tear’ of my aging skin: I didn’t get a drop of blood on the piano. Back this up with the motor-swap I did in my car earlier this year which involved no bleeding, and I’m sold on them.
-it’s worth a mention that many hand lotions ( during the 15 years of working on pianos, I almost never didn’t have a few small cuts on my hands, so I tried many of them )contain alcohol, which rather defeats the purpose. Lanolin-based brands like Udderly Smooth and Working Hands are what I use now: no more slathering hands with the brand of the month, then donning gloves to sleep in an attempt to moisturize & heal overnight
sorry for the wall of text. I know well the constant irritation of multiple small cuts and want to share what has worked for me
addendum: when working on cars, I slather Working Hands on before the gloves. My skin absorbs much less of whatever liquid I encounter, making cleanup a simple hand-wash
Are you talking about a Ford? The coolant lines to the bulkhead of my Focus ST were these obnoxious BS plastic keyed connectors with the key in the least accessible orientation that seemed incredibly overengineered for something that could be done more effectively with good old hose clamps, though I’m sure the ones they used were quicker on the assembly line. I ended up buying new ones and just cutting the old ones out so I could rotate the stub to get at the keyed area. I might have thrown them across the driveway when I got them out.
I was specifically referring to my twin turbo BMW, but probably applicable to my twin turbo F-150. I love putting the quick connects together, but coming apart is tough. I put silicone lube on them this time, hoping for better luck next time.
I’ve been working on a patent for a device that would dispense bandaids like Scotch tape on a roller. It seems feasible
I’m a customer. Does is come in red to match my toolbox?