Yesterday I was installing new brake lines into my 1954 Willys CJ-3B, and while it was quite a simple job, there is one section of the car that’s just a massive pain in the butt, and it got me thinking about all the engineering packaging decisions that have compromised serviceability and thus lost me hours of my time.
Specifically, where the brake master cylinder bolts to the frame is a bit of a shitshow on an old Willys Jeep. The master cylinder is sandwiched between a bracket and the frame via two bolts that thread into — often brake inside of (after rusting) — the frame. Since my Jeep is from California, I narrowly managed to thread those two bolts out, but once the master cylinder was in, routing new brake lines was rough.


The thing about new brake lines is that they’re rarely perfect, meaning you have to fine-tune some of the bends to get them to meet the fittings. My issue was that the brake line has to go through a small hole in my frame before immediately mating up to the master cylinder. Here you can see it from up top”
Here’s a side view:
And here’s a little closer look:
Trying to bend the line, then thread it through that small hole (which already has a hose going through it) took me forever, especially since the fitting was right there after the bend, and especially since I had to do this while on my back.
Another classic example of a packaging decision that has ruined a few of my afternoons is the oil filter housing location on post-~1992 Jeep Cherokee XJs. These things leak like a sieve, and to fix them one has to remove the oil filter adapter from the engine block; it’s held on by a single torx bolt, whose head is so ridiculously close to the unibody rail that you have to either buy a special tool (shown below) or custom-make your own tool to remove it.
I myself had to buy a torx socket, cut it down with an angle grinder, then use a box wrench to just barely fit between that rail and the oil filter adapter.
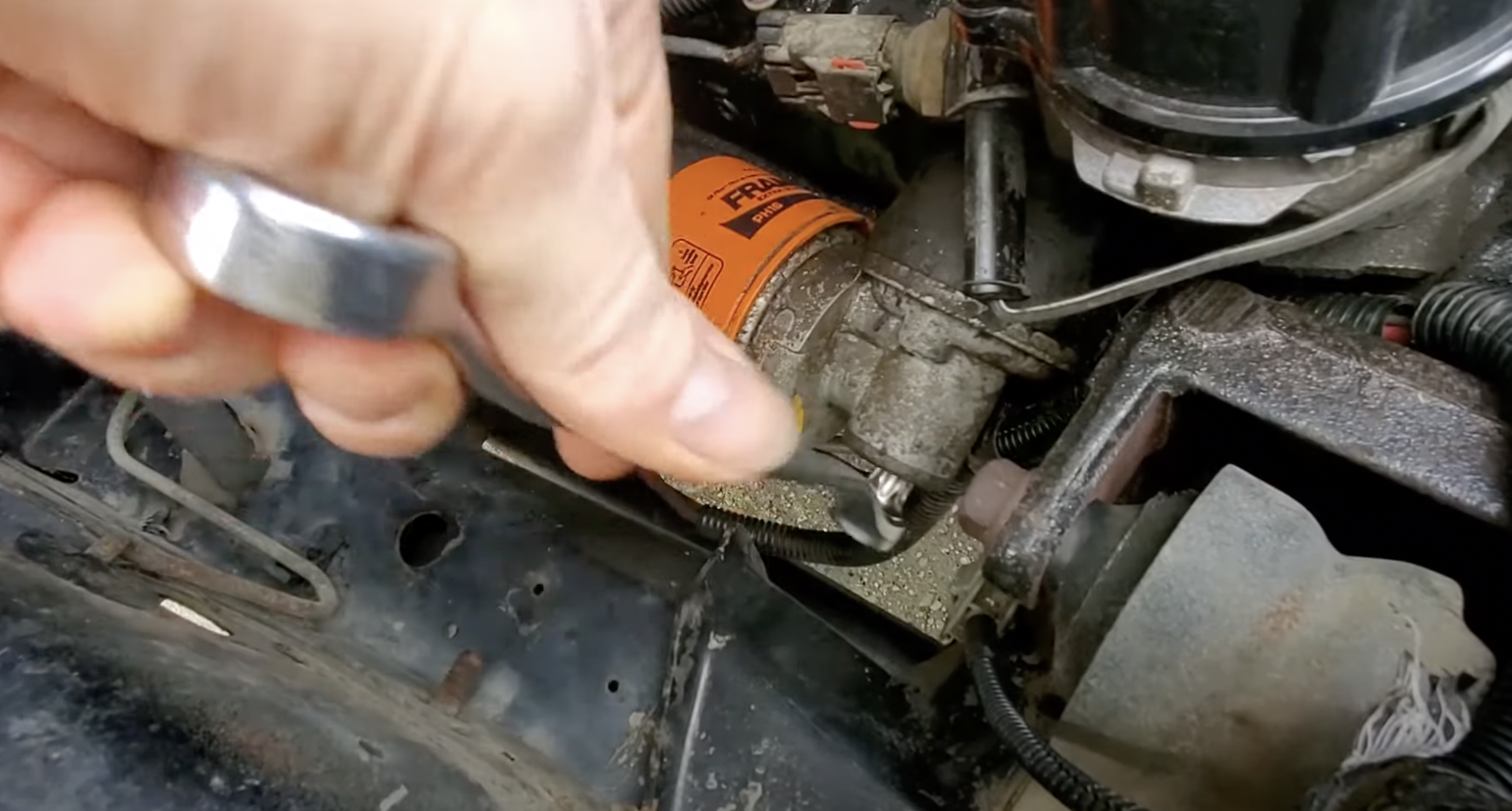
Don’t even get me started on the upper shock bolts on the Jeep Cherokee XJ, which tend to break in the weld nuts captured in the unibody. The result? You have to use an air chisel to break the weld nut and then you have to fish the nut and broken bolt out from behind. Then you have to fish a new bolt in through the top and hold it in place while you thread a nut on — it’s rough, as YouTuber D&E In The Garage shows below:
And then there was my multi-day nightmare with my Chevy HHR control arms!
As with many wrenching endeavors, if you have the right tools is key, and once you’ve figured out how to do it the first time subsequent fixes are usually much easier.
Still, this is a thread for us to complain about tight packaging making repair jobs a bear, so have at it in the comments!
The Lexus Remote Touch interface.
Its odd shaped and so ****ing imprecise.
I have a Volkswagen Auto Group car.. where do you begin on what engineering decisions makes working on my car annoying…
My 1998 Lincoln Continental. Transverse V8, FWD. Need I say more?
How about a built in self destruct device which, if not caught in time, nearly guarantees a junk engine ? Chrysler decision to use a nice 2.7L Mitsubishi V6 that was above most things, but carried a dark secret….a buried water pump, for when it failed, dumped anti freeze into the oil, taking out the main & rod bearings, the cams & rings. No warnings or hints, just 500 lbs of steel & aluminum junk, and a throw away car. 20+ yrs on, not many left intact……
I had a 2004 Renult Modus. A wonderful dorky little car that consistently punched well above it’s weight class. Four 6ft adults? Yes! Family of 5? Yes! Parking almost as easy as a smart car? Yup!
I loved that little thing even if I had to turn the AC off to merge onto the highway(hey, those 8hp were desperately needed!).
But! An oil change involved pulling the entire front facia and bumper off. Renult book value was 2.8 hours of labor, just to start the oil change! Plus another .3 hours of oil change! Same thing for a headlight bulb… 2.8 hours for facia, plus .1 for the bulb!
And there was no work around, there was about 1.5 inches between the engine and facia. Great for packaging a cabin than can handle four adults into an 11ft long car. Great for baked in dealer service charges. Not great for wrenching
For the 9000, Saab routed coolant into the throttle body through a stainless steel pipe set in the crankcase breather hose. I found out when I mistook it for a vacuum line and got sprayed with hot coolant.
Every single engineering decision under the hood of my old B5 S4 made things difficult. Ugh, that thing was a beautiful pain.
If there is anyone here unaware of Kano kroil and silikroil penetrating oil, I wanted to mention the grief they have saved me.
Someone restoring classic cars told me about it.
I don’t pick up a tool until I find a can.
Tea tree oil is key to its effectiveness.
4th gen F-body wiper motor. The thing is so far back in there I swear it’s cuddling the instrument cluster.
Pretty much any transversely mounted V6 near as I can tell.
Some are worse than others, my Acura 3.5 V6 is dead simple to change the plugs on. My old Chevy 3.1 V6 in a Malibu was an frustrating all afternoon affair however. I taught my kid to cuss that day.
Changing the spark plugs on any turbo Subaru from about 2008+.
The damn spark plug wells are right next to the frame rails.
There are plenty of “tricks” that people will tell you to make it “easier.” But they’re still a PITA.
The front coil springs on my Mercedes W123. I think having actual coiled up king cobras there would be safer.
Changing the oil filter on a first-gen Taurus (possibly just the V6). Impossible to get my hand in there. An oil change shop wanted an extra $50 to change the filter during a change.
Did a heater core on a 65 Olds 442, at age 17. Couldn’t dream of that at age 68!