With the advent and growing popularity of EV’s, manufacturers have been working to electrify the various smaller systems that used to be powered by the internal combustion engine — systems like steering, HVAC, and brakes. All of these used to be powered by engine-driven pumps, compressors, and manifold vacuum. Without a traditional engine, or an engine that is always on, OEMs and suppliers have had to find alternative ways to power these systems, and with a massive battery onboard, it makes sense to make everything electrically powered.
In the case of steering, this has resulted in an electric motor driving the rack. Of course, even in non-EV’s or hybrid vehicles, electric steering has taken over due to their higher overall efficiency. In the case of HVAC, it meant an electric motor (and not a gas motor’s accessory drive) driving the AC compressor. In the case of brakes, it has also resulted in an electric motor replacing the old vacuum booster, but there is an added complication that makes braking systems a bit more difficult to electrify.


It’s All About Energy
Braking systems at their fundamental core are really just energy conversion devices. When a car is moving, it has a certain amount of energy which is equal to ½ the vehicle mass times the velocity squared. It’s called Kinetic Energy and every object that is in motion has it.
Kinetic Energy = 1/2 x Mass x Velocity²
In order to bring an object to a stop, you first have to get rid of this kinetic energy. That’s where brakes come in. When you step on the brake pedal, the brake pads make contact with the brake rotors (or drums), and the resulting friction creates heat which is then dissipated to the surrounding air. Heat is another form of energy, so what your brakes are doing is converting the energy of motion, i.e. the kinetic energy, into heat energy. Since kinetic energy is directly related to vehicle speed, as the speed reduces, so does the kinetic energy. In the same way, as the kinetic energy is reduced (by conversion to heat), the speed must also reduce.
Regeneration
The downside here is that standard brakes turn kinetic energy into heat which is then dissipated to the air. All the energy that was used to bring the car up to speed is now lost to the air when you slow down. This is where one of the big advantages of EVs comes in. EVs (and hybrids, too) have the ability to take the electric motor that drives the wheels and temporarily turn it into a generator, which then partially recharges the battery. It’s called regeneration. By doing this, the kinetic energy is not just lost to the air, but is instead turned into electricity and put back into the battery so it can be used again later. This is the fundamental reason why hybrids get better fuel economy than their non-hybrid cousins. Energy that would normally be lost is instead recovered so it can be used again later.
But just as there is a limit to the amount of power an electric motor can provide during acceleration, there is a limit to the amount of power it can generate during deceleration. And this limit is normally well below the capabilities of a normal brake system. Take for example a 2000 Kg car slowing down at 0.8G, which is well within the abilities of most modern brakes. The brakes in this case have to be able to provide on the order of 4000 lb-ft of torque to the 4 wheels. That’s a LOT of torque, but that is perfectly normal for a modern brake system. There are some EV’s out there today that have motors that can deliver that kind of power, but in general, most deliver much less, so it is not possible for them to slow the car down the way the regular brakes would. Also, unless the EV has hub motors, there will not be individual wheel control under regeneration, so there is still a need for standard brakes. On top of that, the electrical energy that is being generated needs to go somewhere. Most batteries cannot recharge at the same rate as they can discharge, so there is a limit to how much energy can flow into the battery. All this means is that we can’t just rely on regeneration to stop the car. We need to combine regeneration and normal hydraulic brakes to get the job done.
But this presents an issue. When you step on the brake pedal, something needs to decide how much of the braking power is going to come from regeneration and how much will come from hydraulic braking. And this decision needs to be made in a way that is transparent to the driver. When you step on the brake pedal, it should feel like an ordinary brake system. You don’t want the pedal feel to change depending on how much braking is done by regeneration vs. hydraulics. It should always feel the same.
In the past, this “blending” of regen and hydraulics was either done mechanically or not at all. Some hybrids used a mechanical system that used a slotted connection between the pedal and the brake booster input rod. As the brake pedal was pushed, a pin would move within the slot and a position sensor would tell the brake module how far the driver was pushing the pedal and how much regen braking was required. The pedal would also push against a spring and/or rubber pucks that were designed to simulate the feel of a normal pedal. Once the pin bottomed out in the slot, the pedal would be pushing directly on the brake booster similar to a standard system, and hydraulic pressure would be sent to the brakes calipers.
Many of these systems had a slight artificial feel to them and the transition between regen braking and hydraulic braking was fairly evident. The pedal feel wasn’t consistent.
The other method was to ignore the problem altogether and put all the regen on the accelerator pedal. Lift off the accelerator and the motor would go into regen and slow the car down. It gave birth to the concept of one-pedal driving where, if you planned ahead enough, you could drive solely with the accelerator and rarely, if ever, touch the brake pedal. The only thing the brake pedal did in these cars was operate the hydraulic brake system. Tesla was the first (to my knowledge) to use this system, and it meant the brake system did not need any fancy EV specific software or hardware.
The problem was that these systems could not utilize the regeneration capability of the motors to their fullest extent since the amount of deceleration this would give was felt to be too much for smooth driving. You would have to be much too careful with your accelerator pedal movements to avoid a jerky ride. In Tesla’s case this meant limiting regen braking to 0.15G. BMW later increased this to 0.2G with the i3.
A Better Way
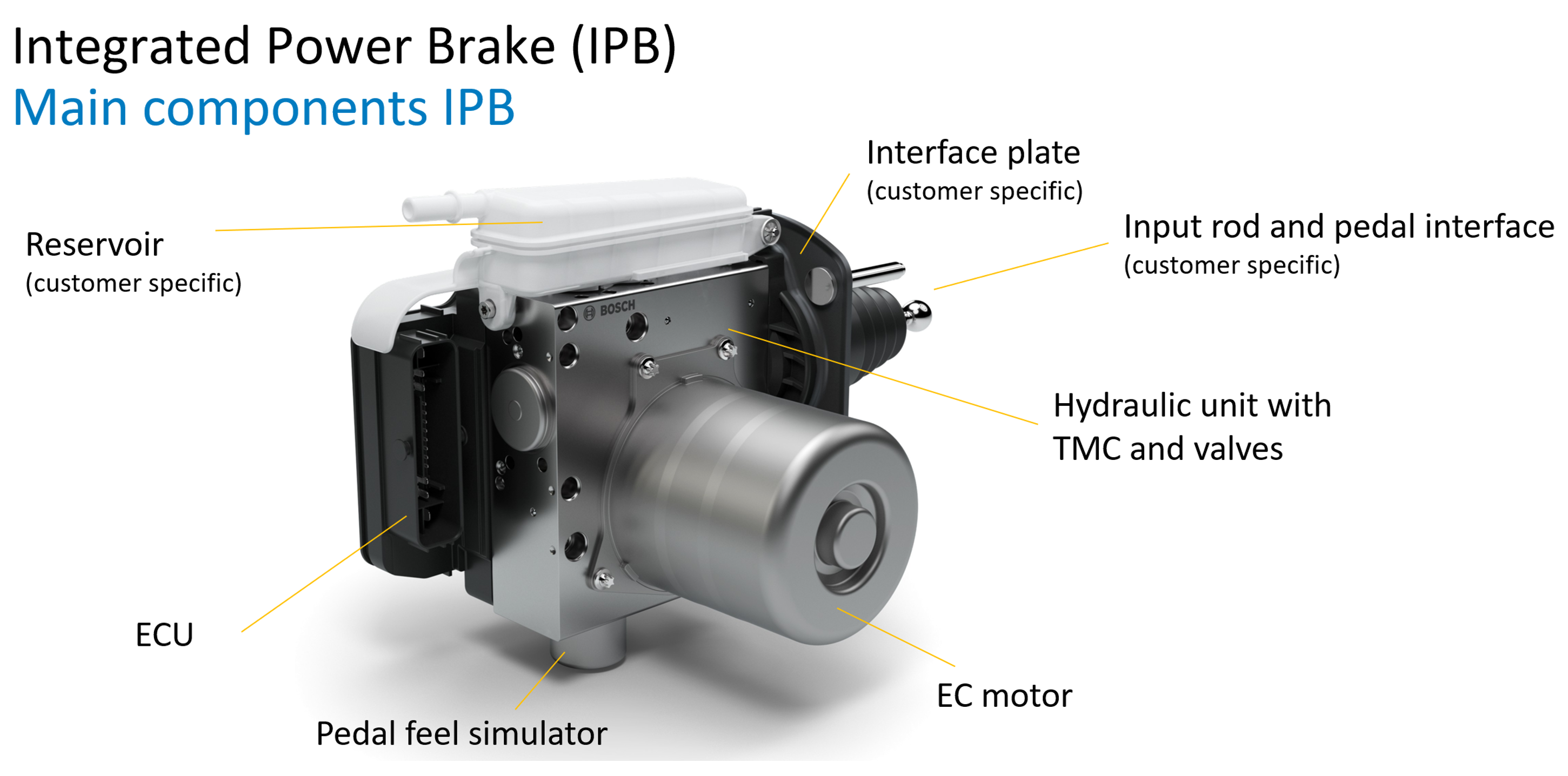
But what if there was a brake system that allowed the fullest use of regen, could blend regen and hydraulic brakes seamlessly, not give a jerky ride, and even give the driver a choice of one-pedal driving or something more like the old car he/she was used to where lifting off only gave a little bit of engine braking? Enter the new de-coupled braking systems.
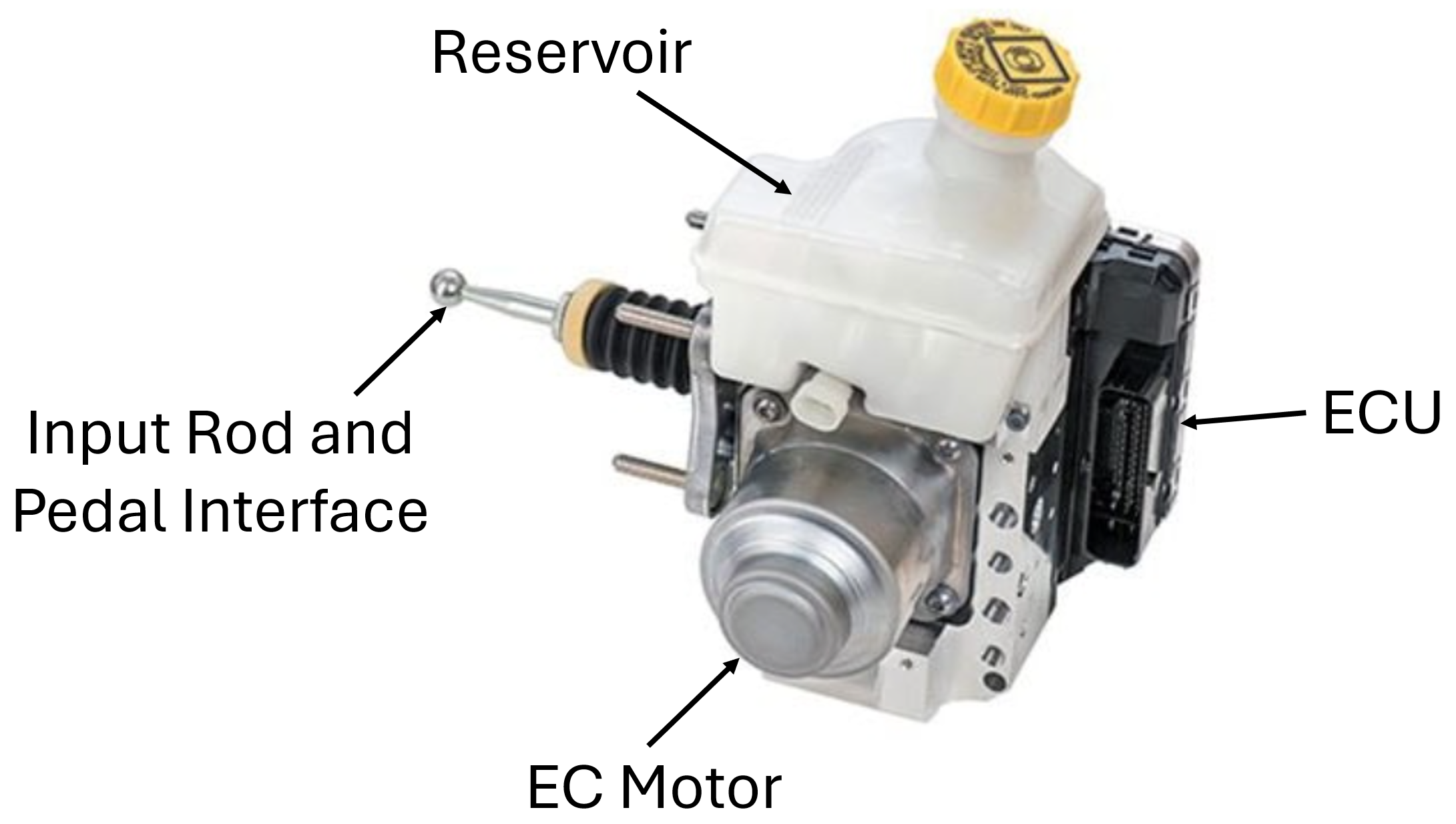
Notice my use of the term “de-coupled” instead of “brake-by-wire.” This is purely intentional and it will become clear later why I say this.
In a standard modern hydraulic braking system, when you press on the brake pedal, it pushes a rod into the master cylinder which sends hydraulic fluid under pressure via the anti-lock brake module out to the brake calipers located at the four wheels.
In a de-coupled system, the brake pedal still pushes a rod into the master cylinder, but now instead of sending hydraulic fluid under pressure to each of the four wheels, the pressure is sent to a “pedal simulator” consisting in many cases of a spring and rubber puck. The hydraulic pressure tries to compress the spring and rubber puck, and the stiffness and shape of the spring and rubber puck give the impression that you are pressing against a normal brake system. At the same time, pressure and position sensors tell the system how hard the driver is pressing on the pedal.
While this is happening, a computer looks at the data coming from the sensors and decides if the desired braking can be accomplished using regeneration or if hydraulic braking is necessary. If regeneration is sufficient to provide enough braking, then the computer will send a signal to the powertrain controller, telling it to start the regeneration process. If, on the other hand, hydraulic brakes are required, the computer will send a signal to a motor housed in the brake booster, which pushes a rod into another smaller master cylinder. This secondary master cylinder is what now sends hydraulic fluid under pressure out to the four wheels via the anti-lock brake module.
In this way, a computer is able to decide how much regeneration is going to be used and how much hydraulic pressure is going to be used to slow the car down while all the time, the driver is simply pushing against a simulator that feels like a normal brake pedal. The driver is blissfully unaware of the decisions this computer is making and just feels the car slowing down in response to their pedal input.
But what would happen if this computer were to fail, or if power to the brake booster were cut for some reason and there was no power available to run this little motor inside the booster? There would be no way to create the hydraulic pressure needed to stop the car.
Fortunately, this has been taken into account in the design of the booster. Here is a diagram of what a typical de-coupled system looks like:
You can see how the pedal is attached to a regular-looking master cylinder and how the pressure from this cylinder goes to the pedal simulator. You can also see the extra motor and its smaller master cylinder and the lines going from there out to the anti-lock brake module and to the wheels. But there are a few extra parts in there as well. These are valves, which control how the hydraulic fluid will flow inside the booster. Two in particular are of interest to us and they are labeled “de-coupling valves” in the diagram above. These valves are normally open, meaning that when they are not powered, they are in an open position. Conversely, the other two valves, which lead out from the smaller master cylinder, are normally closed.
Under normal operating conditions, when the car is powered up, the de-coupling valves will receive power and will close, preventing hydraulic pressure coming from the main master cylinder from flowing out the anti-lock brake module and the four wheels. Instead, this pressure is forced to flow to the pedal simulator. The other two valves which are normally closed, will now be open, and hydraulic fluid will flow from the secondary master cylinder out to the wheels.
But if there were to be a power failure, or if the computer that controls these valves were to stop working, the springs inside the de-coupling valves would automatically open them up again, and the springs inside the other two valves would automatically close them again.
Under these conditions, fluid would be allowed to flow directly from the main master cylinder out to the four wheels, and the whole system would act like a traditional hydraulic brake system.
In this way, there can never be a situation where an electrical failure would prevent the driver from stopping the vehicle.
Terminology
These diagrams also show why brake engineers prefer to call them “de-coupled” rather than “brake by wire.” Under normal conditions, the hydraulic circuit attached to the brake pedal and the hydraulic circuit flowing out to the wheels are de-coupled from each other. While it is true that under these conditions, the only thing connecting the two circuits is a wire going to a computer, the term “de-coupled” more accurately describes what is going on here. It also reserves the term “brake by wire” for future systems that eliminate the use of hydraulics altogether and have only wires (not hydraulic lines) connecting between the brake pedal and the calipers at each wheel. These systems would use a motor at each caliper to actuate the brakes in response to a signal coming from sensors attached to the brake pedal. There would be no hydraulics in such a system at all. This doesn’t yet exist in any form other than experimental, but I can see a future where they get introduced and slowly take over from the hydraulic systems we know today.
Regulation
There is one more aspect of the brake booster that is impacted by the use of a de-coupled brake system. Brakes are some of the most heavily regulated systems in your vehicle. In the U.S, the regulation that governs brakes is called Federal Motor Vehicle Safety Standard 135 (FMVSS 135). In Canada it is CMVSS 135, and in Europe and most of the rest of the world it is the United Nations Economic Commission for Europe regulation R13H (ECE R13H). These regulations cover a multitude of topics starting with the fact that brake systems need to have a backup (which has led to the split braking systems all vehicles have — i.e. two wheels are on one hydraulic system, two wheels are on another separate one), to the conditions the brake lights must come on, and even to the text that must be displayed on the brake reservoir cap and how easily you must be able to see the fluid level in the reservoir. In FMVSS and CMVSS 135, there is also a requirement for the performance of a braking system that has lost power, either through a loss of vacuum in the case of a vacuum-boosted system, or electrical power in the case of an electrically powered system.
If the system that provides power to the brake booster fails, the car must be able to stop from 100 km/h in no more than 551 feet (yeah, there is a weird mix of units here but that’s how it’s written!) while needing a brake pedal effort of no more than 500 N (112 lbs.).
So, what does this mean for our braking system? If our brake system only had to meet the above regulation, it would be fairly easy to design a master cylinder and four calipers to do it. We would choose a relatively small bore master cylinder and use large-diameter pistons at each caliper. That way, for every lb. of pedal force, we would generate a lot of hydraulic pressure, and for each PSI of hydraulic pressure, the pistons in each brake caliper would generate a lot of force against the brake pads. Easy peasy!
Unfortunately, the same master cylinder and brake calipers also need to stop our car from max speed when everything is working correctly. If we used a small bore master cylinder and large diameter pistons in the calipers, we would get a lot of pedal travel. That might be fine for a failed boost emergency situation where all you care about is stopping the car safely, but it’s not fine when everything is working correctly. We don’t want a lot of pedal travel under normal conditions because that would mean our pedal would need to start out very high and it would be uncomfortable to have to move our foot so much. And so, we end up with master cylinders that are a little larger than we would ideally want and caliper pistons that are a little smaller than we would ideally want.
There is one more complication we need to consider here as well, and that is that we need to be able to stop our car when one of our hydraulic circuits has failed. If you’ve ever had a failure of a hydraulic circuit, you will have experienced the problem here, which is that the brake pedal will first move a lot before you get any braking action. This is because the master cylinder cannot build pressure in the remaining good circuit before the bad circuit has bottomed out. This means even more pedal travel has to be accommodated for.
The bottom line here is that we cannot simply use a small bore master cylinder to meet the failed booster requirement. We have to design our system to meet ALL of the requirements and the result is by definition a compromise. Obviously, it is possible since every car out there does it, so it’s not really that big a deal. But, these new de-coupled systems give us a benefit in this regard that is not immediately obvious.
Since the master cylinder is normally only connected to the pedal feel simulator, we can make it any diameter we want. We can design the simulator so that a small diameter master cylinder doesn’t result in long pedal travels. And, since the caliper pistons are normally only connected to the secondary master cylinder, we can make them any diameter we want as well. Large caliper pistons just mean more travel for the secondary master cylinder and motor, but that will have no impact on our pedal travel. When there is a failure in the system and the de-coupling valves open up, we will then have a small-diameter master cylinder pushing fluid into large-diameter caliper pistons. Yes, it will lead to long pedal travel, but at that point, you are only really concerned about stopping the car safely. Pedal travel will be longer, but pedal effort will be lower.
All in all, these new de-coupled brake systems provide some very important, and tangible benefits and when things do go wrong, they can be designed to be even safer than a traditional system.
This seems like a smart and safely engineered solution to a problem, which is good to see nowadays. There’s just one problem: I’m quite sure that the problem is a fictitious one.
I understand why marketing departments think otherwise, but there is really no need to seamlessly integrate multiple braking systems into one pedal.
I know this because I drive cars that have multiple braking systems, not integrated into one pedal, and it’s fine. My cars have hydraulic service brakes, engine braking, and the cable operated parking/emergency brake. That’s 3. There’s also jake brakes on a semi, which are also not integrated into the brake pedal, and also very easy and non problematic to use.
I also don’t think(*as somebody who has never driven an EV*) that heavy regen on the throttle is a big problem. That’s virtually the same as jake brakes on a truck(not an issue), and it’s virtually the same as engine braking with a manual transmission(not a problem). And before you object, yes, engine braking can be very strong braking. A Jeep with a big engine, manual transmission, low gearing, and not a lot of weight will throw you out of your seat if you lift abruptly off the gas at higher rpm in a low gear. And guess what? Nobody ever felt the need to smoothly integrate engine braking into the brake pedal experience using $2000 worth of failure prone pumps, valves, and hydraulic cylinders!
Yeah, those brake-by-wire systems are perfectly safe:
https://mynissanleaf.com/threads/brakes-fail-upon-powering-on.18283/
https://mynissanleaf.com/threads/car-moves-while-i-am-pressing-on-the-brake.18022/
https://www.reddit.com/r/leaf/comments/o426lc/help_breaks_didnt_work_today/
https://www.speakev.com/threads/nissan-leaf-brake-failure.177746/
https://www.speakev.com/threads/total-brake-failure.168633/page-3
Just make sure your 12V battery is in perfect condition at all times!
In reading those threads, it seems like the Leaf brakes are working exactly as Huibert described. They’ve made the choice to have simulated brake feel when in the decoupled mode, while the unassisted brake feel requires so much force that the people in those threads perceive it as the brakes not doing anything. This is because, as Huibert described, they’ve made a choice for a narrow diameter master cylinder so it requires lots of travel to push the fluid where it needs to go. You can even see people talking about this in the threads. A vehicle with regular brakes would behave the same way in the absence of assist.
If the unassisted brakes were not able to stop the vehicle per the regulatory parameters, this would be a very big deal and would lead to huge recalls and stiff fines.
Now, you can say that perhaps the brake assist relying on the electrical system rather than vacuum approaches is less reliable, but this is the system working as intended and I don’t see evidence of these systems failing to meet the regulatory requirements.
Maybe so, but it’s terrifying when the brakes don’t appear to work and your first thought is that perhaps you have your foot on the accelerator instead of the brake.
Actually, I don’t think that it was working as intended. In one of my experiences, the car was on an angled drive and my foot on brakes was holding it there before starting the car.
The regen braking is really nice for descending mountain passes. I really like that I can put my PHEV on cruise control and it will maintain the speed going downhill, increasing the regen so it doesn’t go faster. It makes our Odyssey feel like a dinosaur, having to downshift to not overspeed.
That’s one thing I’ve admired in my Prius; I can’t distinguish the regen braking from the mechanical braking.
I’ve read that switching to Neutral forces it to use mechanical brakes only, which is nice to test them and clean the surface rust off them, but it’s smooth either way.
On the other hand, it also apparently has something called a “brake accumulator” that I hear do a ~5-second whirring noise every few minutes during city driving. Apparently it’s a very expensive part to replace when it goes, and it can cost more than the hybrid battery to get replaced…and apparently it’s a problem part on high-mileage gen 3 Priuses. Joy!
The brake controller in a 2005 Ford Escape Hybrid costs $9,000 plus labor to replace. That’s more than twice what the car is worth. I used to have one and I was terrified the controller would fail. But it never did.
What I find interesting that I am not sure if someone already “fixed” this problem, when you are on regen mode on several vehicles and if you hit a pothole or something big like train tracks, the regen will stop momentary and its a oh shit moment since now you have to apply the brakes more to engage them.
Oh, really? That’s not a universal anti-lock brake experience? I deal with that in my Prius regularly. Just very brief moments, but there nonetheless.
Didn’t have that issue in my van, but I assumed that was just because the rear brakes were drums. The fronts had ABS, at least according to the manual.
In buses, we just handle regeneration and retardation via pressure sensors.
In buses with transmission retarders (like an engine brake, but on the trans):
-As you begin to apply the brakes, different pre-programmed brake system pressures activate the various levels of retard (this varies, Allison trans has a 3 stage, our ZF trans have a 5 stage).
In buses with traction motors and regenerative braking:
-as soon as you’re off the accelerator, regenerative braking starts pretty aggressively. You can almost 1 pedal drive an electric bus.
-Then, similar to the trans retarder, different brake pressures will ramp up the regen until you cease forward motion.
Of course, air systems have the luxury of always being decoupled, so solutions are different. A loss of air pressure simply allows the spring brakes to apply. They’re held in the release position by air. No air, no drive.
Seeing how this could become an issue on things like railroad tracks, coaches and transit buses have an emergency air tank that supplies enough air to release the parking brake and move a vehicle out of harms way. You have no brake pedal during this process, so move slowly.
What an exceptionally clearly written article!
Thanks Huibert, fascinating stuff! (Yes I am a dork).
Makes me wonder my 2nd gen Volts have decoupled brakes.
That being said, with modern ABS, emergency braking, traction control, etc., the computers can completely ignore how much you’re pressing the pedal on coupled systems.
I’d be interested in learning about how ABS using hydraulics differs from electronics.
Cruise ships have “brake by wire” too.
Push the little buttons on the console, and watch the anchors drop…
….then wait.
Great easy to understand write-up. I’m old-school, and cringe whenever simulated feedback is brought up, and like to feel what’s happening. Capturing wasted energy is obviously a huge plus. Has any manufacturer offered the Regen as a completely separate option, perhaps from a steering wheel mounted thumb wheel? There are times when free wheel coasting would be the most economical. Over complicated braking systems reminded me of a stone age simple emergency braking system, I saw a video of, for tractor trailers that deployed a roll of reinforced rubber under the rear tires, instantly locking them up. Couldn’t find it with a brief search. From what I recall, it was violent, but did stop faster.
The man I used to work for and was my mentor at Ford told me about an emergency brake he helped design for buses going through the Alps. It fired a long pin into the pavement and uncoiled a long cable from a big brake drum. Violent, but effective. Even if the bus went over the edge, the cable was strong enough to keep it from falling.
HA!
Yikes, I’d hate to have to use that!
Was it manufactured by ACME, Inc.?
The Chevy Bolt has a hand pedal similar to a flappy shifter paddle that controls regen when you’re not in one pedal drive mode. Used it for a few days when I first got the car and switched to one pedal quickly after. It’s very intuitive after about 5 minutes of driving with it!
Yeah, the Bolt in D will behave like any other automatic, but putting it in L drops it into one-pedal mode. The paddle works all the time, and between L and the paddle you more or less never need to use the brake pedal outside of emergency stops. I don’t have hard numbers, but it feels like you get slightly better Miles/kWh this way. I’ve been getting better at the one-pedal mode, my big hurdle is when I use cruise control. If your muscle memory says ‘hit the brakes to drop out of cruise’ you get hit with >0.2G all of the sudden, it works better to have your foot on the throttle and use the steering wheel controls to drop cruise. That way you aren’t lurching all over the place. Took a bit of practice to nail it at first.
I remember seeing a video, ages ago, like the 80’s maybe, where they showed testing of that type of system that was being developed and tested in Australia. I’m guessing it never really went anywhere since once it was deployed that sheet was sliding on the road and you lost directional control.
I’ve always wanted to see the third pedal (clutch) brought back in EVs as a Regen pedal. Kinda like the retarder pedal some trucks and busses have:
https://images.app.goo.gl/w8TLMD9u1nsXtVh7A
The Volt has a paddle on the steering wheel that’ll do full regent, but it’s all-or-nothing with a built-in ramp-up/delay. It works OK, but it’s pretty hard to brake smoothly with it. I think I’d prefer one-pedal driving with adjustable levels (and maybe a small detente or dead zone at zero).
This is all fine and well as long as you don’t care about brake feel. It’s a spooky sensation to smell brakes overheating (on track) and feel absolutely no change in the pedal… Simulations will get better, but electric brake boosters are to brakes what electric power steering is to steering. It comes with a lot of enablers, but it also increases the separation between the driver and what’s happening at the tires.
You are absolutely right, but I am pretty sure Karen doesn’t understand a single concept you just described.
With that said, it sounds like you have experience with these systems on track. Are you slower or faster? I get that the feel is lost, is the speed lost too? I can imagine there will be a long transition before we get to fully electric, do you embrace it?
Right. This exists to appease the “Karens” (as you say, though I’d say “typical uninterested drivers”). There is no theoretical difference in speed, in ideal conditions, IF tuned properly. I’m currently working on programs with this type of braking systems and we’re having to tune around things that were never issues before electronic brake boosters. In that case, the car IS slower, until we get this resolved. In the track example, you’re leaving it up to the computer to predict when the brakes will start overheating and compensating with more pressure until they’ve overheated and the pedal sinks dramatically. If the driver was fully informed, they would notice the pedal getting a little long and start compensating their driving by lifting and coasting early, or using less pressure and lengthening their brake zone, or simply cooling off and coming in.
Temperature sensors do the same thing, and could let a diver experience consistent performance up to their own judgement of the tradeoffs between performance now and later.
Hell it is not a fundamentally complicated thing to integrate feedback from temp sensors into the brake computer, thus providing any combination of changes you want.
I think there is a fundamental disconnect between “this information is not available” and “I’m not getting the information in the same way I have been used to.” Drivers were the tuning prior to eBoosters. There are no “new” issues.
Careful there. My wife’s name is Karen (that is actually a true statement!), and no, she couldn’t care less about brake feel. As long as it stops the car.
I put it in quotes for exactly that reason and only because the post I was replying to used it. I don’t like to use that term because it’s really not fair to all the perfectly nice Karens out there (no quotations)! Hi, Karen 🙂
Good point, Anthony.
If it’s badly incorporated, yes. But a properly engineered feel module should be better than a direct mechanical coupling. I think one of the big problems in automotive design right now is the lack of rigorous regulatory (or even internal) standards regarding driver control interfaces. This is glaringly obvious when you contrast it with something like aerospace, which has ridiculously strict rules on how pilots interface with the aircraft under a wide range of normal and non-normal conditions. Properly designed modern aircraft, despite using almost exclusively fly-by-wire controls actually give the pilot a much better feel for what is actually going on in their control surfaces and the energy state of the plane than you get with old fashioned (hydraulically assisted) lever and cable connections.
In my experience, very few manufacturers seem to even care about control feel and driver feedback, and those that do tend to only care on their expensive products.
I’m not sure any of these systems will ever be better than a purely mechanical system since they all try to emulate a mechanical system (and yes, i consider hydraulic systems to be “mechanical”). But they should at least be indistinguishable for most people. I disagree that most manufacturers don’t my care about their controls feel though. There are a few who don’t seem to care but the majority spend an inordinate amount of time tuning brake and steering feel. You may not like the results, but it is still the result of a lot of work. They just have a corporate target that is not to everyone’s taste.
I used to have the same opinion that purely mechanical systems would always have superior feedback, but a few years dealing with human interface design has changed it. If you look at the design philosophy behind providing user feedback on a control system (whether it is in a car or a plane), the primary goal is to provide and accurate and intuitive picture of the state of the system under control. The problem with a purely mechanical system used in any reasonably energetic environment (such as braking a car in a brisk manner) is there are always sources of hysteresis, noise, and outside interactions that can provide deceptive or outright erroneous feedback to the user. Just naming some examples that occur with braking a car, you can have air bubbles, water flashing to steam, contaminated rotors or pads, suspension articulation and vehicle attitude changes- all of which can provide feedback that does not accurately reflect the conditions of the braking system. A properly designed electronic or electromechanical system incorporating multiple sensors and integrated control circuits should be able to cancel out these sources of error and give a more accurate picture of the state of the system to the driver. Of course properly designed is doing a lot of work there, and I certainly acknowledge (having done a bit of it myself) that control interface design is really, really hard.
I know car manufacturers spend a lot of time working on their brake and steering feel, but I submit that the majority are either not very good at it, or more generously and likely, forcing engineers to give a lower priority to those things than other design elements, which leads to concessions and compromises in the final product. So I guess what I would say is at the top of my priorities buying a new car is the control feel, and I don’t think most automakers align with that priority.
There are factors such as cost and time that I suspect might prevent the “by-wire” control interfaces in a car getting to the level that you suggest are achievable.
I think the reality of these systems, like most other electronic nannies, is that they are not suited to track use. I would expect a true race car to dispense with these outright anyway in favor of traditional systems. Feel is so important in those types of cars so that you know what’s really going on at the tires. Steer by wire tries to correct this by using a feedback motor that gives force feedback to the driver in response to what is happening at the wheels and i wonder if that is the next development of these braking systems as well.
Yup. Varying brake feel and response, along with ABS calibration, by drive mode is already a thing. The cool thing is being able to alter feel and response of the various control interfaces at the push of a button (even if it’s a virtual button), but it’s only cool if they don’t suck and are genuinely useful. There are many other enablers that come with xyz-by-wire, but feel is generally the one that degrades with the transition.
I’d take electric brakes over hydraulic ones, I just want mechanical backups, like the emergency brake of old, not the stupid electric parking brake only brakes.
I test drove my uncle’s Rivian R1T which was my first experience with one pedal driving and I damn near gave myself motion sickness with how aggressive the regen was. My driving was worse than a 15 year old 2 pedal driving a car for the very first time. I imagine you get used to it and can dial things in with regen levels in the software, but wasn’t the best first impression.
You get used to it and you’ll get more subtle with your pedal movements. Once you get the hang of it, it’s fantastic. You almost never have to move your foot sideways.
I’m curious how I would react to that. I find my right knee gets very sore driving automatics compared to driving manuals. Its odd, but just that periodic release of tension on my right leg to clutch with the left makes a huge difference in comfort for me. I wonder if one pedal driving like you describe, rarely moving the foot, would impact that issue.
I’m renting a Bolt for a week at the end of this month so I’ll give it the old college try. Electric cars were $200 a week cheaper to rent than ICE and my final destination is only 140 miles from the airport.
Can confirm. We have Rivians in our fleet at work and I found a high amount of regenerative breaking very easy to adapt to, and very easy to drive smoothly. The pedal becomes more literally a two-way accelerator pedal.
Oddly, I was used to one-pedal driving the same day I got a hold of, and got to drive, my Polestar 2. Been using it ever since unless I go gonzo.
I was comfortable with one pedal driving in a Model Y within two minutes. After getting one recently it’s becoming second nature. There are the edge cases where it’s still a little jerky.
Wonder if it comes down to how immature Rivian’s software is.
Software can do a lot to soften the transition between on-throttle and off-throttle and make it smooth.
My wife described our Model 3 regen perfectly: “It’s like driving a stick shift in 3rd gear; that great feeling with lots of torque and lots of engine braking.”
That’s a helpful description, thanks!
Basically everything has moved to the eboost setup these days, both ev and ice. I’m waiting to see if someone comes out with a good eboost unit to use to retrofit classic cars as hydroboost isn’t great for feel, and aggressive cam profiles can render vac boost useless and can also have inconsistent pedal force. Most just opt to go full manual but I’d like some power assist in mine.
Also newer one pedal drive setups are going as aggressive as 0.3g or even 0.4g. Enough regent that regen while turning or in other dynamic maneuvers needs to be carefully managed.
Yes, lift-off oversteer can be a real problem with regen if it is not carefully managed in the suspension design.
The Bosch iBooster electronic brake booster as seen on ICE vehicles is very different from the sort of EV and hybrid system that is described in this article. The iBooster uses a single, very normal looking twin piston master cylinder. iBooster (bosch-mobility.com)
There are multiple versions of the ibooster but the origin mask one we put on the Tesla Model S was simply a replacement for a vacuum booster, nothing more. What it did was give us the opportunity to program different pedal force maps so we could have a light pedal for those who wanted that or a heavy pedal for those who liked that. The system did not separate the pedal from the hydraulics at all like these new systems do though.
If you don’t have good vacuum in your classic car for the power brakes, and you don’t want hydro boost, you can keep your vacuum brakes and just run an electric vacuum pump, or an engine driven vacuum pump from a diesel.
Thank you Huibert! I enjoy reading your learning articles.
It gives me insight into my Gen 2 Volt, which has those multiple braking options.
1. Regen paddle to engage regen whenever pulled.
2. 1 Pedal Driving mode
3. Normal Drive mode which has no regen engaged (besides when you pull paddle).
Electric brake actuation is a thing on some aircraft and I think it’s way better than hydraulics.
I agree but aircraft often have triple redundancy and a very rigid maintenance schedule. It’s coming though. Like death and taxes.
I’m all for it. There’s no reason cars can’t have two (or more) independent systems on the same caliper. We’ve already got 2, 4, 6 and 8 pot calipers. Those pistons would be actuated by a motor instead of hydraulics, which is susceptible to leaks, moisture, heat and air. Those motors could easily be run by different busses or independent systems and would require far less maintenance, and the system as a whole would need way fewer components. Sensors and motors with two independent channels in the same housing are possible as well. I’m sure the performance of ABS and stability control would go way up, too.
Give me back my manual cable-operated parking brakes as a backup and then maybe we can talk about electrifying the service brakes.