You’ve probably driven behind pickup trucks and noticed that one rear shock is usually ahead of the rear axle and the shock on the other outboard side of the truck is mounted behind the axle. You’ve probably also noticed that some vehicles have shocks mounted towards the center of the car/truck, while others have the shocks way on the outside, not too far from the wheels. I’m gonna break that all down, and you bet I’m going to use some nerdy simulation tools to do it. Let’s go!
My fellow Autopians, welcome to another edition of Ask an Engineer. This time we are going to answer a question posed to me by one of our faithful readers who asked me to explain why the rear shocks on his pickup truck were not mounted in the same way left and right. It’s a very good question, and there is a very real and specific answer to it.


Staggered Shocks
(138) What are Staggered Shocks and Why Are They Used? – YouTube
Anyone who has had to replace the shocks on a pickup truck with leaf springs made during the last few decades knows it really isn’t a very hard job unless the car is very rusty (looking at you, David Tracy!). Trucks tend to be high off the ground, and there is usually a lot of room around the rear suspension. If you’ve ever done this, you might have noticed something odd about the way the left and right shocks are attached. In many cases, they are not symmetrical, meaning the left and right shocks are not mounted as mirror images of each other. The left shock will be mounted in front of the axle and the right one will be mounted behind the axle, or visa-versa. What you are looking at are what are called “staggered shocks,” and there is a very good reason why they are mounted this way.
Leaf Spring Wrap
To understand why staggered shocks ever became a thing, we need to understand the behavior of leaf springs during acceleration and braking.
When you apply drive torque to a leaf spring solid axle suspension, the torque that is trying to rotate the wheels forward is also trying to rotate the whole axle housing in the opposite direction. This is called the reaction torque.
What keeps the axle from actually rotating is the suspension, which holds the axle to the vehicle. But in the case of a leaf spring suspension, the leaf springs ARE the suspension. Leaf springs by their nature aren’t very stiff, otherwise they wouldn’t be very good at being springs, so they have a hard time dealing with this reaction torque. The result is they get twisted into an “S” shape, with the axle pivoting around a point somewhere along the length of the spring, like this:
Under normal circumstances this isn’t really a problem. Normal acceleration would just twist the spring slightly and then when you let off the gas, the spring would return to its normal shape, and everything would be fine. Unfortunately, that’s not the case if you accelerate hard or if you are on a more slippery surface like a wet road. What happens then is that the spring deforms into an “S” shape but as soon as the wheel loses traction, the spring snaps back straight. Then when the wheel regains traction, the spring twists into the S shape again until the wheel loses traction again. This can start a cycle that can happen several times per second and can cause the wheel to hop up and down and forward and backward. If you’ve ever experienced this, you will know that it can be quite violent and can even cause damage to the vehicle. Terms like “axle tramp” or “axle hop” are used to describe the problem, and it was particularly bad years ago when high powered muscle cars still had leaf spring rear suspensions. It was common back then to add traction bars to these cars to help reduce the axle hop by preventing the twisting of the springs. If you’re my age, you will remember seeing a lot of these in the high school parking lot.
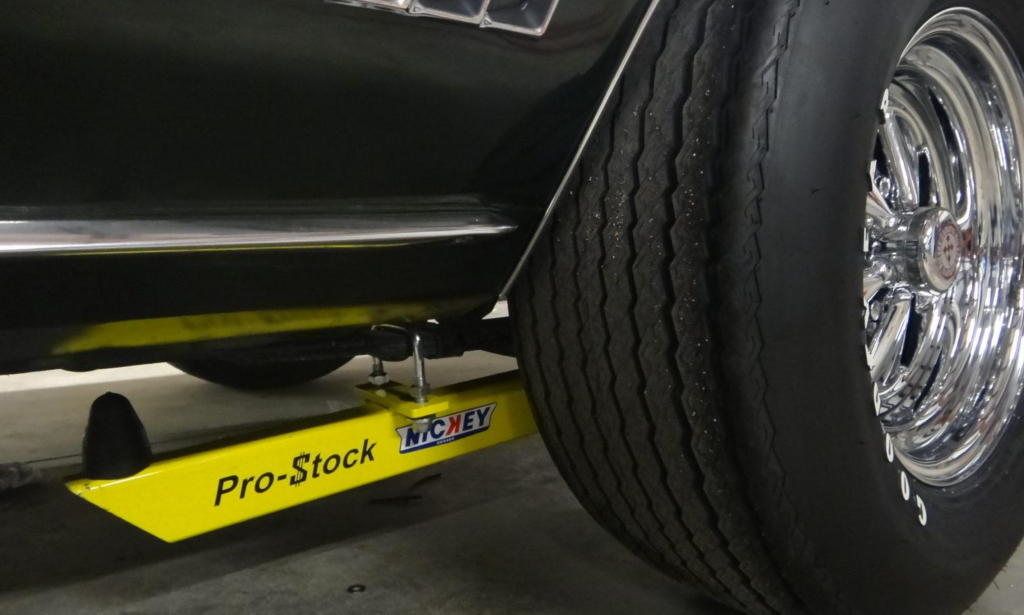
And even though cars stopped using leaf springs decades ago, they are still very common on pickup trucks, so this isn’t a problem from a bygone age.
By the way, I’m talking here mostly about axle tramp under acceleration, but the same thing can happen during braking as well. The axle just gets rotated in the opposite direction.
Adding Shocks
Let’s go back to our diagram and see what happens if we add some shocks. To start off, we’ll put them behind the axle like this:
Now, when we apply acceleration torque, we get this situation:
What happens is that the spring still twists into an “S” shape, but because we added a shock, the point the axle rotates around has changed. Shocks work by providing a force when you try to move them, so they resist motion. As the axle tries to rotate, the force in the shock requires the axle to pivot around the point where the shock is attached to the axle. It doesn’t stop the axle from rotating, it just changes where the axle rotates. The same would happen if we mounted the shocks in front of the axle instead of behind it.
But what would happen if we mounted one shock in front and the other behind the axle? Let’s say we mount the right side shock behind the axle and the left side shock in front of the axle. Like this:
Now, when the axle tries to rotate, one or both of the dampers are forced to move since they no longer form a single pivot axis the axle can rotate around:
However, since shocks generate a force when they move, they resist the rotation of the axle and thereby resist the twisting that happens under acceleration. In this way, having the shocks “staggered,” dampens [Ed Note: I asked Huibert if this should be damped, and he said he often says dampen. And given that he designed the Ford GT and Tesla Model S suspension, I’m gonna just say that he gets to make the rules. -DT] out the rotation of the axle and stops axle hop and tramp.
Other Types of Solid Axles
So far we’ve only talked about leaf spring suspensions, but the same hop and tramp can happen with a coil-sprung four or five link solid axle as well, especially if the links use relatively soft bushings for a quiet and comfortable ride. Back in the 80’s this became a big problem for Fox body Mustangs and Thunderbirds, so Ford came up with a novel solution using a second set of shocks, called Quad-shocks. They were small shocks mounted horizontally between the axle and the body, one on each side of the car. The image below shows a yellow Bilstein “Quad Shock” on the back right:

Since they were mounted horizontally, they didn’t impact the vertical motion of the axle but when the axle tried to twist under acceleration, they worked together with the regular shocks to stop the rotation.
Lateral Spacing
While we’re on the topic of how shocks are mounted to live axles, there is another aspect we should talk about and that is the lateral spacing of the shocks relative to the wheels.
(36) Lateral Spacing of Shock – Why it Matters – YouTube
If you’ve driven behind pickup trucks, you may have noticed that the side-to-side location of the shocks varies considerably between different models of trucks. Some have the shocks mounted close to the center of the vehicle:
Others have them mounted much further outboard:
The question is: Does the side to side spacing of the shocks matter, and if so, why?
To answer that question, I built a computer model of a leaf spring axle and included two sets of shocks: one mounted outboard and the other mounted inboard.
With this model we can see the difference in how the shocks behave. To do this, we need to look at both vertical and roll motion. Vertical motion would be like going over normal road undulations and roll motion would be like going through a turn or when one wheel hits a bump.
Vertical Motion
Let’s start out looking at vertical motion. If we move the axle up some arbitrary amount, we can measure how much each shock moved and compare them. In this case, I’ve moved the axle up 121.225 mm:
If we now measure how much the shocks have moved, we see that the inboard shock moved 120.4 mm:
and the outboard shocks moved the same 120.4 mm:
This tells us that when the axle moves vertically, the shocks move almost exactly the same amount as the axle does. The ratio of the shock vs the wheel motion is therefore 1:1, meaning that for every millimeter the wheel moves, the shocks move a millimeter as well.
Roll Motion
But what happens when the body rolls? Similar to what we did for vertical motion, let’s roll the axle some arbitrary amount and see how the motion of the shocks compares with the motion of the wheels:
In this case, the right side wheel has moved up just over 70 mm but now the outboard shocks only moved 54 mm
and the inboard shocks only moved 37 mm
Both shocks moved quite a bit less than the wheel did. If we calculate the motion ratios now, we got 1:0.77 for the outboard shocks and 1:0.53 for the inboard shocks. This means that for every millimeter the wheel moves, the outboard shocks only move 0.77 mm and the inboard shocks only moves 0.53 mm. In both cases, the shocks moved a lot less than they did during vertical motion and that is the crux of the issue: the shock motion ratio on a live axle is different when the axle is moving vertically vs when it is moving in roll.
Why it Matters
OK. So what? Why would we care if the motion ratios are different?
When a vehicle moves down the road, it moves up and down over road undulations (vehicle dynamics engineers call this “ride”) and it also rolls side to side during turns and when one wheel goes over a bump. The body is constantly moving in both roll and ride and the job of the shocks is to control those motions, so the vehicle doesn’t bounce around all over the place. Since we only have one set of shocks, they have to control both ride and roll and we want the right amount of damping for both. Vehicle Dynamics engineers spend a lot of time getting the shocks tuned just right and while I’ve driven cars that have too much ride damping, I’ve never driven a car that had too much roll damping. Having lots of roll damping makes a car feel like it has more roll stiffness than it actually does. It will feel like it has a much bigger anti-roll bar because the vehicle isn’t “falling over” when you enter a corner. To accomplish this, we want to get the most performance out of the shocks in roll which means getting the best motion ratio in roll that we possibly can.
To further illustrate how the lateral shock position impacts roll damping, lets look at a fictitious vehicle where the shocks are mounted very close to the middle of the axle:
In this case, if we move the axle vertically, the shocks move with the axle just like they did for the inboard and outboard shocks we looked at before:
The problem comes when we look at roll motion, in which case the shocks basically don’t move at all:
If we had a vehicle with the shocks mounted like this, we would get great damping in ride motion but none at all in roll. That would not be a good situation. We need damping for both ride and roll which means we want the shocks to move as much as they possibly can for every ride and roll motion the vehicle encounters. We already know that no matter where we place them, the shocks move directly with the wheels during ride motions. But we also know that the closer the shocks are to the center of the vehicle, the less motion we get during roll. We therefore want to locate the shocks as far outboard as we possibly can so that we optimize their motion ratio in roll.
The Package Problem
Sounds simple, doesn’t it? So why doesn’t everyone mount the shocks way outboard like the truck pictured above? Why are some shocks still located so far inboard? The problem is package. Shocks are fairly tall things and the best place to mount them is unfortunately also where the frame wants to be:
We are very limited in where we can put the shocks. We can go inboard or outboard of the frame. Outboard would be preferable, but that’s also where the tire is. If we want to put the shocks outboard, then we need to make sure there is enough room between the tire and the frame. This may be fine for some trucks but if we need to accommodate dually tires, like a superduty truck does, there just isn’t enough space and we are forced to put the shocks inboard of the frame:
As usual, suspension design is the art of compromise, and this is just another example.
Independent Suspensions
So far we’ve talked about live axles, but what about independent suspensions? Do they have the same problem? Lets look at a model of an independent suspension and move it the same way we did before:
This happens to be a model of a front suspension but it could just as easily be a rear, it really doesn’t matter. Let’s move this suspension 40 mm vertically:
and measure how much the shock moved. We can see it moved 22.6 mm:
This gives a motion ratio of 0.56:1, meaning the shock moves 0.56 mm for every millimeter the wheel moves. Now lets look at the same suspension during roll:
In this case the right wheel moved up the same 40 mm and the shock has moved the same 22.6 mm as it did before:
This means the motion ratio in roll is exactly the same as it is for vertical motion and even though the ratio in this case is lower than it was for the live axle, we can deal with it more easily since it is always the same. The motion ratio we got here is only for this particular example. Other independent suspension designs could be much higher. The key here is that the shock motion ratio is not less in roll than it is in ride, and we can pick a shock setting that works well for ride without sacrificing roll damping.
Of course, there are trade-offs that have to be taken into account. For example, independent suspensions are expensive and live axles are cheap. That’s a big deal when you’re making a million vehicles per year and trying to keep the price down while keeping profits up. As in all aspects of vehicle design, we never get everything we want, it’s all a compromise.
If you have a question about suspension design or anything suspension related, send them to AskAnEngineer@theautopian.com and I will do my best to answer them.
Huibert’s write ups are the best!
Weirdly.
This is an excellent write up!
I’ve always noticed this on muscle type cars and wondered if there was more to it. Like is there a preference as to which side takes the front and back shock, in relation to the driveshaft rotation direction when gunning it forward?
2017- ? Colorado (ZR2 anyway) had shocks in board, skids were sold by after market cause this lowest point. At some point they moved them out for better clearance. This piece explains the +/- of both versions.
Semi-related, but how does this shock placement change with Chevy’s trailing arm (coil spring) setup they used from ’63-72, and why did they abandon it? Was it a good design?
In the 60’s and 70’s, GM used a 4 link setup to locate the rear axle. This reduced the wind-up and tramp problems significantly and gave much better handling as a result. Many years ago I owned a 1971 Monte Carlo (which I still have), a 1968 Ford Torino, and a 1968 Mercury Cougar. The Torino and the Cougar had leaf springs while the Monte Carlo had the 4 link with coil springs. The Monte Carlo, even though it was bigger and heavier, would run rings around those other cars. That rear suspension was vastly superior. Burn-outs all day long without tramp or hop.
I wasn’t clear; I was referring to the trailing arm design seen on the C10. I’m not a suspension expert, but I don’t think it was a 4-link.
That’s right, it’s 2 trailing control arms that the coil springs sit on, plus a panhard rod. You can see a good diagram here https://www.lmctruck.com/1967-72-chevy-gmc/suspension-front-rear/cb-1967-67-rear-suspension-with-coil-springs
I’m no expert, but I’d imagine Chevy abandoned it because it was cheaper and easier to use a standard leaf spring setup. And whatever ride benefit there is, didn’t help with sales or profits in their eyes
Yes, I see how this is made. The biggest problem is that the whole thing is basically made out of three very rigid pieces: the axle housing and the two trailing arms. All three are rigidly connected together. When the truck rolls in a turn, the trailing arms need to be able to move in opposite directions, one up and one down. Since everything is beefy and rigidly connected together, that can only happen if one of them bends. More likely than not, what will happen is that the connections between the parts, i.e. the U-bolts, will slip and work their way loose and eventually fail. I don’t know if these have a history of sailing but that is what I would predict would happen.
No history of failing even on the “3/4 ton” trucks. The “truck arm” suspension is what every Nascar legal car was required to use for ~40 years. It wasn’t until recently that it was retired.
Great article as usual.
I’m of sufficient age that I think Chrysler was the king of muscle car leaf springs with springs biased against wind-up and the pinion snubber on the rear axle.
Excellent explainer and you should get overtime for your illustrative models. So your enthusiasm for writing is not dampened.
My wife insists I post this. “Weirdly”. Not “weird”
Weirdly is indeed correct. I before E, except after C or when sounding like A as in weigh and neighbor. Except for one word….. weird. Gotta love the English language.
There’s more exceptions to the “I before E except after C” rule, than there is words which adhere to it. It basically depends on which root language the English stole the the word from. And we steal from a lot of different languages.
I read the headline and thought, “pickups have the shocks mounted completely normally.”
Yeah, they do.
Thanks Huibert, I always learn something (actually, a lot) new – even the terminology is new to me…I’d never heard “tramp” before.
But have a odd pragmatic question and this seems as good a place as any to ask.
I have one of those Mustangs with the quadra-shock setup. I’m getting ready to replace the main shocks and struts, and wondered if I need to do the quad shocks too? Do they wear like the vertical ones and should be replaced at the same time, or do they last longer since they’re more stabilizer in function?
I always thought that a torque tube instead of a drive shaft was an elegant solution to axle tramp. Why isn’t it common ?
A torque tube would certainly fix tramp but it severely limits what you can do with the suspension geometry since it forces the axle to rotate (in side view) about the front point of the torque tube as the axle moves up and down. Anti-lift and anti-squat are very limited in those designs.
True, although I must admit that most of the pickups I have been exposed to handle like a pogo stick so I was pretty oblivious squat and dive characteristics.
Those Peugeot 504 and 505 station wagons seemed pretty civilized considering that they were pretty good on terrible “roads”. On the other hand, the French don’t really care how silly a car’s dynamics look from the outside.
The Peugeots were very robust and were used a lot on the roads of Africa.
The other question this article just brought to my mind is what was the last car sold in US and/or Canada that had a solid axle leaf spring set up?
Technically, leaf springs are still in production in cars. The Volvo SC90 (technically an SUV, I suppose) has a transverse leaf spring in the rear. The C7 Corvette had a transverse leaf spring in the rear. But I believe the last US/Canadian car to use leaf springs in the form of a Hotchkiss arrangement (which is what pickups use) was the 1981 Camaro/Firebird.
I believe Sentras had it almost until the millennium, and every Dodge minivan had leaf springs until 2008. I’m certain LTDs and Caprices had leaf springs long after 1981 too. Not quite that many decades.
B14 Sentras/200SXes had a beam rear axle, but as I once replaced the springs on my 200SX I can confirm they were traditional coils on all four corners. I assume the B15 that followed had the same arrangement.
Man, you guys are awesome. Thanks for correcting me.
LTDs and Caprixes have coil springs in the rear, for since before the 70s.
A minivan is a minivan and not a car. Now that I’ve done a bit more research it appears that the last car was the M-body Chrysler which lasted until 1989.
According to the Internet the last leaf -sprung solid axle car was the ’89 Dodge Diplomat
The other bonus to staggered shocks is it can result in less unique parts. Many older leaf set ups the u-bolt plate does double duty as the lower shock mount. That means you only need 1 part number that will do both sides.
The one thing I don’t see mentioned is how the angle the shock is mounted at affects all of this. Many shocks are angled and some angle them fore and aft while others angle them side to side. To my untrained eye it seems that those angled fore and aft could do better at controlling spring wrap but those that are angled to each other could be better at controlling roll.
I don’t have much to add in a comment, but commenting anyway so I can make sure the editors know how much we appreciate this type of content!
On the topic of of Damp vs Dampen. Damp is the correct word in this situation. To Dampen something is to make it wet. I work for a company that builds vibration isolators and helicopter lead lag dampers, I can assure you the engineering professionals in the industry do not use the word dampen. I can’t tell you that many people on the business and marketing teams accidentally call a helicopter lead lag damper a lead lag dampener.
This is an excellent article. I always figured axle wrap was why shocks were mounted front and back of the axle, which isn’t the case on my Jeep Comanche. In the right situation it will axle hop real bad.
I think this will be an on-going discussion in linguistic circles. According to the Oxford dictionary, “Dampen” has two meanings: 1- Make slightly wet, 2- Make less strong or intense. Merriam-Webster similarly shows two meanings: 1- To make damp, 2- to check or diminish the activity or vigor of. I think it becomes a personal choice and I suspect some industries have consensed on specific meanings for specific cases and systems.
In the case of gunpowder and girlfriends if you leave them out in the rain it tends to diminish their activity or vigor so it’s both!
As an aside, the mechanical engineering terms for shocks/struts “damper” and “dampener” are also both correct.
Please keep these articles going! I tend to go down “but why” rabbit holes for cars, and this really scratches that itch. Keep it technical and nerdy
I second the sentiment of the above comment.
While I read every article posted here, Huibert’s are the ones I go back and reread on rainy days
Don’t worry. I really don’t know any other way.
I had always wondered why shocks were on opposite sides of the axle. Thanks!
Another awesome article Huibert. Thank you! 🙂
The 96+ Chevy S10 with the ZQ8 suspension package had a 3rd lateral shock to help with wheel hop as well.
Ram 2500 trucks still have this today, except it’s a single shock mounted in the middle.
Thanks for letting me know. Always love hearing about how others solve problems.
Some number of Gen2 Explorers had a 3rd lateral shock as well, it was only on certain years/models. I think it was for the shitty “active” suspension that was around on the limited model for the first few years. I don’t think it made it past 1998 though. Didn’t help much, they all handled like shit anyway.