Last week David Tracy and Jason Torchinsky showed us some pictures of the upcoming Slate EV, which is going to come equipped with a MacPherson strut front suspension and a De Dion setup in the rear. The Slate EV is meant to be very inexpensive, and in trying to keep the price low, we will likely see many examples of design decisions made in the interest of cost. The choice of suspensions is a good example of this. Let’s talk about it.
MacPherson front suspensions have adorned cheap cars for decades. They are easy to manufacture, cheap to assemble, and relatively easy to maintain and service. The low number of parts involved in their design helps keep cost low. Considering the fact that this design has been in use in cheap FWD cars for the past 30-40 years, you’d think they were just that: cheap, but not very good. You’d be wrong though.


A MacPherson strut is cheap to make but can also perform very well if designed properly. The BMW 3 Series has used a MacPherson strut since time immemorial and the Porsche 911 has used one since 1989 when they switched away from the independent torsion bar system the car was originally introduced with. Nobody would say the suspension on the BMW 3 series and 911 don’t work well!
So, the choice of a MacPherson strut as the front suspension in the Slate EV seems like a logical move. Cheap to make but can work very well if properly designed. We’ll reserve judgment on the second part of that sentence once we get a chance to drive it.
But what about that rear suspension? Why choose a De Dion? My guess is that most Autopians have never heard of it. In fact, the chances of seeing one under any car built in the last 130 years are pretty slim. Very few OEMs used it. Let’s have a little history lesson to bring us all up to speed on what a De Dion axle is.
What Is A De Dion Suspension?
The De Dion axle takes its name from Jules-Albert de Dion who founded the French automobile company De Dion-Bouton in 1883. And while the axle has the name of the company founder, it was actually invented around 1894 by co-founder Georges Bouton’s brother-in-law Charles Trépardoux. At that time, De Dion-Bouton were building steam powered cars which had the engine and driveline mounted at the rear of the frame. Since the engine was mounted in the rear, there was no room for a driveshaft between the engine and the differential. Many cars and trucks of that era with similar powertrain layouts used chain drive to connect the powertrain to the wheels, but perhaps Trépardoux felt this was not adequate for their cars.
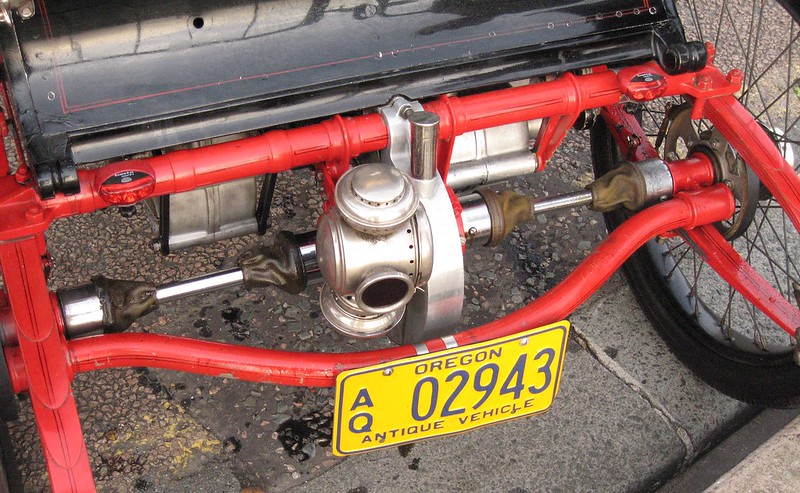
Whatever his reasons, he designed a suspension that solved the problem of getting the power out to the wheels without the need for chains or a traditional driveshaft.
The design consists of a left and right hub, rigidly connected to each other by a large metal tube, a center mounted differential, and two short halfshafts connecting the left and right hubs to the differential.
Patent drawing via: De Dion Suspension History – Historic Vehicles
Since the hubs were rigidly connected to each other via a connecting tube, the whole assembly acts very much like a solid live axle. The wheels are kept at a constant camber angle and maintain their relationship to the ground. Of course, the axle also has the same issue as a solid axle does where when one wheel hits a bump, it causes the other wheel to tilt. It’s not an independent suspension
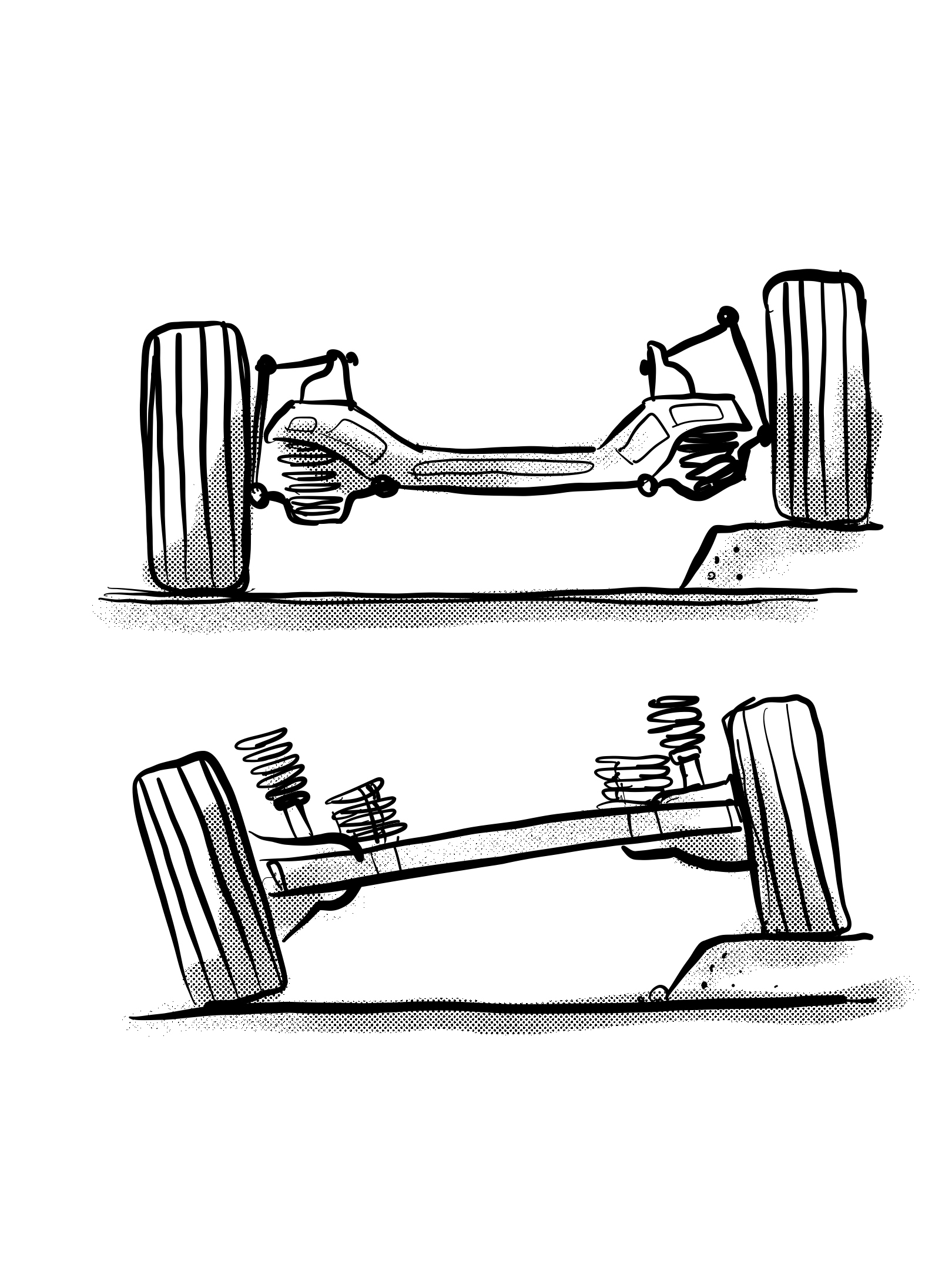
However, the fact that the differential is not part of the axle assembly means you need two halfshafts to transfer the power from the differential out to the wheels. In this way it is similar to an independent design.
In the image two above, the axle is shown mounted on leaf springs, but the beauty of the design is that it can be mounted just like any solid axle can: with leaf springs, coil springs, 4 links, Panhard rods, Watts links, etc. Any way you can think of to mount a solid axle can also be used to mount a De Dion. But no matter how you mount it, one difference always remains: While a solid axle includes the differential as part of the suspension, the De Dion takes the differential and mounts it to the frame, and that is one of the great advantages of this design and why it is such a winner for an EV.
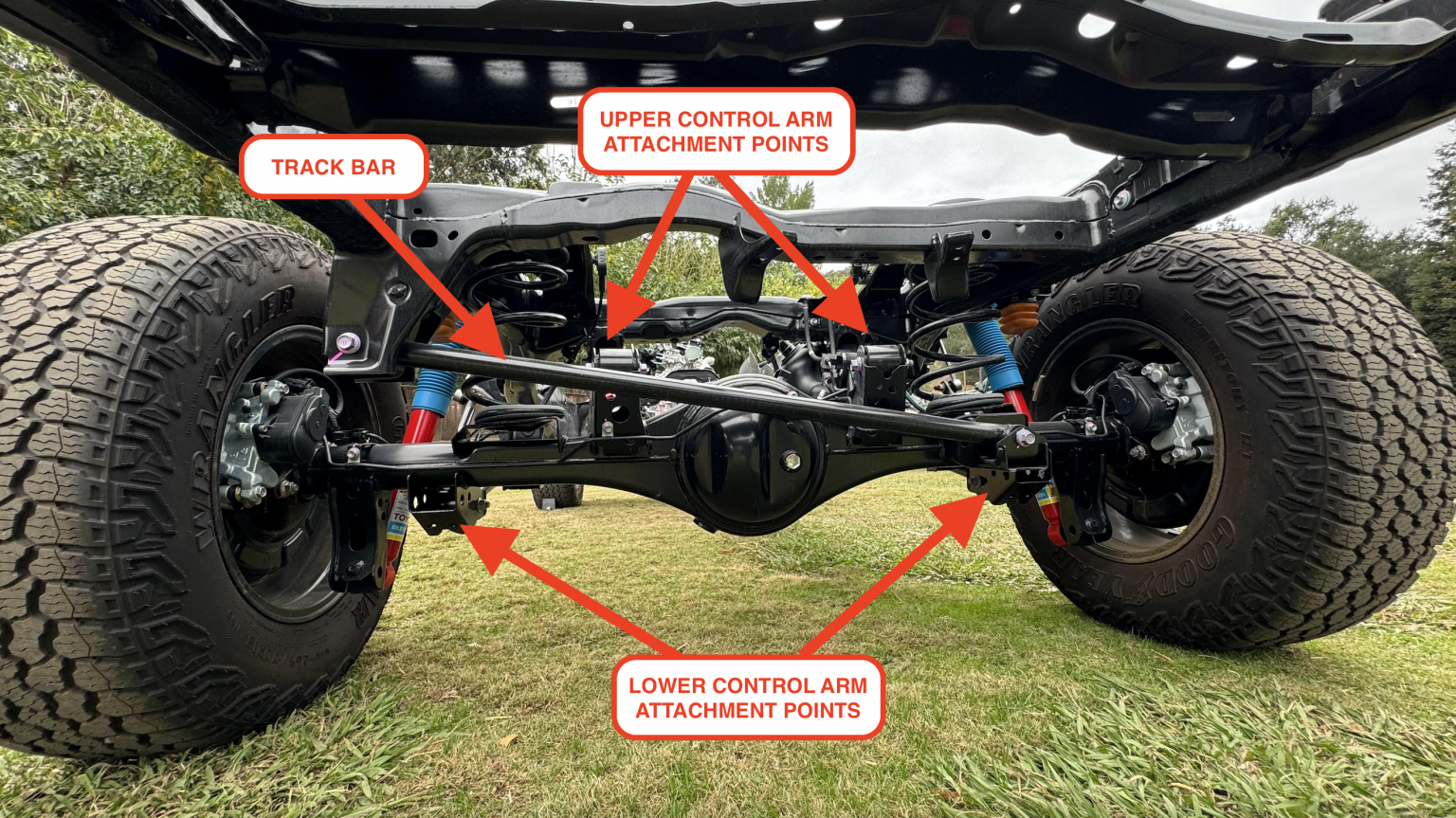
The reason this is so important is that differentials are heavy, and when they are part of the suspension, they have to move up and down with it as well. It’s called un-sprung mass.
Un-Sprung Mass
When a solid axle encounters a bump in the road, the wheels and suspension have to move up and over the bump. When the differential is part of the suspension, there is a lot of mass that has to be forced up and over the bump. All that mass then has to be slowed down by the springs and dampers and pushed back down to let the tires maintain contact with the road.
In the old days of luxo-barge American cars, springs were quite soft to give a plush ride. This meant there wasn’t a lot of force coming from them to help push all that mass back down after a bump. The result was that the axles would “dance” and tramp, losing traction in braking, accelerating, and cornering on rough roads. Having the differential disconnected from the axle means far less un-sprung mass and a much smoother and more controlled ride as well as better handling since the tires could better maintain contact with the road. It’s interesting that what we now see as the primary advantage of the De Dion design wasn’t even an issue in the early days. I can pretty much guarantee that un-sprung mass and tire traction over rough roads did not even enter Trépardoux’s mind when he invented it.
Regardless of the reasons why it was invented, the design proved quite useful and saw a lot of use up through the 1920s. It fell out of favor for a few decades but was then used extensively by Alfa-Romeo in the Alfeta, GT, GTV, GT6, Alfa 6, 75/Milano and others.
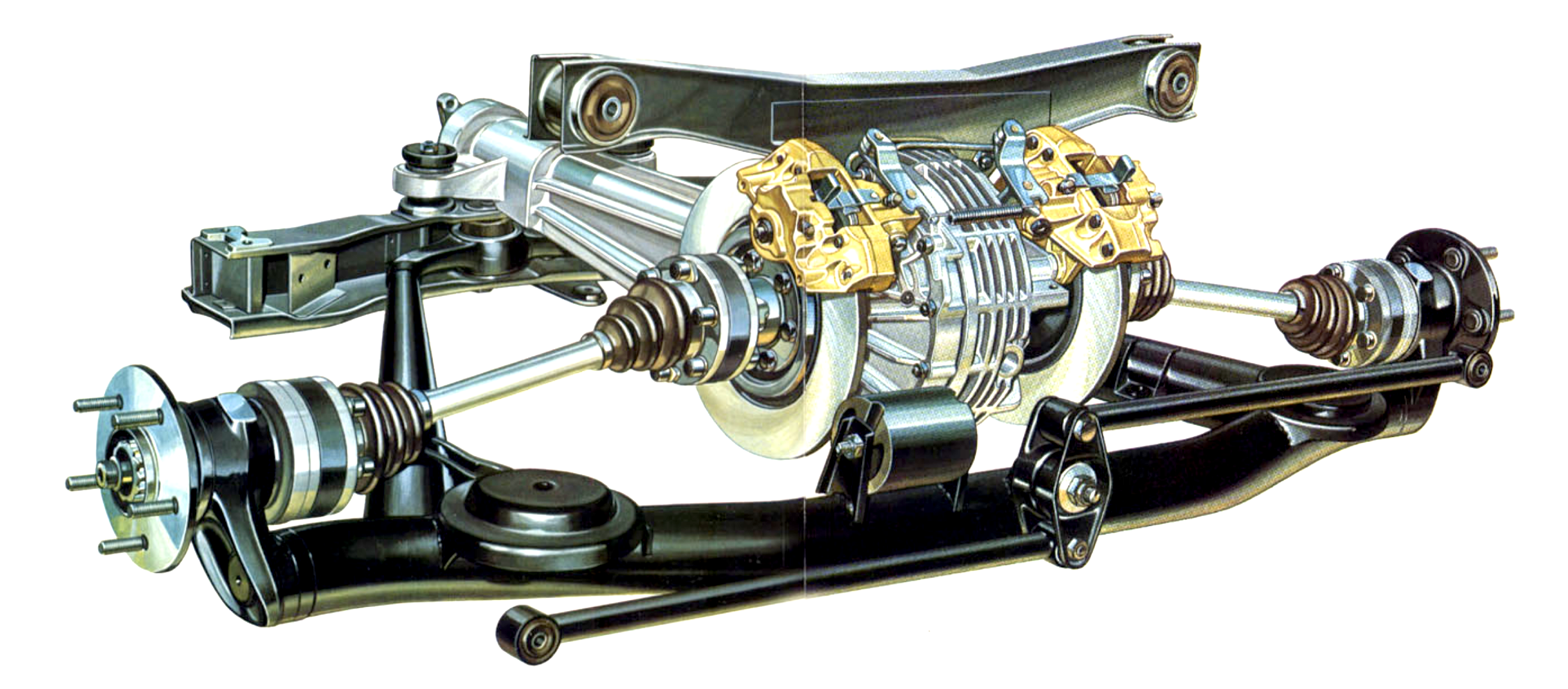
It was also in use on all Aston-Martin cars from 1967-1989. It is now used on several electric trucks as well as the Mercedes-Benz EQG.
[Mercedes’s note: All three generations of the Smart Fortwo also have De Dion axles!]
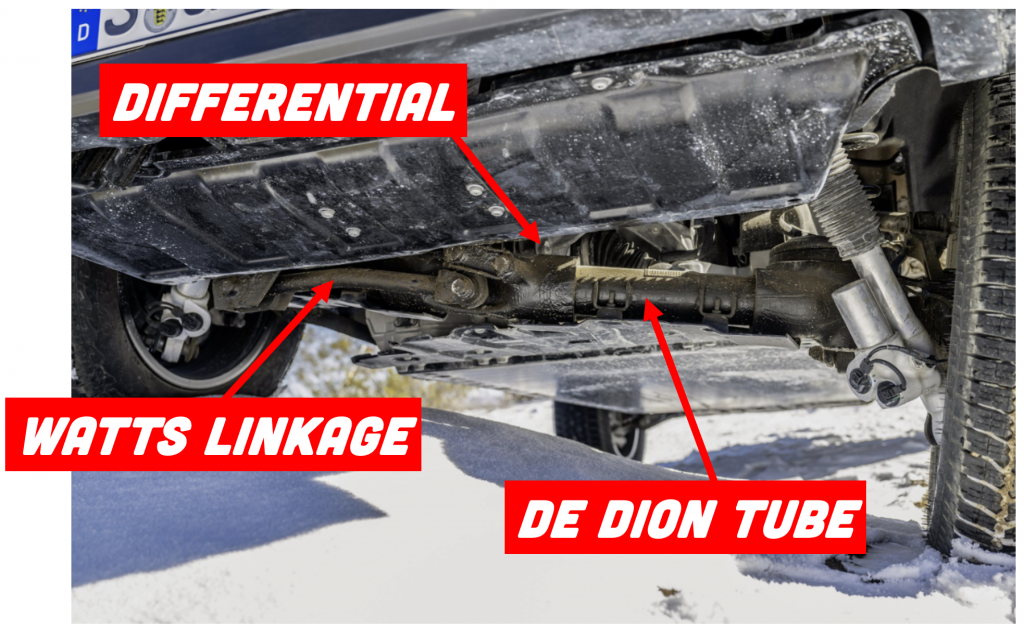
Why Is This So Good for EVs?
So, why does this design make so much sense for an EV? If you watched the video David Tracy and I made about the Ford F150, Raptor and Lightning (see above) you will remember how the package of the battery in the Lightning meant there couldn’t be a traditional driveshaft running down the center of the vehicle. All that space was needed for the battery and it forced the electric drive motor to be packaged in between the rear wheels right where the live axle needed to be. Ford’s answer to this problem was to ditch the live axle and design an independent rear suspension using two trailing arms.
They could have used a De Dion but decided against it, I believe, for package reasons. Look again at the early patent drawing above and the image of the Alfa suspension. In the patent drawing, the tube runs underneath the differential. However, in later cars where ground clearance is at a minimum below the diff, there isn’t room for the tube. The solution is to place the tube behind the differential. In an F-150 Lightning, however, this is where the spare tire is and making space for a De Dion tube would have meant a longer rear overhang. Since Ford’s desire was to reuse as mush sheet metal as possible, a longer rear overhang was out of the question. It meant the De Dion would not have worked for them.
So, the short of it is that, in an EV, a De Dion tube works so well because it’s simple, rugged, offers good articulation, keeps unsprung mass down (which would be a big problem given that, unlike on an ICE, a solid rear axle “eBeam” includes the electric motor), and still allows for rear motor packaging, which is necessary, because the battery takes up all the space in the middle of the vehicle. There’s a reason why well-known EV-conversion specialist EV West sells these in bulk.
Specifically, EV West sells the De Dion tube axle that came in the rather rare Ford Ranger EV. Here’s a look at a stack of Ranger De Dions:
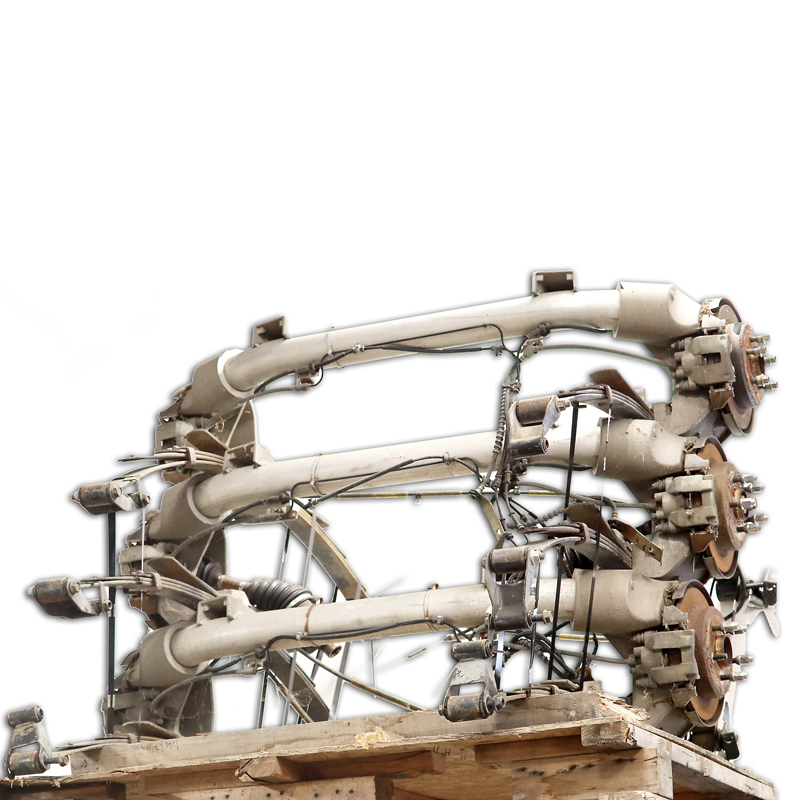
As EV West notes, this simple suspension makes mounting a rear drive unit in a gas vehicle that already has a solid axle easy, making for a clean conversion:
These are De Dion axles from the original Ford Ranger EV that was produced in 1998-2001. These are a great path to mounting a Tesla motor in the rear of your pickup or van project to free up the engine bay for the battery pack. These will also maintain the full efficiency of the Tesla drive by allowing a transverse mounting. Ford engineered and manufactured. These are limited to quantity on hand.
The Slate De Dion
Slate, however didn’t have the Ford F-150 Lightning’s packaging problem. The new company mounted its (optional) spare tire on the rear tailgate so there is nothing behind the differential. There is plenty space to package a De Dion tube. That doesn’t mean they didn’t consider other option, though. Based on a conversation David Tracy had with Eric Keipper, Slate’s head of Engineering, we know they looked at numerous other suspension architectures, including independent suspension and beam axles.
Beam axles for EV’s, sometimes called E-Beam’s, are under development by several companies and are designed to replace the live axles currently found in almost all pickup trucks:
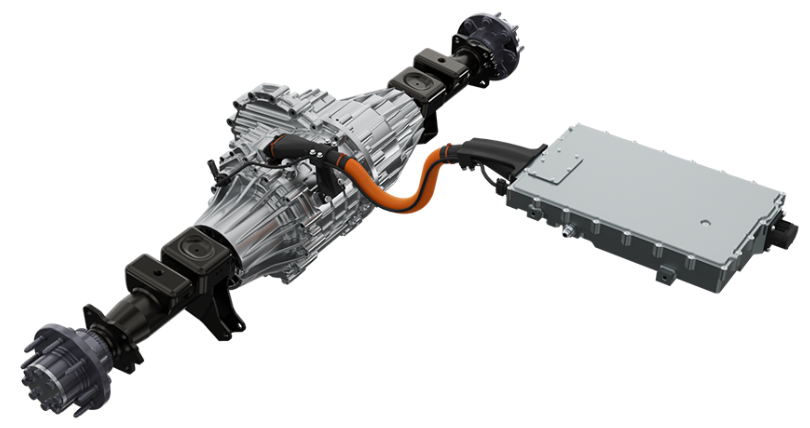
These axles are designed to swap in place of a live axle with minimal modification to the truck’s design and can be mounted using any of the usual live axle spring and link systems used today. But while a traditional live axle contains the differential as part of the axle, an E-beam includes the entire electric motor as well. All that mass is now moving up and down with the wheels over bumps in the road. As we learned earlier, a live axle isn’t great from a ride and handling perspective due to high unsprung mass. Now imagine adding the weight of the electric motor to it. Also, the majority of e-beam type axles under development are designed for larger pickups since that is where the market is. They are not meant for a low-cost small vehicle.
A beam axle was therefore ruled out early in the process since no designs were available for the class of vehicle Slate was developing. This left the De Dion as the natural choice.
Slate’s implementation of this design can be seen here:
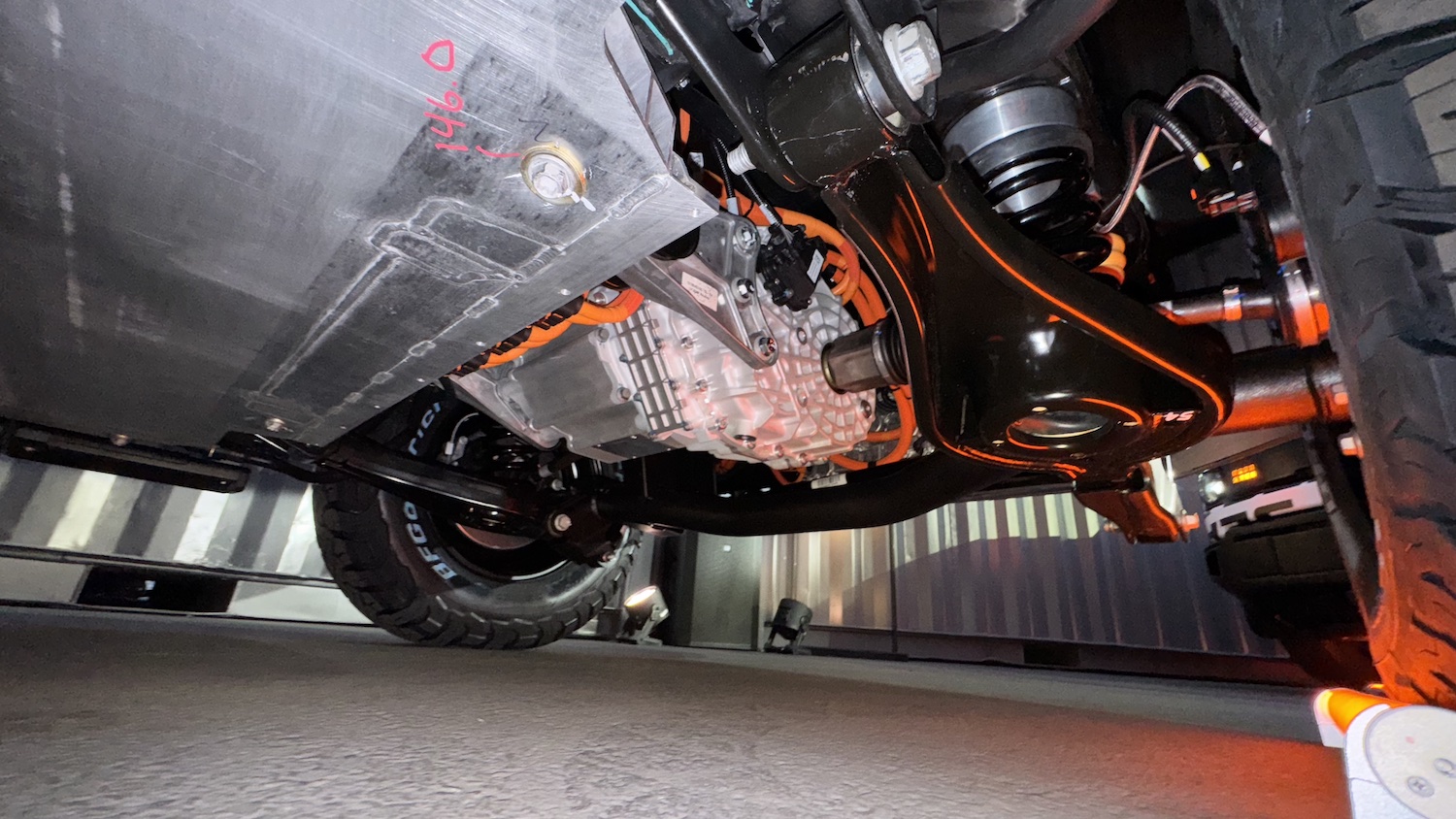
As I mentioned earlier, De Dion axles can be mounted in any of the many ways live axles can. Slate chose to use a classic 4-link design with a Panhard rod. Cheap, easy to make, and easy to assemble. The two lower links are clearly visible above as well as the Panhard rod. The upper links are a bit buried in this image, but you see the bolt holding the left side link to the De Dion tube. It’s a very good solution and should work well for them. The only thing that does stand out to me is that I would have preferred to see the Panhard rod be perfectly horizontal. The angle shown above will cause some side-to-side motion of the rear end over bumps and undulations in the road which could easily be prevented with a more horizontal installation angle. Perhaps this could be a future ride and handling upgrade (Note: This is a preproduction unit).
All things considered though, the design looks quite decent. A De Dion makes perfect sense for a low-cost truck-like EV. It’s relatively cheap, easy to make and due to lower un-sprung mass, will work better than a live axle or e-beam.
Peugeot 604’s and most 504 sedans\coupes had a DeDion rear suspension, those was the first one I ever saw. Very cool.
You guys listed several examples of de Dion suspension, but left out what is very likely the highest production de Dion axle of the last 50 years or so:
AWD Chrysler minivans, both generations, used a de Dion rear suspension.
The regular minivans used a dead beam axle that was just a pipe, so it made sense for the AWD version to keep the same suspension and just add half shafts. Those minivan de Dion axles are the only ones I’ve actually seen in person.
Didn’t old Jaguars use a De Dion axle with inboard brakes to further reduce unsprung weight?
Independent double wishbone, not de Dion.
The Jag system used a “H” arm as the bottom link and the driveshaft as the upper link. It’s called an “H” arm because there were two attachments to the knuckle and two attachments to the differential on the inboard side. It made the arm look a little like an “H”. There were also links going forward from the H arms to the body.
Why my Autopian subscription is well worth the $.
If remember correctly, my tr6 used a similar setup. I differential was bolted to the sheet metal body with half shafts to the wheels. A common problem with aging tr6’s was the bolts eventually ripped themselves out of the sheet metal. The repair was to reinforce the mount under the spare tire and rebolt the differential the fix worked well, but like all British automobiles at the time, some other catastrophe would happen. I really enjoyed my 6, it just didn’t make sense for it to be a daily driver.
I had a 1971 TR6 while living in England and had to do the same repair to the differential mounts. Very common.
The suspension is very different though. The TR6 used 2 independent trailing arms. Halfshafts ran from the differential (which was mounted to the body) to the hubs using two universal joints. Since these joints do not allow plunge, there is a spline in the middle of each shaft to allow the halfshafts to change length as required.
I had a buddy back in the early ’90s who had a TR7. It was a fun little car–when it ran. Most of my memories of that car involved making roadside repairs so we could get back to the ship before the clock ran out on our Cinderella liberty.
If the TR6 was like other British cars of the era, there was always the possibility of the brakes or electrical system randomly bursting into flames. I think either of those would definitely qualify as “some other catastrophe.”
Great stuff Huibert!
I love these technical deep dives! Thank you for this, I learned a lot.
I don’t know if Ford would like to have their sheet metal called mushy, maybe a little rusty if treated badly enough. “Since Ford’s desire was to reuse as mush sheet metal as possible”. It did make me laugh since I have seen some very rusty trucks over the years.
Lol. Blame the editors!
Judging by the high volume of comments to this article, I’m thinking of opening a De Dion bar right next to the third most popular taillight bar. Business should be brisk.
There are quite a number of De Dion equipped vehicles from less than 130 years ago around… Some have been mentioned, Apart from those mentioned (most well-known are of course the RWD Alfas (like the Giulietta, Alfetta, Alfa 6, GTV, 75), the Caterham Lotus super 7 versions, as well as Lancia Aurelia and Flaminia and some Opels (Diplomat I think), DAF and even some Ferrari (Mondial/Monza, 410) come to mind as well.
Having the advantages and simplicity of a live axle without the unsprung weight associated was not a totally bad thing for several designers.
My god Huibert, you’ve managed to cram some understanding through my thick skull. I’ve spent the past week feeling left out because I didn’t understand what’s so special about of Dion but now I finally get it! Now I can finally join the cool kids club!
Welcome. We have cookies
I know just enough about manufacturing to be dangerous. I’m baffled by the choices made in design and specification. What problem are they trying to solve? Who are their customers? And how in the world will they be able manufacture this thing and not lose tons of money on each one? The specs and the design are interesting but show me the factory. Show me the list of suppliers. Tell me about the logistics of how this thing will be put together. The product itself, its features and design, is secondary to their ability to execute the build and control costs. What about distribution? Service? Parts? Repair? This is vapor. There is no car.
Twist beam rear suspension on 2WD Maverick. I’m a fan. Enjoyed reading information about future Slate pickup. It will be a hell of a comparison Maverick vs. Slate in respect to value.
New Maverick?
I love the twist beam axle after using one from a Subaru.
Subaru doesn’t make any never has made a vehicle with a twist beam suspension, unless I am very mistaken.
There are multiple names for it, so I may have the terminology not quite right.
It has a rigid tube with a torsion bar inside it, damped by a coil spring in the center, which is adjustable.
The rigid end pieces rotate on the spring assembly.
Shocks are mounted on the hub assembly and the rigid part that was attached to the frame.
Later versions had two subframes instead of one piece, but were essentially the same.
Mine is from the wagon and is slightly stronger.
Maybe a 70s DL 2WD?
I’m still using the suspension.
Honda Acty kei truck used a de Dion axle in the rear due to its mid engine layout. The Z as well. Works quite well for packaging. Many ev conversions also have de Dion axles as it’s easy to just use the leaf springs.
I believe Honda also used a de Dion axle on the first-gen H-RV, which was based on the platform of the fwd Logo model. The Logo used a 3-link beam axle, so the logical way of adding awd for the H-RV was to use a de Dion axle with the same 3-link location method.
Lovely read as usual Huibert. Question on the Panhard rod: I feel like most of the ones I’ve seen in pictures are at an angle so I thought that was standard. Or the rod is slightly kinked to reach up to the frame mount. Maybe a lot of the images I’ve seen are of lifted vehicles so they aren’t factory-designed.
The angle of the panhard rod will determine if the axle gets pushed sideways when it tries to move up and down. The axle really wants to move straight up and down, but the motion of the panhard rod is by definition an arc. It will therefore force the axle to move along this arc as well. What you want is for the arc to be as vertical as possible right near your normal ride height. That way the axle is pushed sideways as little as possible.
The pictures you’ve probably seen are of vehicles on a hoist where the wheels are hanging all the way down.
Why not use a watts linkage? less side to side wobble.
Bravo!
This is the same approach that Ryzon (Daimler trucks) is using for the rear suspension of their Class 4 (and 5?) EV trucks. Makes a lot of sense for these applications.