The Tesla Cybertruck’s bare metal panels are unique compared to the painted panels of most automobiles. Now that the truck is in the hands of customers, you may have read all the stories about the rust issues, as people learn how to care for stainless steel, and how it behaves out in the elements. Questions have swirled around whether the Cybertruck can hold up to the weather, and just what stainless steel is really capable of. Let’s take the Cybertruck as a jumping off point, and explore the reality of stainless steel in more detail.
The hubbub right now is that a number of Cybertruck owners have reported seeing rust spots on their vehicles, in some cases just days after taking delivery. This set off alarm bells, with outlets rushing to cover the story. Dig down into the forum posts, and it’s easy to see why some owners were getting upset. One poster known as Raxar shared pictures of small orange-brown spots peppering the body, as did OnTheSnap. and Vertigo3pc had a similar experience after a rain storm in LA.


Nobody wants a six-figure truck that looks like a crappy Walmart barbecue left outside in the winter. As good as the name “stainless steel” sounds, we’ve all seen some cheap stainless steel appliances plagued by the orange-brown rot of corrosion. Does that mean the same fate awaits the Cybertruck?
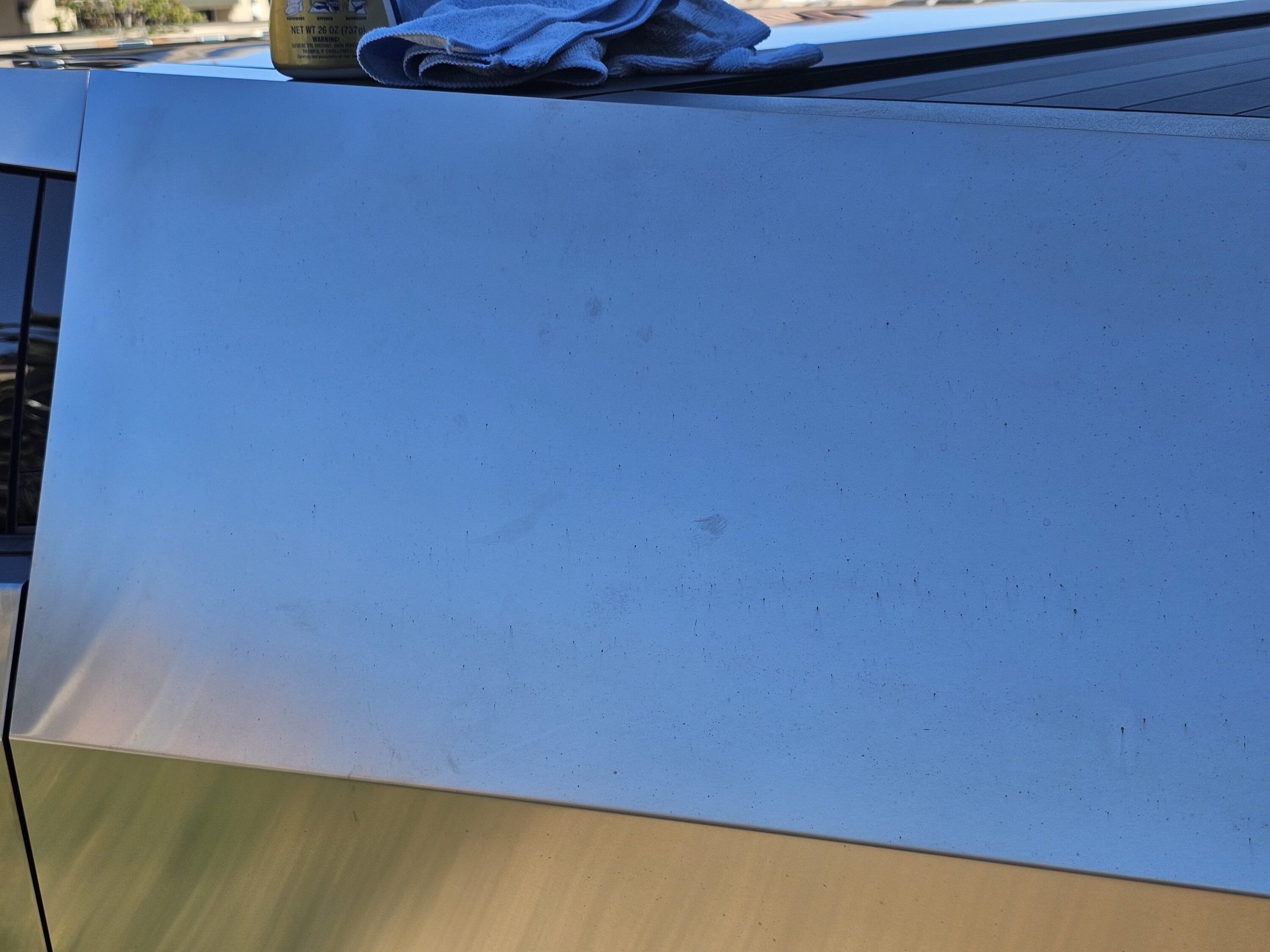
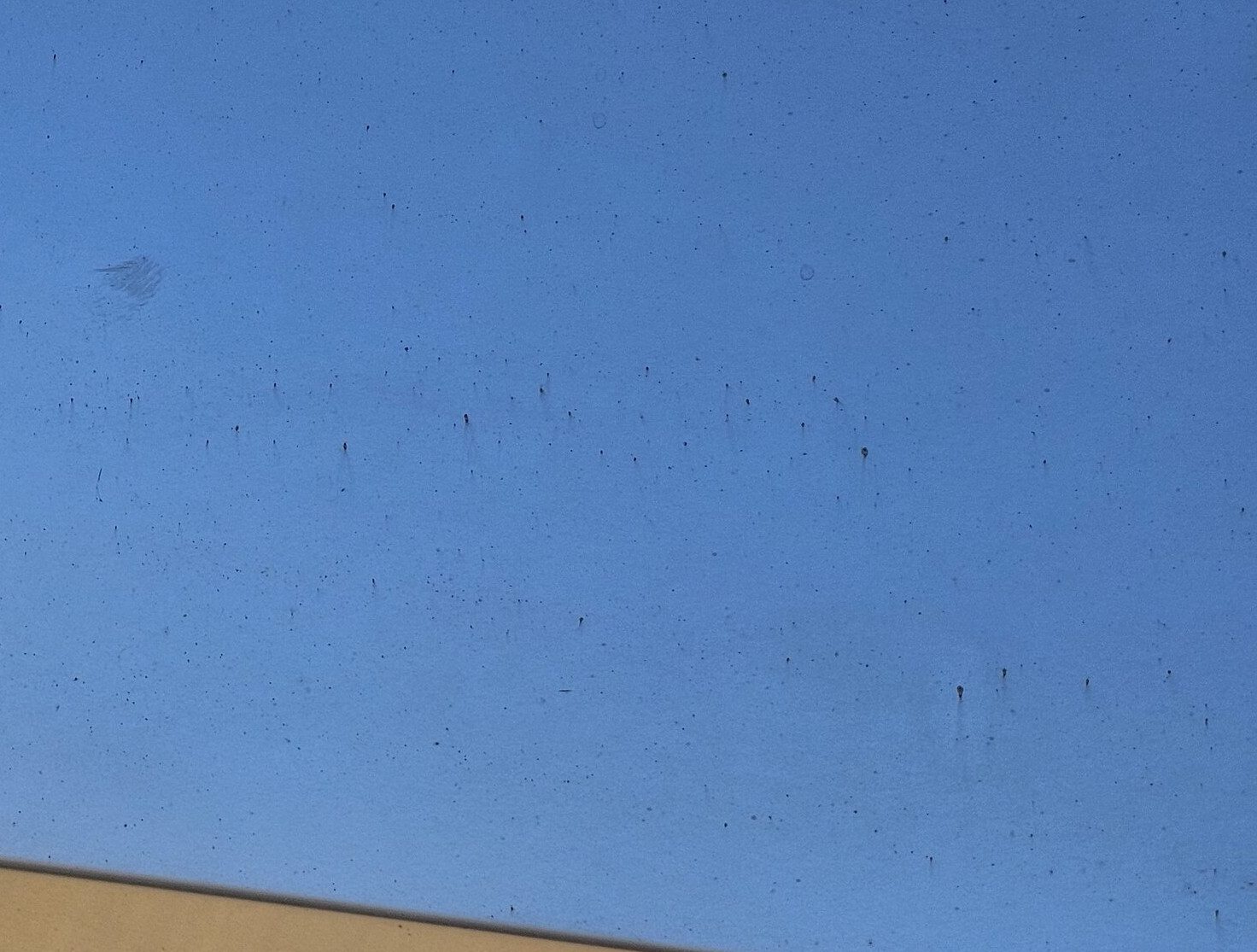
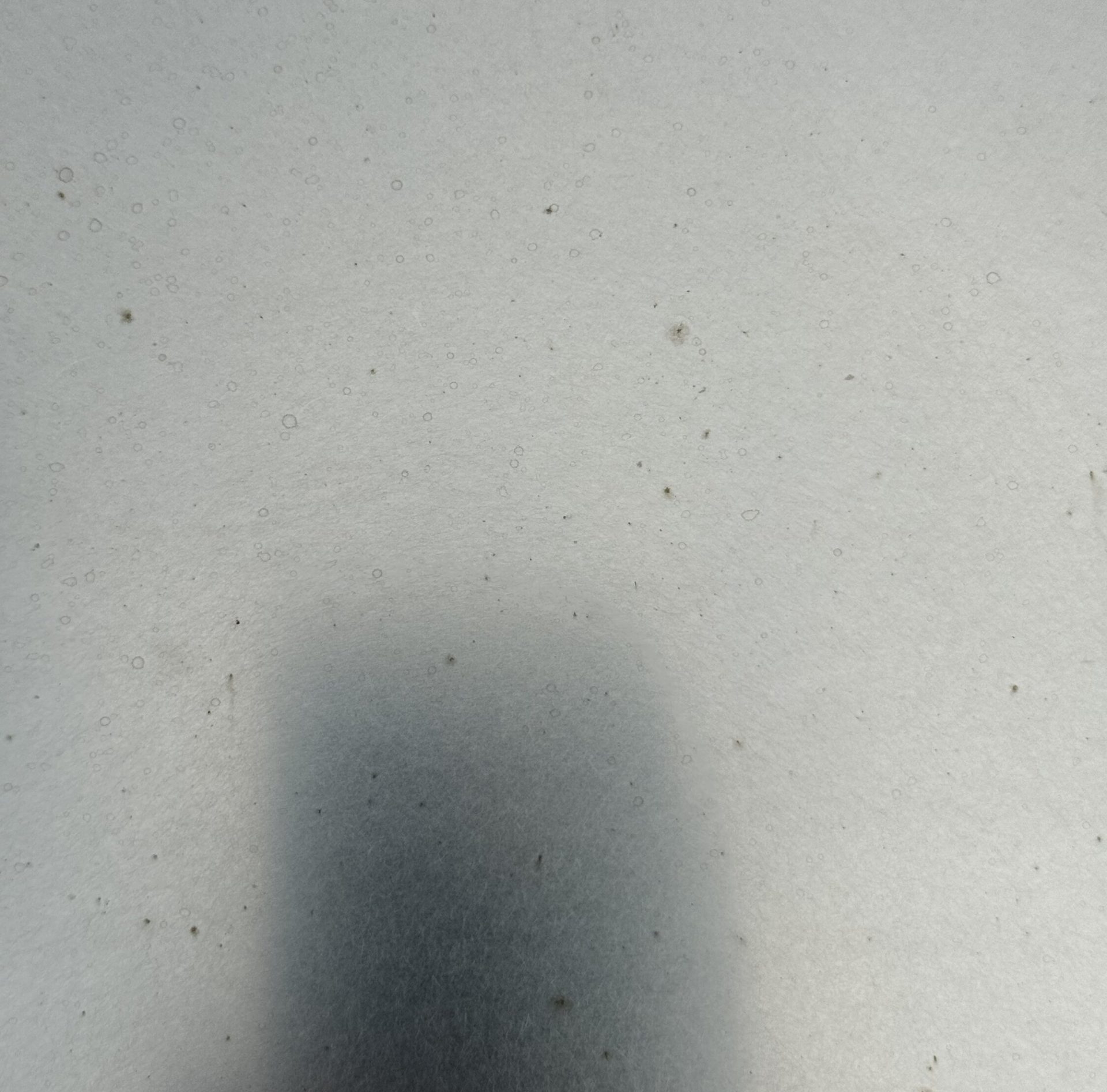
Speaking to The Autopian, vertigo3pc explained their discovery of rust marks on the Cybertruck. “I discovered the marks on my Cybertruck’s finish probably the fifth day I had the truck at home,” he explains, noting it was after a days-long rain storm in California. “I noticed the tiny spots on the right and left panels next to the vault.” The rusty-looking spots didn’t come off with the use of a clay bar, so he headed to the forums for answers. “I thought it was some sort of contamination, moreso than something sitting on the metal,” he says.
Multiple owners have since come forward to share similar photos of marks and rusty-looking spots on their new Cybertrucks. To understand what’s going on, let’s dive into some chemistry and see if learning about stainless steel can solve this problem.
Does Stainless Steel Rust?
Well, here’s where it gets complicated. Stainless steel is not one singular material. Instead, it’s a name applied to a great number of different steel alloys which are prized for being more resistant to corrosion than typical mild steels. Note that phrasing—more resistant. Not corrosion-proof, by any means. Nobody’s calling it “stainproof steel,” it’s stainless steel because it stains less.
That’s just wordplay, though (a joke). The true properties of any stainless steel alloy come down to its precise content and preparation. By and large, stainless steels normally contain at least 10.5% chromium, with carbon content anywhere from 0.2 to 2.11%. The chromium is the key components in its corrosion resistance. In stainless steel, chromium atoms in the alloy react with oxygen in the air to form a protective layer against further oxidation. This layer is only a few nanometers thick; for context, a human hair is around 50,000 times thicker. If this layer is compromised, such as by abrasion, further chromium atoms in the steel will react with oxygen and reform the protective layer. The process is called “self-passivation,” and it’s why many stainless steel items are able to last for decades without succumbing to rust.
Adding higher levels of chromium, or certain levels of nickel or molybdenum, can further improve the materials resistance to corrosion. That’s why some stainless steel items seem to rust quite easily, like cheap appliances, while others hold up far better, like quality stainless steel sinks.
Just because stainless steel doesn’t typically oxidize in open air, that doesn’t mean it can’t be corroded. Let’s explore grade 304 stainless steel as an example. Some grades, such as 304, are particularly susceptible to corrosion from chemical chlorides, with salt (sodium chloride) being perhaps the most common. Grade 304 stainless steel will tend to suffer pitting corrosion when exposed to salt water or salt spray. The mechanisms involves chloride breaking down the passive oxide layer on the surface, allowing corrosion of the iron content of the alloy itself. Once there is a small break in the passivation layer, a pit forms, in which a tiny electrochemical cell can be formed between the corroding metal and the base metal, which sustains the corrosion over time.
For demanding outdoor uses, grade 316 stainless steel is typically used. This grade is far more resistant to attack from chlorides, and pitting corrosion in general. This sees it used in things like street furniture and marine-adjacent applications. It all comes down to the molybdenum content in grade 316 stainless steel. The role it plays is complex, but in simple terms, it helps form a thicker passivation layer, and improves the layer’s ability to repassivate when damaged. This creates a stainless steel which is more resistant to attack by chloride ions than 304 stainless steel, which lacks the beneficial molybdenum content to support its chromium passivation layer.
Of course, you can’t just dump extra molybdenum into an alloy and call the job done. It’s not just about the input costs of the raw materials, either. Every tiny change to an alloy’s composition effects a wide variety of parameters. Crystal structures can change, affecting everything from strength to formability, melting points, and beyond. Picking the right alloy for a given application requires making the right tradeoffs between cost, manufacturability, and fitness for purpose.
You might want to make your car out of the most corrosion-resistant stainless steel possible, but then you find out it’s really expensive and nearly impossible to shape effectively. Thus, you have to compromise.
So what did Tesla use in the Cybertruck? Well, we don’t know. Tesla hasn’t specifically stated what alloy it uses in the Cybertruck’s body panels. We know the company refers to it as HFS, or “Hard Freaking Stainless.” As you might have guessed, though, that’s an internal term, not a common industrial grade of stainless steel. All we know is that CEO Elon Musk described it as a “ultra-hard 30X cold-rolled stainless-steel.”
Notably, being a 300-series stainless steel, it’s in the same class as the 304 alloy used in the body of the DeLorean. Ultimately, though, it’s hard to draw any direct correlations with the DeLorean without knowing its exact chemical makeup. In any case, the DeLorean was not free of corrosion concerns. Panels can suffer pitting corrosion over time, even badly enough to eat through the 0.8mm-thick (0.03-inch) panels.
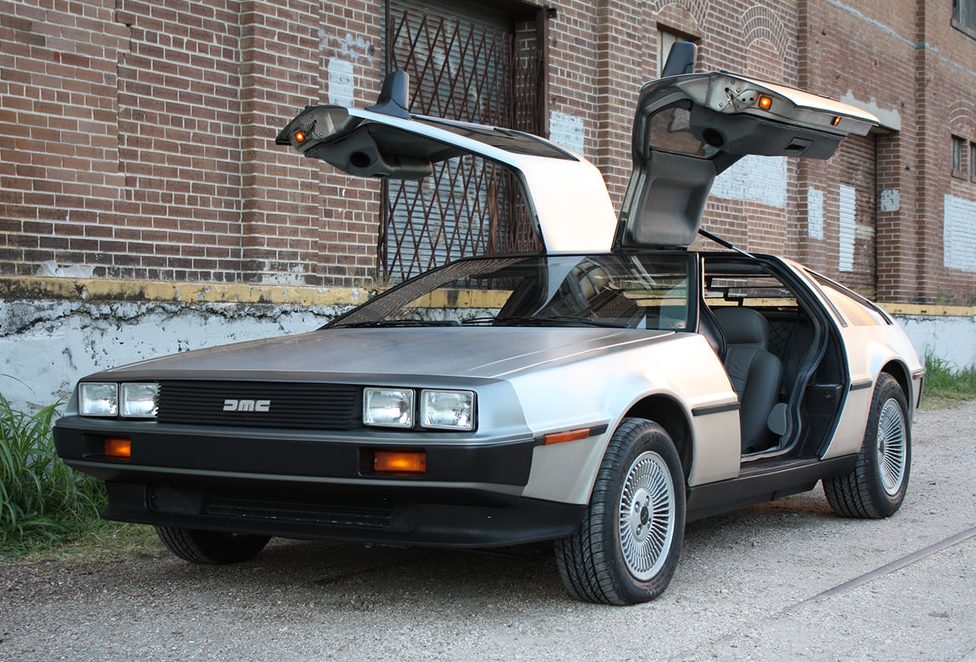
A Potential Explanation
There are other routes towards corrosion for stainless steels, too. One of the most common ways for stainless steel to rust is when it comes into contact with non-stainless steel. For example, using steel wool to clean stainless steel can leave tiny iron particles in the stainless steel which penetrate the passivation layer and enable further corrosion. Another common way it happens is when particulates from welding operations land on stainless steel in a factory environment. Cross-contamination can also occur when tools are used to cut both mild steel and stainless steel components. The presence of non-stainless steel particles can prevent the formation of a passivation layer in a small area, leading to corrosion.
Indeed, it may be iron in particulate form is the cause for the corrosion seen in some of these Cybertruck photos. We see tiny little spots where rust is occurring. These spots may be rail dust, tiny iron particles thrown up from train wheels and rails. Rail dust is a well-known problem in the car detailing community, particularly for people in areas with heavy rail use or for cars that have been transported via rail.
Rail dust can affect any car, but is most visible on light paint jobs. Once the tiny particles land on a vehicle, they can corrode on top of the paint – the problem has been around forever. The usual treatment to remove rail dust from a regular car’s paint finish is to use some kind of detailing product which dissolves the material. The solution is then washed off to avoid any damage to the paint.
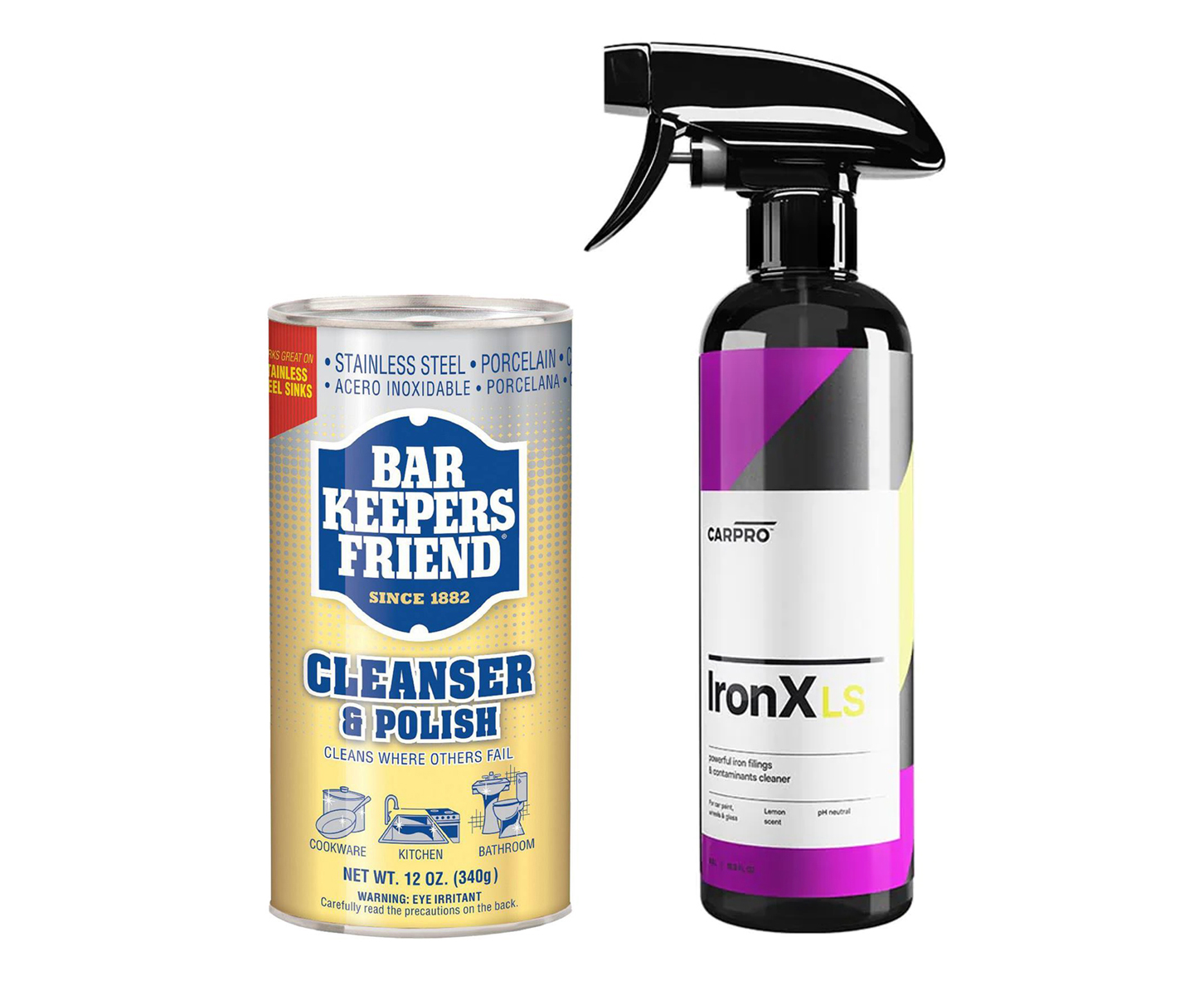
Reports from the forums support the rail-dust hypothesis. Both posters mentioned above found success cleaning off the spots using a product called Bar Keeper’s Friend. It’s a popular product for cleaning stainless steel, particularly in the hospitality industry, and contains three main ingredients. It’s made up of feldspar, likely used as a mild abrasive, sodium dodecylbenzene sulfonate, which is a detergent, and citric acid. It’s the latter that probably had the most beneficial effect on the stainless steel of the Cybertruck, helping to remove any iron contamination on the surface. Once rinsed off, the stainless steel would be able to reform its chromium passivation layer, and the panel would look unblemished once more. That is, as long as the corrosion was treated quickly and not left too long. If corrosion took hold and created deeper pits in the surface, more polishing would be required to get back to a smooth finish.
Both OnTheSnap and vertigo3pc were happy to share their stories with The Autopian, and their photos in turn. Both used Bar Keeper’s Friend to clean their Cybertrucks, with positive results. “I usd the soft liquid variant of BKF,” explained OnTheSnap, adding “After applying it with a sponge I cleaned it off using Windex. He’s had little issue since, too. “It has maintained the same state.” He notes that he has also used the foam spray version of Bar Keeper’s Friend on the whole car since, which brought the shade of the stainless steel up to a lighter color. “So far it’s equivalent to owning a painted car that you wish to maintain, except I use Windex instead of water to quickly clean it” he explains, noting that he follows the typical guidance to remove bird droppings or other contaminants as he sees them.
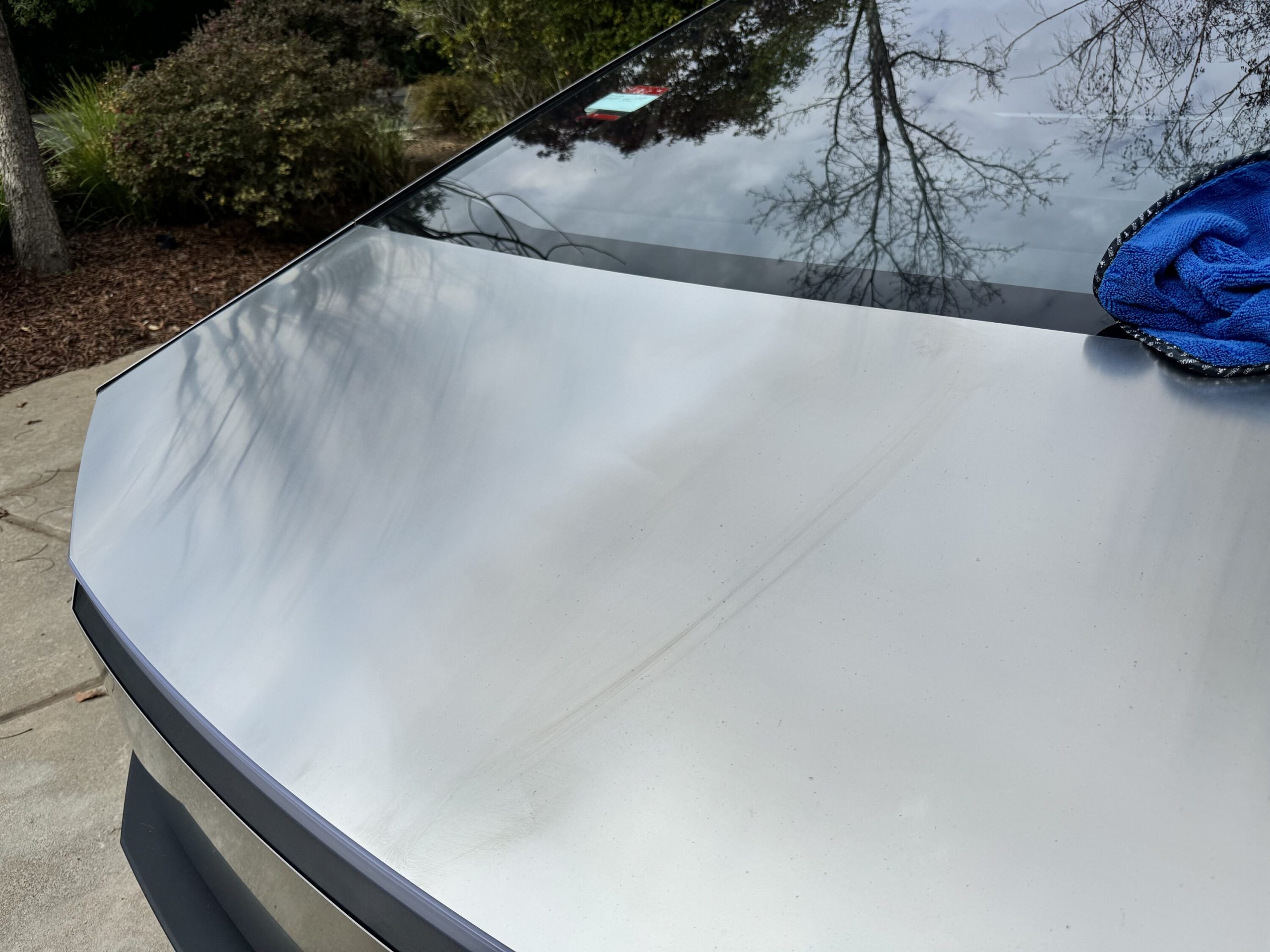
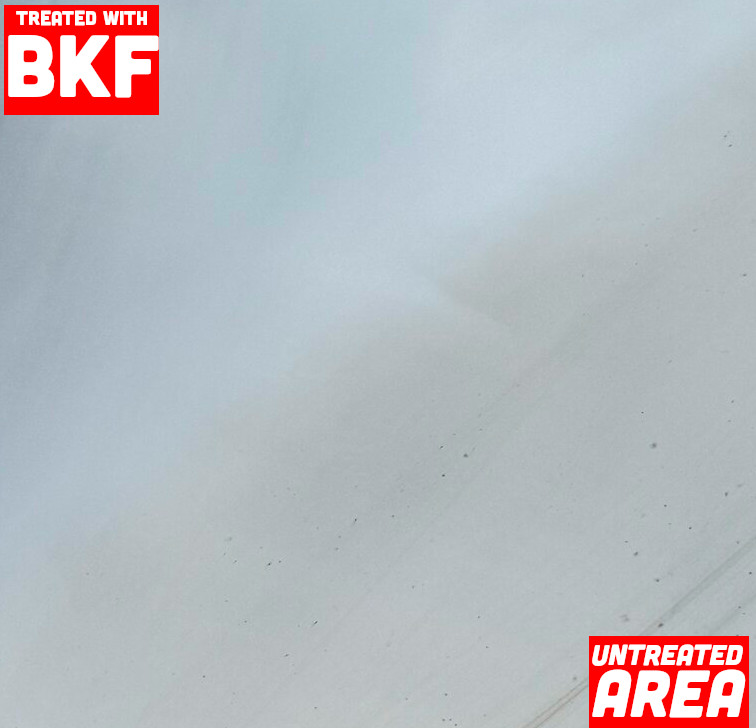
As for vertigo3pc, he had similar success. “I removed the spots using Barkeeper’s Friend (soft version), using a tiny amount on the surface of a microfiber rag, and gently wiping over the spots,” he explains. “I assumed that wiping harder with BKF would definitely remove it, but also just using the rag wet with BKF soft also removed it… so I believed the BKF soft liquid had something to neutralize and remove the spots, whatever they were.” Since the treatment, he hasn’t seen the spots reoccur. He also tried an iron decontamination detailing spray from Chemical Guys, just in case. “After 2 rounds, I noticed no purple runoff, so I assumed the contaminants were gone,” he says.
“I found the best way to remove the spots was Barkeeper’s Friend Soft, followed by soap and water, followed by ammonia-free window cleaner and wipe dry,” says vertigo3pc. He’s contemplating adding a coat of Everbrite ProtectaClear in future to preserve the look of the stainless steel.
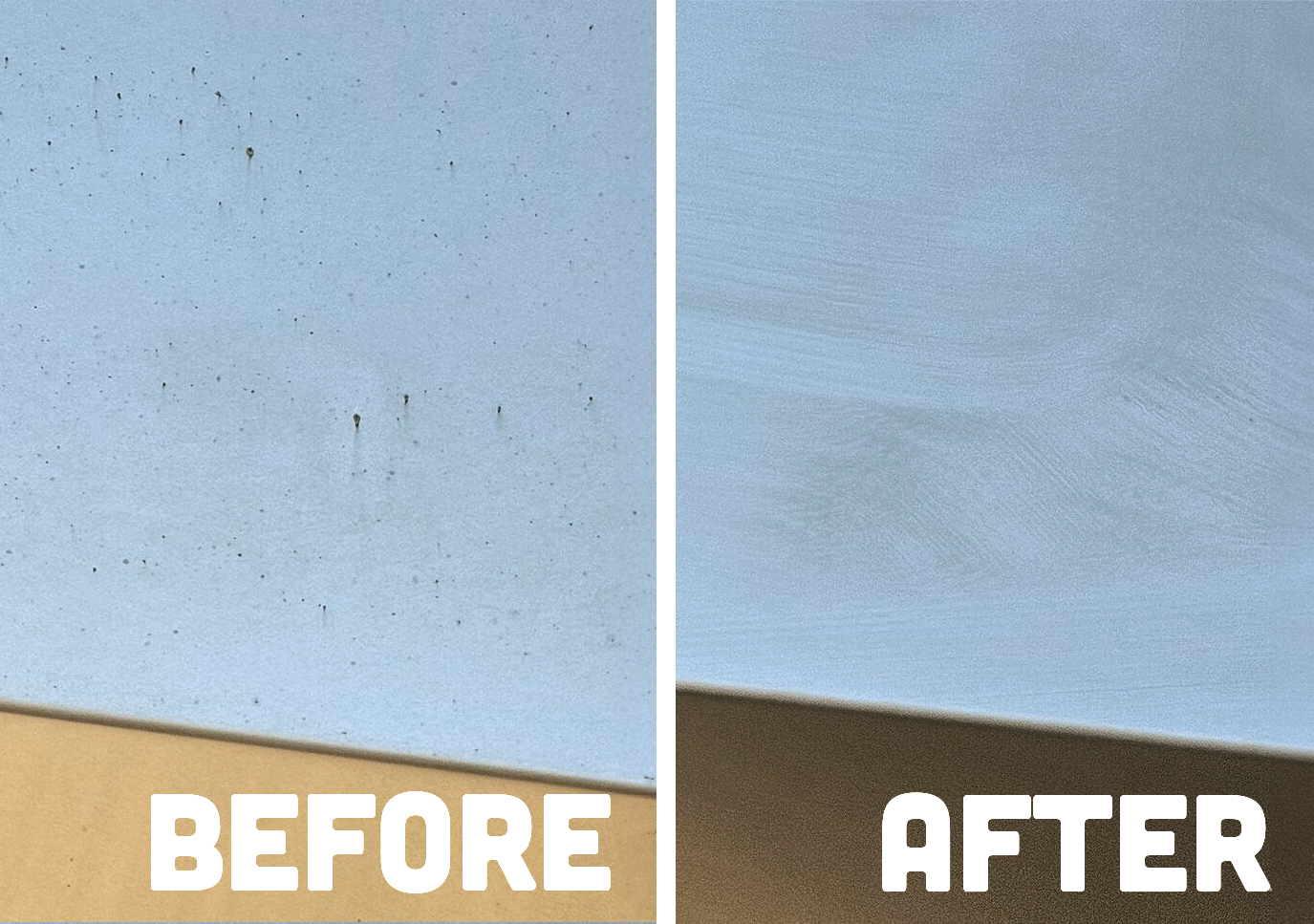
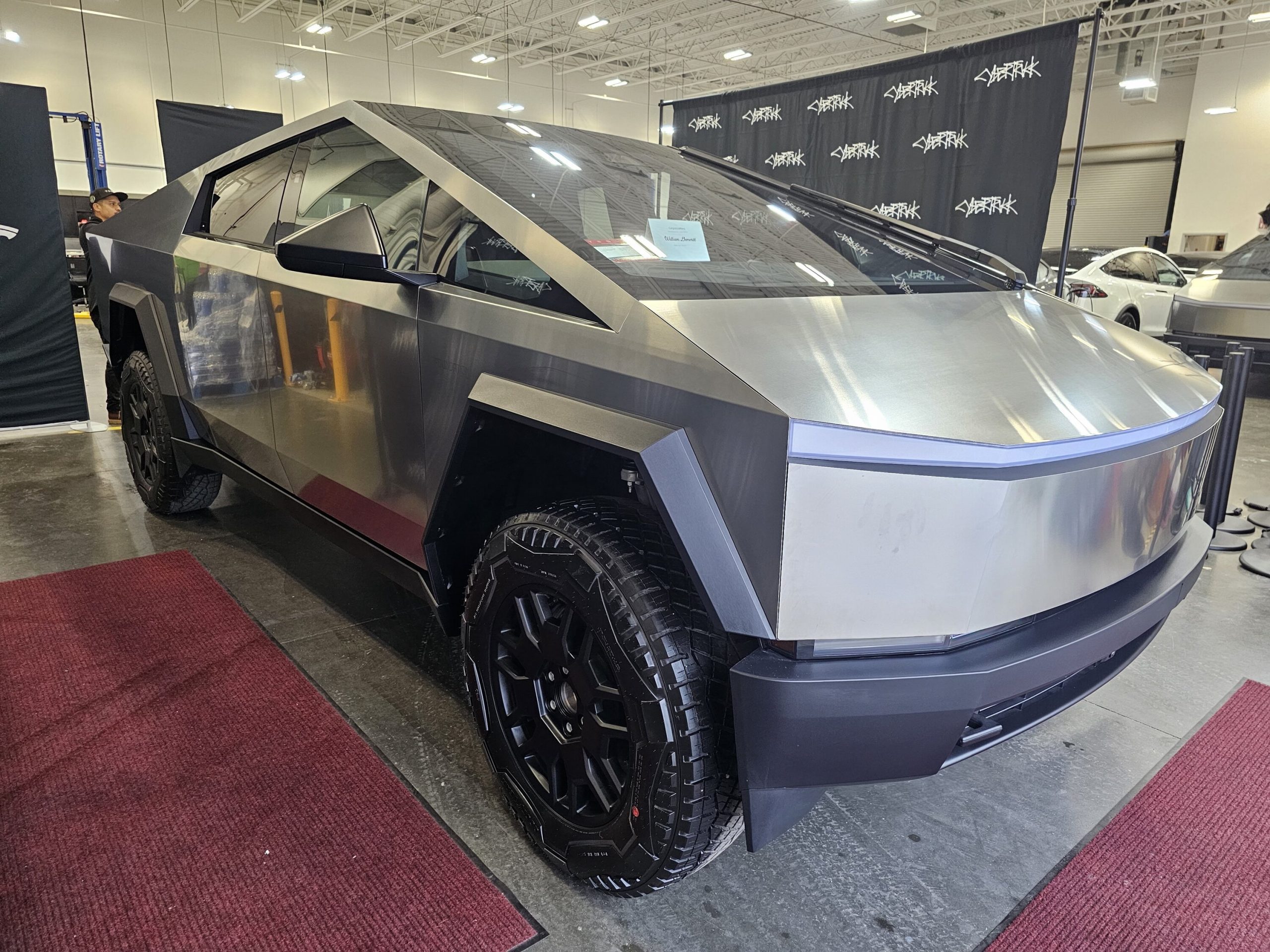
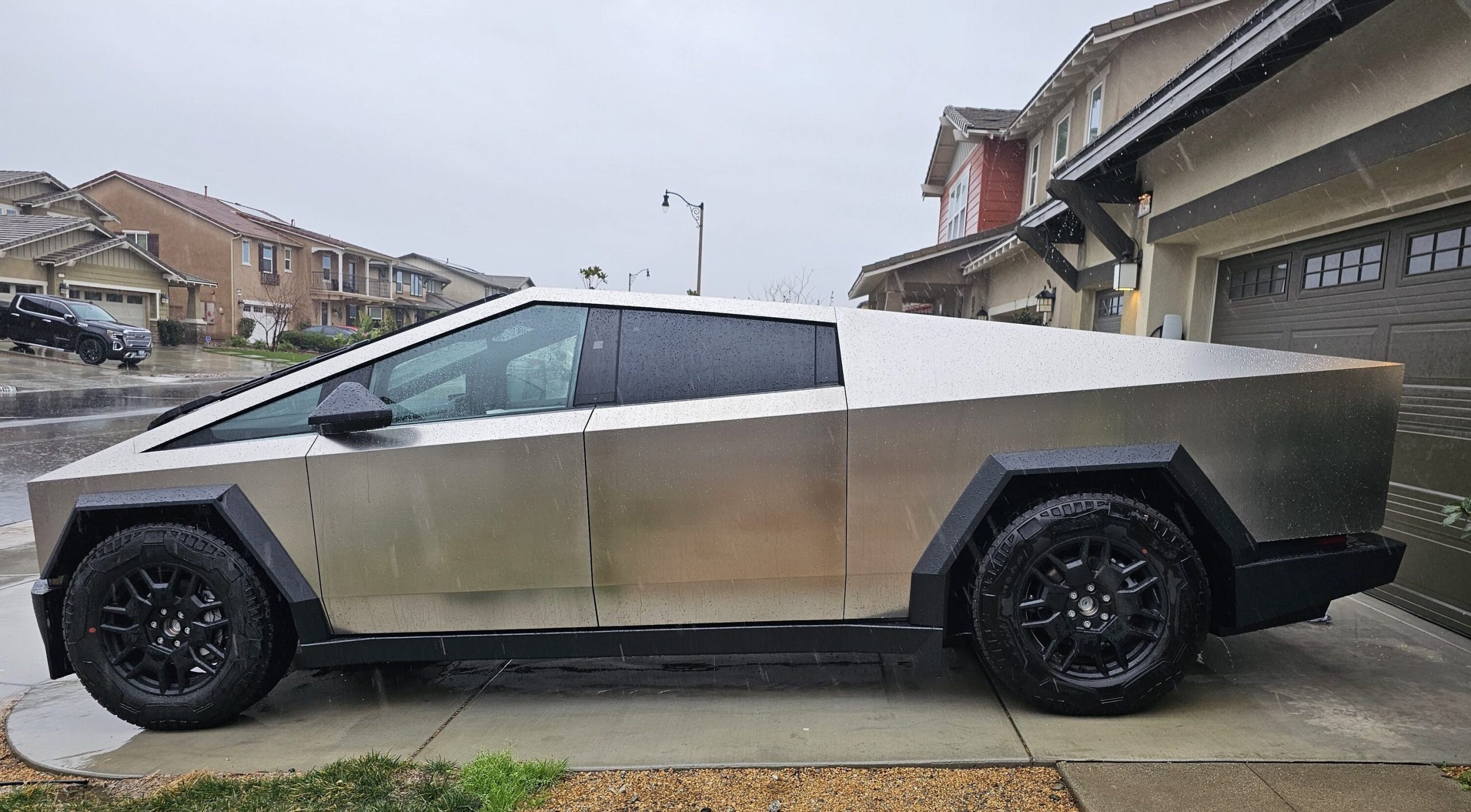
Of course, the corrosion could always reoccur if the trucks were re-exposed to iron contamination. If you lived in an area where iron particulates frequently came down with the rain, you could find yourself detailing the car fairly regularly. Indeed, the Cybertruck manual advises owners to “immediately remove corrosive substances (such as grease, oil, bird droppings, tree resin, dead insects, far spots, road salt, industrial fallout, etc).” At the same time, most automakers make similar suggestions for cars with regular paint finishes, too.
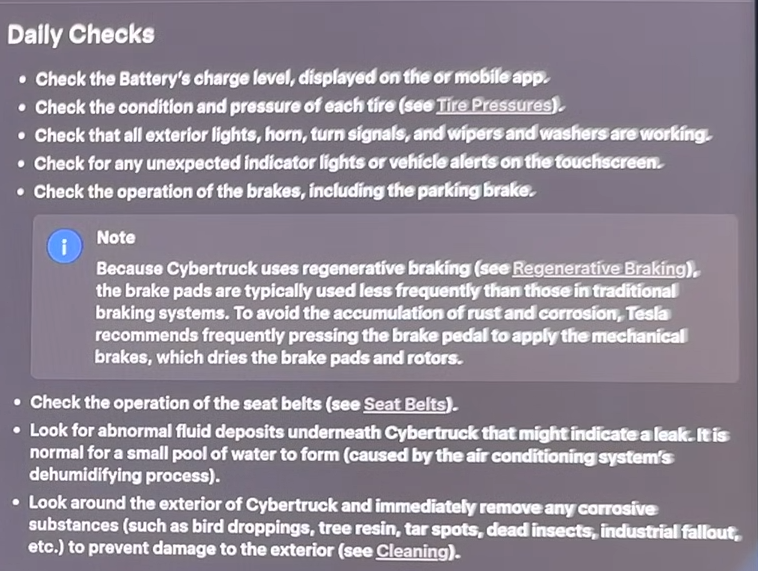
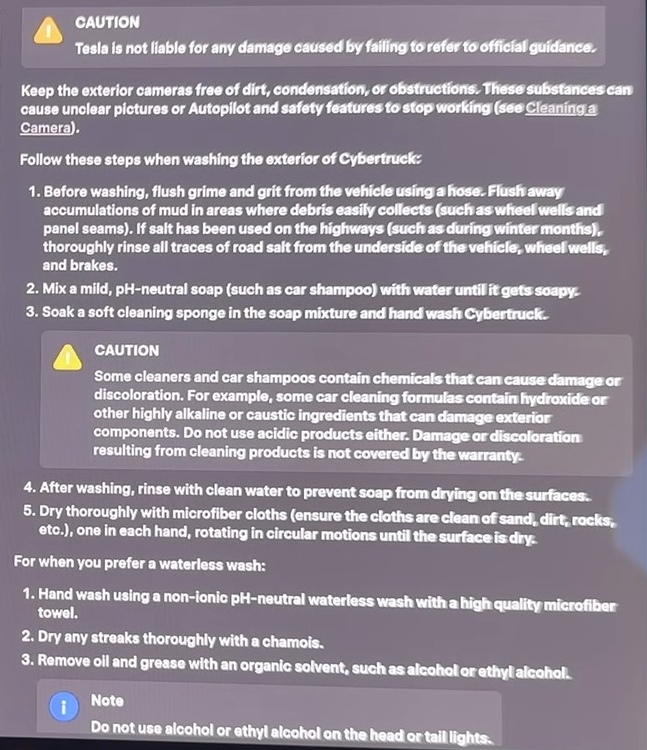
Supporting Evidence
It bears noting that Cybertruck lead engineer Wes Morrill has come out and stated that this type of corrosion is to be expected on the vehicle. On Twitter, he explained that iron particles sitting on the surface of the stainless steel will create corrosion, and that cleaning off with a solution like Bar Keeper’s Friend is recommended.
Good myth busting. Stainless is reactive and free iron that sits on it will rust. It's surface contamination only and can be cleaned off easily. Bar Keeper's Friend used here works well, citrisurf77 can also loosen the deposit and simply wipe it off. If anything stubborn use a… https://t.co/HD3Xeo0inH
— Wes (@wmorrill3) February 16, 2024
You can see Bar Keeper’s Friend in action in a video from Out of Spec Detailing. It doesn’t concern corrosion specifically, moreso how to generally detail the Cybertruck’s stainless steel panels. Regardless, it’s clear to see the effect of the cleaning product on the surface. As a mild abrasive and acidic cleaner, it does a good job of shining up the panels. Presenter Coleton recommends applying it to the entire vehicle to ensure a consistent finish across the truck.
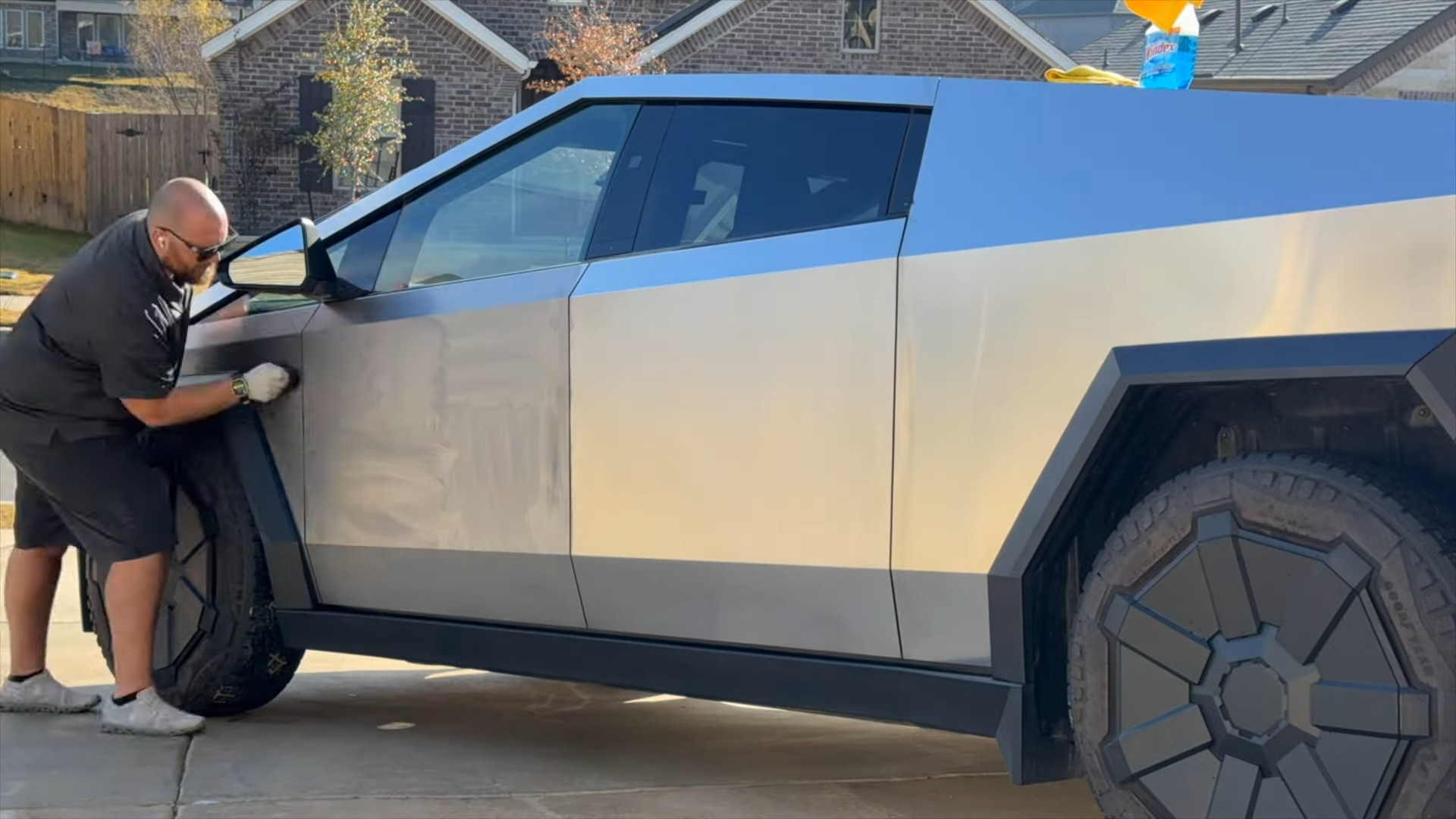
Lots of Cybertrucks, near the delivery center in Austin TX
byu/GunGeekATX incybertruck
There is a large variation in color between panels on new Cybertrucks seen in many photos. One wonders whether a full-car detail could sort this out, or if it’s happening in pre-delivery.
Cold, Hard Reality
So, we’ve learned that stainless steel can indeed corrode, and the conditions under which that can happen. However, for now, it’s really too early to tell if the Cybertruck has a real corrosion problem. If you live right next to a railway, or you regularly transport your car via train, then yes, I’d suspect you might have some corrosion issues to deal with on the regular. Outside of that, it’s probably too soon to tell. Unless Tesla shares its alloy composition with us, or shows us the results of exposure tests that it ran on real panels, we won’t know for some time.
Ultimately, it could prove frustrating for some owners in areas where this kind of contamination is common. Nobody wants to be spending every weekend detailing their truck to avoid unsightly corrosion. While iron particulate contamination can stick in a regular clearcoat and appear ugly, you can at least rest relatively easy in the knowledge that it’s not going to cause too much problem for the metal underneath the paint. In the case of the Cybertruck, there is zero protective layer, so anything on the surface is interacting with bare metal. We should know in the next few months just how much of a burden—or not!—this will prove to be for Cybertruck owners. It may just be the case that a rub-down with Bar Keeper’s Friend once every month or two is enough.
If I had a Cybertruck, I’d be looking to the community to see what works and what doesn’t. I’d absolutely avoid using any steel wool or other iron products on the vehicle, and I’d try and keep the car parked somewhere where it’s not going to be exposed to contaminants like bird droppings or leaf litter. That’s just good practice for any car, though. I’d stop short of personally supporting the use of Bar Keeper’s Friend, having not tried it myself. It makes sense, but I’d hate to see anyone ruin their vehicle. Whatever you do, this sage advice always rings true: “Test on an inconspicuous area first.”
I hope this article has enlightened you to the magic (and limitations) of stainless steel. We might not have all the answers yet, but the science can point you towards the right (and wrong) things to do when it comes to taking care of your stainless steel vehicle. If you’ve got your own Cybertruck, reach out to us for a chat—we’d love to get more word about what’s happening on the ground!
Image credits: Tesla, Out of Spec Detailing via YouTube screenshot, Bar Keeper’s Friend, Carpro, Jason Leung
We had a lot of success with testing the BKF More liquid spray product, easier to apply and neutralize. On several Cybertruck forums we have had in depth discussions leading to great interest and successes with ProtectaClear to stop not only corrosion but fingerprints, water spots, tarnish and salt corrosion. Not only can ProtectaClear be used on Cybertrucks but is often used by automobile enthusiasts on other highly polished accessories such as wheels.
Says you…. I’ll dump all the extra mollybedemnmmum wherever the hell I want.
“Authorities are reporting that a new EPA Super Fund cleanup site has been declared…”
Lewin,
Congrats on writing a truly excellent article about this.
A few comments to add:
As noted elsewhere the best bet is that this stainless is closest to 301, which doesn’t have nearly the corrosion resistance of 304 let alone 316. Based on the web chatter it looks like Delorean started with 304 and then moved to 316 to make their panels more corrosion resistant. Hopefully someone soon will get an XRF gun to tell us what the exact composition is.
It seems like Tesla is not passivating/pickling the panels after forming – this will leave iron from the tooling pressed into the stainless, which will create seeds where corrosion will form. Passivation is key if you do not want your stainless to rust.
One other issue may be when you cold work 304 or other stainless the metal can become magnetic (a relatively high temp heat treat/anneal is required to eliminate this, so my guess is this is not something that can be easily eliminated). This magnetism could be attracting rail dust or other iron particles, which again will be seeds for corrosion.
In short, stainless is not the solution that non-engineers & metallurgists think it is. And some of us engineers keep relearning this again and again – it is a difficult thing to internalize. Almost all metals can corrode – even titanium and nickel – depends on the chemicals, metals and metal ions, pressures and temperatures they are exposed to… I am getting some flashbacks now to some really frustrating projects…
Very good insight!
I’ve heard that about the DeLorean. I would dearly love someone to prove this with the relevant material analysis.